Why is Component Orientation Important?
Proper component orientation is essential for several reasons:
-
Functionality: Incorrect orientation of components can lead to malfunction or complete failure of the electronic device. Many components, such as diodes, electrolytic capacitors, and integrated circuits (ICs), have specific polarity or pin assignments that must be followed for proper operation.
-
Manufacturing: Automated assembly processes, such as pick-and-place machines, rely on correct component orientation for accurate placement. Incorrectly oriented components may cause assembly errors, leading to increased production time and costs.
-
Space optimization: Efficient component orientation allows for optimal use of PCB space, enabling more compact designs and reducing overall device size.
-
Signal integrity: Proper orientation of components can minimize signal interference and crosstalk, ensuring the device performs as intended.
-
Thermal management: Some components, such as power regulators and heat sinks, require specific orientation for effective heat dissipation. Incorrect orientation may lead to overheating and reduced reliability.
Types of Component Orientation
There are several types of component orientation used in PCB design and assembly:
Surface Mount Technology (SMT)
SMT components are mounted directly onto the surface of the PCB. They come in various package types, each with its own orientation requirements.
-
Chip components: Resistors, capacitors, and inductors in chip packages have no specific orientation requirements, as they are symmetrical. However, some chip components, such as diodes and LEDs, have polarity markings that must be followed.
-
Gull-wing packages: ICs and other components in gull-wing packages, such as SOICs and QFPs, have leads that extend from the sides of the package and are bent downwards to form a gull-wing shape. The orientation is determined by the pin 1 marking, which is typically a dot or notch on one corner of the package.
-
J-lead packages: Similar to gull-wing packages, J-lead packages have leads that extend from the sides of the package but are bent inwards to form a J-shape. The orientation is also determined by the pin 1 marking.
-
Ball Grid Array (BGA): BGA packages have an array of solder balls on the bottom of the package. The orientation is determined by the position of the balls relative to the package outline and any markings on the top of the package.
Through-Hole Technology (THT)
THT components have leads that are inserted through holes drilled in the PCB and soldered on the opposite side.
-
Axial components: Resistors, capacitors, and diodes in cylindrical packages have leads extending from each end. The orientation is determined by the polarity markings or the length of the leads.
-
Radial components: Capacitors and some inductors in radial packages have both leads extending from the same side of the component body. The orientation is determined by the polarity markings or the spacing between the leads.
-
DIP (Dual Inline Package): ICs in DIP packages have two parallel rows of leads. The orientation is determined by the pin 1 marking, which is typically a notch or dot on one end of the package.
Orientation Markings and Symbols
To ensure correct component orientation, various markings and symbols are used on components and PCBs. Some common markings include:
-
Pin 1 marking: A dot, notch, or beveled edge on the package indicates the location of pin 1. This is crucial for orienting ICs and other multi-pin components.
-
Polarity markings: A plus sign (+) or a colored band indicates the positive lead of polarized components such as electrolytic capacitors and diodes.
-
Cathode marking: A band or a notch on the cathode end of a diode indicates its orientation.
-
Silkscreen indicators: PCBs often have silkscreen printed symbols, such as component outlines, polarity markers, and pin 1 indicators, to guide the placement and orientation of components during assembly.
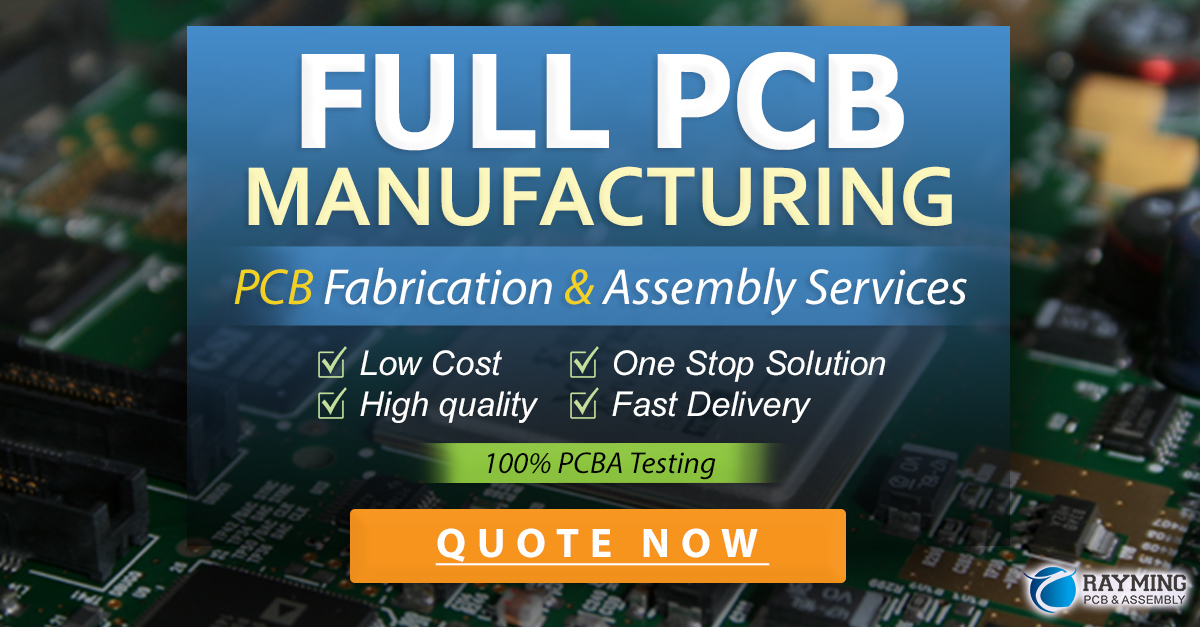
Common Orientation Errors and Their Impact
Incorrect component orientation can lead to various issues, affecting the functionality and reliability of the electronic device. Some common orientation errors include:
-
Reversed polarity: Incorrectly oriented polarized components, such as electrolytic capacitors and diodes, can cause short circuits, overheating, or component failure.
-
Swapped pins: Incorrectly oriented ICs or connectors can lead to swapped signals, causing malfunction or damage to the device.
-
Misaligned components: Improperly aligned components can cause assembly issues, such as poor solder joints or mechanical stress on the component leads.
-
Inverted components: Components placed upside-down can cause shorts, poor connections, or interference with other components.
These errors can result in:
- Device malfunction
- Reduced performance
- Increased power consumption
- Overheating and potential fire hazards
- Increased manufacturing costs due to rework and scrap
Best Practices for Ensuring Correct Component Orientation
To minimize orientation errors and ensure proper assembly, consider the following best practices:
-
Clear documentation: Provide clear and accurate assembly drawings, schematics, and bills of materials (BOM) that specify the correct orientation of each component.
-
Consistent marking: Use consistent and unambiguous markings on components and PCBs to indicate orientation, such as pin 1 dots, polarity symbols, and silkscreen indicators.
-
Design for manufacturability: Consider the capabilities and limitations of the assembly process when designing the PCB layout. Provide adequate space between components and use standard package types to facilitate automated assembly.
-
Assembly process control: Implement quality control measures, such as visual inspection, automated optical inspection (AOI), and X-ray inspection, to detect and correct orientation errors during the assembly process.
-
Training and communication: Ensure that all personnel involved in the design, manufacturing, and assembly processes are trained on the importance of correct component orientation and the potential consequences of errors. Foster open communication to address any concerns or issues promptly.
Component Orientation in Different Industries
The importance of component orientation varies across different industries and applications. Here are some examples:
Industry | Importance of Component Orientation |
---|---|
Automotive | High importance due to safety-critical applications and harsh operating conditions. |
Medical | High importance due to the need for reliability and the potential impact on patient safety. |
Aerospace | High importance due to the need for reliability in extreme environments and long product life. |
Consumer | Moderate importance, balancing cost and performance. Aesthetics may also be a consideration. |
Industrial | High importance for applications requiring reliability and long-term performance. |
FAQ
Q1: What is the difference between SMT and THT component orientation?
A1: SMT (Surface Mount Technology) components are mounted directly onto the surface of the PCB, while THT (Through-Hole Technology) components have leads that are inserted through holes in the PCB and soldered on the opposite side. SMT components have specific orientation requirements based on their package type, such as gull-wing or J-lead, while THT components are oriented based on lead polarity or pin arrangement.
Q2: How can I identify pin 1 on an IC package?
A2: Pin 1 on an IC package is typically indicated by a dot, notch, or beveled edge on one corner of the package. Refer to the component datasheet for specific details on the pin 1 marking for a given package type.
Q3: What should I do if I discover a component orientation error during assembly?
A3: If a component orientation error is discovered during assembly, it should be corrected as soon as possible to avoid potential damage or malfunction of the device. Depending on the stage of assembly and the type of component, this may involve desoldering and repositioning the component or replacing it with a new one. It is essential to document the error and take steps to prevent similar occurrences in the future.
Q4: Can component orientation affect the thermal performance of a device?
A4: Yes, component orientation can affect the thermal performance of a device. Some components, such as power regulators and heat sinks, are designed to dissipate heat in a specific direction. If these components are oriented incorrectly, heat may not be effectively removed from the device, leading to overheating and reduced reliability. It is crucial to follow the manufacturer’s recommendations for component orientation to ensure proper thermal management.
Q5: How can I ensure correct component orientation in my PCB design?
A5: To ensure correct component orientation in your PCB design, follow these guidelines:
- Use clear and consistent markings on components and PCBs to indicate orientation, such as pin 1 dots, polarity symbols, and silkscreen indicators.
- Refer to component datasheets and application notes for specific orientation requirements.
- Use CAD tools that support component orientation checks and design rule checks (DRCs) to identify potential issues.
- Communicate the importance of correct component orientation to all team members involved in the design and assembly process.
- Implement quality control measures, such as visual inspection and automated optical inspection (AOI), to detect and correct orientation errors during assembly.
By understanding the importance of component orientation, the different types of orientation, and best practices for ensuring correct orientation, you can design and manufacture reliable, high-quality electronic devices.
Leave a Reply