What is Plated Through-Hole (PTH) Technology in PCB?
Plated through-hole (PTH) technology is a crucial process in the production of printed circuit boards (PCBs). It involves creating holes in the PCB substrate and plating them with a conductive material, typically copper, to establish electrical connections between different layers of the board. PTH is essential for creating reliable and durable electrical connections in PCBs, especially in applications that require high mechanical strength and thermal stability.
The PTH Process
The PTH process consists of several steps:
- Drilling: Holes are drilled through the PCB substrate at specific locations based on the design requirements.
- Deburring: The drilled holes are cleaned and deburred to remove any rough edges or debris.
- Electroless copper deposition: A thin layer of copper is deposited onto the walls of the holes using an electroless plating process.
- Electrolytic copper plating: The holes are further plated with a thicker layer of copper using an electrolytic plating process to achieve the desired thickness and conductivity.
- Inspection: The plated holes are inspected for quality and conformance to specifications.
Advantages of PTH Technology
PTH technology offers several advantages over other methods of creating electrical connections in PCBs:
- Mechanical strength: PTH provides excellent mechanical strength and stability to the PCB Assembly, especially in applications that require high reliability and durability.
- Thermal conductivity: The plated holes act as thermal vias, allowing heat to dissipate efficiently from the components to the PCB substrate and preventing overheating.
- Electrical conductivity: PTH ensures reliable and low-resistance electrical connections between different layers of the PCB, minimizing signal loss and improving signal integrity.
- Compatibility: PTH is compatible with a wide range of components, including through-hole and surface-mount devices, making it a versatile choice for various PCB designs.
Applications of PTH in PCB
PTH technology finds applications in various industries and products, such as:
- Automotive electronics: PTH is used in Automotive PCBs to ensure reliable and durable electrical connections in harsh environmental conditions, such as high temperatures and vibrations.
- Aerospace and defense: PTH is essential in aerospace and defense applications, where high reliability and mechanical strength are critical for the proper functioning of electronic systems.
- Industrial control systems: PTH is used in industrial control PCBs to provide robust and stable electrical connections in demanding industrial environments.
- Medical devices: PTH is employed in medical device PCBs to ensure reliable and safe operation of electronic components in life-critical applications.
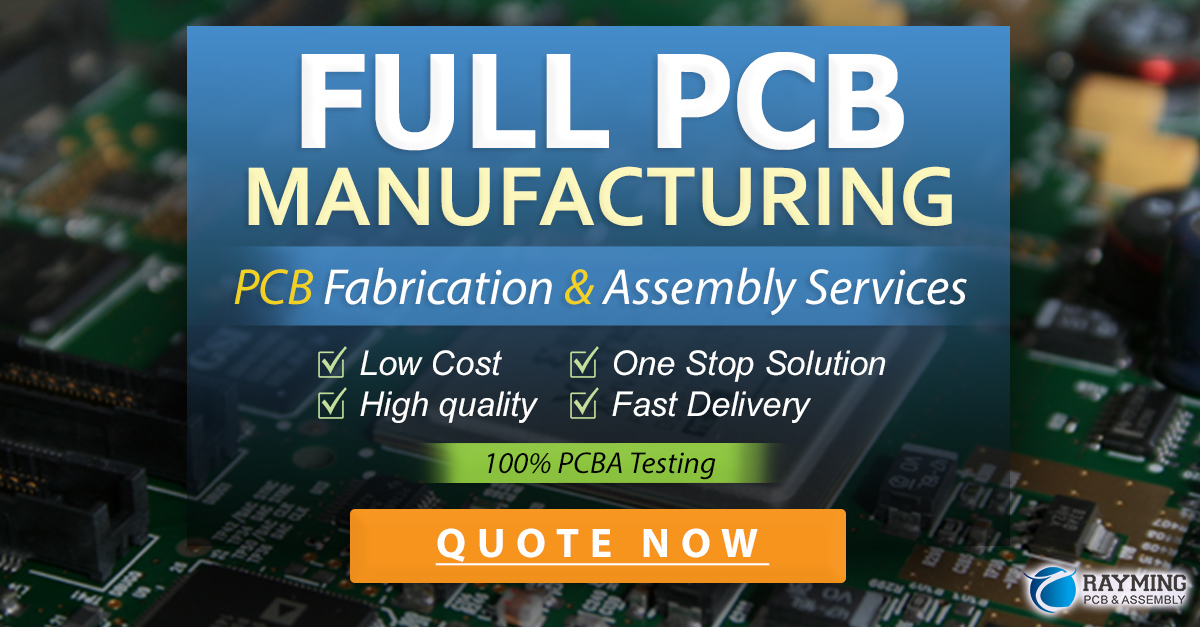
Challenges and Considerations in PTH
While PTH technology offers numerous benefits, there are some challenges and considerations to keep in mind:
- Hole size and aspect ratio: The size and aspect ratio of the plated holes can affect the reliability and manufacturability of the PCB. Smaller holes with higher aspect ratios are more challenging to plate uniformly and may require specialized equipment and processes.
- Material selection: The choice of PCB substrate material and plating chemistry can impact the quality and reliability of the plated holes. Different materials have varying thermal expansion coefficients and adhesion properties, which must be considered during the design and manufacturing process.
- Cost: PTH is generally more expensive than other methods of creating electrical connections, such as surface-mount technology (SMT), due to the additional processing steps and materials involved.
- Design constraints: PTH imposes certain design constraints, such as minimum hole size and spacing, which must be taken into account during the PCB layout and routing process.
Advancements in PTH Technology
Recent advancements in PTH technology have focused on improving the reliability, efficiency, and cost-effectiveness of the process:
- High-aspect-ratio plating: Developments in plating chemistry and equipment have enabled the plating of holes with higher aspect ratios, allowing for denser and more complex PCB designs.
- Selective plating: Selective plating techniques allow for the precise plating of specific areas or holes on the PCB, reducing material consumption and processing time.
- Automation: Automated PTH processing equipment has improved the consistency, throughput, and quality of the plating process, reducing human error and increasing efficiency.
- Alternative materials: Research into alternative plating materials, such as graphene and conductive polymers, has the potential to improve the performance and sustainability of PTH technology.
Conclusion
Plated through-hole technology remains a critical process in PCB production, offering numerous advantages in terms of mechanical strength, thermal conductivity, electrical conductivity, and compatibility. While there are challenges and considerations to keep in mind, advancements in PTH technology continue to improve the reliability, efficiency, and cost-effectiveness of the process. As electronic devices become more complex and demanding, PTH will continue to play a vital role in ensuring the proper functioning and durability of PCBs across various industries.
Frequently Asked Questions (FAQ)
-
What is the difference between PTH and surface-mount technology (SMT)?
PTH involves creating plated holes through the PCB substrate to establish electrical connections, while SMT involves mounting components directly onto the surface of the PCB without through-holes. -
Can PTH be used with surface-mount components?
Yes, PTH is compatible with both through-hole and surface-mount components, making it a versatile choice for various PCB designs. -
What factors affect the quality and reliability of plated through-holes?
Factors such as hole size, aspect ratio, material selection, and plating chemistry can impact the quality and reliability of plated through-holes. -
How does PTH contribute to the thermal management of PCBs?
The plated holes in PTH act as thermal vias, allowing heat to dissipate efficiently from the components to the PCB substrate, preventing overheating and improving thermal management. -
What are some recent advancements in PTH technology?
Recent advancements in PTH technology include high-aspect-ratio plating, selective plating, automation, and research into alternative plating materials such as graphene and conductive polymers.
Aspect | PTH | SMT |
---|---|---|
Electrical Connections | Through plated holes in the PCB substrate | Surface-mounted components without through-holes |
Mechanical Strength | Excellent mechanical strength and stability | Relatively lower mechanical strength |
Thermal Conductivity | Plated holes act as thermal vias for heat dissipation | Limited thermal conductivity through surface mounting |
Compatibility | Compatible with through-hole and surface-mount devices | Compatible primarily with surface-mount devices |
Cost | Generally more expensive due to additional processing | Typically more cost-effective for high-volume production |
Leave a Reply