Introduction to Teflon PCB
Teflon PCB, also known as PTFE (Polytetrafluoroethylene) PCB, is a specialized type of printed circuit board that utilizes Teflon as the base material instead of the more commonly used FR-4. Teflon is a synthetic fluoropolymer known for its exceptional properties, including high thermal stability, low dielectric constant, and excellent chemical resistance. These characteristics make Teflon PCBs an ideal choice for applications that require high-frequency performance, low signal loss, and the ability to withstand harsh environmental conditions.
Advantages of Teflon PCB
-
Low Dielectric Constant: Teflon has a low dielectric constant (typically around 2.1), which reduces signal propagation delay and minimizes signal loss, making it suitable for high-frequency applications.
-
High Thermal Stability: Teflon PCBs can withstand extreme temperatures ranging from -200°C to +260°C, making them suitable for applications in aerospace, military, and industrial sectors.
-
Excellent Chemical Resistance: Teflon is resistant to most chemicals, solvents, and acids, ensuring the longevity and reliability of the PCB in harsh environments.
-
Low Moisture Absorption: Teflon has a very low moisture absorption rate, which prevents the PCB from absorbing moisture and maintains its electrical properties over time.
-
Smooth Surface: The smooth surface of Teflon PCBs allows for easy trace routing and reduces the risk of signal reflections, resulting in improved signal integrity.
Applications of Teflon PCB
Teflon PCBs find applications in various industries where high-frequency performance, reliability, and durability are critical. Some of the key applications include:
-
Aerospace and Defense: Teflon PCBs are used in radar systems, satellite communication equipment, and avionics due to their ability to withstand extreme temperatures and harsh environments.
-
Telecommunications: High-frequency communication devices, such as 5G networks, benefit from the low dielectric constant and low signal loss properties of Teflon PCBs.
-
Medical Devices: Teflon PCBs are used in medical equipment that requires high reliability and resistance to chemicals and sterilization processes.
-
Industrial Automation: In industrial settings where PCBs are exposed to high temperatures, chemicals, and moisture, Teflon PCBs provide a reliable solution.
-
Automotive Electronics: Teflon PCBs are used in automotive radar systems, engine control units, and other electronic components that require high-frequency performance and durability.
Manufacturing Process of Teflon PCB
The manufacturing process of Teflon PCBs differs from that of traditional FR-4 PCBs due to the unique properties of Teflon. The process involves the following steps:
-
Material Selection: The appropriate Teflon laminate is selected based on the specific requirements of the application, such as the dielectric constant, thickness, and copper cladding.
-
Drilling: Holes are drilled into the Teflon laminate to accommodate through-hole components and vias. Specialized drills and strict process control are required to prevent delamination and ensure hole quality.
-
Plating: The drilled holes are plated with copper to establish electrical connections between the layers of the PCB. Electroless plating is commonly used for Teflon PCBs.
-
Patterning: The desired circuit pattern is transferred onto the Teflon laminate using photolithography. The photoresist is applied, exposed, and developed to create the circuit pattern.
-
Etching: The unwanted copper is removed from the laminate using a chemical etching process, leaving only the desired circuit pattern.
-
Solder Mask Application: A solder mask is applied to the PCB to protect the copper traces and prevent short circuits. The solder mask also helps in the soldering process by restricting the solder to the exposed pads.
-
Surface Finish: A surface finish, such as ENIG (Electroless Nickel Immersion Gold) or HASL (Hot Air Solder Leveling), is applied to the exposed pads to enhance solderability and protect the copper from oxidation.
-
Silk Screen Printing: The component designators, logos, and other markings are printed onto the PCB using silk screen printing.
-
Cutting and Profiling: The PCB panel is cut into individual boards, and the edges are profiled to the desired shape and size.
Challenges in Manufacturing Teflon PCB
Manufacturing Teflon PCBs presents some unique challenges due to the material’s properties:
-
Delamination: Teflon has a low surface energy, which can lead to poor adhesion between the laminate and the copper layer. Proper surface treatment and careful process control are necessary to prevent delamination.
-
Drilling: Teflon is a soft material, and drilling holes can cause the material to deform or create rough hole walls. Specialized drills and optimized drilling parameters are required to ensure hole quality.
-
Plating: The low surface energy of Teflon can result in poor copper adhesion during the plating process. Special surface treatments and plating chemistries are used to overcome this challenge.
-
Dimensional Stability: Teflon has a high coefficient of thermal expansion (CTE), which can cause dimensional changes during the manufacturing process. Proper material selection and process control are essential to maintain the dimensional stability of the PCB.
Teflon PCB Material Properties
Teflon, or PTFE, is a synthetic fluoropolymer with unique properties that make it an excellent choice for high-frequency and high-reliability PCB applications. Some of the key material properties of Teflon are:
Dielectric Constant
The dielectric constant (Dk) of a material determines its ability to store electric energy. A low dielectric constant is desirable for high-frequency applications as it reduces signal propagation delay and minimizes signal loss. Teflon has a dielectric constant of around 2.1, which is significantly lower than that of FR-4 (typically 4.2 to 4.6).
Material | Dielectric Constant (Dk) |
---|---|
Teflon (PTFE) | 2.1 |
FR-4 | 4.2 – 4.6 |
Rogers RO4003C | 3.38 |
Rogers RO4350B | 3.48 |
Dissipation Factor
The dissipation factor (Df) is a measure of the energy loss in a material when subjected to an alternating electric field. A low dissipation factor indicates lower signal loss and is preferred for high-frequency applications. Teflon has a very low dissipation factor, typically around 0.0002 to 0.0005, which is significantly lower than that of FR-4 (0.02).
Material | Dissipation Factor (Df) |
---|---|
Teflon (PTFE) | 0.0002 – 0.0005 |
FR-4 | 0.02 |
Rogers RO4003C | 0.0027 |
Rogers RO4350B | 0.0037 |
Thermal Stability
Teflon PCBs can withstand extreme temperatures, ranging from -200°C to +260°C, without significant degradation in their mechanical and electrical properties. This thermal stability makes Teflon PCBs suitable for applications in harsh environments, such as aerospace, military, and industrial sectors.
Chemical Resistance
Teflon is resistant to most chemicals, solvents, and acids, ensuring the longevity and reliability of the PCB in harsh environments. This property is particularly valuable in applications where the PCB may be exposed to chemicals, such as in medical devices or industrial automation.
Moisture Absorption
Moisture absorption can negatively impact the electrical properties and dimensional stability of a PCB. Teflon has a very low moisture absorption rate, typically less than 0.01%, which helps maintain its electrical properties and prevents moisture-related issues.
Material | Moisture Absorption |
---|---|
Teflon (PTFE) | < 0.01% |
FR-4 | 0.10% – 0.20% |
Rogers RO4003C | 0.06% |
Rogers RO4350B | 0.05% |
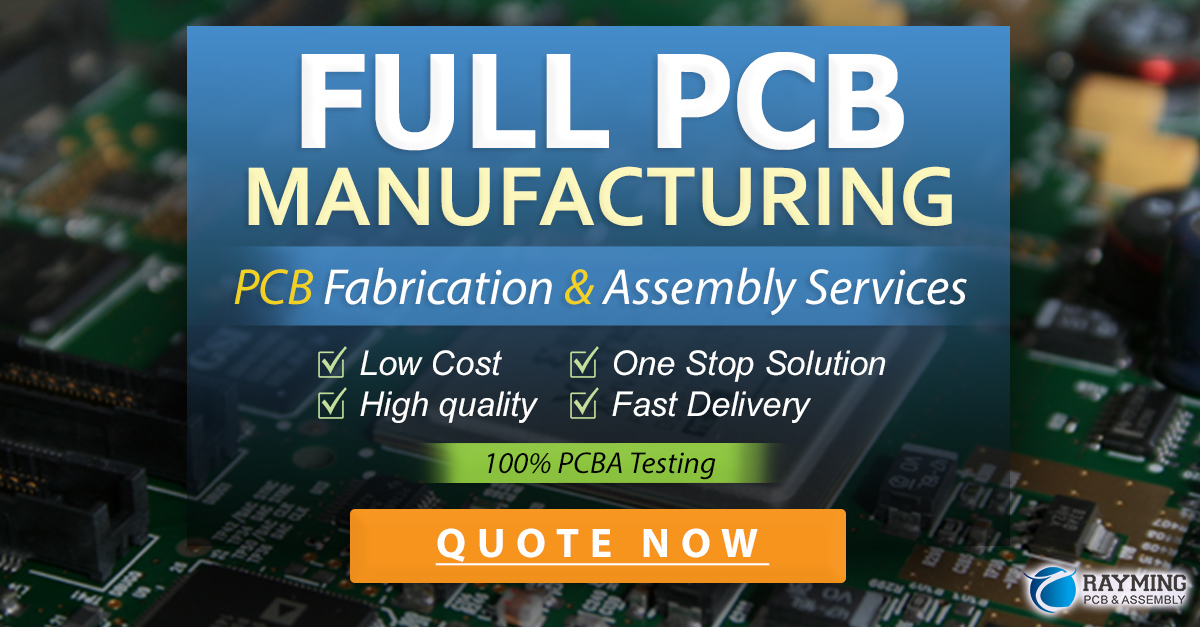
Designing with Teflon PCB
Designing with Teflon PCBs requires consideration of the material’s unique properties and the specific requirements of the application. Some key factors to consider when designing Teflon PCBs include:
Signal Integrity
The low dielectric constant and dissipation factor of Teflon make it an excellent choice for high-frequency applications where signal integrity is critical. However, designers must still consider factors such as impedance matching, trace geometry, and via placement to optimize signal integrity.
Thermal Management
Although Teflon has excellent thermal stability, it is essential to consider the thermal management of the PCB, especially in high-power applications. Designers should incorporate appropriate thermal management techniques, such as the use of thermal vias, heatsinks, and proper component placement, to ensure reliable operation.
Mechanical Considerations
Teflon’s soft nature and high CTE require special consideration during the design and manufacturing process. Designers should work closely with the PCB manufacturer to ensure proper material selection, hole wall quality, and dimensional stability.
Cost
Teflon PCBs are generally more expensive than traditional FR-4 PCBs due to the higher material cost and specialized manufacturing processes required. Designers should consider the cost implications and justify the use of Teflon based on the specific application requirements.
FAQ
-
Q: What is the main difference between Teflon PCB and FR-4 PCB?
A: The main difference between Teflon PCB and FR-4 PCB is the base material. Teflon PCBs use PTFE (Polytetrafluoroethylene) as the dielectric material, while FR-4 PCBs use a flame-retardant epoxy-glass composite. Teflon has a lower dielectric constant, lower dissipation factor, and higher thermal stability compared to FR-4. -
Q: Are Teflon PCBs suitable for all applications?
A: Teflon PCBs are particularly suitable for high-frequency applications, harsh environments, and applications that require high reliability. However, they may not be the most cost-effective solution for all applications. The decision to use Teflon PCBs should be based on the specific requirements of the application, such as signal integrity, thermal stability, and chemical resistance. -
Q: Can Teflon PCBs be manufactured using the same processes as FR-4 PCBs?
A: While some of the manufacturing processes for Teflon PCBs are similar to those used for FR-4 PCBs, there are specific challenges and considerations due to Teflon’s unique properties. The low surface energy of Teflon can lead to issues with copper adhesion and delamination, requiring specialized surface treatments and plating chemistries. Additionally, the soft nature of Teflon requires careful drilling and handling to ensure hole quality and dimensional stability. -
Q: How do the costs of Teflon PCBs compare to other PCB materials?
A: Teflon PCBs are generally more expensive than FR-4 PCBs due to the higher cost of the Teflon material and the specialized manufacturing processes required. However, the cost may be justified for applications that require the unique properties of Teflon, such as high-frequency performance, thermal stability, and chemical resistance. The cost of Teflon PCBs is typically comparable to other high-performance PCB materials, such as Rogers laminates. -
Q: Are there any specific design guidelines for Teflon PCBs?
A: When designing Teflon PCBs, it is essential to consider the material’s unique properties and work closely with the PCB manufacturer. Some specific design guidelines include: - Optimizing trace geometry and via placement for signal integrity
- Incorporating appropriate thermal management techniques
- Considering the material’s soft nature and high CTE during the design and manufacturing process
- Justifying the use of Teflon based on the specific application requirements and cost implications
Conclusion
Teflon PCBs offer unique properties that make them an excellent choice for high-frequency, high-reliability, and harsh-environment applications. With a low dielectric constant, low dissipation factor, high thermal stability, and excellent chemical resistance, Teflon PCBs can provide superior performance compared to traditional FR-4 PCBs.
However, designing and manufacturing Teflon PCBs requires careful consideration of the material’s properties and specialized processes. Designers must work closely with PCB manufacturers to ensure proper material selection, signal integrity, thermal management, and mechanical stability.
While Teflon PCBs may not be the most cost-effective solution for all applications, their unique properties make them an invaluable option for industries such as aerospace, defense, telecommunications, medical devices, and industrial automation. As technology continues to advance and the demand for high-performance electronics grows, Teflon PCBs will likely play an increasingly important role in enabling the next generation of electronic devices and systems.
Leave a Reply