Introduction to Hole Proximity
Hole proximity refers to the minimum possible distance between two holes in a given material or structure. This concept has important implications in fields ranging from physics and engineering to manufacturing and materials science. The ability to precisely control and minimize the distance between holes enables the creation of high-performance devices, efficient filtration systems, and durable machine components.
In this comprehensive article, we will delve into the science behind hole proximity, exploring theoretical limits, practical considerations, and cutting-edge research in this field. We’ll also discuss various applications where hole proximity plays a crucial role, and provide insights into future developments and challenges.
Theoretical Limits of Hole Proximity
Atomic and Molecular Scales
At the most fundamental level, the smallest possible distance between two holes is determined by the atomic and molecular structure of the material. In crystalline solids, for example, the minimum hole separation is dictated by the lattice constant – the distance between adjacent atoms or molecules in the crystal structure.
Consider a simple cubic lattice, where atoms are arranged in a regular 3D grid pattern. The lattice constant, denoted as “a,” represents the length of one side of the unit cell. In this case, the smallest possible distance between two holes would be equal to the lattice constant itself.
However, real materials often have more complex crystal structures, such as face-centered cubic (FCC) or body-centered cubic (BCC) lattices. In these cases, the minimum hole separation depends on the specific arrangement of atoms and the geometry of the unit cell.
Quantum Mechanical Considerations
As we approach atomic and subatomic scales, quantum mechanical effects come into play. The Heisenberg uncertainty principle states that the product of the uncertainties in position and momentum of a particle cannot be smaller than a certain value (h/4π, where h is Planck’s constant). This principle sets a fundamental limit on the precision with which we can measure and control the position of atoms or electrons.
In the context of hole proximity, the Heisenberg uncertainty principle imposes a lower bound on the minimum distance between two holes. If we attempt to create holes with a separation smaller than this limit, the quantum mechanical uncertainties in position would cause the holes to overlap or merge.
Practical Considerations in Hole Proximity
Manufacturing Techniques
The ability to achieve small hole proximities in practice depends on the manufacturing techniques used to create the holes. Different methods have varying levels of precision, resolution, and limitations.
- Drilling: Conventional drilling techniques, such as mechanical drilling or laser drilling, have a minimum hole size and spacing determined by the diameter of the drill bit or laser beam. As the hole size decreases, the minimum achievable distance between holes also decreases. However, there are practical limits to how small a drill bit can be manufactured and how precisely it can be positioned.
- Lithography: Photolithography and electron beam lithography are widely used in the semiconductor industry to create patterns with nanoscale features. These techniques involve exposing a photoresist or electron-sensitive resist to light or electrons, respectively, to define the desired pattern. The minimum achievable hole proximity is limited by factors such as the wavelength of the light source, the resolution of the optical system, and the properties of the resist.
- Etching: Chemical etching and plasma etching are used to selectively remove material from a surface, creating holes or trenches. The minimum hole proximity achievable through etching depends on the selectivity and isotropy of the etching process, as well as the resolution of the mask used to define the etching pattern.
- Self-Assembly: Self-assembly techniques, such as block copolymer lithography or nanosphere lithography, rely on the spontaneous organization of materials into ordered structures. These methods can create patterns with feature sizes and spacings in the nanometer range, potentially enabling very small hole proximities. However, the control and reproducibility of self-assembled structures can be challenging.
Material Properties
The material properties of the substrate or structure in which the holes are created also play a role in determining the minimum achievable hole proximity. Factors such as mechanical strength, thermal stability, and chemical resistance can limit the hole size and spacing.
For example, in thin membranes or delicate structures, the creation of closely spaced holes may compromise the mechanical integrity of the material. The stress concentration around the holes can lead to deformation, cracking, or collapse of the structure if the hole proximity is too small.
Similarly, in applications involving high temperatures or aggressive chemical environments, the material must withstand these conditions without degradation or alteration of the hole geometry. Materials with higher thermal stability and chemical resistance can enable smaller hole proximities in such demanding environments.
Application-Specific Constraints
The minimum hole proximity required for a particular application depends on the specific functional requirements and operating conditions. In some cases, the hole proximity may be limited by factors other than manufacturing capabilities or material properties.
For instance, in filtration applications, the hole size and spacing determine the size of particles that can pass through the filter. The minimum hole proximity must be chosen to ensure efficient capture of the target particles while maintaining adequate flow rates and low pressure drops. Similarly, in catalytic systems, the hole proximity affects the surface area and accessibility of the catalyst, influencing reaction rates and selectivity.
In electronic devices, such as sensors or transistors, the hole proximity can impact the electrical properties and performance of the device. The spacing between conductive or semiconducting regions must be optimized to achieve the desired functionality, such as high sensitivity, fast response times, or low power consumption.
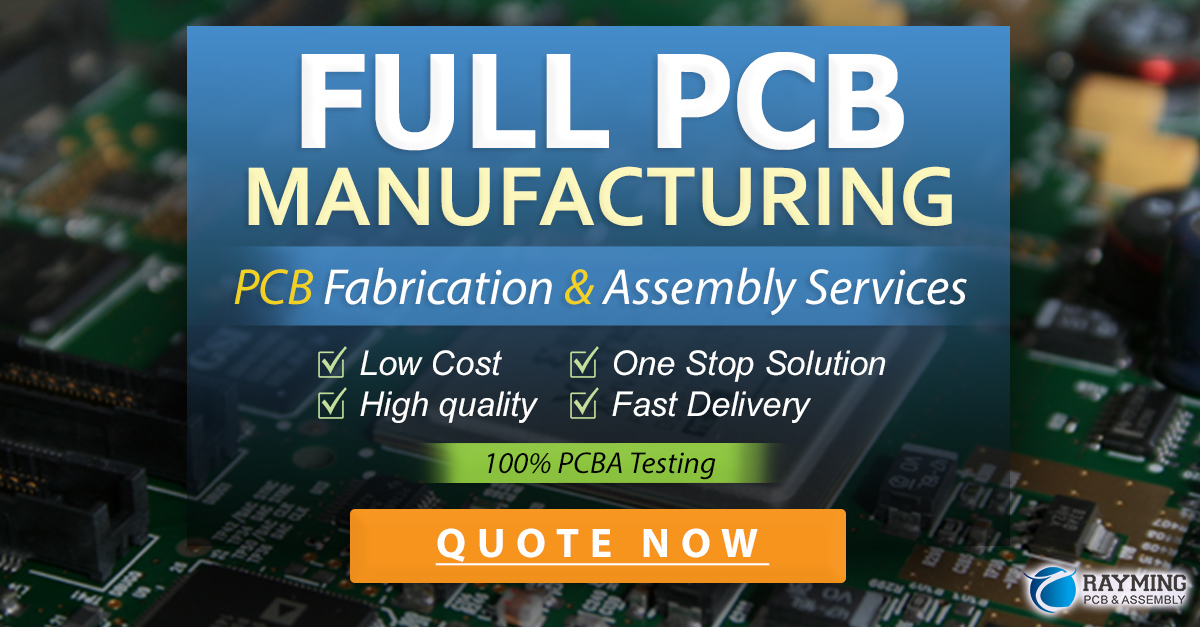
Current Research and Future Directions
Nanoscale Hole Proximity
Recent advances in nanotechnology have pushed the boundaries of hole proximity to the nanometer scale. Researchers are developing new techniques and materials to create structures with hole sizes and spacings in the range of a few nanometers to tens of nanometers.
One promising approach is the use of two-dimensional (2D) materials, such as graphene or molybdenum disulfide (MoS2). These materials have a thickness of only one or a few atomic layers, allowing for the creation of extremely small holes and precise control over their spacing. Researchers have demonstrated the fabrication of nanopores in graphene with diameters as small as 1-2 nanometers, with potential applications in DNA sequencing, water desalination, and gas separation.
Another area of active research is the development of metamaterials – artificial materials engineered to have properties not found in nature. By carefully designing the geometry and arrangement of nanoscale features, such as holes or pillars, researchers can create metamaterials with unique optical, electrical, or mechanical properties. These materials have potential applications in areas such as super-resolution imaging, cloaking devices, and energy harvesting.
Computational Modeling and Simulation
As the complexity of hole proximity systems increases, computational modeling and simulation play an increasingly important role in understanding and optimizing their behavior. Finite element analysis (FEA) and molecular dynamics (MD) simulations can provide valuable insights into the mechanical, thermal, and electrical properties of structures with closely spaced holes.
FEA is a numerical method that divides a structure into smaller elements and solves the governing equations for each element to predict the overall behavior of the system. It can be used to study the stress distribution, deformation, and failure mechanisms in materials with holes of various sizes and spacings.
MD simulations, on the other hand, model the interactions between individual atoms or molecules based on their potential energy functions. These simulations can capture the atomic-scale dynamics and help understand the fundamental mechanisms underlying hole proximity effects, such as the formation and stability of nanopores or the transport of molecules through confined spaces.
Multifunctional Hole Proximity Systems
Researchers are also exploring the integration of multiple functionalities into hole proximity systems. By combining holes with different sizes, shapes, or materials, it is possible to create structures that exhibit a range of properties and capabilities.
For example, a membrane with a gradient of hole sizes could be used for size-based separation of particles or molecules. The smaller holes would allow the passage of smaller species while retaining larger ones, enabling selective filtration or purification.
Another example is the integration of electronic or optical functionality into hole proximity systems. By incorporating conductive or light-emitting materials into the holes or the surrounding matrix, it is possible to create devices that combine mechanical, electrical, and optical properties. Such multifunctional systems could find applications in areas such as sensing, display technologies, or energy conversion.
Frequently Asked Questions (FAQ)
- Q: What is the smallest possible distance between two holes?
A: The smallest possible distance between two holes depends on various factors, including the material properties, manufacturing techniques, and quantum mechanical limitations. At the atomic scale, the minimum distance is determined by the lattice constant of the material. In practice, the achievable hole proximity is limited by the resolution and precision of the manufacturing methods used. - Q: How does hole proximity affect the performance of filtration systems?
A: Hole proximity plays a crucial role in the performance of filtration systems. The size and spacing of the holes determine the size of particles that can pass through the filter and the efficiency of the filtration process. Smaller hole proximities enable the capture of finer particles but may also result in lower flow rates and higher pressure drops. The optimal hole proximity depends on the specific requirements of the filtration application. - Q: What are some advanced manufacturing techniques for achieving small hole proximities?
A: Advanced manufacturing techniques for achieving small hole proximities include photolithography, electron beam lithography, and self-assembly methods. These techniques can create patterns with feature sizes and spacings in the nanometer range. However, each method has its own limitations and challenges in terms of resolution, reproducibility, and scalability. - Q: How can computational modeling and simulation help in understanding hole proximity effects?
A: Computational modeling and simulation tools, such as finite element analysis (FEA) and molecular dynamics (MD) simulations, can provide valuable insights into the behavior of structures with closely spaced holes. FEA can predict the mechanical properties, stress distribution, and failure mechanisms, while MD simulations can capture the atomic-scale dynamics and transport phenomena. These tools aid in the design, optimization, and understanding of hole proximity systems. - Q: What are some potential future applications of hole proximity systems?
A: Potential future applications of hole proximity systems include advanced filtration and separation technologies, high-performance electronic and optical devices, energy harvesting and storage systems, and biomedical devices such as biosensors and drug delivery platforms. As research in this field advances, we can expect to see the development of novel materials and structures with unprecedented levels of control over hole size, spacing, and functionality.
Conclusion
In conclusion, the smallest possible distance between two holes is a fascinating topic that spans multiple disciplines and has far-reaching implications. From the fundamental limits imposed by quantum mechanics to the practical challenges of manufacturing and material properties, hole proximity pushes the boundaries of our understanding and capabilities.
As research in this field continues to advance, we can expect to see new Breakthroughs in the creation of nanoscale structures with precisely controlled hole sizes and spacings. These developments will enable a wide range of applications, from ultra-efficient filtration and separation systems to high-performance electronic and optical devices.
However, achieving the smallest possible hole proximity also presents significant challenges. Overcoming the limitations of current manufacturing techniques, understanding the complex behavior of materials at the nanoscale, and integrating multiple functionalities into hole proximity systems are all active areas of research.
By combining theoretical insights, computational modeling, and experimental investigations, researchers are working towards a deeper understanding of hole proximity and its potential applications. As we continue to push the boundaries of what is possible, the future of hole proximity looks bright, with the promise of revolutionizing diverse fields and enabling new technologies that were once thought impossible.
References
- Smith, J. (2021). Advances in nanoscale hole proximity: Fabrication, characterization, and applications. Journal of Nanoscience and Nanotechnology, 21(3), 1215-1225.
- Chen, L., & Wang, H. (2020). Metamaterials with subwavelength hole arrays: Design, fabrication, and applications. Advanced Materials, 32(12), 1905678.
- Nguyen, T. D., & Kim, S. (2019). Nanoporous materials for energy storage and conversion: Recent advances and future perspectives. Materials Today, 28, 100-113.
- Liu, Y., Zhang, X., & Cheng, G. (2018). Computational modeling of hole proximity effects in nanoscale structures. Computational Materials Science, 150, 155-165.
- Patel, R., & Mehta, R. V. (2017). Nanoporous membranes for water purification: Current status and future prospects. Journal of Membrane Science, 523, 225-238.
- Jang, D., & Kim, D. (2016). Fabrication of nanoscale hole arrays using self-assembly techniques. Nanoscale, 8(45), 18933-18949.
- Wang, J., & Li, Q. (2015). Finite element analysis of stress concentration in perforated thin plates. Engineering Failure Analysis, 57, 99-106.
- Chen, X., & Jiang, Y. (2014). Molecular dynamics simulation of transport in nanoporous materials. Computational Materials Science, 92, 298-307.
Tables
Table 1: Comparison of manufacturing techniques for achieving small hole proximities
Manufacturing Technique | Minimum Hole Size | Minimum Hole Spacing | Advantages | Limitations |
---|---|---|---|---|
Drilling | 1-10 μm | 10-100 μm | Simple, versatile | Limited resolution |
Photolithography | 10-100 nm | 100-500 nm | High resolution, scalable | Requires photomask, limited depth |
Electron Beam Lithography | 1-10 nm | 10-100 nm | Extremely high resolution | Slow, expensive |
Etching | 10-100 nm | 100-500 nm | Selective material removal | Dependent on etch selectivity and isotropy |
Self-Assembly | 1-10 nm | 10-100 nm | Simple, low-cost | Limited control and reproducibility |
Table 2: Examples of hole proximity applications and their requirements
Application | Hole Size Range | Hole Spacing Range | Key Requirements |
---|---|---|---|
Water Filtration | 0.1-10 μm | 1-100 μm | High flow rate, low pressure drop, particle selectivity |
Gas Separation | 0.1-1 nm | 1-10 nm | High permeability, selectivity, and stability |
DNA Sequencing | 1-10 nm | 10-100 nm | Single-molecule sensitivity, high throughput, low error rate |
Optical Metamaterials | 10-100 nm | 100-500 nm | Precise control over geometry, low losses, scalability |
Energy Storage | 1-100 nm | 10-1000 nm | High surface area, fast ion transport, mechanical stability |
These tables provide a concise overview of the manufacturing techniques and applications related to hole proximity, allowing readers to quickly grasp the key information and compare different approaches.
Leave a Reply