What is PCB Panelization?
PCB panelization is the process of arranging multiple printed circuit board designs on a single panel for manufacturing. This technique is used to optimize the production process, reduce costs, and improve efficiency. By grouping several PCBs together, manufacturers can produce a larger number of boards in a single run, minimizing material waste and setup time.
Benefits of PCB Panelization
- Cost reduction
- Improved efficiency
- Reduced material waste
- Faster production times
- Consistent quality
The 8 Importance of PCB Panelization
1. Cost Savings
One of the primary reasons for using PCB panelization is the significant cost savings it offers. By producing multiple PCBs on a single panel, manufacturers can reduce the overall cost per board. This is achieved through:
- Reduced material waste
- Minimized setup time
- Optimized use of production equipment
Panelization | Cost per Board |
---|---|
No | $10 |
Yes | $7 |
As seen in the table above, panelization can lead to a 30% reduction in the cost per board.
2. Improved Efficiency
PCB panelization streamlines the manufacturing process, resulting in improved efficiency. By grouping multiple boards together, manufacturers can:
- Reduce handling time
- Minimize the number of setups required
- Optimize the use of production equipment
This improved efficiency translates to faster production times and increased output.
3. Reduced Material Waste
When producing individual PCBs, there is often a significant amount of material waste due to the spacing required between boards. PCB panelization helps to minimize this waste by:
- Optimizing the layout of boards on the panel
- Reducing the spacing between boards
- Utilizing the maximum available space on the panel
Panelization | Material Utilization |
---|---|
No | 70% |
Yes | 90% |
The table above demonstrates how panelization can improve material utilization by up to 20%.
4. Faster Production Times
PCB panelization enables manufacturers to produce a larger number of boards in a single production run. This leads to faster overall production times, as:
- Setup time is reduced
- Handling time is minimized
- Production equipment is used more efficiently
Faster production times mean that manufacturers can deliver finished products to their customers more quickly.
5. Consistent Quality
By producing multiple PCBs on a single panel, manufacturers can ensure consistent quality across all boards. This is because:
- All boards are subjected to the same production conditions
- Any issues with the panel will affect all boards equally
- Quality control measures can be applied uniformly
Consistent quality is essential for ensuring the reliability and performance of the final product.
6. Simplified Handling
PCB panelization simplifies the handling of boards throughout the manufacturing process. Instead of dealing with individual boards, operators can:
- Handle entire panels
- Use automated equipment for panel handling
- Minimize the risk of damage to individual boards
Simplified handling reduces the likelihood of human error and improves the overall efficiency of the production process.
7. Compatibility with Automated Assembly
Many modern PCB assembly processes rely on automated equipment to place components and solder boards. PCB panelization ensures compatibility with these automated systems by:
- Providing a standardized panel size
- Incorporating fiducial marks for machine vision systems
- Including breakaway tabs or mousebites for easy depanelization
Compatibility with automated assembly is crucial for high-volume production and ensures that the manufacturing process remains efficient and cost-effective.
8. Flexibility in Design
PCB panelization offers flexibility in the design of individual boards. Manufacturers can:
- Combine different board designs on a single panel
- Incorporate test coupons or other features
- Optimize the layout for maximum material utilization
This flexibility allows for the production of a wide range of PCB designs while still benefiting from the advantages of panelization.
FAQ
-
Q: What is the minimum number of PCBs required for panelization to be cost-effective?
A: The minimum number of PCBs required for panelization to be cost-effective varies depending on factors such as board size, complexity, and production volume. Generally, panelization becomes advantageous when producing at least 10-20 boards per panel. -
Q: Can different PCB designs be combined on a single panel?
A: Yes, different PCB designs can be combined on a single panel, provided they share similar characteristics such as board thickness, material, and surface finish. This allows for greater flexibility in production and can further reduce costs. -
Q: How are individual boards separated from the panel after production?
A: Individual boards are typically separated from the panel using a process called depanelization. This can be done through methods such as: - V-scoring: Creating grooves along the board edges for easy separation
- Tab routing: Adding breakaway tabs that can be snapped off
-
Mousebites: Creating perforations along the board edges for separation
-
Q: Can panelization be used for both through-hole and surface-mount PCBs?
A: Yes, panelization can be used for both through-hole and surface-mount PCBs. The specific panelization techniques and considerations may vary depending on the type of components and assembly process used. -
Q: Are there any limitations to the size of panels used in PCB panelization?
A: The size of panels used in PCB panelization is typically limited by the capabilities of the production equipment. Most manufacturers have standard panel sizes that they work with, such as 18″ x 24″ or 21″ x 24″. It is important to consult with the manufacturer to determine the optimal panel size for a given project.
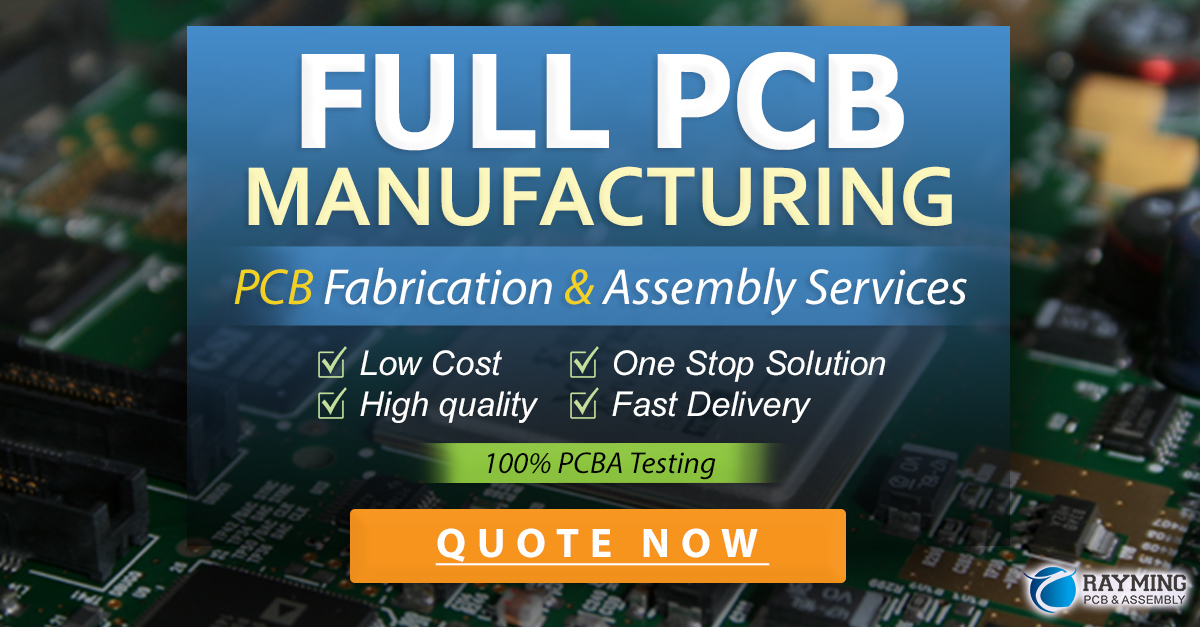
Conclusion
PCB panelization is a critical aspect of the PCB manufacturing process, offering numerous benefits that include cost savings, improved efficiency, reduced material waste, faster production times, consistent quality, simplified handling, compatibility with automated assembly, and flexibility in design. By understanding the importance of PCB panelization, designers and manufacturers can optimize their production processes and deliver high-quality products to their customers more efficiently and cost-effectively.
Leave a Reply