Smaller PCB Size and Higher Component Density
One of the most significant advantages of SMT is the ability to produce smaller PCBs with higher component density. Surface-mount components are much smaller than their through-hole counterparts, allowing for more efficient use of board space. This miniaturization enables the creation of compact, lightweight electronic devices that are highly portable and suitable for a wide range of applications.
Component Type | Size Comparison | PCB Area Utilization |
---|---|---|
Through-hole | Larger | Lower |
Surface-mount | Smaller | Higher |
The smaller size of surface-mount components also allows for higher component density on the PCB. By placing components on both sides of the board and using fine-pitch packages, manufacturers can achieve a much higher number of components per square inch compared to through-hole technology. This increased density enables more complex and feature-rich designs within a smaller footprint.
Improved PCB Performance and Reliability
SMT offers several performance and reliability advantages over THT:
Reduced Parasitic Effects
Surface-mount components have shorter leads and are placed closer to the PCB surface, resulting in reduced parasitic inductance and capacitance. This reduction in parasitic effects improves signal integrity and allows for higher-frequency operation, making SMT ideal for high-speed digital circuits and RF applications.
Better Mechanical Stability
Surface-mount components are securely attached to the PCB using solder paste and a reflow soldering process. This strong mechanical bond enhances the overall stability and durability of the assembly, making it more resistant to vibration and shock. The improved mechanical stability is particularly beneficial for devices exposed to harsh environments or high levels of stress.
Enhanced Thermal Management
SMT allows for better thermal management compared to THT. The smaller size and lower profile of surface-mount components facilitate more efficient heat dissipation, as the heat can be quickly conducted away from the component and into the PCB. Additionally, the absence of through-holes reduces the thermal resistance between the component and the board, further improving heat transfer.
Faster and More Efficient PCB Assembly
SMT enables faster and more efficient PCB assembly processes, leading to reduced manufacturing time and costs.
Automated Assembly
SMT is highly compatible with automated assembly processes, such as pick-and-place machines and reflow soldering ovens. These automated systems can quickly and accurately place components on the PCB, significantly reducing the time and labor required for assembly. Automated assembly also minimizes the risk of human error, resulting in more consistent and reliable PCBs.
Simultaneous Component Placement
With SMT, multiple components can be placed on the PCB simultaneously using a single machine. This parallel processing capability greatly increases the assembly throughput compared to the sequential placement required for through-hole components. The ability to handle multiple components at once streamlines the assembly process and reduces the overall manufacturing time.
Reduced Manual Labor
SMT reduces the need for manual labor in PCB assembly. While through-hole components require manual insertion and soldering, surface-mount components can be placed and soldered automatically. This reduction in manual labor not only saves time but also lowers the associated labor costs, making SMT a more cost-effective option for high-volume production.
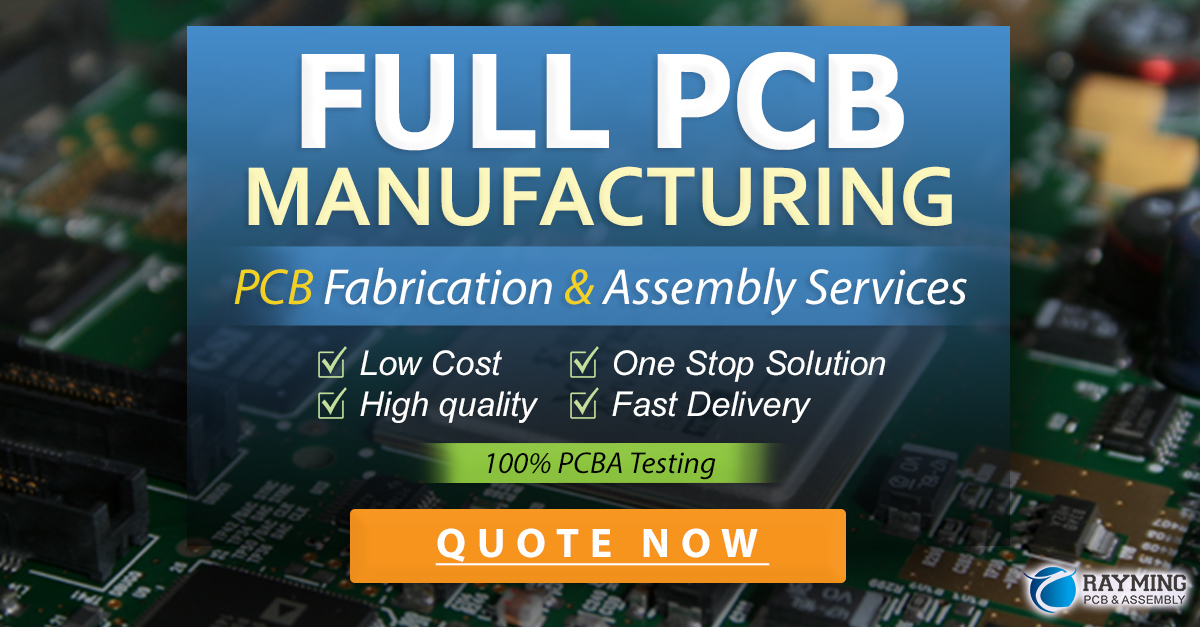
Cost Savings in PCB Manufacturing
Implementing SMT in PCB manufacturing offers several cost-saving benefits:
Lower Material Costs
Surface-mount components are generally less expensive than their through-hole equivalents due to their smaller size and simpler packaging. Additionally, SMT requires less PCB material because of the smaller board size and the absence of through-holes. These factors contribute to lower overall material costs for SMT-based PCBs.
Reduced Assembly Time and Labor Costs
As mentioned earlier, SMT enables faster and more automated assembly processes, which significantly reduce the time and labor required for PCB manufacturing. The shorter assembly time and lower labor costs translate into cost savings for the manufacturer, making SMT a more economical choice for high-volume production runs.
Improved Inventory Management
SMT components are smaller and more standardized than through-hole components, making them easier to store and manage. The compact size of surface-mount components allows for more efficient use of storage space, reducing inventory costs. Furthermore, the standardization of SMT packages simplifies component sourcing and minimizes the risk of obsolescence, leading to better inventory management and cost control.
Environmental Benefits of SMT
SMT offers several environmental benefits compared to THT:
Reduced Material Waste
The smaller size of surface-mount components and the elimination of through-holes in SMT PCBs result in less material waste during manufacturing. This reduction in waste helps conserve resources and minimizes the environmental impact of PCB production.
Lower Energy Consumption
SMT assembly processes, such as reflow soldering, consume less energy compared to the wave soldering used for through-hole components. The lower energy consumption not only reduces manufacturing costs but also contributes to a smaller carbon footprint and a more environmentally friendly production process.
Compliance with Environmental Regulations
SMT-based PCBs are more likely to comply with environmental regulations, such as the Restriction of Hazardous Substances (RoHS) directive. Surface-mount components are available in RoHS-compliant versions, making it easier for manufacturers to produce PCBs that meet the required environmental standards.
Frequently Asked Questions (FAQ)
1. What is the difference between SMT and THT?
SMT (Surface-Mount Technology) and THT (Through-Hole Technology) are two different methods of mounting components on a PCB. In SMT, components are placed directly on the surface of the board and soldered using a reflow process. In THT, components have long leads that are inserted through holes in the PCB and soldered on the opposite side.
2. Can SMT and THT components be used on the same PCB?
Yes, it is possible to use both SMT and THT components on the same PCB. This combination is known as a mixed-technology or hybrid assembly. However, it is essential to consider the different assembly processes required for each technology and ensure compatibility between the components and the PCB design.
3. Are there any disadvantages to using SMT?
While SMT offers numerous advantages, there are a few potential disadvantages to consider. SMT components can be more sensitive to thermal stress during the reflow soldering process, requiring careful temperature control. Additionally, manual rework and repair of SMT components can be more challenging due to their small size and close spacing.
4. Is SMT suitable for low-volume production?
Although SMT is often associated with high-volume production, it can also be cost-effective for low-volume runs. The automated nature of SMT assembly processes reduces the setup time and labor costs, making it a viable option even for smaller production quantities. However, the cost-effectiveness of SMT for low-volume production depends on factors such as the specific components, PCB complexity, and available assembly equipment.
5. How does SMT impact PCB design considerations?
When designing a PCB for SMT, several factors need to be considered to ensure optimal manufacturability and reliability. These include component selection, pad sizing and spacing, solder mask design, and thermal management. It is essential to follow SMT design guidelines and work closely with the PCB manufacturer to ensure a successful SMT assembly process.
In conclusion, the advantages of PCB SMT are numerous and far-reaching. From smaller PCB sizes and higher component density to improved performance, faster assembly, cost savings, and environmental benefits, SMT has transformed the PCB manufacturing industry. As technology continues to advance, SMT will remain a crucial enabler for the development of innovative, compact, and reliable electronic devices across a wide range of applications.
Leave a Reply