Introduction
A flexible printed circuit board (PCB) is a type of PCB made from flexible materials that allow the board to bend and flex without damage. Flexible PCBs provide several advantages over traditional rigid PCBs, making them useful for many applications where flexibility is required. This article provides an in-depth look at what flexible PCBs are, how they work, their materials, design and fabrication, applications, pros and cons, and more.
What is a Flexible PCB?
A flexible PCB, also known as a flex circuit or flex PCB, is a PCB made from flexible polymer materials like polyimide (Kapton) or polyethylene terephthalate (PET). Rather than using rigid FR-4 laminates like traditional PCBs, flex PCBs use thin flexible laminates that can be bent and flexed repeatedly without damage. The conductive traces on a flex PCB are also made from flexible conductive materials like copper rather than rigid materials.
Flex PCBs provide the following key advantages:
- Flexibility – Can be bent, folded, twisted, and flexed to fit mechanically dynamic applications
- Lightweight – Very thin, lightweight construction compared to rigid boards
- Durable – Flexible materials allow reliable operation under bending and vibration
- Thin profile – Extremely thin compared to rigid boards, allowing compact design
- High density – Small traces and spacing support complex, dense circuit layouts
- Reduced assembly cost – May allow eliminating connectors, harnesses, and other assembly parts
Common applications that benefit from flex PCB properties include:
- Consumer electronics – Cell phones, laptops, wearables, VR headsets
- Medical devices – Hearing aids, implants, monitors, imaging
- Industrial electronics – Robotics, machinery, sensors, controls
- Automotive electronics – Navigation, engine/transmission controls, sensors
- Aerospace/defense – Avionics, guidance systems, radar, testing equipment
Overall, flexible PCBs provide the ability to build reliable circuitry that can be dynamically shaped and integrated into applications requiring thin, lightweight, and high-density electronics.
Flexible PCB Materials
The unique properties of flex PCBs come from the specialized flexible materials used in their construction. While rigid PCBs use materials like FR-4 that are reinforced with fiberglass for mechanical stability, flex PCBs achieve flexibility by using polymer films reinforced with fabric instead.
Common flexible PCB materials include:
Polyimide (Kapton)
Polyimide film, like DuPont’s Kapton brand, is the most popular flex PCB substrate. It provides:
- High dielectric strength
- Stable electrical and mechanical properties over temperature
- Excellent chemical resistance
- Withstands bending and flexing without damage
- UL 94 V-0 flammability rating
Kapton is ideal for dynamic and high-reliability flex applications. However, polyimide absorbs moisture which requires careful handling.
Polyethylene Terephthalate (PET)
PET films, like Mylar, offer benefits including:
- Low cost
- Processing ease
- Dimensional stability
- Chemical resistance
- UL 94 V-0 rating
However PET has lower temperature tolerance than polyimide. It is commonly used for simpler, low cost flex circuits.
Polyethylene Naphthalate (PEN)
PEN films like Teonex provide:
- Highly stable dielectric properties
- Retains flexibility at very low temperatures
- Withstands over 200°C continuously
- Excellent dimensional stability
- Low moisture absorption
PEN is used when robust electrical and mechanical performance over a wide temperature range is required. However, PEN is more expensive than polyimide or PET.
Fluoropolymers (PTFE)
Fluoropolymer films like polytetrafluoroethylene (PTFE) offer:
- Extremely low dielectric constant
- Excellent high frequency signal performance
- Outstanding chemical resistance
- Stable electrical properties over wide temperature range
- Low friction coefficient
PTFE substrates are chosen when superior high frequency or chemical performance is critical.
Flexible PCB Construction
Although the materials differ, flex PCB construction shares many similarities with rigid PCB fabrication. Basic flex PCB construction consists of the following components laminated together:
Conductors – Typically copper traces define the circuit interconnects. Some flex PCBs also use aluminum conductors for specialized applications.
Dielectric substrate – The flexible polymer base layer that supports the copper traces. Polyimide is most common but PET, PEN, and PTFE are also used.
Adhesive – Bonds the copper foil to the substrate. Flexible acrylic, epoxy, or polyimide adhesives are typically used.
Cover layer – A flexible polymer layer laminated over the traces to protect the circuitry. Polyimide is most common. Coverlay films with adhesive prepreg are also available.
Stiffeners – Optional rigid reinforcement layers. Used to create stiffened sections on rigid-flex boards. FR-4 or polyimide are commonly used.
Finishes – Coatings and platings applied to protect traces from corrosion and improve soldering, bonding, or assembly.
Flex layer stackups are constructed using lamination processes similar to rigid PCBs. Multi-layer flex boards with more than two conductor layers are also possible for high density designs.
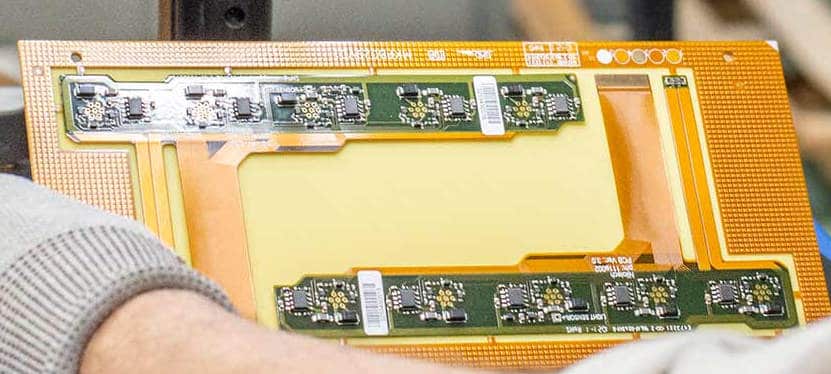
Flexible vs Rigid-Flex PCBs
In additional to pure flexible PCBs, hybrid rigid-flex PCBs combine flex and rigid sections for applications requiring both properties:
Flexible PCB
- Made solely from thin flexible base materials
- Can be dynamically flexed and bent during operation
- Used where free-form flexibility is required
Rigid-flex PCB
- Combines rigid sections for strength and component mounting
- Flexible “hinges” connect the rigid sections
- Folds and bends at flexible joints between rigid areas
- Used where flexibility and rigidity are both needed
Rigid-flex PCBs allow integrating flexible connections between rigid PCBs into a single integrated assembly. This eliminates connectors for a more compact, reliable design.
Flexible PCB Design Considerations
Designing a flex PCB requires accounting for the flexible material properties during layout. Some key design considerations include:
Flexible Bends
Avoid sharp flexing bends below the minimum bend radius for the substrate material used. Typical minimum bend radii range from 2-10x the board thickness depending on materials. Gradual bends maintain maximum flex life.
Dynamic Flex Areas
Minimize conductor widths and spacing in areas subject to continuous dynamic bending to prevent cracked traces. Wider traces are more prone to flexural failure.
Thermal Loads
Carefully consider component power dissipation. Flex boards provide less heat sinking compared to thicker rigid boards. Use rigid sections or stiffeners for high-power components.
Component Attach
SMD packages with leadless terminations are preferred over leaded components. Leaded parts undergo more stress during flexing. Use flexible adhesives to attach strained components.
Reinforcements
Add stiffener strips or plates to strengthen areas around connectors, components, and high-stress regions for reliable performance under flexing.
Patterning and Plating
Avoid uncovered copper near board edges. Use solder mask or encapsulant to prevent copper wicking and dendrite growth during flexing. Edge plating improves reliability.
Flex PCB Assembly and Connectors
Special considerations apply when assembling components and connectors to flex PCBs:
- Soldering – Reflow soldering SMD components is preferred over hand soldering to avoid heat damage. Soldering to stiffened areas reduces flexing stress.
- Adhesives – Use flexible epoxies or acrylics to attach strained components and connectors. Avoid rigid adhesives.
- Connectors – Avoid large, heavy connectors. Use flex-tail connectors soldered directly to the PCB without strain relief hardware. Consider connector-less folded/soldered flex joints.
- Harnesses – Eliminate rigid wire harnesses. Directly attach cables to flex PCBs to reduce strains. Consider printed flex cabling.
- Conformal coating – Select flexible coatings like silicones or urethanes. Avoid rigid acrylics which restrict bending.
Properly designed assembly processes are critical to producing robust, reliable flex PCBs able to withstand bending stresses.
Flex PCB Applications
The thin, lightweight, and flexible properties of flex PCBs make them well suited for many applications with space, weight, or flexibility constraints.
Consumer Electronics
Flex PCBs are widely used in smartphones, tablets, wearables, and other mobile consumer technology where low weight and small size are critical. Flex circuits integrate nicely into tight, dynamically bending mechanical assemblies.
Medical Devices
Medical devices like patient monitoring systems, imaging equipment, and implantable devices use flex PCBs to fit printed circuits into small, curving spaces. Flex circuits withstand repeated sterilization and cleaning processes.
Industrial Electronics
Industrial automation systems benefit from flex PCBs. Flexible sensor instrumentation and control circuits simplify integrating wiring into moving machine parts. The durability of flex PCBs also withstands vibration and continuous motion.
Automotive Electronics
Vehicles utilize flex PCBs in dashboard displays, around moving parts, and in the hot engine bay environment. Flex circuits survive vibration while providing reliable interconnections and a lighter weight alternative to wire harnesses.
Aerospace/Defense
Avionics systems, guidance controls, and other air and spacecraft use flex PCB technology due to its durability under vibration and minimal space requirements. Weight savings are also beneficial for aerospace applications.
Medical Devices
Hearing aids, implants, and patient monitoring equipment are ideal applications for flex PCB technology. The small, lightweight circuits integrate well into curving earpieces, sensors, and probes. Flexibility and reliability are also critical for life-sustaining devices.
Pros and Cons of Flexible PCBs
Advantages
- Extremely lightweight and thin
- Can conform to a wide range of shapes
- Dynamic and repeated flexing/bending ability
- Vibration and impact resistance
- No wiring or connectors needed for flex joints
- High component density with small features
- Reduced assembly compared to discrete wiring
- Improved reliability over wires and connectors
- Lower overall product weight
Disadvantages
- Generally higher PCB cost compared to rigid technology
- Limited to smaller component sizes and lower power
- Special design considerations for flex areas
- PCB layout is more complex
- Special assembly process care required
- Repair and rework is more difficult
- Smaller production volumes increase cost
Flexible PCB Cost Considerations
Flex PCBs are generally more expensive than rigid PCBs, but they can reduce overall system cost when factoring in assembly benefits. Cost factors include:
PCB Materials – Specialty flexible base materials are more expensive than rigid FR-4. But as volume increases, flex materials become cost-competitive.
Layers – Complex multilayer designs are more costly than simple 2 layer boards. But flex PCB technology supports very high layer counts.
Volume – Smaller prototype volumes increase tooling costs. Higher volume production reduces individual PCB pricing significantly.
Tolerances – Tighter tolerances and smaller features increase cost but are supported with flex PCBs.
Testing – Advanced testing adds cost, but helps validate proper flex performance.
Assembly – Eliminating wires, connectors, and manual assembly steps reduces overall system cost.
While individual flex PCB prices can be higher than rigid boards, the system-level benefits often offset the difference in high volume production.
Flexible PCB Fabrication Process
Producing flexible PCBs requires specialized manufacturing processes adapted to handle the flexible base materials. However, flex PCB fabrication shares many similarities with rigid PCB methods.
Inner Layer Production
- Photolithography patterns copper-clad laminate with etched conductors. Polyimide films replace rigid FR-4.
- Flexible laminates require use of polyimide or acrylic adhesive layers.
- Smaller circuit features and spacing are possible vs. rigid technology.
Layer Alignment and Lamination
- Sheet and roll-to-roll processes adapt rigid multilayer lamination methods.
- Laser drilled microvias provide interlayer connections on multilayer flex boards.
Outer Layer Processing
- Additional patterned copper layers bonded to the flex circuit core using plated or adhesive filled blind vias.
- Fine features defined photolithographically and etched on the outer layers.
Solder Mask
- Liquid photoimageable (LPI) solder mask coats conductors with flexible epoxy or acrylic polymers.
- Solder mask prevents shorts and protects circuits from environmental contamination.
Final Finish
- Electroless nickel/immersion gold (ENIG) provides a reliable final finish for flex PCBs.
- Finishes protect conductive traces and provide soldering, bonding, and contact surfaces.
Testing and Inspection
- Electrical testing validates proper connectivity and performance during dynamic flexing.
- Automated optical inspection (AOI) ensures quality standards are met.
Summary of Key Points
- Flexible PCBs use thin, bendable materials to build circuits that dynamically flex without failure
- Polyimide, PET, PEN, and PTFE are common flexible PCB substrates
- Flexible materials provide light weight, small size, and vibration resistance
- Flex-to-rigid boards combine both flexible and rigid PCB sections
- Careful design is needed around flex areas and components
- Assembly process must maintain flexibility with special approaches
- Flexible PCBs bring size and weight benefits to many applications
- Flex PCBs have a higher cost, but enable overall system benefits
- Specialized fabrication processes allow producing high quality flexible circuits
Flexible PCB Frequently Asked Questions
What are the typical layer counts for flexible PCBs?
Simple flex PCBs often use 2 conductive layers, while complex designs may have 12 or more layers. Typical layer counts range from 2 to 8. Multilayer flex boards provide design flexibility to route dense interconnects in complex circuits.
What line/space rules can be achieved with flex PCBs?
Flexible PCBs support very fine feature sizes, down to trace/space of 100 μm (4 mils) or below. Rigid PCB technology typically sees minimum features around 125 μm (5 mils). The thin flexible materials enable tighter photolithographic patterning.
What are typical flex PCB minimum bend radii?
Minimum bend radius varies based on the flexible material used. As a general guideline:
- Polyimide (Kapton) – 3x material thickness
- PET – 10x material thickness
- PEN – 5x material thickness
- PTFE – 4x material thickness
So a common 50 μm thick Kapton board could bend to a 3 mm radius without damage.
How are components attached to flexible PCBs?
Both SMD and leaded components can be used on flex PCBs but SMD packages are preferred when possible. SMD parts avoid stresses from leads bending. Flexible adhesives help minimize stresses on attachments. Avoid large or heavy parts in dynamically flexing areas.
How do you connect a flex PCB to a rigid PCB?
There are several approaches to connecting flex PCBs to rigid boards:
- Use a flex-to-rigid connector soldered directly to the flex circuit
- Solder the flex tail directly to pads on the rigid board
- Use a ZIF or other mechanical socket for a demountable connection
- Use a rigid-flex board with integrated flex hinge between rigid regions
Careful strain relief and structural support is critical with any approach.
Conclusion
Flexible PCBs provide a unique set of advantages compared to traditional rigid boards, making them an enabling technology across many fields. From complex consumer gadgets to mission-critical aerospace systems, flex circuits deliver capabilities not achievable with other approaches. With a solid understanding of flexible PCB materials, design factors, assembly, fabrication, and applications, engineers can effectively apply and benefit from flex PCB technology. While flex PCBs have a higher base cost, their system-level advantages and continually improving economy make them a key part of the future of electronics.
Leave a Reply