What are PCB Applications?
Printed Circuit Boards (PCBs) are essential components in modern electronic devices. They provide a platform for electrical components to be mounted and interconnected, enabling the efficient functioning of various electronic systems. PCBs find applications in a wide range of industries, from consumer electronics to aerospace and defense. In this comprehensive article, we will explore six major PCB applications and their significance in the world of electronics.
1. Consumer Electronics
1.1 Smartphones and Tablets
PCBs are the backbone of smartphones and tablets, enabling these devices to perform complex functions while maintaining a compact form factor. The PCBs in these devices house various components, such as processors, memory modules, wireless communication modules, and sensors.
1.2 Laptops and Computers
Laptops and computers rely heavily on PCBs for their functionality. The motherboard, which is the main PCB in a computer, connects all the essential components, including the CPU, RAM, storage devices, and peripheral interfaces.
1.3 Home Appliances
PCBs are also widely used in home appliances, such as televisions, refrigerators, washing machines, and air conditioners. These PCBs control the various functions of the appliances and enable features like smart connectivity and energy efficiency.
2. Automotive Electronics
2.1 Engine Control Units (ECUs)
PCBs play a crucial role in automotive electronics, particularly in Engine Control Units (ECUs). ECUs are responsible for managing various aspects of a vehicle’s engine, such as fuel injection, ignition timing, and emission control. The PCBs in ECUs are designed to withstand harsh environmental conditions, including extreme temperatures and vibrations.
2.2 Infotainment Systems
Modern vehicles feature advanced infotainment systems that provide navigation, entertainment, and communication capabilities. PCBs are used to integrate various components, such as displays, audio systems, and wireless connectivity modules, into a cohesive and user-friendly interface.
2.3 Advanced Driver Assistance Systems (ADAS)
PCBs are essential for implementing Advanced Driver Assistance Systems (ADAS) in vehicles. ADAS features, such as lane departure warning, adaptive cruise control, and automatic emergency braking, rely on PCBs to process data from various sensors and make real-time decisions to enhance vehicle safety.
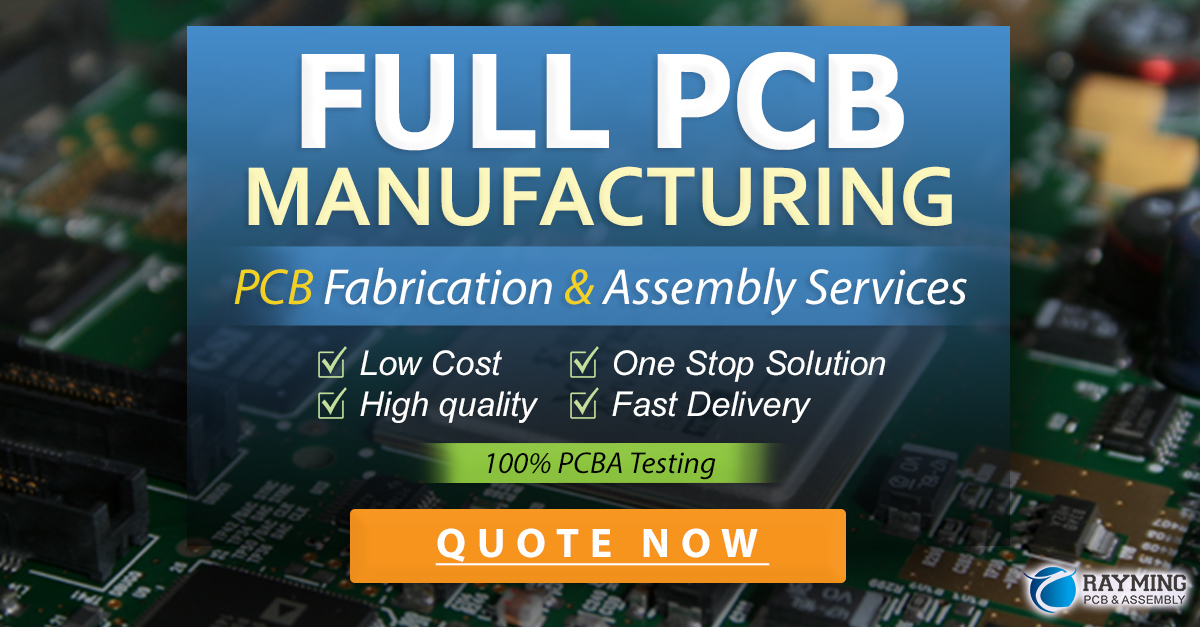
3. Medical Devices
3.1 Diagnostic Equipment
PCBs are used in a wide range of medical diagnostic equipment, such as MRI machines, CT scanners, and ultrasound devices. These PCBs are designed to meet stringent quality and reliability standards to ensure accurate and reliable diagnostic results.
3.2 Monitoring Systems
Medical monitoring systems, such as patient monitors and wearable devices, rely on PCBs to collect, process, and display vital signs and other physiological data. These PCBs are often designed to be compact, lightweight, and power-efficient to ensure patient comfort and ease of use.
3.3 Implantable Devices
PCBs are also used in implantable medical devices, such as pacemakers, defibrillators, and neurostimulators. These PCBs are designed to be highly reliable and long-lasting, as they are intended to function within the human body for extended periods.
4. Industrial Automation
4.1 Process Control Systems
PCBs are essential components in industrial process control systems, which monitor and regulate various parameters, such as temperature, pressure, and flow rate. These PCBs are designed to be rugged and reliable, ensuring the smooth and efficient operation of industrial processes.
4.2 Programmable Logic Controllers (PLCs)
Programmable Logic Controllers (PLCs) are widely used in industrial automation to control machinery and processes. PCBs form the core of PLCs, enabling them to read inputs, execute control logic, and generate outputs to control various devices and systems.
4.3 Human-Machine Interfaces (HMIs)
PCBs are used in Human-Machine Interfaces (HMIs), which provide a means for operators to interact with industrial automation systems. HMIs typically include displays, touch panels, and input devices, all of which are integrated using PCBs.
5. Aerospace and Defense
5.1 Avionics Systems
PCBs are critical components in avionics systems, which control various aspects of aircraft operation, such as navigation, communication, and flight control. These PCBs are designed to meet stringent safety and reliability standards to ensure the safe and efficient operation of aircraft.
5.2 Satellite Systems
Satellites rely on PCBs for various functions, including power management, data processing, and communication. PCBs used in satellite systems are designed to withstand the harsh conditions of space, including extreme temperatures, radiation, and vacuum.
5.3 Military Equipment
PCBs are used in a wide range of military equipment, such as radar systems, communication devices, and weapon control systems. These PCBs are designed to be rugged, reliable, and secure to ensure the effective operation of military equipment in challenging environments.
6. Internet of Things (IoT)
6.1 Smart Home Devices
PCBs are the foundation of smart home devices, such as smart thermostats, security systems, and lighting controls. These PCBs enable the devices to communicate with each other and with cloud-based platforms, allowing for remote monitoring and control.
6.2 Wearable Technology
Wearable technology, such as smartwatches and fitness trackers, relies on PCBs to integrate various sensors, processors, and communication modules into compact and lightweight devices. These PCBs are designed to be power-efficient and comfortable to wear for extended periods.
6.3 Industrial IoT
PCBs play a crucial role in enabling the Industrial Internet of Things (IIoT), which involves the integration of sensors, communication networks, and data analytics to optimize industrial processes. PCBs used in IIoT applications are designed to be rugged, reliable, and capable of processing large amounts of data in real-time.
Frequently Asked Questions (FAQ)
1. What is the difference between a single-sided and double-sided PCB?
A single-sided PCB has conductive traces on only one side of the board, while a double-sided PCB has conductive traces on both sides. Double-sided PCBs offer more design flexibility and higher component density compared to single-sided PCBs.
2. What materials are used to manufacture PCBs?
PCBs are typically made from a combination of materials, including:
– Substrate: Usually made of fiberglass or other insulating materials
– Copper: Used for creating conductive traces and pads
– Solder mask: A protective layer that covers the copper traces
– Silkscreen: Used for printing component labels and other markings on the PCB
3. What are the advantages of using PCBs in electronic devices?
PCBs offer several advantages in electronic devices, including:
– Compact size: PCBs enable the integration of multiple components into a small form factor
– Reliability: PCBs provide a stable and reliable platform for electrical connections
– Cost-effectiveness: PCBs can be mass-produced, reducing the overall cost of electronic devices
– Ease of maintenance: PCBs simplify the process of identifying and replacing faulty components
4. How are PCBs designed and manufactured?
The PCB design and manufacturing process typically involves the following steps:
1. Schematic design: Creating a schematic diagram that represents the electrical connections between components
2. PCB layout: Designing the physical layout of the PCB, including the placement of components and routing of traces
3. Fabrication: Manufacturing the PCB based on the designed layout
4. Assembly: Mounting and soldering components onto the PCB
5. Testing: Verifying the functionality and reliability of the assembled PCB
5. What are the future trends in PCB applications?
Some of the future trends in PCB applications include:
– Miniaturization: The increasing demand for smaller and more compact electronic devices will drive the development of smaller and more dense PCBs
– Flexible and stretchable PCBs: The growing interest in wearable technology and flexible electronics will lead to the development of PCBs that can bend and stretch without compromising functionality
– High-speed and high-frequency applications: The increasing demand for faster data transmission and processing will require PCBs that can handle high-speed and high-frequency signals
– Sustainable and eco-friendly materials: The push for environmentally friendly electronics will drive the development of PCBs made from biodegradable and recyclable materials
Conclusion
PCBs are essential components in a wide range of electronic devices and systems, enabling the efficient functioning and integration of various components. From consumer electronics to aerospace and defense, PCBs find applications in numerous industries, each with its own set of requirements and challenges. As technology continues to advance, PCBs will play an increasingly important role in shaping the future of electronics, driving innovation and enabling the development of new and exciting applications.
PCB Application | Key Characteristics |
---|---|
Consumer Electronics | Compact, cost-effective, and feature-rich |
Automotive Electronics | Rugged, reliable, and capable of withstanding harsh environments |
Medical Devices | High-quality, reliable, and designed for patient safety and comfort |
Industrial Automation | Rugged, reliable, and capable of handling complex control tasks |
Aerospace and Defense | Designed to meet stringent safety and reliability standards |
Internet of Things (IoT) | Compact, power-efficient, and capable of seamless communication |
As the demand for more advanced and sophisticated electronic devices continues to grow, the importance of PCBs in enabling these innovations cannot be overstated. By understanding the various applications of PCBs and their key characteristics, engineers and designers can create electronic systems that are more efficient, reliable, and cost-effective, ultimately benefiting end-users and driving technological progress across industries.
Leave a Reply