Printed circuit boards (PCBs) are used to mechanically support and electrically connect electronic components using conductive pathways or traces etched from copper sheets laminated onto a non-conductive substrate. PCBs require various connectors to integrate with other electronic components and devices. Connectors serve as electromechanical interfaces that enable quick and removable connection of a cable to a PCB or from one PCB to another. They provide both electrical contacts and mechanical components like housings and latches. Common types of connectors used on PCBs include:
Edge Connectors
Edge connectors are commonly used to connect a PCB to a motherboard or backplane in computers and other electronic devices. They consist of conductive pads, fingers, or pins on the edge of a PCB that insert into a mating socket or slot connector on the motherboard.
Advantages
- Provide compact and low-profile interconnections
- Allow easy insertion and removal of PCBs
- Available in standard layouts and pitches for compatibility
- Low cost compared to other connectors
Disadvantages
- Vulnerable to wear, contamination, and damage
- Limited contact density compared to some other connectors
- Require proper alignment and insertion force
- Not suitable for frequent mating cycles
Types
- Single row: One set of contacts on one edge of the PCB
- Dual row: Two sets of contacts on opposite edges of the PCB
- Stamped: Contacts stamped from sheet metal into housing
- Printed: Etched directly onto the PCB
Common pitches: 1.27mm, 2.00mm, 2.54mm
Number of contacts can range from under 10 to over 100. Standard layouts available including PCI, PCIe, SO-DIMM, etc.
Header Connectors
Header connectors (or pin headers) provide an array of protruding pins that mate with socket connectors. They allow interfacing between PCBs or from cables to PCBs.
Advantages
- Allow direct soldering to PCB
- Variety of layouts and pitches available
- Durable when mated properly
- Economical and simple to implement
Disadvantages
- Not ideal for high mate/unmate cycles
- Exposed pins susceptible to bending or other damage
- May require polarity keys for proper orientation
Types
- Single row (1xN): One row of pins
- Dual row (2xN): Two parallel rows of pins
- Right angle: Pins bent 90 degrees
- Shrouded: Plastic housing around pins for alignment
Common pitches: 2.54 mm, 2.00 mm, 1.27 mm, 1.00 mm
Number of pins from 2 to 50+. Double density versions with offset rows. Standard layouts like USB, HDMI, etc.
Board-to-Board Connectors
Board-to-board connectors provide removable connections between PCBs using mating connectors on each board. This allows boards to be joined together to expand function, but separated again for serviceability.
Advantages
- Allow connections between different PCBs
- High reliability with positive retention
- No soldering required
- Available in many layouts, pitches and sizes
Disadvantages
- Higher cost than headers/edges
- Only viable when frequent mating required
- Requires connectors on both boards
- Significant space requirements
Types
- Mezzanine/stacking: 90° orientation of PCBs
- Hinge: Variable angular adjustment of PCBs
- Surface mount: Low profile direct mounting
- Compliant pin: Pins flex for tolerance absorption
- High speed: Impedance matched for signals up to 25+ Gb/s
Pitches from 1.27mm to 2.54mm. Number of contacts from 10 to over 100. Standard layouts like board-to-board PCIe, LVDS, etc.
Card Edge Connectors
Card edge connectors have insulating housings with slotted cavities that receive the edge of a PCB. The PCB has exposed metallic tabs or pads that make contact with springs or pins inside the connector cavity. They provide demountable connections for expansion cards like GPUs.
Advantages
- Allow insertion/removal of cards without cables
- Wipe electrical contacts for reliable connections
- Keying options to ensure proper orientation
- Available in standard layouts (PCIe, memory, etc)
Disadvantages
- Only compatible with PCB cards, not cables
- Vulnerable to wear and damage over mating cycles
- Fixed orientation once inserted
- Significant insertion and extraction forces
Types
- Solder mount: Soldered terminations
- Press-fit: Pins press-fit into plated through holes
- Surface mount: Soldered to surface pads on PCB
- Right-angle: Side insertion of card edge
Pitches from 1.27mm to 2.54mm. Number of contacts from 20 to over 100. Standard layouts like PCIe x16, SD Card, etc.
Circular Connectors
Circular connectors use cylindrical housings that mate with circular plugs or receptacles. This provides a secure mechanical coupling and reliable environmental sealing for regular mating/unmating. Common types of circular connectors include:
- D-subminiature (DE-9, DE-15, etc)
- USB
- DC power
- Coaxial (BNC, TNC, etc)
Advantages
- Strong mating and environmental sealing
- Allows frequent matings without damage
- Variety of contact types and arrangements
- Rugged and durable materials available
- Locking features to prevent vibration/moisture issues
Disadvantages
- Larger footprint than low profile connectors
- More complex parts and assembly
- Specific gendered mating interfaces
- Generally higher cost
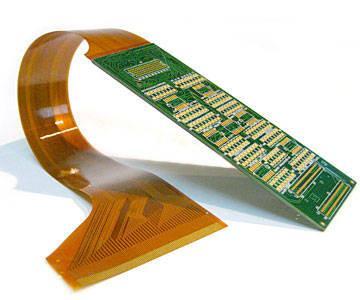
FFC/FPC Connectors
FFC (Flat Flexible Cable) and FPC (Flat Flex Printed Circuit) connectors allow connections from flexible thin ribbon cables to rigid PCBs. The flexible cable inserts into a plastic connector housing clipped onto the PCB. Metal tabs or springs within the housing grasp conductive pads on the cable to make electrical contact.
Advantages
- Compact and space saving
- Allows movable interconnections
- Simple mating by cable insertion
- Lower assembly cost
- Fine pitch capabilities
Disadvantages
- Lower current and density than other connectors
- Cable can degrade over repeated flexing
- Less ruggedized than circular connectors
- Limited mainly to internal connections
Common pitches from 0.5mm to 2.0mm. Number of positions from 10 to over 100. Single and dual row models. Zero insertion force and low insertion force types.
Terminal Blocks
Terminal blocks provide termination points for connecting cables and wires to a PCB. The PCB has metal pads, holes, or surface mounts that attach to screw terminals, spring clips, or insulation displacement slots on the terminal block. This allows tool-free field wiring.
Advantages
- Allow easy connection of field cables and wires
- Variety of termination styles
- Printing capabilites for circuit identification
- Rugged insulated housings
- Simplifies prototyping and deployment
Disadvantages
- Larger footprint than soldered connections
- Limited density and circuit count
- Not ideal for complex cabling
- Generally used for simpler I/O wiring
Standard spacing between 5mm to 10mm. Feedthrough, jumper, ground, and fused types available. Often used for power inputs, sensors, analog I/O, etc.
Application Specific Connectors
In addition to general connector types, application specific connnectors are designed to meet the interface needs of particular devices and industries:
- USB – Type A, B Mini, Micro, and C connectors. Used for peripheral devices.
- HDMI – 19 pin compact multimedia interface. Used for video and audio.
- RJ45 – 8P8C connectors used for Ethernet networks.
- D-Sub – DE-9 and DE-15 connectors used for RS-232, VGA, etc.
- Memory – DIMM, SODIMM, and other modules. Used for RAM expansion.
- Automotive – A wide array of circular and rectangular connectors to handle automotive environments.
These provide standardized interfaces tailored for their specific applications.
Choosing a Connector
Key considerations when selecting a connector for a PCB design include:
- Function – What devices need to interface with the board?
- Signal types – Data speeds, frequencies, voltages, etc.
- Environment – Vibration, moisture, temperature, etc.
- Mating cycles – Frequency of connection and disconnection.
- Currents and density – Number of contacts and currents per contact.
- Orientation – Which directions the connectors need to mate.
- Mounting – Through-hole or surface mount.
- Standards – Compatibility requirements.
- Cost – Component cost, assembly cost, long term maintenance.
Analyzing these factors helps narrow the selection to connectors that can provide the right functionality, performance, and reliability needed for the particular application.
Connector Manufacturers
Some of the major manufacturers that produce a wide range of connectors for PCBs include:
- TE Connectivity
- Molex
- JST
- Samtec
- Hirose Electric
- Amphenol
- JAE Electronics
- Foxconn
- 3M
These companies offer extensive connector product lines covering everything from simple wire-to-board options to rugged high speed interfaces. They provide detailed specifications, 3D models, and other resources to aid in the connector selection and PCB design process.
Connector Interfaces
There are some standard interfaces used by many connectors that designers should be familiar with:
PCI Express (PCIe)
- Serial computer expansion bus standard
- Uses lanes with differential pairs operating at 2.5/5/8/16 Gbps
- Connectors have x1, x4, x8, x16 lane configurations
- Edge connectors, card edge slots, board-to-board
DDR Memory
- Double data rate synchronous DRAM standard
- High speed with data clocked on rising and falling edges
- Speeds up to DDR4-3200 and beyond
- DIMM, SODIMM, RDIMM connectors
USB
- Universal Serial Bus for peripherals
- USB 1.0/2.0 speeds up to 480 Mbps
- USB 3.0 up to 5 Gbps
- USB 4.0 based on Thunderbolt protocol
- Type A/B plugs, Micro, Mini, USB-C ports
HDMI
- High Definition Multimedia Interface
- Supports video and audio over a single cable
- 19-pin Type A/B connectors
- Bandwidth up to 48 Gbps
Ethernet
- Based on IEEE 802.3 standards
- Speeds up to 10 Gbps, 25 Gbps, 40 Gbps, 100 Gbps
- Uses RJ45 connectors, SFP ports
Following standard connector specifications makes it easier to integrate common interfaces into a design.
Design Considerations
Here are some key points that PCB designers need to consider when incorporating connectors in their layouts:
Schematics – Capture all connector pins and required support circuitry like ESD protection, filters, etc.
Component Footprints – Use recommended land patterns from manufacturer datasheets for each connector.
Interfaces – Ensure connector layout matches interface specs like PCIe, USB, HDMI pinouts.
Spacing – Leave adequate space around connectors for mating clearances.
Height – Account for connector height to avoid collisions with nearby components.
Routing – Carefully route differential pairs, control impedances, minimize crosstalk.
Assembly – Design robust mechanical attachments like screws, snaps, or adhesives.
Test Points – Provide test points to validate voltages and signals at connectors.
Paying attention to these aspects helps create effective, manufacturable connector implementations.
Connector Reliability and Testing
Connectors play a vital role in system reliability. Failure of a connector can lead to full system failure. Important reliability factors include:
- Contact resistance – Should maintain low stable contact resistance.
- Insulation resistance – Prevent shorting between adjacent contacts.
- Mating durability – Withstand repeated insertion cycles without damage.
- Vibration resistance – Maintain integrity under vibration stress.
- Temperature cycling – Perform across full operating temperature range.
- Contamination – Avoid issues with fluid ingress, particles, etc.
- Mixed signal connections – Prevent crosstalk between digital and analog signals.
Thorough testing across these parameters is required to validate connector design robustness. Common connector tests include:
- Contact resistance – 4-wire Kelvin method
- Insulation resistance – 500VDC megohmmeter
- Durability – 100s to 100,000s of mating cycles
- Vibration – 10-60Hz up to 10G loads
- Thermal cycling – e.g. -40°C to 105°C
- Mixed signal crosstalk – Time domain reflectometer
- Environmental – salt spray, humidity, etc.
Failing any criteria requires connector redesign or alternative selection. Rigorous testing ensures connectors meet application demands.
Conclusion
Connectors perform the critical task of interfacing PCBs to external components, boards, and cables. The wide variety of connector types offers solutions tailored for diverse applications and environments. Connector implementation has a major impact on the overall manufacturability and reliability of a PCB assembly. Following best practices for selection, design, and testing helps ensure connectors provide the connectivity and durability needed to keep systems functioning reliably over their target lifespan. As PCB technology continues advancing into higher speeds and denser designs, connector evolution will also be at the forefront enabling these developments through progressively more sophisticated interconnection solutions.
FQA
What are the main advantages of board-to-board connectors?
Some key advantages of board-to-board connectors include:
- Allow connections between different PCBs
- High reliability with positive retention
- No soldering required
- Available in many layouts, pitches and sizes
Board-to-board connectors provide a removable interconnection between PCB assemblies, expanding functionality while maintaining serviceability.
How is impedance controlled in PCB connectors?
For high-speed signals, connectors must match the impedance of the transmission line on the PCB. Common techniques include:
- Ground planes adjacent to signal pins
- Specific dielectric materials between pins
- Controlled dimensions of pins/contacts
- Impedance-matched transmission lines on PCB
This minimizes discontinuities and prevents signal reflections at the connector interfaces.
What is a compliant pin connector?
Compliant pin connectors use flexible pins that can flex slightly to absorb tolerance variations when mated to the receiving connector or PCB. This provides reliable interconnect despite minor deviations in mating components. Useful for board-to-board applications.
How can crosstalk be reduced in mixed-signal connectors?
Strategies to reduce crosstalk in mixed-signal connectors include:
- Ground pins placed between analog and digital signals
- Shielded connector housings
- Differential pair routing of digital signals
- Separate connectors for analog and digital
This prevents coupling between sensitive analog signals and noisy digital signals.
What testing is used to validate connector durability?
Connector durability is typically validated by mating cycle testing. The connector pair is inserted and removed for hundreds to thousands of cycles, sometimes while monitoring contact resistance. This verifies the connector can withstand repeated mating without degradation in performance.
Leave a Reply