What is Solder?
Solder is a fusible metal alloy used to create a permanent bond between two or more metal surfaces. It is commonly used in electronic assembly and repair to join components to printed circuit boards (PCBs) or to create electrical connections between wires. Solder typically consists of a combination of tin (Sn) and lead (Pb), although lead-free alternatives are becoming increasingly popular due to environmental and health concerns.
Types of Solder
There are several types of solder available, each with its own unique properties and applications. Let’s explore some of the most common types:
Lead-based Solder
Traditionally, lead-based solder was the most widely used type in the electronics industry. It typically consists of a 60/40 ratio of tin to lead (Sn60/Pb40). Lead-based solder offers excellent wetting properties, making it easy to work with and resulting in reliable connections. However, due to the toxicity of lead and its harmful effects on the environment and human health, the use of lead-based solder has been largely phased out in many countries.
Lead-free Solder
As an alternative to lead-based solder, lead-free solder alloys have gained popularity in recent years. These alloys are typically composed of tin, silver, and copper (Sn/Ag/Cu) in various proportions. Some common lead-free solder alloys include:
- SAC305 (Sn96.5/Ag3.0/Cu0.5)
- SAC387 (Sn95.5/Ag3.8/Cu0.7)
- SN100C (Sn99.3/Cu0.7/Ni+Ge)
Lead-free solder offers comparable performance to lead-based solder while being more environmentally friendly. However, it typically requires higher melting temperatures and may have slightly different wetting characteristics.
Low-temperature Solder
Low-temperature solder alloys have a lower melting point compared to standard solder alloys. They are often used in applications where heat-sensitive components are involved or when soldering on temperature-sensitive substrates. Some examples of low-temperature solder include:
- Bismuth-based alloys (Bi/Sn/Ag)
- Indium-based alloys (In/Sn)
These alloys melt at temperatures below 200°C, reducing the risk of thermal damage to components during the soldering process.
Factors to Consider When Choosing Solder
When selecting the best solder for your circuit board project, there are several key factors to consider:
Melting Temperature
The melting temperature of the solder is an important consideration, especially when working with heat-sensitive components. Choose a solder with a melting temperature that is appropriate for your specific application. Lead-free solder generally has a higher melting point compared to lead-based solder.
Wetting Properties
Wetting refers to the ability of the molten solder to flow and adhere to the surfaces being joined. Good wetting properties ensure a strong and reliable connection. Consider the wetting characteristics of the solder alloy and ensure compatibility with the materials you are soldering.
Mechanical Strength
The mechanical strength of the solder joint is crucial for the long-term reliability of your circuit board. Solder alloys with higher tensile strength and shear strength provide better durability and resistance to mechanical stress. Lead-free solder alloys often exhibit higher mechanical strength compared to lead-based solder.
Flux Type
Flux is a chemical compound that helps remove oxidation and promotes the flow of solder during the soldering process. Solder wire typically comes with a flux core, which can be either rosin-based or water-soluble. Rosin-based flux is commonly used for electronic soldering and provides good wetting and protection against oxidation. Water-soluble flux is easier to clean after soldering but may require additional cleaning steps.
Environmental and Health Considerations
When selecting solder, it’s important to consider the environmental and health implications. Lead-based solder is known to have toxic effects and has been restricted or banned in many countries. Opting for lead-free solder alternatives is a more environmentally friendly and safer choice.
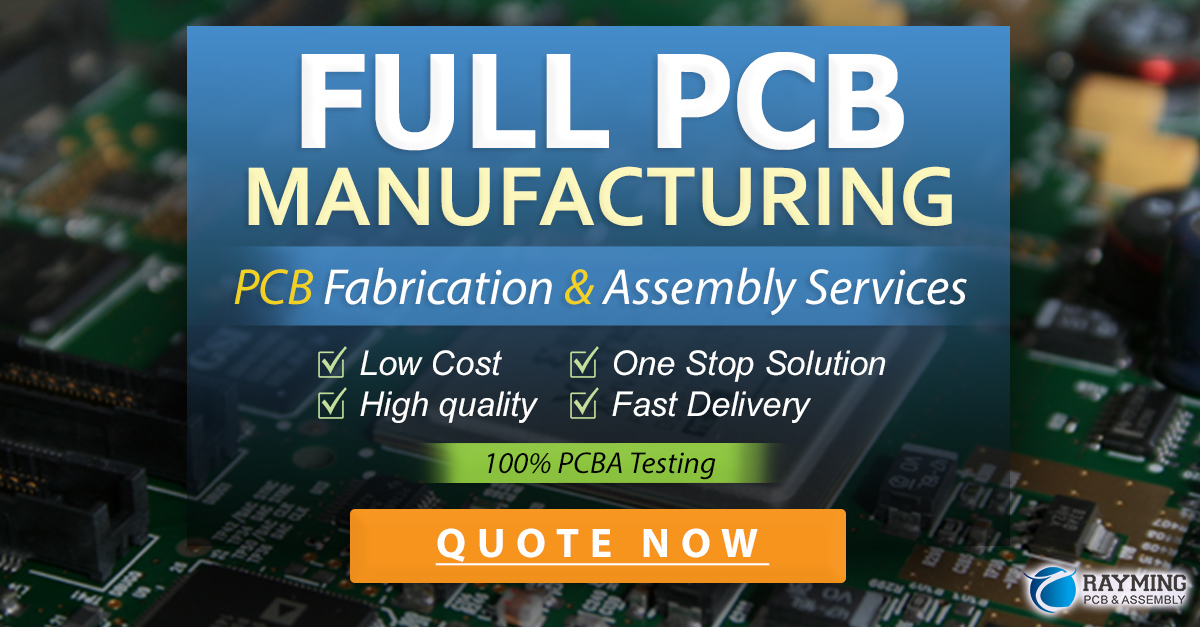
Solder Selection Chart
To help you make an informed decision, here’s a comparison chart of common solder alloys and their properties:
Solder Alloy | Composition | Melting Range (°C) | Wetting | Mechanical Strength | Applications |
---|---|---|---|---|---|
Sn60/Pb40 | 60% Sn, 40% Pb | 183-190 | Excellent | Good | General purpose (phasing out) |
SAC305 | 96.5% Sn, 3% Ag, 0.5% Cu | 217-220 | Good | Very Good | Lead-free alternative for general purpose |
SAC387 | 95.5% Sn, 3.8% Ag, 0.7% Cu | 217-220 | Very Good | Excellent | High-reliability lead-free applications |
SN100C | 99.3% Sn, 0.7% Cu, Ni+Ge | 227-228 | Good | Good | Lead-free alternative for wave soldering |
Bi/Sn/Ag | Various compositions | 139-170 | Good | Fair | Low-temperature applications |
Frequently Asked Questions (FAQ)
-
Q: What is the difference between lead-based and lead-free solder?
A: Lead-based solder contains lead (Pb) as one of its main components, typically in a 60/40 ratio with tin (Sn). Lead-free solder, on the other hand, uses alternative alloys without lead, such as tin-silver-copper (SAC) alloys. Lead-free solder is becoming more prevalent due to environmental and health concerns associated with lead. -
Q: Can I mix different types of solder?
A: Mixing different types of solder is generally not recommended, as it can lead to incompatibility issues and poor solder joint quality. It’s best to stick with the same type of solder throughout your project to ensure consistent properties and performance. -
Q: What is the shelf life of solder?
A: The shelf life of solder depends on various factors, such as storage conditions and the type of solder. Generally, solder has a shelf life of several years when stored properly in a cool, dry place. However, solder wire with flux may have a shorter shelf life due to the degradation of the flux over time. -
Q: How do I choose the right solder diameter?
A: The diameter of the solder wire should be chosen based on the size of the components and the soldering iron tip you are using. For smaller components and fine-pitch soldering, a thinner solder wire (e.g., 0.5mm or 0.8mm) is preferred. For larger components and general-purpose soldering, a thicker solder wire (e.g., 1.0mm or 1.2mm) can be used. -
Q: Can I use lead-free solder on old circuit boards that were previously soldered with lead-based solder?
A: Yes, you can use lead-free solder on circuit boards that were previously soldered with lead-based solder. However, keep in mind that lead-free solder typically requires higher soldering temperatures, so adjust your soldering iron accordingly. Additionally, ensure proper cleaning of the old solder joints before applying the new lead-free solder.
Conclusion
Choosing the best solder for your circuit board project is essential for creating strong and reliable connections. Consider factors such as melting temperature, wetting properties, mechanical strength, flux type, and environmental concerns when making your selection. Lead-free solder alloys, such as SAC305 and SAC387, offer excellent performance and are a safer alternative to lead-based solder.
Remember to always follow proper soldering techniques, use the appropriate tools, and take necessary safety precautions when working with solder. With the right solder choice and proper soldering practices, you can ensure the success and longevity of your electronic projects.
Leave a Reply