Understanding Copper Thickness Tolerances in PCB Manufacturing
Printed Circuit Boards (PCBs) are the backbone of modern electronics, providing a platform for components to be mounted and interconnected. One critical aspect of PCB design and manufacturing is the copper thickness, which plays a vital role in the board’s electrical and thermal performance. This article delves into the intricacies of copper thickness tolerances on PCBs, exploring their significance, industry standards, and best practices for designers and manufacturers.
The Importance of Copper Thickness in PCBs
Copper is the primary conductive material used in PCBs due to its excellent electrical and thermal properties. The thickness of the copper layer on a PCB directly impacts several key factors:
-
Current Carrying Capacity: Thicker copper layers can carry more current without overheating, making them suitable for high-power applications.
-
Impedance Control: Copper thickness affects the characteristic impedance of traces, which is crucial for high-speed signaling and impedance-controlled designs.
-
Thermal Management: Copper acts as a heat spreader, dissipating heat generated by components. Thicker copper layers enhance the PCB’s thermal management capabilities.
-
Mechanical Strength: Copper thickness contributes to the overall mechanical strength and rigidity of the PCB.
Industry Standards for Copper Thickness
The PCB industry follows several standards that specify the acceptable ranges and tolerances for copper thickness. The most widely recognized standards are:
- IPC-6012: Generic Performance Specification for Rigid Printed Boards
- IPC-6013: Qualification and Performance Specification for Flexible Printed Boards
- IPC-6018: Microwave End Product Board Inspection and Test
These standards define the minimum and maximum copper thicknesses for various PCB classes and applications. They also specify the tolerances, which are the allowable deviations from the nominal copper thickness.
IPC-6012 Copper Thickness Tolerances
IPC-6012 defines three classes of PCBs based on their end-use requirements:
- Class 1: General Electronic Products
- Class 2: Dedicated Service Electronic Products
- Class 3: High Reliability Electronic Products
The copper thickness tolerances for each class are as follows:
Class | Nominal Thickness (µm) | Tolerance (µm) |
---|---|---|
1 | 17.5 – 70 | ± 5.25 |
2 | 17.5 – 70 | ± 4.375 |
3 | 17.5 – 70 | ± 3.5 |
For copper thicknesses above 70 µm, the tolerance is ±10% of the nominal thickness for all classes.
Factors Affecting Copper Thickness Variation
Several factors can contribute to variations in copper thickness during the PCB manufacturing process:
-
Plating Process: The uniformity and consistency of the electroplating process directly impact the copper thickness distribution across the board.
-
Board Geometry: Complex board shapes, high aspect ratio holes, and dense copper areas can lead to uneven current distribution during plating, resulting in thickness variations.
-
Surface Preparation: Inadequate surface preparation before plating can cause poor adhesion and non-uniform copper deposition.
-
Process Control: Variations in process parameters such as current density, temperature, and agitation can affect the plating rate and uniformity.
Designing for Copper Thickness Tolerances
To ensure the reliability and performance of PCBs, designers must consider copper thickness tolerances during the design phase. Here are some best practices:
-
Choose the appropriate copper weight: Select the copper thickness based on the electrical and thermal requirements of the design, considering the current carrying capacity and thermal management needs.
-
Use copper thieving: Incorporate copper thieving or balancing techniques to promote even current distribution during plating, minimizing thickness variations.
-
Consider the aspect ratio: Be mindful of the aspect ratio of plated through-holes and vias, as high aspect ratios can lead to uneven plating and thickness variations.
-
Specify clear requirements: Clearly communicate the copper thickness requirements and tolerances to the PCB manufacturer to ensure they meet the design specifications.
Copper Thickness Measurement Techniques
Accurate measurement of copper thickness is crucial for quality control and ensuring compliance with industry standards. There are several methods for measuring copper thickness on PCBs:
X-ray Fluorescence (XRF)
XRF is a non-destructive technique that uses X-rays to excite the atoms in the copper layer, causing them to emit characteristic fluorescent X-rays. The intensity of these X-rays is proportional to the copper thickness. XRF is widely used for its speed, accuracy, and ability to measure multiple points on the board.
Cross-Sectioning
Cross-sectioning involves cutting a small sample of the PCB and examining the copper thickness under a microscope. This destructive method provides a direct measurement of the copper thickness at the cross-section location. However, it is time-consuming and only provides data for a specific point on the board.
Electrical Resistance Measurement
This method measures the electrical resistance of a copper trace with known length and width. By comparing the measured resistance to the theoretical resistance calculated based on the trace geometry and copper resistivity, the average copper thickness can be determined. This technique is non-destructive but requires accurate trace dimensions and may not capture local thickness variations.
FAQ
What is the typical copper thickness used in PCBs?
The typical copper thickness in PCBs ranges from 0.5 oz/ft² to 4 oz/ft², which corresponds to approximately 17.5 µm to 140 µm. The choice of copper thickness depends on the specific application, current carrying requirements, and thermal management needs.
How does copper thickness affect the current carrying capacity of a PCB?
Thicker copper layers can carry more current without overheating. The current carrying capacity is proportional to the cross-sectional area of the copper trace, which is determined by its width and thickness. Increasing the copper thickness allows for higher current carrying capacity, making it suitable for high-power applications.
Can copper thickness variations cause signal integrity issues?
Yes, copper thickness variations can impact signal integrity, particularly in high-speed and impedance-controlled designs. Variations in copper thickness can lead to changes in the characteristic impedance of traces, causing impedance mismatches and signal reflections. Consistent copper thickness is crucial for maintaining signal integrity and minimizing signal distortion.
How can designers minimize the impact of copper thickness tolerances?
Designers can minimize the impact of copper thickness tolerances by:
- Choosing the appropriate copper weight based on the electrical and thermal requirements of the design.
- Using copper thieving or balancing techniques to promote even current distribution during plating.
- Considering the aspect ratio of plated through-holes and vias to avoid uneven plating.
- Specifying clear copper thickness requirements and tolerances to the PCB manufacturer.
What are the consequences of copper thickness being out of tolerance?
If the copper thickness is out of tolerance, it can lead to various issues such as:
- Insufficient current carrying capacity, leading to overheating and potential failure.
- Impedance mismatches and signal integrity problems in high-speed designs.
- Inadequate thermal management, resulting in higher operating temperatures and reduced reliability.
- Non-compliance with industry standards and customer specifications.
PCB manufacturers must strictly adhere to copper thickness tolerances to ensure the reliability, performance, and functionality of the final product.
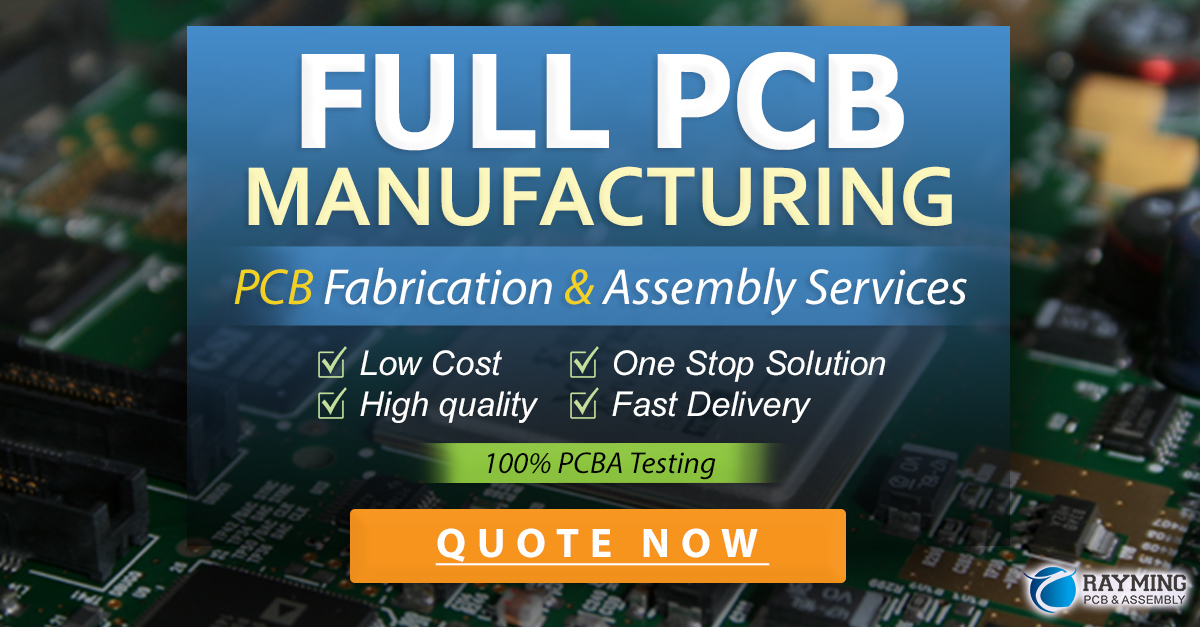
Conclusion
Copper thickness tolerances play a vital role in the performance, reliability, and manufacturability of PCBs. Understanding the industry standards, design considerations, and measurement techniques is essential for both PCB designers and manufacturers. By adhering to the specified tolerances and implementing best practices, designers can ensure their PCBs meet the electrical, thermal, and mechanical requirements, while manufacturers can deliver high-quality boards that comply with industry standards. Effective communication and collaboration between designers and manufacturers are key to navigating the challenges posed by copper thickness tolerances and achieving successful PCB production.
Leave a Reply