Understanding PCB Conductivity
PCB conductivity refers to the ability of a PCB to allow electrical current to flow through its various components, including vias and traces. The conductivity of a PCB is determined by several factors, such as the material used for the conductive layers, the thickness of the copper, and the geometry of the vias and traces.
Factors Affecting PCB Conductivity
-
Material Selection: The choice of material for the conductive layers of a PCB plays a significant role in determining its conductivity. Copper is the most commonly used material due to its excellent electrical conductivity and relatively low cost. Other materials, such as silver and gold, offer even better conductivity but are more expensive and are typically used in specialized applications.
-
Copper Thickness: The thickness of the copper layer on a PCB directly impacts its conductivity. Thicker copper layers provide lower resistance and higher current-carrying capacity. The standard copper thickness for PCBs ranges from 0.5 oz to 2 oz per square foot, with 1 oz being the most common.
-
Via and Trace Geometry: The size, shape, and spacing of vias and traces on a PCB also influence its conductivity. Wider traces and larger via diameters allow for better current flow, while narrower traces and smaller vias can increase resistance and limit current-carrying capacity.
Vias: The Vertical Conductors
Vias are small, plated holes that provide electrical connections between different layers of a PCB. They allow signals to travel vertically through the board, enabling more complex routing and reducing the overall size of the PCB.
Types of Vias
-
Through-hole Vias: These vias extend through all layers of the PCB and are typically used for mounting through-hole components or providing structural support.
-
Blind Vias: Blind vias connect an outer layer to an inner layer, but do not extend through the entire thickness of the PCB.
-
Buried Vias: Buried vias are located entirely within the inner layers of a PCB and do not connect to either of the outer layers.
-
Microvias: Microvias are small, laser-drilled vias that are used for high-density interconnects in advanced PCB designs.
Via Conductivity
The conductivity of a via depends on several factors, including:
-
Via Diameter: Larger via diameters provide lower resistance and higher current-carrying capacity.
-
Via Plating: The thickness and quality of the copper plating inside the via directly impact its conductivity.
-
Via Fill: Filling vias with conductive materials, such as copper or conductive epoxy, can enhance their conductivity and improve thermal management.
Traces: The Horizontal Highways
Traces are the thin, conductive paths that carry electrical signals horizontally across the layers of a PCB. They are typically made of copper and are etched onto the PCB substrate using a photolithographic process.
Trace Conductivity
The conductivity of a trace is influenced by several factors, including:
-
Trace Width: Wider traces have lower resistance and can carry more current than narrower traces.
-
Trace Thickness: As with copper thickness, thicker traces provide better conductivity and current-carrying capacity.
-
Trace Length: Longer traces have higher resistance than shorter traces, which can impact signal integrity and power delivery.
Trace Design Considerations
When designing traces on a PCB, several factors must be taken into account to ensure optimal conductivity and signal integrity:
-
Current-Carrying Capacity: Traces must be sized appropriately to handle the expected current flow without overheating or causing voltage drops.
-
High-Speed Signals: Traces carrying high-speed signals must be designed to minimize reflections, crosstalk, and other signal integrity issues.
-
Impedance Control: Traces that require precise impedance control, such as those used in high-speed digital interfaces or RF applications, must be carefully designed and spaced to maintain the desired impedance.
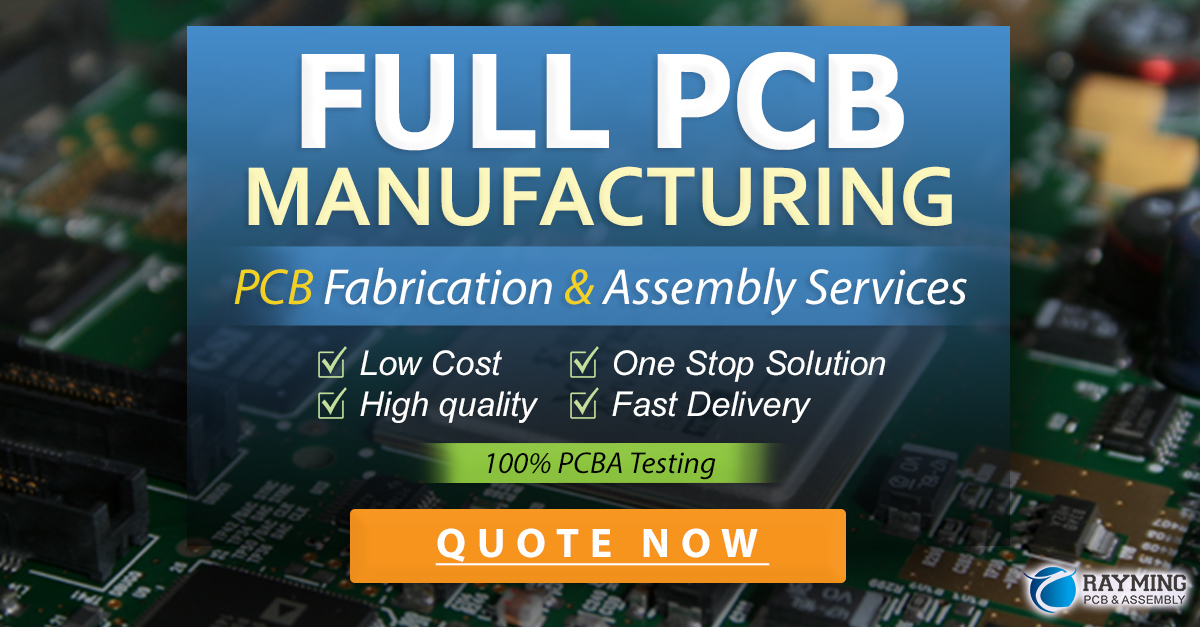
Enhancing PCB Conductivity
There are several methods for improving the conductivity of vias and traces on a PCB:
-
Increasing Copper Thickness: Using thicker copper layers can reduce resistance and improve current-carrying capacity.
-
Optimizing Via and Trace Geometry: Carefully designing the size, shape, and spacing of vias and traces can minimize resistance and improve signal integrity.
-
Using High-Quality Materials: Choosing high-quality PCB substrates and copper foils can ensure consistent conductivity and reliability.
-
Employing Advanced Manufacturing Techniques: Techniques such as high-density interconnect (HDI) and sequential build-up (SBU) can enable the creation of smaller, more conductive vias and traces.
PCB Conductivity Testing
To ensure that a PCB meets the required conductivity specifications, various testing methods can be employed:
-
Resistance Testing: Measuring the resistance of vias and traces using a multimeter or dedicated resistance tester can help identify any high-resistance or open-circuit issues.
-
Continuity Testing: Verifying the continuity of electrical connections between different points on a PCB can ensure that signals are being properly conducted.
-
Time-Domain Reflectometry (TDR): TDR testing can be used to characterize the impedance and signal integrity of traces, helping to identify any discontinuities or reflections.
Frequently Asked Questions (FAQ)
- What is the most common material used for PCB traces and vias?
Copper is the most widely used material for PCB traces and vias due to its excellent electrical conductivity and relatively low cost.
- How does copper thickness affect PCB conductivity?
Thicker copper layers provide lower resistance and higher current-carrying capacity, improving the overall conductivity of the PCB.
- What are microvias, and how do they differ from traditional vias?
Microvias are small, laser-drilled vias that are used for high-density interconnects in advanced PCB designs. They are typically smaller than traditional vias and can be used to create more complex routing patterns.
- How can I ensure that my PCB traces have the proper impedance?
To ensure proper impedance control, traces must be carefully designed and spaced according to the specific requirements of the application. This may involve adjusting trace width, spacing, and dielectric thickness to achieve the desired impedance.
- What testing methods can be used to verify PCB conductivity?
PCB conductivity can be tested using various methods, including resistance testing, continuity testing, and time-domain reflectometry (TDR). These tests can help identify any high-resistance, open-circuit, or signal integrity issues that may impact the performance of the PCB.
Factor | Impact on Conductivity |
---|---|
Material Selection | Copper is the most common material due to its excellent electrical conductivity and low cost. |
Copper Thickness | Thicker copper layers provide lower resistance and higher current-carrying capacity. |
Via and Trace Geometry | Larger via diameters and wider traces offer better conductivity and current-carrying capacity. |
Via Plating | The thickness and quality of the copper plating inside the via directly impact its conductivity. |
Trace Length | Longer traces have higher resistance than shorter traces, which can impact signal integrity and power delivery. |
In conclusion, the conductivity of vias and traces on a PCB is a critical factor in ensuring the proper functioning and reliability of electronic devices. By understanding the factors that influence PCB conductivity and employing appropriate design, manufacturing, and testing techniques, engineers can create PCBs that meet the demanding requirements of today’s advanced electronic applications.
Leave a Reply