What is a Transparent PCB?
A transparent PCB is a printed circuit board that allows light to pass through its substrate material while maintaining its electrical conductivity and functionality. Unlike conventional PCBs that use opaque materials such as FR-4, transparent PCBs employ optically clear substrates, such as glass, polyethylene terephthalate (PET), or polyimide (PI). The conductive traces on these boards are typically made of transparent conductive materials, such as indium tin oxide (ITO) or silver nanowires (AgNWs).
The main advantage of transparent PCBs lies in their ability to integrate electronic components and circuitry seamlessly into devices that require high optical transmissivity, such as displays, touch screens, or light-emitting diode (LED) lighting systems. By allowing light to pass through the board, transparent PCBs enable the creation of more compact, lightweight, and visually appealing electronic devices.
Manufacturing Process of Transparent PCBs
The manufacturing process of transparent PCBs differs from that of traditional PCBs due to the unique properties of the materials involved. The general steps in the production of transparent PCBs are as follows:
-
Substrate preparation: The optically clear substrate, such as glass or PET, is cleaned and prepared for the subsequent steps. This may involve surface treatment to improve adhesion and reduce surface defects.
-
Conductive layer deposition: A transparent conductive material, such as ITO or AgNWs, is deposited onto the substrate using methods like sputtering, spin coating, or spray coating. The thickness and uniformity of the conductive layer are crucial for achieving the desired electrical and optical properties.
-
Patterning: The conductive layer is patterned into the desired circuit layout using photolithography or laser ablation techniques. This process involves applying a photoresist, exposing it to light through a mask, and developing the pattern.
-
Etching: The exposed areas of the conductive layer are etched away using chemical or physical methods, leaving behind the desired conductive traces.
-
Insulation and protection: A transparent insulating layer, such as a clear solder mask or a dielectric coating, is applied to protect the conductive traces and prevent short circuits.
-
Component assembly: Electronic components are attached to the transparent PCB using conductive adhesives or transparent solder materials. Special care is taken to ensure the compatibility of the components with the transparent substrate and conductive materials.
-
Testing and inspection: The assembled transparent PCB undergoes various tests to verify its electrical functionality, optical transmissivity, and mechanical integrity.
Materials Used in Transparent PCBs
The selection of materials for transparent PCBs is crucial to achieve the desired balance between electrical conductivity, optical transparency, and mechanical stability. Some of the commonly used materials in transparent PCBs include:
- Substrates:
- Glass: Borosilicate or soda-lime glass offers excellent optical clarity, dimensional stability, and high-temperature resistance. However, glass substrates are brittle and require careful handling during manufacturing and assembly.
- PET: Polyethylene terephthalate is a lightweight, flexible, and cost-effective substrate material. It offers good optical transparency and can be easily processed using roll-to-roll manufacturing techniques. PET is commonly used in flexible transparent PCBs for wearable devices and displays.
-
PI: Polyimide is a high-performance polymer that combines excellent thermal stability, mechanical strength, and optical transparency. PI substrates are suitable for applications that require high reliability and durability, such as in aerospace and automotive industries.
-
Conductive materials:
- ITO: Indium tin oxide is a widely used transparent conductive material due to its high optical transmittance and good electrical conductivity. ITO is typically deposited as a thin film using sputtering techniques and can be patterned using photolithography or laser ablation.
- AgNWs: Silver nanowires are an emerging alternative to ITO, offering comparable optical and electrical properties while being more flexible and less expensive. AgNWs can be deposited using solution-based methods, such as spin coating or spray coating, and can be patterned using various techniques, including photolithography, laser ablation, or direct writing.
-
PEDOT:PSS: Poly(3,4-ethylenedioxythiophene) polystyrene sulfonate is a transparent conductive polymer that offers high optical transparency and good electrical conductivity. PEDOT:PSS can be easily processed using solution-based methods and is suitable for flexible and stretchable transparent PCBs.
-
Insulating materials:
- Clear solder mask: A transparent solder mask is applied to protect the conductive traces and prevent short circuits. The solder mask should have good optical clarity, adhesion, and chemical resistance.
- Dielectric coatings: Transparent dielectric materials, such as acrylic or polyurethane, can be used to provide additional insulation and protection to the conductive traces. These coatings should have high optical transparency and good dielectric properties.
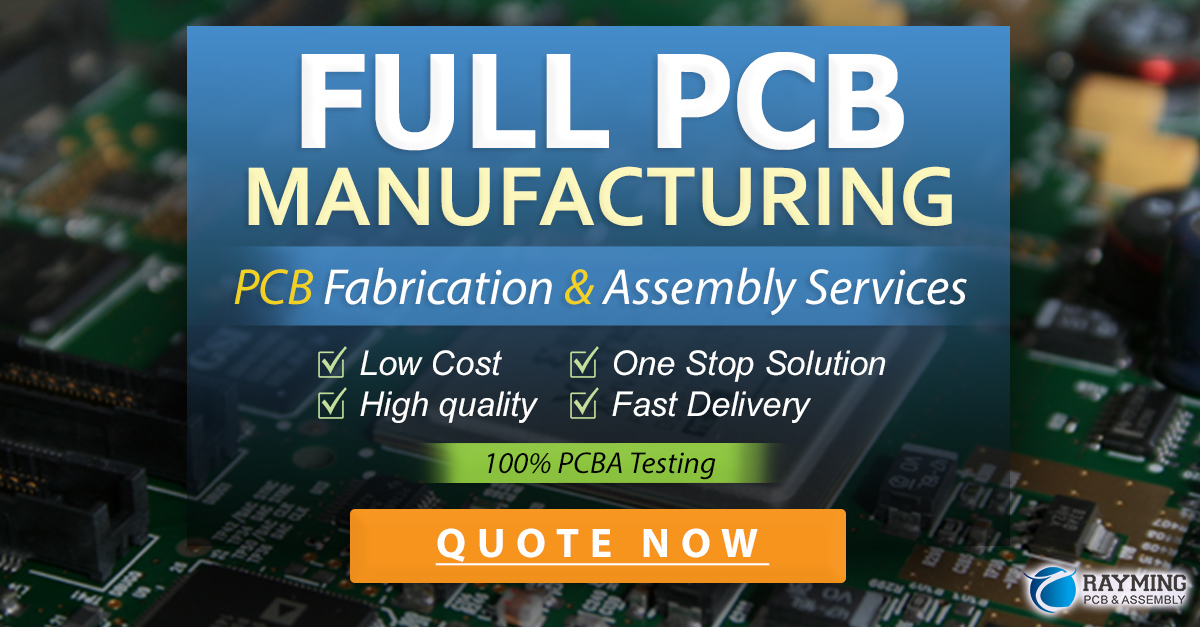
Advantages of Transparent PCBs
Transparent PCBs offer several advantages over traditional opaque PCBs, making them an attractive choice for various applications:
-
Optical transparency: The most obvious advantage of transparent PCBs is their ability to allow light to pass through the board, enabling the integration of electronic components with displays, touch screens, or lighting elements.
-
Design flexibility: Transparent PCBs offer greater design flexibility by allowing the placement of components and circuitry in areas that would otherwise be obscured by an opaque board. This enables the creation of more compact and visually appealing devices.
-
Improved aesthetics: The see-through nature of transparent PCBs enhances the visual appeal of electronic devices, making them more attractive to consumers. This is particularly important in consumer electronics, where aesthetics play a crucial role in product differentiation.
-
Reduced weight and thickness: By eliminating the need for separate display and touch panel layers, transparent PCBs can help reduce the overall weight and thickness of electronic devices. This is especially beneficial in portable and wearable devices, where size and weight are critical factors.
-
Enhanced durability: Some transparent PCB materials, such as glass and polyimide, offer excellent mechanical stability and resistance to environmental factors, such as temperature, humidity, and chemicals. This can lead to improved reliability and longer product lifetimes.
-
Potential for new applications: The unique properties of transparent PCBs open up new possibilities for innovative applications, such as transparent displays, interactive surfaces, or smart windows.
Applications of Transparent PCBs
Transparent PCBs find applications in various industries, ranging from consumer electronics to automotive and medical devices. Some of the potential applications include:
-
Displays and touch screens: Transparent PCBs can be integrated into displays and touch screens, enabling the creation of thinner, lighter, and more responsive devices. This is particularly relevant in smartphones, tablets, and wearable devices.
-
Automotive displays: Transparent PCBs can be used in automotive head-up displays (HUDs) and instrument clusters, providing essential information to drivers without obstructing their view.
-
Medical devices: Transparent PCBs can be employed in medical devices that require high optical clarity, such as endoscopes, microscopes, or biosensors. They can also be used in wearable health monitoring devices, where the transparency of the board allows for better integration with the user’s skin.
-
Smart windows and mirrors: Transparent PCBs can be incorporated into smart windows and mirrors, enabling the display of information, graphics, or lighting effects without compromising the optical clarity of the glass.
-
Lighting systems: Transparent PCBs can be used in LED lighting systems, allowing for more uniform light distribution and improved energy efficiency. They can also enable the creation of novel lighting designs, such as transparent OLED panels.
-
Wearable devices: Transparent PCBs are well-suited for wearable devices, such as smartwatches, fitness trackers, or augmented reality glasses. The transparency of the board allows for better integration with the device’s aesthetics and can improve user comfort.
-
Aerospace and defense: Transparent PCBs can find applications in aerospace and defense industries, where the ability to integrate electronic components with transparent surfaces, such as windows or displays, can provide enhanced functionality and situational awareness.
Challenges and Future Developments
Despite the numerous advantages and potential applications of transparent PCBs, there are still some challenges that need to be addressed to fully realize their potential:
-
Cost: The materials and manufacturing processes involved in producing transparent PCBs are generally more expensive than those used in traditional PCBs. This can limit their adoption in cost-sensitive applications.
-
Conductivity and transparency trade-off: Achieving high electrical conductivity while maintaining high optical transparency is a major challenge in transparent PCBs. Current transparent conductive materials, such as ITO and AgNWs, have limitations in terms of conductivity, flexibility, and cost. Researchers are actively exploring new materials and techniques to improve the performance of transparent conductive layers.
-
Reliability and durability: Transparent PCBs may be more susceptible to environmental factors, such as temperature, humidity, and UV radiation, which can affect their long-term reliability. Developing robust encapsulation and protection methods is crucial to ensure the durability of transparent PCBs in various applications.
-
Manufacturing scalability: The production of transparent PCBs often involves specialized materials and processes, which can limit their manufacturing scalability. Adapting existing PCB manufacturing infrastructure to handle transparent materials and developing new high-throughput production techniques are essential for the widespread adoption of transparent PCBs.
As research and development in transparent PCBs continue, we can expect to see advancements in materials, manufacturing processes, and design techniques. Some of the future developments in this field may include:
-
Novel transparent conductive materials: Researchers are investigating new materials, such as graphene, carbon nanotubes, or conductive polymers, that can offer improved electrical conductivity, optical transparency, and mechanical flexibility compared to existing options.
-
Hybrid transparent PCBs: Combining transparent and opaque materials in a single PCB can provide the benefits of both worlds, enabling the creation of devices with selective transparency and enhanced functionality.
-
3D transparent PCBs: The development of 3D printing techniques for transparent conductive materials can enable the fabrication of complex, three-dimensional transparent PCB structures, opening up new possibilities for device design and integration.
-
Self-healing transparent PCBs: Incorporating self-healing materials or mechanisms into transparent PCBs can improve their reliability and extend their lifespan by enabling the autonomous repair of defects or damage.
-
Integration with other technologies: Transparent PCBs can be combined with other emerging technologies, such as flexible electronics, printed electronics, or energy harvesting, to create multifunctional, self-powered, or adaptive devices.
Frequently Asked Questions (FAQ)
-
Q: What is the difference between a transparent PCB and a traditional PCB?
A: A transparent PCB uses optically clear substrate materials and transparent conductive traces, allowing light to pass through the board while maintaining electrical functionality. Traditional PCBs use opaque materials, such as FR-4, and do not have optical transparency. -
Q: What are the main advantages of using transparent PCBs?
A: Transparent PCBs offer several advantages, including optical transparency, design flexibility, improved aesthetics, reduced weight and thickness, enhanced durability, and the potential for new applications that require the integration of electronic components with transparent surfaces. -
Q: What materials are commonly used in transparent PCBs?
A: Transparent PCBs typically use optically clear substrates, such as glass, PET, or PI, and transparent conductive materials, such as ITO, AgNWs, or PEDOT:PSS. Clear solder masks and dielectric coatings are used for insulation and protection. -
Q: What are some of the potential applications for transparent PCBs?
A: Transparent PCBs find applications in various industries, including consumer electronics (displays, touch screens, wearable devices), automotive (HUDs, instrument clusters), medical devices (endoscopes, biosensors), smart windows and mirrors, lighting systems, and aerospace and defense. -
Q: What are the main challenges in the development and adoption of transparent PCBs?
A: The main challenges in transparent PCBs include the higher cost of materials and manufacturing processes, the trade-off between conductivity and transparency, reliability and durability concerns, and manufacturing scalability. Ongoing research and development aim to address these challenges and improve the performance and viability of transparent PCBs.
Conclusion
Transparent PCBs represent a significant advancement in the field of printed circuit board technology, offering a unique combination of electrical functionality and optical transparency. By enabling the integration of electronic components with transparent surfaces, transparent PCBs open up new possibilities for the design and development of innovative devices across various industries.
While there are still challenges to be addressed, such as cost, performance, and manufacturing scalability, ongoing research and development efforts are expected to drive the progress of transparent PCB technology. As new materials, manufacturing techniques, and design approaches emerge, we can anticipate the increasing adoption of transparent PCBs in a wide range of applications, from consumer electronics to medical devices and beyond.
The future of transparent PCBs looks promising, with the potential to revolutionize the way we interact with electronic devices and create new opportunities for product innovation. As the technology continues to evolve, it will be exciting to witness the development of more advanced, multifunctional, and visually stunning devices that leverage the unique properties of transparent PCBs.
Leave a Reply