Introduction to Through Hole Components and PCB Design
Through hole technology has been a staple in the electronics industry for decades. Despite the rise of surface mount technology (SMT), through hole components still play a crucial role in many applications, particularly where mechanical stability, high power handling, or ease of manual assembly are required. Understanding the relationship between through hole pin length and PCB Thickness is essential for designing reliable and manufacturable circuit boards.
What are Through Hole Components?
Through hole components are electronic parts that have leads or pins designed to be inserted into drilled holes on a printed circuit board (PCB). These leads are then soldered to copper pads on the opposite side of the board to create a strong mechanical and electrical connection. Examples of common through hole components include:
- Resistors
- Capacitors
- Inductors
- Diodes
- Transistors
- Connectors
- Sockets
Advantages of Through Hole Technology
Through hole technology offers several advantages over surface mount technology:
- Mechanical strength: Through hole components provide a stronger mechanical bond to the PCB due to the leads being soldered on the opposite side of the board.
- Power handling: Through hole components can generally handle higher power levels than their SMT counterparts due to their larger size and better heat dissipation.
- Ease of manual assembly: Through hole components are easier to handle and solder manually, making them ideal for prototyping, low-volume production, or hobbyist projects.
- Reliability: The robust mechanical connection provided by through hole technology can lead to increased reliability, particularly in harsh environments or applications subject to vibration or mechanical stress.
PCB Thickness and Its Impact on Design
PCB thickness is a critical factor in the design and manufacturing of electronic devices. The thickness of a PCB can affect its mechanical strength, thermal dissipation, and the components that can be used.
Standard PCB Thicknesses
PCBs are typically available in a range of standard thicknesses, measured in either inches or millimeters. Some common PCB thicknesses include:
Imperial (inches) | Metric (mm) |
---|---|
0.031″ | 0.8 mm |
0.062″ | 1.6 mm |
0.093″ | 2.4 mm |
0.125″ | 3.2 mm |
The choice of PCB thickness depends on several factors, such as:
- The size and weight constraints of the final product
- The number of layers required for the circuit design
- The power handling requirements of the components
- The mechanical strength needed to withstand the intended operating environment
Impact on Component Selection
PCB thickness can directly influence the selection of through hole components. The length of the component leads must be sufficient to pass through the PCB and allow for soldering on the opposite side. If the PCB is too thick for a given component’s lead length, the leads may not protrude far enough to be soldered properly, leading to poor connections and potential reliability issues.
Choosing the Right Pin Length for Your PCB Thickness
To ensure proper assembly and reliable performance, it is crucial to select through hole components with lead lengths compatible with your chosen PCB thickness.
Minimum Lead Length Requirements
The minimum lead length required for a through hole component depends on the thickness of the PCB. As a general rule, the lead should protrude at least 1.5 mm (0.06″) beyond the surface of the PCB to allow for adequate soldering. This additional length is known as the “clinch length” or “toe length.”
For example, if you are using a 1.6 mm (0.062″) thick PCB, the minimum lead length required would be:
PCB thickness + Clinch length = Minimum lead length
1.6 mm + 1.5 mm = 3.1 mm (0.122″)
Maximum Lead Length Considerations
While ensuring a sufficient lead length is essential, it is also important to consider the maximum lead length that can be accommodated by your PCB design. Excessively long leads can introduce several problems:
- Mechanical interference: Long leads may interfere with other components, connectors, or the enclosure of the final product.
- Increased lead inductance: Longer leads can exhibit higher parasitic inductance, which may affect high-frequency performance or lead to unwanted oscillations.
- Difficulty in automated assembly: Excessively long leads can complicate automated assembly processes, such as wave soldering or selective soldering, leading to increased manufacturing costs or reduced yields.
As a general guideline, aim to keep the lead length between 2-3 times the PCB thickness. This range provides a good balance between mechanical stability and the considerations mentioned above.
Lead Trimming and Forming
In some cases, you may need to use components with leads longer than the ideal range for your PCB thickness. In these situations, it is common practice to trim and form the leads to the desired length before assembly.
Lead trimming and forming can be done manually using tools like wire cutters and pliers or automatically using dedicated lead forming machines. When trimming leads, ensure that the remaining length is sufficient for proper soldering and mechanical stability.
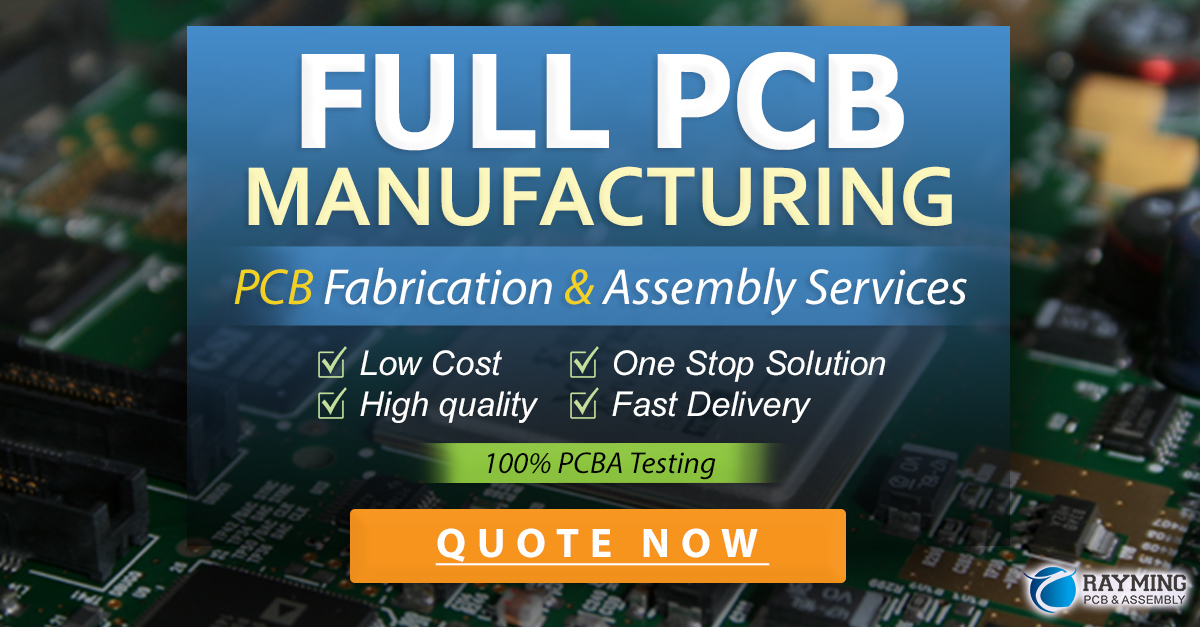
PCB Design Tips for Through Hole Components
When designing PCBs for through hole components, there are several best practices to follow to ensure optimal performance and manufacturability.
Hole Size and Pad Diameter
The drill hole size for a through hole component should be slightly larger than the lead diameter to allow for easy insertion and proper soldering. A common rule of thumb is to use a hole size that is 0.2-0.5 mm (0.008-0.02″) larger than the lead diameter.
The pad diameter should be large enough to accommodate the hole and provide sufficient area for soldering. Typically, the pad diameter is 1.5-2 times the hole size. For example, if the hole size is 0.8 mm (0.031″), a pad diameter of 1.2-1.6 mm (0.047-0.063″) would be appropriate.
Component Placement and Orientation
When placing through hole components on your PCB, consider the following guidelines:
- Alignment: Ensure that the component leads are aligned with the holes to facilitate easy insertion and soldering.
- Orientation: Pay attention to the orientation of polarized components, such as diodes, electrolytic capacitors, and connectors, to ensure proper functionality.
- Clearance: Provide adequate clearance between components to allow for easy assembly and to avoid mechanical interference.
- Thermal considerations: Position heat-sensitive components away from high-power devices or heat sources to prevent damage during soldering or operation.
Soldering and Inspection
Proper soldering is critical for ensuring reliable electrical and mechanical connections between through hole components and the PCB. Some key considerations include:
- Solder type: Use the appropriate solder alloy for your application, considering factors such as melting temperature, strength, and environmental requirements.
- Soldering temperature: Ensure that the soldering iron or soldering station is set to the correct temperature for the solder type and component being used.
- Soldering technique: Apply the soldering iron and solder to the pad and lead simultaneously, allowing the solder to flow evenly around the joint. Avoid excessive heat or solder, which can lead to bridging or damage to the component or PCB.
- Inspection: Visually inspect the soldered joints for proper wetting, fillets, and the absence of defects such as bridging, cold joints, or insufficient solder.
Frequently Asked Questions (FAQ)
1. What happens if the lead length is too short for the PCB thickness?
If the lead length is too short for the PCB thickness, the component may not be able to be soldered properly to the board. This can result in poor electrical connections, mechanical instability, and potential reliability issues. Always ensure that the lead length is sufficient to pass through the PCB and allow for adequate soldering on the opposite side.
2. Can I use components with leads longer than necessary for my PCB thickness?
Yes, you can use components with leads longer than necessary for your PCB thickness. However, you may need to trim and form the leads to the desired length before assembly to avoid mechanical interference, increased lead inductance, or difficulties in automated assembly processes.
3. What is the recommended range for lead length relative to PCB thickness?
As a general guideline, aim to keep the lead length between 2-3 times the PCB thickness. This range provides a good balance between mechanical stability and other considerations, such as mechanical interference, lead inductance, and ease of automated assembly.
4. How do I choose the appropriate hole size and pad diameter for a through hole component?
The drill hole size for a through hole component should be slightly larger than the lead diameter, typically by 0.2-0.5 mm (0.008-0.02″). The pad diameter should be large enough to accommodate the hole and provide sufficient area for soldering, usually 1.5-2 times the hole size.
5. What soldering techniques should I use for through hole components?
When soldering through hole components, ensure that the soldering iron is set to the correct temperature for the solder type and component being used. Apply the soldering iron and solder to the pad and lead simultaneously, allowing the solder to flow evenly around the joint. Avoid excessive heat or solder, which can lead to bridging or damage to the component or PCB. Visually inspect the soldered joints for proper wetting, fillets, and the absence of defects.
Conclusion
Understanding the relationship between through hole pin length and PCB thickness is crucial for designing reliable and manufacturable electronic devices. By selecting components with appropriate lead lengths, designing PCBs with suitable hole sizes and pad diameters, and following best practices for component placement and soldering, you can ensure optimal performance and longevity for your through hole assemblies.
As always, it is essential to consult with your PCB manufacturer and assembly partners to ensure that your design is compatible with their processes and capabilities. By working closely with these stakeholders and staying up-to-date with industry standards and best practices, you can create high-quality, reliable electronic products that meet the needs of your customers and end-users.
Leave a Reply