How COVID-19 Disrupted Medical Electronics Supply Chains
One of the most immediate and severe impacts of the pandemic on the Medical PCB industry was the major disruption to global supply chains, especially in the early phases of the outbreak. Several key factors contributed to medical electronics supply chain issues:
- Lockdowns and closures of PCB production facilities in China and other manufacturing hubs
- Travel restrictions and freight transportation bottlenecks
- Shortages of raw materials and components
- Surge in demand for medical devices leading to depleted inventory
The table below shows the decrease in China’s PCB exports in early 2020 compared to 2019 as factories shut down to contain the virus:
Month | 2019 Exports (Million Units) | 2020 Exports (Million Units) | Percent Change |
---|---|---|---|
Jan | 1,785 | 1,327 | -25.6% |
Feb | 1,047 | 379 | -63.8% |
Mar | 1,842 | 1,035 | -43.8% |
Source: TrendForce
These supply shortages created a cascading effect, delaying production of critical medical equipment worldwide as manufacturers waited for PCB shipments. Ventilators, patient monitors, ultrasound machines, and COVID-19 test equipment faced increased lead times.
Mitigating Supply Chain Risks Post-Pandemic
As the initial shockwaves subsided, medical device companies took steps to make their supply chains more resilient against future disruptions:
- Diversifying suppliers across multiple geographic regions to avoid over-reliance on any single country
- Increasing inventory levels of essential components to cushion against temporary shortages
- Forming strategic partnerships with key suppliers to receive priority allocation of constrained parts
- Re-shoring some PCB manufacturing domestically to improve control and security of supply
Surging Demand for Medical Devices and PCBs
Respiratory and Ventilator Equipment
While some sectors saw sales decline during COVID-19, many medical device categories experienced unprecedented demand. Most notably, respiratory support and ventilator equipment was urgently needed to treat critically ill patients.
Ventilator Manufacturer | Pre-COVID Monthly Production | COVID Peak Monthly Production | Percent Increase |
---|---|---|---|
Philips Healthcare | 1,000 | 4,000 | +300% |
GE Healthcare | 2,500 | 10,000 | +400% |
Medtronic | 200 | 1,000 | +500% |
Source: Company reports
Ventilators require sophisticated PCBs to control air flow, pressure, and patient monitoring. Multilayer boards with fine pitch traces, high layer counts, and rigid-flex combinations are common. The spike in ventilator production drove a comparable increase in orders for these high-end medical PCBs.
Remote Patient Monitoring and Telehealth
Another segment that saw rapid growth due to COVID-19 was remote patient monitoring (RPM) and telehealth devices. To reduce exposure risks and preserve hospital capacity, more healthcare services were delivered remotely using electronic devices.
Common RPM medical devices include:
- Pulse oximeters
- Blood glucose meters
- ECG/EKG monitors
- Blood pressure monitors
- Digital stethoscopes
These products transmit patient vital signs to physicians, who can then provide consultations via secure video conferencing. Wearable RPM devices like smartwatches and wrist-worn health trackers also gained popularity.
The global RPM market is projected to reach $117 billion by 2025, up from $23 billion in 2020, a 38% CAGR. Telehealth as a whole could grow from $79 billion to $396 billion by 2027. This rapid adoption is expected to continue even after the pandemic subsides.
COVID-19 Testing Equipment
The development and mass production of COVID-19 testing equipment was another area of high demand for medical PCBs. RT-PCR machines to process viral RNA samples required complex PCB designs. Antibody and antigen test cassettes with electrochemical biosensors also contained PCBAs.
Leading medical device companies with strong PCB supply chains were able to rapidly scale up production of testing equipment:
Company | COVID-19 Test Type | Tests Shipped in 2020 |
---|---|---|
Abbott Labs | Molecular, Antigen | 300 million |
Roche Diagnostics | Molecular, Antibody | 100 million |
Cepheid | Molecular | 45 million |
Quidel | Antigen | 70 million |
Source: Company reports
Accurate and widely available COVID-19 tests were essential in controlling the pandemic’s spread. Medical PCB Manufacturers played a vital role in enabling the mass production of these critical diagnostic devices.
Long-Term Impacts on Medical PCB Industry
Accelerated Adoption of Advanced Technologies
COVID-19 highlighted the importance of medical devices in modern healthcare. In response, many medical PCB companies are investing in advanced manufacturing capabilities to meet the increased demand for miniaturized, high-density interconnect (HDI), and flexible boards.
Some of the key technology trends shaping the future of medical PCBs include:
- Increased use of flexible circuits and rigid-flex for wearable health monitors
- Wider adoption of COF and COB package types for ultra-compact devices
- More stringent cleanliness requirements to minimize leakage currents
- Tighter signal integrity controls for high-speed data transmission
- Expansion of microelectronics fabrication for next-gen microfluidics and lab-on-chip
By embracing these cutting-edge technologies, medical PCB specialists aim to enable the next wave of connected, intelligent, and data-driven medical devices.
Renewed Focus on Domestic Production
The supply chain turmoil of 2020 underscored the risks of relying heavily on offshore production. In response, initiatives are underway in the US and Europe to bolster domestic PCB manufacturing capacity, especially for sensitive medical and defense applications.
The US DoD recently announced a $14 million award to establish a medical electronics prototyping facility in California. Congresswoman Anna Eshoo introduced the “Printed Circuit Board Investment Act” to help revive American PCB production. Germany launched a €400 million “Hospital Future Act” to promote domestic medical equipment manufacturing.
While the geographical imbalances in global PCB production won’t disappear overnight, COVID-19 has sparked renewed efforts to cultivate local manufacturing ecosystems for greater resilience and self-sufficiency.
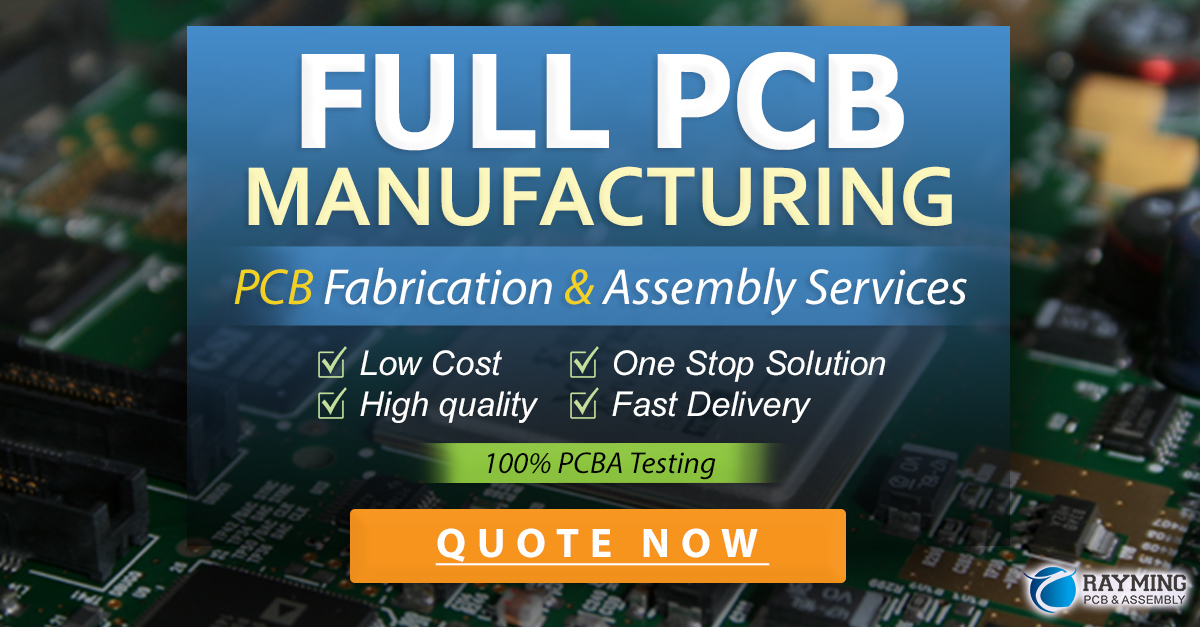
Frequently Asked Questions
What types of PCBs are used in medical ventilators?
Ventilators use a variety of PCBs including high layer count multilayers, rigid-flex boards, and HDI designs. Key requirements are reliability, compact form factors to fit inside portable units, and high cleanliness to avoid leakage in sensitive analog Sensor Circuits.
How did COVID-19 affect the supply of raw materials for PCBs?
The pandemic disrupted mining and refining of metals like copper and gold used in PCBs. There were also shortages of certain plastics, epoxies and films used in PCB substrates and solder masks. Freight and logistics bottlenecks further delayed shipments of raw materials.
Are lead times for medical PCBs back to pre-pandemic levels?
In most cases, lead times have improved significantly since the peak of the supply chain disruptions in early 2020. However, the recovery varies by factory location and PCB technology. Some specialized medical PCBs may still have extended lead times of 8-12 weeks or more.
What are some of the cleaning and contamination control standards for medical PCBs?
Key standards include IPC-6012 Medical Addendum which defines 4 levels of PCB cleanliness based on ROSE testing and Ion Chromatography results. IPC-6018 also provides guidelines for handling, packaging and traceability of medical PCBs to avoid contamination.
Will the medical PCB industry continue to grow after COVID-19 subsides?
Most analysts expect the medical device and PCB sectors to see strong long-term growth even after the pandemic due to aging populations, rising chronic disease prevalence, and accelerated adoption of digital health technologies. However, the pace of growth may moderate from the peak rates seen in 2020-2021.
Conclusion
COVID-19 created both immense challenges and opportunities for the medical PCB industry. While the initial supply chain disruptions were severe, the sector showed remarkable agility in adapting to meet the surge in demand for life-saving medical devices.
The pandemic also catalyzed wider adoption of advanced PCB technologies and re-shoring efforts that will benefit medical electronics for years to come. With the right strategic investments, medical PCB companies can emerge stronger and well-positioned to power the digital healthcare revolution in the post-pandemic era.
Leave a Reply