Introduction to PCB Electrical Tests
Printed Circuit Boards (PCBs) are essential components in modern electronic devices. To ensure their reliability and performance, various electrical tests are conducted during the manufacturing process. These tests help identify defects, verify functionality, and ensure compliance with industry standards. In this article, we will explore the different types of electrical tests performed on PCBs and their significance in delivering high-quality products.
The Importance of PCB Electrical Testing
PCB electrical testing is crucial for several reasons:
- Quality Assurance: Electrical tests help identify defects and manufacturing issues, ensuring that only high-quality PCBs are released to the market.
- Reliability: By conducting thorough electrical tests, manufacturers can ensure that PCBs will function reliably under various operating conditions.
- Safety: Electrical tests help prevent potential safety hazards, such as short circuits or overheating, which could lead to device failures or even fire hazards.
- Compliance: Many industries have specific standards and regulations for PCBs. Electrical testing ensures that PCBs meet these requirements, making them suitable for use in various applications.
Common Types of PCB Electrical Tests
Continuity Test
A continuity test is performed to verify that all the intended connections on a PCB are intact and that there are no unintended short circuits. This test is typically conducted using a multimeter or a dedicated Continuity Tester. The tester applies a small voltage across each connection and checks for the presence of a conductive path.
Continuity Test Procedure
- Set the multimeter to the continuity test mode.
- Place the probes on the two points of the connection being tested.
- If the multimeter beeps or indicates a low resistance, the connection is continuous.
- Repeat the process for all the connections on the PCB.
Isolation Test
An isolation test, also known as an insulation resistance test, is performed to ensure that there are no unintended conductive paths between different parts of the PCB. This test helps identify potential leakage currents or short circuits that could lead to device malfunction or safety hazards.
Isolation Test Procedure
- Set the multimeter to the insulation resistance test mode.
- Connect one probe to the ground plane or a common point on the PCB.
- Touch the other probe to various points on the PCB where isolation is required.
- The multimeter should indicate a high resistance value (typically in the range of megaohms) if the isolation is adequate.
Voltage Test
A voltage test is conducted to verify that the PCB is receiving the correct voltage levels at various points. This test helps ensure that the PCB will function correctly when powered up and that there are no issues with the power supply or voltage regulation circuitry.
Voltage Test Procedure
- Set the multimeter to the voltage measurement mode.
- Connect the probes to the appropriate test points on the PCB.
- Check the voltage readings against the expected values specified in the PCB design.
- Repeat the process for all the critical voltage points on the PCB.
Current Test
A current test is performed to measure the amount of current flowing through specific paths on the PCB. This test helps identify any excessive current draw or potential short circuits that could damage components or cause overheating.
Current Test Procedure
- Set the multimeter to the current measurement mode.
- Connect the multimeter in series with the path being tested.
- Apply power to the PCB and measure the current flow.
- Compare the measured current values with the expected values specified in the PCB design.
Functional Test
A functional test is conducted to verify that the PCB performs its intended functions correctly. This test involves powering up the PCB and testing its various features, such as inputs, outputs, communication interfaces, and signal processing capabilities.
Functional Test Procedure
- Connect the PCB to the appropriate power supply and test equipment.
- Apply the necessary inputs or stimuli to the PCB.
- Monitor the outputs and behavior of the PCB to ensure they match the expected functionality.
- Test all the features and operating modes of the PCB as specified in the design.
Boundary Scan Test
Boundary scan testing, also known as JTAG (Joint Test Action Group) testing, is an advanced technique used to test complex PCBs with high component density. This test uses a special test access port (TAP) and boundary scan cells to control and observe the inputs and outputs of individual components on the PCB.
Boundary Scan Test Procedure
- Design the PCB with boundary scan capabilities, including the TAP and boundary scan cells.
- Connect the PCB to a boundary scan test system.
- Use the test system to control the inputs and outputs of the components through the boundary scan cells.
- Verify the functionality and interconnections of the components by analyzing the test results.
In-Circuit Test (ICT)
In-Circuit Testing (ICT) is a comprehensive test method that involves directly probing the PCB to measure the performance of individual components and their interconnections. ICT requires a dedicated test fixture with probes that make contact with specific test points on the PCB.
In-Circuit Test Procedure
- Design the PCB with test points accessible for probing.
- Develop a test fixture with probes that match the test points on the PCB.
- Place the PCB in the test fixture and apply the necessary test signals.
- Measure the response of the components and compare them with the expected values.
- Identify any faulty components or interconnections based on the test results.
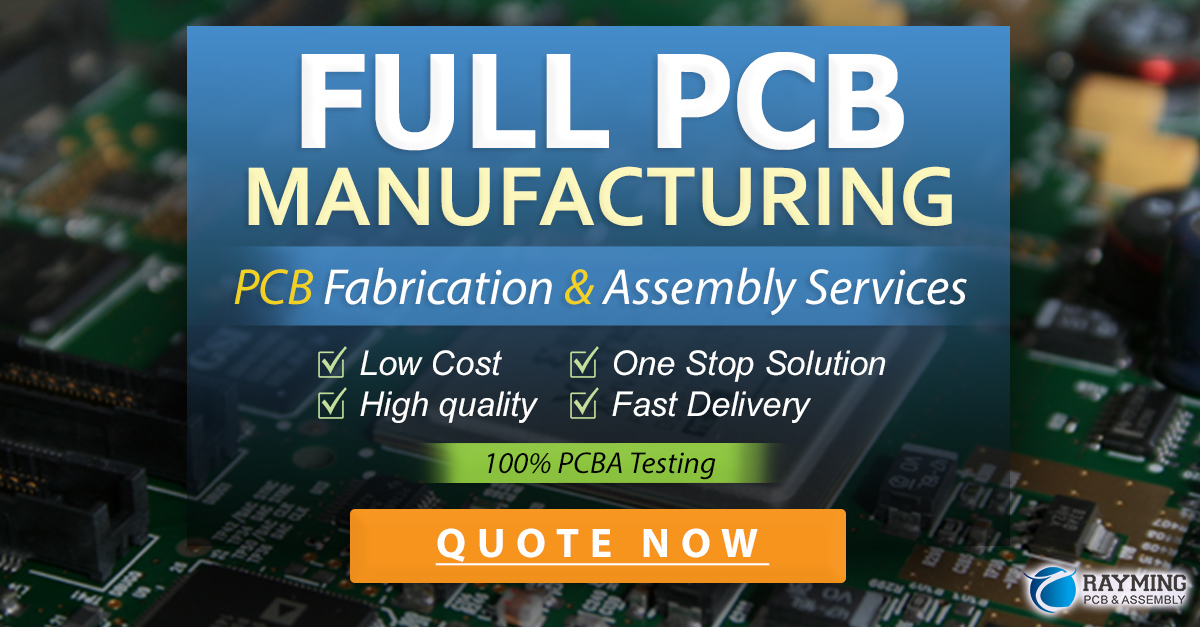
Advantages and Limitations of Different PCB Electrical Tests
Test Type | Advantages | Limitations |
---|---|---|
Continuity Test | Quick and simple to perform Identifies short circuits and open connections |
Limited to detecting continuity issues |
Isolation Test | Verifies electrical isolation between different parts of the PCB | May not detect all types of insulation failures |
Voltage Test | Ensures correct voltage levels at various points on the PCB | Limited to static voltage measurements |
Current Test | Identifies excessive current draw and potential short circuits | Requires interrupting the circuit to measure current |
Functional Test | Verifies the overall functionality of the PCB | May not detect all possible failure modes |
Boundary Scan Test | Enables testing of complex PCBs with high component density | Requires special design considerations and test equipment |
In-Circuit Test | Comprehensive testing of individual components and interconnections | Requires custom test fixtures and may be time-consuming |
Frequently Asked Questions (FAQ)
-
Q: What is the purpose of conducting electrical tests on PCBs?
A: Electrical tests on PCBs are conducted to ensure the quality, reliability, and functionality of the boards. These tests help identify defects, verify proper connections, and ensure compliance with industry standards. -
Q: How often should PCB electrical tests be performed?
A: PCB electrical tests should be performed at various stages of the manufacturing process, including prototyping, production, and final quality control. The frequency of testing depends on the complexity of the PCB and the specific requirements of the application. -
Q: Can PCB electrical tests be automated?
A: Yes, many PCB electrical tests can be automated using specialized test equipment and software. Automated testing helps improve efficiency, consistency, and throughput in the manufacturing process. -
Q: What are the consequences of not conducting proper PCB electrical tests?
A: Failing to conduct proper PCB electrical tests can lead to several issues, such as device malfunctions, reduced reliability, safety hazards, and non-compliance with industry standards. These issues can result in costly recalls, repairs, and damage to the manufacturer’s reputation. -
Q: How can I choose the right electrical tests for my PCB?
A: The choice of electrical tests depends on various factors, such as the complexity of the PCB, the application requirements, and the industry standards. It is recommended to consult with experienced PCB designers, test engineers, and industry experts to determine the most appropriate tests for your specific PCB.
Conclusion
PCB electrical testing is a critical aspect of ensuring the quality, reliability, and safety of electronic devices. By conducting various tests, such as continuity, isolation, voltage, current, functional, boundary scan, and in-circuit tests, manufacturers can identify defects, verify functionality, and ensure compliance with industry standards. Each test type has its own advantages and limitations, and the choice of tests depends on the specific requirements of the PCB and its application.
As PCBs continue to become more complex and integrated into a wide range of products, the importance of thorough electrical testing cannot be overstated. By investing in proper testing procedures and equipment, manufacturers can deliver high-quality PCBs that meet the demanding requirements of today’s electronic devices.
Leave a Reply