Introduction to PCB Layout
Printed Circuit Board (PCB) layout is a critical step in the design and manufacture of electronic devices. A well-designed PCB layout ensures that the electronic components are correctly placed, interconnected, and function as intended. It also plays a crucial role in the overall performance, reliability, and manufacturability of the final product. This article will discuss various strategies and best practices for designing efficient and effective PCB layouts.
Understanding the Basics of PCB Layout
Key Components of a PCB
A PCB consists of several key components that work together to create a functional electronic device. These components include:
- Substrate: The base material on which the electronic components are mounted and interconnected.
- Copper Layers: Thin layers of copper that form the conductive pathways for electrical signals.
- Solder Mask: A protective layer that covers the copper traces, leaving only the exposed areas for soldering components.
- Silkscreen: Text and symbols printed on the PCB for component identification and assembly instructions.
- Vias: Conductive holes that allow electrical connections between different layers of the PCB.
PCB Layer Stackup
PCBs can have multiple layers, depending on the complexity of the design and the required functionality. A typical PCB layer stackup consists of:
- Top Layer: Usually contains the main components and their interconnections.
- Ground Plane: A solid copper layer that provides a low-impedance return path for electrical currents.
- Power Plane: A solid copper layer that distributes power to the components on the PCB.
- Signal Layers: Additional layers that contain the interconnections between components.
- Bottom Layer: Often used for additional components and connectors.
Planning the PCB Layout
Schematic Design
Before starting the PCB layout, it is essential to have a complete and accurate schematic design. The schematic should include all the necessary components, their electrical connections, and any specific requirements such as power supply voltages, signal integrity, and EMC considerations.
Component Placement
Once the schematic is finalized, the next step is to place the components on the PCB. Consider the following factors when placing components:
- Functionality: Group components that work together in close proximity to minimize signal path lengths and reduce noise.
- Mechanical Constraints: Consider the physical dimensions of the components and the available space on the PCB.
- Thermal Management: Place heat-generating components away from temperature-sensitive components and provide adequate cooling.
- Manufacturing: Ensure that the component placement allows for easy assembly and soldering.
Routing Strategies
After placing the components, the next step is to route the electrical connections between them. Consider the following strategies when routing the PCB:
- Signal Integrity: Route critical signals first, keeping them as short and direct as possible to minimize signal distortion and crosstalk.
- Power Distribution: Provide adequate power distribution to all components, using wide traces and power planes where necessary.
- Grounding: Create a solid ground plane to provide a low-impedance return path for electrical currents and minimize noise.
- EMC: Follow EMC guidelines to minimize electromagnetic interference, such as using ground shields and avoiding sharp bends in traces.
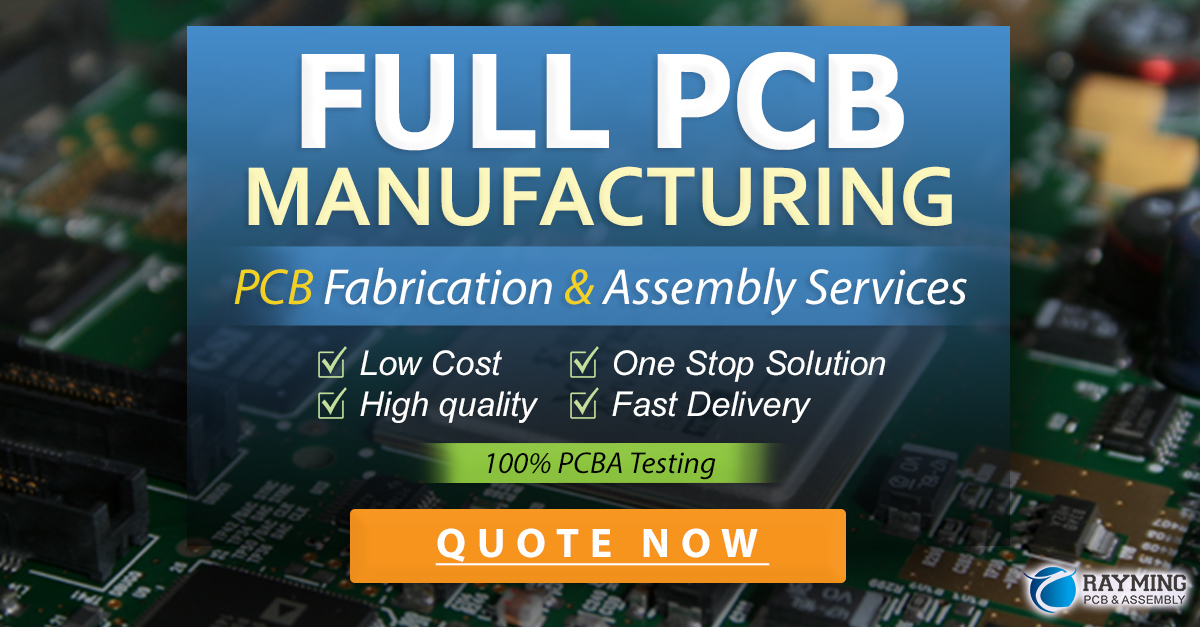
Advanced PCB Layout Techniques
High-Speed Design Considerations
When designing high-speed PCBs, additional considerations are necessary to ensure signal integrity and minimize noise. Some techniques include:
- Impedance Matching: Match the impedance of the traces to the characteristic impedance of the signal source and load to minimize reflections.
- Length Matching: Match the lengths of critical signal paths to ensure synchronous arrival of signals at their destinations.
- Differential Pairs: Use differential signaling for high-speed signals to minimize noise and crosstalk.
- Decoupling Capacitors: Place decoupling capacitors close to the power pins of ICs to provide a stable power supply and reduce high-frequency noise.
Thermal Management
Proper thermal management is crucial for the reliability and longevity of electronic components. Some techniques for effective thermal management include:
- Copper Pours: Use large copper pours connected to the ground plane to dissipate heat from components.
- Thermal Vias: Place thermal vias under heat-generating components to transfer heat to the other side of the PCB.
- Heatsinks: Use heatsinks to dissipate heat from high-power components.
- Airflow: Ensure adequate airflow over the PCB to remove heat from the components.
Manufacturability
Designing a PCB with manufacturability in mind can save time and costs in the long run. Some considerations for manufacturability include:
- Design for Assembly (DFA): Choose components and package sizes that are easy to assemble and solder.
- Design for Manufacturing (DFM): Follow the manufacturing capabilities and guidelines of the PCB fabricator, such as minimum trace widths and spacings.
- Panelization: Group multiple PCBs on a single panel to reduce manufacturing costs.
- Testability: Provide test points and access to critical signals for easy testing and debugging.
PCB Layout Tools and Software
There are various PCB layout tools and software available in the market that can help designers create efficient and effective PCB layouts. Some popular options include:
Software | Vendor | Key Features |
---|---|---|
Altium Designer | Altium | Comprehensive PCB design suite with 3D capabilities |
Eagle | Autodesk | User-friendly interface, extensive component libraries |
KiCad | Open Source | Free and open-source, growing community support |
OrCAD | Cadence | Powerful simulation and analysis tools |
PADS | Mentor Graphics | Scalable solution for complex PCB designs |
Conclusion
Designing an efficient and effective PCB layout requires careful planning, attention to detail, and adherence to best practices. By understanding the basics of PCB layout, planning the component placement and routing strategies, and applying advanced techniques for high-speed design, thermal management, and manufacturability, designers can create PCBs that meet the functional and performance requirements of their electronic devices.
FAQs
-
Q: What is the importance of a well-designed PCB layout?
A: A well-designed PCB layout ensures the correct placement and interconnection of electronic components, leading to better performance, reliability, and manufacturability of the final product. -
Q: What are the key components of a PCB?
A: The key components of a PCB include the substrate, copper layers, solder mask, silkscreen, and vias. -
Q: What factors should be considered when placing components on a PCB?
A: When placing components on a PCB, consider factors such as functionality, mechanical constraints, thermal management, and ease of manufacturing. -
Q: What are some techniques for ensuring signal integrity in high-speed PCB designs?
A: Techniques for ensuring signal integrity in high-speed PCB designs include impedance matching, length matching, using differential pairs, and placing decoupling capacitors close to IC power pins. -
Q: What are some popular PCB layout tools and software?
A: Some popular PCB layout tools and software include Altium Designer, Eagle, KiCad, OrCAD, and PADS, each with their own unique features and capabilities.
Leave a Reply