Introduction to PCB Environmental Control
Printed Circuit Boards (PCBs) are essential components in modern electronics. The manufacturing process of PCBs requires precise control over various environmental factors to ensure high quality and reliability. Two critical factors that significantly impact PCB production are light and moisture. In this article, we will explore the importance of controlling light and moisture in a PCB factory and discuss the methods and technologies used to achieve optimal environmental conditions.
The Impact of Light on PCB Manufacturing
Photoresist Sensitivity
Light plays a crucial role in the PCB manufacturing process, particularly in the photolithography stage. Photoresists, light-sensitive materials used to create circuit patterns on PCBs, are highly sensitive to specific wavelengths of light. Exposure to uncontrolled light sources can cause unintended polymerization or degradation of the photoresist, leading to defects in the final product.
Controlling Light in the PCB Factory
To mitigate the impact of light on photoresists, PCB factories implement strict light control measures:
-
Yellow Room Lighting: PCB manufacturing areas, especially those involving photoresist application and exposure, use yellow room lighting. Yellow light has a longer wavelength that does not affect most photoresists, allowing operators to work without causing unintended exposure.
-
UV Filtering: Windows and other light sources in the PCB factory are fitted with UV filters to block harmful ultraviolet radiation that can interact with photoresists.
-
Light Curtains and Partitions: Light curtains and partitions are used to separate different manufacturing zones and prevent light contamination between areas.
Light Measurement and Monitoring
Regular monitoring of light levels in the PCB factory is essential to maintain optimal conditions. Light meters, such as lux meters or radiometers, are used to measure the intensity and wavelength of light in various areas of the facility. These measurements help identify any deviations from the desired light levels and enable timely corrective actions.
Area | Recommended Light Level (lux) |
---|---|
Photoresist Coating Area | 100-300 |
Exposure Area | 500-1000 (yellow light) |
Etching Area | 500-1000 |
Inspection Area | 1000-2000 |
The Impact of Moisture on PCB Manufacturing
Moisture Sensitivity of PCBs
Moisture is another critical factor that can significantly affect the quality and reliability of PCBs. Excessive moisture can lead to various issues, including:
-
Delamination: Moisture can penetrate between the layers of the PCB, causing them to separate or delaminate, which can result in electrical failures.
-
Corrosion: Moisture can promote the growth of corrosion on metal surfaces, leading to reduced conductivity and potential short circuits.
-
Warpage: Uneven moisture absorption can cause PCBs to warp or twist, making them difficult to assemble or fit into their intended enclosures.
Controlling Moisture in the PCB Factory
To control moisture levels in the PCB factory, several strategies are employed:
-
Humidity Control: PCB manufacturing areas are equipped with humidity control systems, such as dehumidifiers or humidifiers, to maintain relative humidity within the recommended range of 30-60%.
-
Moisture Barrier Bags (MBBs): PCBs are often stored and transported in moisture barrier bags, which are designed to prevent moisture ingress and protect the boards from humidity fluctuations.
-
Baking: PCBs that have been exposed to excessive moisture can be baked in specialized ovens to remove the absorbed moisture before further processing or assembly.
Moisture Measurement and Monitoring
Continuous monitoring of moisture levels in the PCB factory is crucial to ensure consistent product quality. Relative humidity sensors and dew point meters are used to measure and record moisture levels in different areas of the facility. These measurements help maintain the desired humidity range and trigger alerts if moisture levels exceed acceptable limits.
Relative Humidity Range | Impact on PCBs |
---|---|
< 30% | Potential static charge buildup |
30-60% | Optimal range for PCB manufacturing |
> 60% | Increased risk of moisture-related issues |
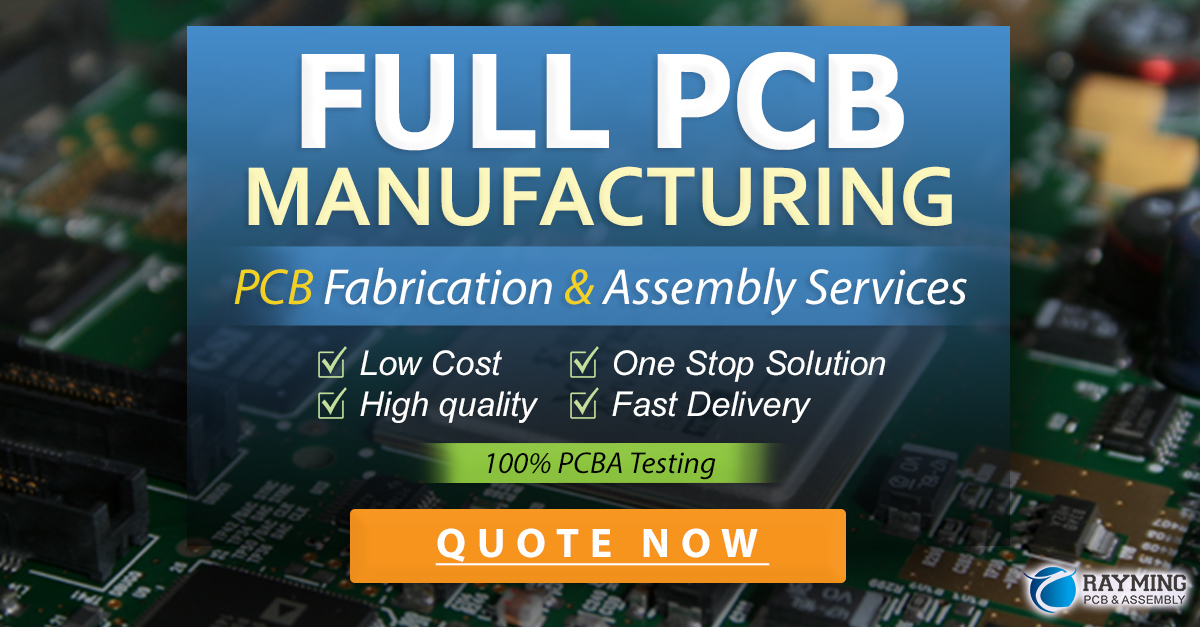
Best Practices for PCB Environmental Control
To achieve optimal light and moisture control in a PCB factory, consider the following best practices:
-
Implement a comprehensive environmental monitoring system that continuously measures and records light and moisture levels in critical areas of the facility.
-
Establish clear protocols for maintaining the desired light and moisture levels, including regular calibration of control systems and sensors.
-
Train personnel on the importance of environmental control and proper handling of PCBs to minimize exposure to uncontrolled light and moisture.
-
Use appropriate packaging materials, such as moisture barrier bags and desiccants, to protect PCBs during storage and transportation.
-
Regularly audit and review environmental control processes to identify areas for improvement and ensure ongoing compliance with industry standards and customer requirements.
Frequently Asked Questions (FAQ)
-
Q: What is the recommended relative humidity range for PCB manufacturing?
A: The optimal relative humidity range for PCB manufacturing is between 30-60%. This range minimizes the risk of moisture-related issues while preventing static charge buildup. -
Q: Why are yellow rooms used in PCB manufacturing?
A: Yellow rooms are used in PCB manufacturing because yellow light has a longer wavelength that does not affect most photoresists used in the photolithography process. This allows operators to work with photoresist-coated PCBs without causing unintended exposure. -
Q: How can moisture cause delamination in PCBs?
A: Moisture can penetrate between the layers of a PCB, weakening the adhesive bonds that hold the layers together. As the moisture expands and contracts with temperature changes, it can cause the layers to separate or delaminate, leading to electrical failures. -
Q: What is the purpose of baking PCBs?
A: Baking PCBs in specialized ovens is a process used to remove excess moisture that the boards may have absorbed during manufacturing or storage. This helps to prevent moisture-related issues, such as delamination or corrosion, during subsequent processing or assembly. -
Q: How often should environmental monitoring be conducted in a PCB factory?
A: Environmental monitoring, including light and moisture level measurements, should be conducted continuously in a PCB factory. This allows for real-time tracking of environmental conditions and enables prompt corrective actions if any deviations from the desired levels are detected.
Conclusion
Controlling light and moisture levels in a PCB factory is essential for ensuring the quality, reliability, and longevity of printed circuit boards. By implementing strict environmental control measures, such as yellow room lighting, humidity control systems, and moisture barrier packaging, PCB manufacturers can minimize the impact of these factors on their products.
Regular monitoring, adherence to best practices, and continuous improvement of environmental control processes are key to maintaining optimal conditions in the PCB factory. By prioritizing the control of light and moisture, manufacturers can deliver high-quality PCBs that meet the demanding requirements of modern electronics applications.
Leave a Reply