Introduction
Printed circuit boards (PCBs) are fundamental building blocks of modern electronics. They provide the mechanical structure and electrical connections between components in an electronic device. PCBs were first developed in the 1930s and have evolved tremendously over the decades. Today, PCBs come in all shapes and sizes, from simple single-sided boards to complex multilayer boards.
A custom PCB is designed and manufactured for a specific application, rather than mass-produced for general use. Custom PCBs allow circuit designers great flexibility to lay out a board to perfectly meet the needs of their project. However, custom PCBs also come with higher costs and lead times compared to standard boards.
This article examines the key benefits and drawbacks of using a custom printed circuit board design. We’ll look at factors like flexibility, cost, lead time, quality control, and more.
Pros of Custom PCBs
Flexible Design and Layout
The primary advantage of a custom PCB is the ability to tailor the design and layout precisely to the requirements of the circuit and application. When using off-the-shelf or standardized PCB designs, engineers often need to make compromises and work around the limitations of the predefined board layout.
With a custom design, board size, shape, layer count, component placement, trace routing, and other attributes can be configured for optimal performance, space efficiency, manufacturability, serviceability, and other factors specific to the application.
For example, a custom PCB for a handheld device can be designed to fit precisely within the enclosure while positioning heat-sensitive components away from areas prone to higher temperatures. In contrast, an off-the-shelf design may lead to wasted space or less than ideal component placement.
Component Selection and Integration
A custom PCB design allows the designer to select the exact components required, rather than being limited to parts that fit a standardized board. This may include special power or analog components with unique footprints or packages.
Components from multiple vendors can also be mixed and matched in a custom design, rather than being constrained to use a single supplier. Additionally, components can be tightly integrated with optimized placement to simplify PCB layout and enhance performance through shorter trace lengths.
Standard PCBs often include superfluous components or require components to be located far from where they are needed due to predefined layouts.
Signal and Power Integrity Optimization
With full control over PCB stackup and trace routing, engineers can design layer stacking, trace widths and clearances, component placement, and other attributes to ensure excellent signal and power integrity. This leads to maximized circuit performance.
For high-speed digital circuits and precise analog circuits, signal integrity techniques like controlled impedance traces, minimizing unintended crosstalk, and proper return path design can be implemented. For power distribution, managing IR drops over long traces and providing sufficient decoupling capacitance become easier with a custom design approach.
Thermal Management
Careful placement of heat-generating components along with thermal relief cutouts in ground and power planes permits superior thermal performance. Thermal vias can also be placed strategically to conduct heat away from sensitive hot spots. In some cases, active cooling elements can be integrated into the PCB design itself.
This level of thermal analysis does not exist with off-the-shelf PCBs intended for generic applications. Excessive heating can be avoided in custom designs, improving long-term reliability.
Design for Manufacturing and Testability
With tight control over all design parameters, PCBs can be optimized for efficient manufacturing and assembly. This includes strategies like minimizing unique part numbers, enabling easier sourcing of materials, standardizing hole sizes, and providing test points for quality control.
Testability features like traces to probe key signals, vias to access internal planes, and component clearance for accessing test points can be designed in from the start. These DFM and DFT techniques reduce production costs and ensure quality.
Verification Through Simulation and Prototyping
Every design parameter from trace impedances to power supply voltages can be simulated using SPICE or other circuit modeling tools. This allows performance verification and troubleshooting prior to committing to an actual board fabrication.
Prototyping services also allow 1-2 custom boards to be built quickly from the engineering CAD data to enable practical testing before high volume production.between simulation and prototyping, the design can be proven comprehensively.
Design Reuse
Once a custom PCB design is completed and verified, the same design can be reused in future product updates or separate products with similar requirements. Design costs are amortized over a longer product lifetime and across multiple products.
Some enhancements may be needed from one generation to the next, but much of the proven base design can be preserved or adapted to new applications rather than starting completely from scratch.
Low and Medium Volume Production
For production volumes in the hundreds to tens of thousands of boards, custom PCBs can make economic sense. Standard PCBs with high tooling costs only become cost-effective at much higher volumes.
A custom design tailored to the specific product needs also avoids the risk of inefficient use of board space or excessive component count inherent in standardized designs aimed at wide applicability.
In short, for a specialized product, a custom PCB allows for an optimized design while keeping volumes at a modest level. This combination ensures efficiency and rapid time-to-market.
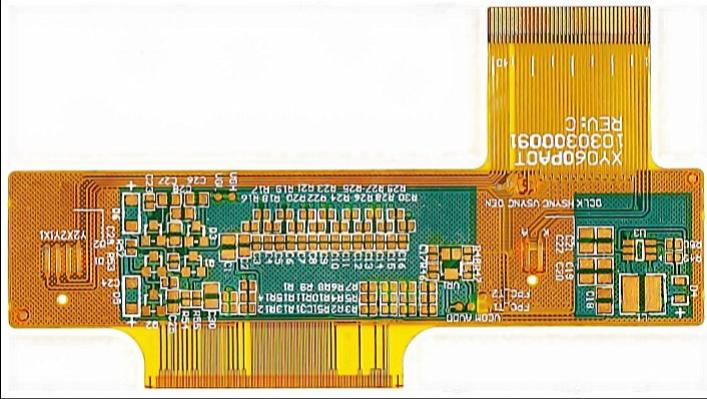
Cons of Custom PCBs
Higher Cost Per Board at Low Volumes
The primary tradeoff for a custom PCB design is higher cost per board at production volumes below a few thousand units. The non-recurring engineering (NRE) costs for custom design, prototyping, and documentation are amortized over the number of boards produced. With an off-the-shelf PCB, these NRE costs have already been absorbed by huge production volumes.
At 25-100 unit volumes, custom board costs can easily be 5-10X higher than standardized boards ordered from a catalog. The crossover point where custom boards become cost-effective depends greatly on the complexity, layer count, tolerances, and other specifications of a design. In general, simpler and looser tolerance boards reach cost parity at 1,000-2,000 units.
Longer Lead Times
The design, documentation, fab quoting, and manufacturing process for a custom PCB all demand additional time compared to procuring a standard design from inventory. While standard PCBs ship in 2-4 weeks, a complex custom board can require 12 weeks from design completion to delivery. Simpler boards may ship in 6-8 weeks.
Additionally, if multiple prototype iterations are required, additional time must be allotted. Production lead times must be factored in early in the project schedule for custom boards.
Potential Quality Issues
Given tighter tolerances, higher layer counts, and lower production volumes, custom PCBs can be more prone to defects like electrical shorts, open traces, drilling errors, and thin spots in plating. With standard designs, these fabrication processes are refined over years of high-volume production.
Rigorous quality control steps are required to ensure custom boards meet specifications. Pre-production testing using test coupons, inspection of bare boards, and thorough functional testing of populated boards helps prevent problems from reaching end-customers. But cost and effort must be spent on quality control.
Supply Chain Complexity with Low Volumes
Low to moderate production volumes can make supply chain management more complex for custom PCBs. Certain fabrication and assembly steps are best suited to larger volume board shops while others specialize in quick-turn prototypes. Shipping between multiple suppliers adds delays and costs.
Sourcing components in hundreds of units from distributors adds overhead versus ordering reels of thousands from manufacturers. Managing dozens of unique part numbers and Bill of Materials (BOM) revisions further complicates procurement, inventory management, and production planning. Hobbyist volumes are best served by standardized boards.
Iteration Overhead
For cutting edge or highly complex designs, multiple prototype iterations may be needed to refine a custom PCB to meet all specifications. This adds costs and delays for each revision cycle. Problems only revealed during full volume production require even more dramatic re-spins.
Standardized boards tend to incorporate proven, mature designs less prone to unforeseen issues. While necessary, engineering verification and design iteration overhead should be minimized where possible.
High NRE Costs
Non-recurring engineering (NRE) costs encompass all the upfront design, simulation, documentation, and one-time fees required to create a custom board and associated assemblies. These NRE costs apply whether a few prototypes or high volumes are produced.
NRE can easily exceed $10,000 for a complex design, and often over $50,000 for boards like advanced FPGAs. High layer counts, small features sizes, and special processes like impedance control or buried/blind vias raise NRE costs. The benefits of customization must justify these unavoidable NRE expenses.
Potential Obsolescence
If a custom PCB is designed for a very specific application, future component availability or manufacturing process changes can limit its useful lifetime. Functional requirements may also evolve beyond the fixed capabilities of the original board.
Standard product roadmaps and predefined succession plans for replacing aging designs are rare with custom boards. Continuing viability past the original project requires planning for potential obsolescence risks.
Key Factors in Evaluating Custom PCB Need
Not every project necessarily requires a custom designed PCB, but the following factors help identify promising applications for customization:
- Unique requirements not easily met by any standard design
- Need for optimization for size, performance, cost, or other attributes
- Expected volumes in the hundreds to tens of thousands of boards over lifetime
- Constant or slightly varying volumes suited for medium-scale production
- Acceptance of development timeline on the order of 8-16 weeks
- Willingness to engage in design reviews and prototype iterations
- Mechanisms to control manufacturing quality and component sourcing
For very low volumes under 100 units, standardized boards keep costs affordable. On the other end, volumes above tens of thousands favor high-volume assembly using standardized boards. In between, custom boards strike an effective balance.
The level of complexity is also a factor. Simpler boards with loose tolerances and specifications can be cost-effectively sourced as catalog items. Very complex and precise boards with tight constraints strongly justify custom design to meet requirements.
Lastly, unique aspects of the end product like size, shape, environment, use case, and performance targets help determine whether customization is preferable to an off-the-shelf industry standard PCB.
Best Practices for Effective Custom PCB Development
To maximize the benefits and minimize the risks of developing a custom printed circuit board, engineers should follow best practices like:
- Involve the CM/Fab early – Get board shop input during design to ensure manufacturability, DFM guidelines are followed, and fabrication processes are understood.
- Simulate first – Verify circuit operation and performance through simulation before finalizing schematics & layout. Saves prototype iteration time.
- Build in testability – Include features on the board to support testing at bare board, populated board, and system level. Traces, vias, testpoints etc.
- Review designs thoroughly – Let multiple experts examine schematics, layout, BOM, drawings, etc. Check designs using automated DRC/ERC tools plus human review before release.
- Prototype multiple times – Validate designs through at least two prototype builds before committing to full production. Spot potential errors early.
- Monitor component life cycles – Select parts which will remain available over the target product life cycle. Avoid obsolete or end-of-life components when possible.
- Design with a revision plan – Consider how designs could be revised or adapted for future product generations or applications.
- Manage quality expectations – Understand fabrication yield and defect rates may be lower than commercial PCBs. Inspect and test thoroughly to catch issues early.
- Plan for obsolescence – Be aware of limits onlifetime viability and make contingency plans for redesign or replacement when required.
Pros vs Cons Summary
Pros | Cons |
---|---|
Fully flexible design tailored to requirements | Higher cost per board at low volumes |
Component selection and integration optimization | Longer lead times for fabrication and assembly |
Signal and power integrity optimization | Potential quality problems require extensive quality control |
Thermal management capabilities | Supply chain complexity at low volumes |
Design for manufacturing/test considerations | Additional costs and time for prototype iterations |
Verification through simulation and prototyping | High non-recurring engineering (NRE) costs |
Reuse of proven designs | Concerns regarding potential obsolescence |
Conclusion
Custom printed circuit boards provide engineers with a blank canvas to design the optimal board for an application without compromises. This allows innovating products which are sized, shaped, and specified exactly as needed.
However, customization comes at a cost premium and demands rigorous engineering verification and quality control. The value versus standardized design must be weighed based on volumes, complexity, requirements, and time-to-market priorities.
For a range of medium complexity and volume applications, custom PCB development unlocks superior solutions. But all projects differ, and through careful analysis the best approach can be selected. With upfront planning and engineering discipline, custom boards can deliver tremendous long-term value.
Frequently Asked Questions
What are the key factors to determine if a custom PCB is the right choice?
- Unique size, shape, or interconnection requirements
- Need for optimized performance or features not in standard boards
- Volumes in hundreds to tens of thousands over product lifetime
- Acceptable development timeline (~12 weeks for fabrication)
- Ability to verify design through simulation and prototyping
- Mechanism for quality control during fabrication
What volume of custom PCBs starts to become cost effective?
- The crossover point depends greatly on complexity, layer count, tolerances, and other specifications. In general, simpler 2-4 layer boards reach cost parity around 1,000-2,000 units when compared to off-the-shelf boards. More complex or high-layer-count boards may require 5,000+ units to offset NRE expenses.
How can I reduce the risk of errors and issues with a custom PCB design?
- Thoroughly simulate circuit performance before finalizing the design
- Build in testability features like probe points
- Perform design reviews, follow DFM guidelines
- Prototype boards at least twice before full production
- Perform inspections and testing at multiple assembly stages
- Select stable, long lifetime components when possible
What level of quality difference can be expected with a low-volume custom PCB?
- Expect 2-5X more defects versus a commercial high-volume PCB. Rigorous testing at multiple stages is required. Target >95% yield for complex or high layer count boards. Simpler boards can target >98% yield.
How many times should a custom PCB be prototyped before release?
- At least two prototype iterations should be budgeted. The first prototype tests basic functionality and reveals obvious errors early. The second prototype verifies design corrections and characterizes board performance prior to commiting to production.
Leave a Reply