Introduction
Keeping printed circuit boards (PCBs) clean is critical for proper function and reliability. As PCBs are processed and assembled, various contaminants can build up on the boards. Cleaning is necessary to remove harmful residues and substances that can lead to issues. There are several effective cleaning methods and solutions for PCBs.
The type of cleaning processes utilized depends on the stage of production. Different cleaning approaches are used on bare boards after fabrication, on assembled boards during rework, and on finished populated boards. Understanding the appropriate methods and materials for cleaning PCBs is essential for electronics manufacturing and repair.
This article explores common PCB contaminants, when cleaning is needed, effective techniques and chemicals, safety precautions to take, and recommendations for proper cleaning processes.
Types of PCB Contamination
Several types of contamination may be present on PCBs that require cleaning:
- Flux residues – From soldering operations. Rosin, water-soluble, and no-clean flux types.
- Solder pastes – Left over solder material and coatings.
- Oils and greases – Fingerprints, machining lubricants, dielectric greases.
- Metal particles – Copper or solder debris. Burrs or dust.
- Salts and acids – From etching, plating, testing chemicals.
- Dust and dirt – Fibers, packaging debris, environmental particles.
- Conformal coatings – Excess material outside target areas.
- Adhesives and tapes – From production processes.
- Marker inks – Pen and marker writing on boards.
Proper cleaning removes unwanted contamination without spreading or redepositing it. The cleaning process, chemistry, temperature, and drying steps are tailored to the specific types of substances to be removed.
When to Clean PCBs
PCB cleaning is performed at various points through assembly, including:
Bare Board Cleaning
Done after fabrication to prepare boards for assembly. Removes residues from manufacturing. Critical for high reliability boards to prevent electrochemical migration.
Pre-Soldering Cleaning
Prior to soldering, boards are cleaned to eliminate oils, dust, and particulates to ensure proper wetting and solder joint formation.
Post-Solder Cleaning
Removes flux residues after soldering. Prevents dendritic growth and other issues. Done with no-clean fluxes as well as conventional fluxes.
Conformal Coating Prep
Cleaning prior to conformal coating improves adhesion. Oils and residues can cause coating defects or delamination.
Rework Cleaning
Localized cleaning during rework removes previous solder and fluxes in repair area to prepare for new solder joints
Final Cleaning
End-of-line cleaning to remove all debris, markings, adhesives, etc. from populated boards before testing, inspection, and shipment.
PCB Cleaning Methods
PCBs can be cleaned using different techniques:
Aqueous Cleaning
Involves washing PCBs in water-based cleaners diluted with DI water. Used with soaps, detergents, surfactants to dissolve ionic contaminants. Effective cleaning method for removing flux residues.
Solvent Cleaning
Employs solvents to dissolve and displace contaminants. Solvents such as isopropyl alcohol (IPA), acetone, and methanol are commonly used with PCBs along with agitation.
Abrasive Cleaning
Makes use of mechanical action to scrub away contaminants. Abrasive films, wipes, and air-driven media provide scouring action.
Ultrasonic Cleaning
Uses high frequency sound energy to agitate a liquid cleaning solution. Cavitation provides strong localized scrubbing. Used with aqueous and solvent-based chemistries.
Plasma Cleaning
Utilizes ionized gas plasma to provide chemical cleaning action. Works by breaking down and volatilizing organics. Provides thorough cleaning for PCB rework and repairs.
Laser Cleaning
Focused laser ablates away contaminants layer by layer. Excels at removing conformal coating and surface coatings without damage.
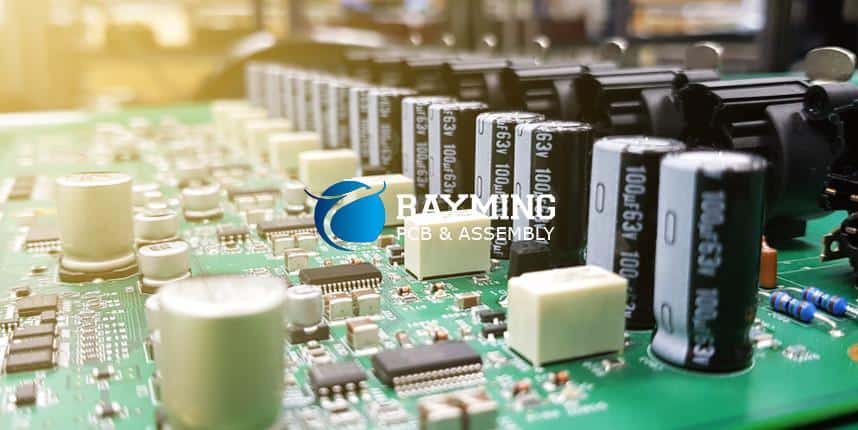
PCB Cleaning Chemicals
Specialty chemicals used for cleaning PCBs include:
Surfactants and Detergents
- Lower surface tension of water for better wetting and cleaning action.
- Anionic and non-ionic types used. Remove ionic residues.
- Must be fully rinsed to prevent film or residue.
Solvents
- Quickly dissolves and flushes away organic and ionic contaminants.
- Isopropyl Alcohol (IPA) most common. Also acetone and methanol.
- Allowed to fully dry after cleaning.
Saponifiers
- Convert hard-to-remove substances into more soluble soaps.
- Used for removing some silicone contaminants.
- Requires thorough post-cleaning rinse.
Acids and Bases
- Dissolve inorganic residues and convert to soluble salts.
- Weak organic acids commonly used along with detergents.
- Must neutralize and rinse completely. Corrosive if left on board.
Chelating Agents
- Bind and capture hard water ions and inorganic compounds.
- Allow ionic residues to be rinsed away.
- Include chelates like EDTA and citric acid.
Enzymes
- Specialty enzyme cleaners break down organics like fluxes.
- Used in ultra-low residue flux removal.
- Compatible with numerous substrates.
Silicone Removers
- Designed to penetrate and solubilize silicone type contaminants.
- React with silicone to allow complete removal.
- Used prior to conformal coating to promote adhesion.
Aqueous PCB Cleaning Process
Aqueous or detergent-based cleaning is a popular, effective approach used with PCBs. Here is a typical aqueous cleaning process sequence:
- Pre-rinse – DI water spray rinse to remove loose debris and pre-heat boards.
- Wash – Immerse boards in cleaning solution diluted with DI water. Typically 5-30% concentration. Agitate boards or solution. Time and temperature depends on cleaner chemistry.
- Post rinse – Thorough rinse in multiple DI water baths at ~100-140°F to flush away all detergent and contaminants. Cascading water flow used.
- Dry – Dry boards in oven or using air knives. Forced air if aqueous cleaner is flammable. Verify boards are fully dry.
- Next process – May do additional cleaning or straight to soldering, coating, inspection etc.
Key factors are using the proper concentration, temperature, and contact time of the detergent chemistry along with thorough rinsing.
Solvent PCB Cleaning Basics
Solvent cleaning with alcohols and other solvents is quick and effective. Here is an overview:
- Highest purity anhydrous solvents normally used to prevent residue.
- Can be applied manually by wiping, brushing, or spraying onto boards.
- Often done by immersion and agitation in solvent baths.
- Ultrasonic tanks commonly used to provide strong agitation.
- Allows very rapid cleaning action at room temp, though heating speeds the process.
- Thorough drying needed afterwards, usually with forced air.
- Vapors must be safely collected and handled.
Isopropyl alcohol (IPA) is the most prevalent PCB cleaning solvent, often at 90%+ purity levels.
Abrasive PCB Cleaning Options
Abrasives can scrub away tough surface contamination:
Abrasive Films and Papers
- Use abrasive films to wipe boards or abrasive papers on rubbing blocks.
- Works for thick or cured surface contamination layers.
- Typically use micron-range abrasives to prevent board damage.
- Must avoid excessive abrasion which can harm delicate components.
Air-Propelled Abrasives
- Use compressed air to shoot abrasive media at boards.
- Media types include baking soda, plastic beads, crushed walnut shells.
- Removes thick coatings, oxides, etc.
- Risk of static charge buildup. Media must be fully recovered.
Brushing
- Stiff nylon or copper brushes used to mechanically scrub boards.
- Works for removing oxidation and tarnish on exposed copper.
- Care needed around fragile parts. Potential for copper scratching.
- Often done with solvents, cleaners, or DI water.
Ultrasonic Cleaning Systems
Ultrasound is highly effective for cleaning PCBs:
- Transducers vibrate cleaning solution at 20-50+ kHz frequencies.
- Cavitation bubbles scrub board surfaces.
- Works with aqueous and solvent-based cleaning solutions.
- Provides consistent, thorough contaminant removal.
- Allows complex geometries and hidden areas to be reached.
- Typically heat solution to accelerate cleaning action.
- Used for rework, prototype, and production PCB cleaning.
Laser PCB Cleaning Characteristics
Lasers provide contactless, precise cleaning:
- Infrared lasers most common, though UV lasers also used.
- Scan pulsed laser over areas to ablate away layers of contamination.
- Allows selective removal without spreading material around.
- Excellent for conformal coatings, paints, oxides, etc.
- Adds process time. Complex boards take longer.
- Avoid material redeposition around laser site.
- Risk of thermal damage if settings exceed material limits.
Plasma PCB Cleaning Properties
Plasma offers thorough, residue-free PCB cleaning:
- Uses ionized gas plasma discharge. Oxygen and air most common gases.
- Reactive plasma constituents break down organics through oxidation.
- Provides microscopic cleaning action. Removes submicron particles.
- Does not damage substrates or sensitive components.
- Equipment cost is higher compared to other methods.
- Depends on exposed surfaces so shadowed areas are harder to clean.
- Often integrated into rework equipment for flux removal.
Post-Clean Inspection
After cleaning PCBs, inspection verifies boards are properly cleaned:
- Visual inspection – Checks for complete removal of visible surface residues. Verifies acceptable appearance and finish.
- Blacklight inspection – Flourescent dyes in many contaminants will glow if still present when viewed under UV light.
- Solvent extraction testing – Involves sampling boards using solvents to extract any remaining residues which are then quantified. Verifies cleaning efficiency meets specifications.
- Ion chromatography – Identifies and measures ionic contamination left on boards after cleaning. Checks for remaining flux, salts, and acids.
- FTIR analysis – Fourier transform infrared spectroscopy used to detect organic contamination like oils and greases.
PCB Cleaning Safety Precautions
Cleaning can involve hazardous chemicals. Some key precautions include:
- Selecting cleaning solutions rated as nonhazardous when possible.
- Avoiding cleaners with toxic, flammable, or corrosive ingredients.
- Using the lowest concentration of chemicals needed for effective cleaning.
- Separating incompatible materials like acids and solvents.
- Safely collecting and neutralizing spent cleaning solutions.
- Keeping solutions off of skin using protective apparel and gloves.
- Providing adequate ventilation for vapors and mists.
- Storing cleaning chemicals properly in approved containers.
- Training workers on chemical handling procedures.
Recommended PCB Cleaning Guidelines
Here are some best practice guidelines for PCB cleaning:
- Test processes on non-critical boards first to verify compatibility.
- Follow chemical manufacturers recommended usage concentrations and conditions.
- Use cleaners specifically formulated for electronics. Avoid general industrial chemicals.
- Change out cleaning solutions once fully loaded with contaminants per solution instructions.
- Allow sufficient process dwell time for optimally effective cleaning.
- Rinse thoroughly with pure water to completely flush away all detergent and chemical residues.
- Dry immediately after aqueous cleaning using oven drying or forced air systems.
- Inspect boards under blacklight or use ion chromatography testing to confirm cleaning efficacy.
- Store boards in protective packaging after cleaning to prevent recontamination.
Frequently Asked Questions
What is the most common PCB cleaning solvent used?
Isopropyl alcohol (IPA) is the most prevalent solvent used for cleaning PCBs and electronics. It quickly dissolves ionic contaminants and dries fast without leaving any residues.
What temperature should aqueous PCB cleaning solutions be?
Aqueous cleaner baths are typically run anywhere from room temperature up to 60°C (140°F). Elevated temperatures accelerate cleaning speed. The optimal temperature depends on the chemistry.
How should solvents be applied to PCBs?
Solvents are often applied by spraying, brushing, or wiping onto PCBs manually. Immersion cleaning in solvent ultrasonic baths is also common. Solvents evaporate rapidly at room temperature.
How does plasma cleaning work for PCBs?
Plasma systems use ionized gas to create reactive species that break down and volatilize organic contaminants on boards through oxidation reactions. It provides residue-free cleaning.
When should final PCB cleaning be performed?
Final PCB cleaning should be done after all assembly steps are complete and any previous cleaning processes. It removes all manufacturing residues before testing, inspection, and packing boards for shipment.
Leave a Reply