Introduction to PCB Thickness
Printed Circuit Boards (PCBs) are essential components in modern electronic devices. They provide a platform for mounting and interconnecting electronic components, allowing for the creation of complex circuits. One crucial aspect of PCB design is choosing the appropriate thickness. PCB thickness plays a significant role in the overall performance, reliability, and manufacturability of the board. In this article, we will delve into the world of standard PCB thickness and help you determine the right standards for your specific application.
Understanding PCB Thickness Measurements
Before we explore the various standard PCB thicknesses, it’s essential to understand how PCB thickness is measured. PCB thickness is typically expressed in either millimeters (mm) or mils (thousandths of an inch). One mil is equal to 0.0254 mm. For example, a PCB with a thickness of 1.6 mm is equivalent to approximately 63 mils.
PCB thickness is determined by the combined thickness of the copper layers, substrate material, and any additional layers such as solder mask or silkscreen. The substrate material, which is usually made of FR-4 (a type of fiberglass), contributes the most to the overall thickness of the PCB.
Standard PCB Thickness Options
There are several standard PCB thicknesses available in the market, each suitable for different applications and requirements. Let’s take a closer look at the most common PCB thickness options:
0.4 mm (16 mils)
- Ultrathin PCBs
- Suitable for compact and lightweight devices
- Commonly used in smartwatches, wearables, and small sensors
- Limited to single or double-layer designs
- Requires specialized manufacturing processes
0.6 mm (24 mils)
- Thin PCBs
- Ideal for space-constrained applications
- Used in mobile phones, tablets, and compact electronics
- Supports up to four layers
- Offers a balance between thickness and manufacturability
0.8 mm (31 mils)
- Slim PCBs
- Widely used in consumer electronics and portable devices
- Suitable for four to six-layer designs
- Provides good mechanical stability and durability
- Allows for moderate component density
1.0 mm (39 mils)
- Standard thickness for many applications
- Supports six to eight layers
- Offers excellent mechanical strength and rigidity
- Suitable for a wide range of electronic devices
- Provides ample space for component placement and routing
1.2 mm (47 mils)
- Robust PCBs
- Ideal for applications requiring higher layer counts (eight to ten layers)
- Offers increased mechanical stability and durability
- Commonly used in industrial and automotive electronics
- Provides better heat dissipation compared to thinner PCBs
1.6 mm (63 mils)
- Thick PCBs
- Suitable for high-power and high-reliability applications
- Supports ten or more layers
- Offers excellent mechanical strength and thermal management
- Used in aerospace, military, and medical equipment
- Allows for the integration of heavy components and connectors
2.0 mm (79 mils) and above
- Extra-thick PCBs
- Used in specialized applications requiring extreme durability
- Supports high layer counts and complex designs
- Provides superior mechanical strength and thermal dissipation
- Commonly found in industrial control systems, power electronics, and backplanes
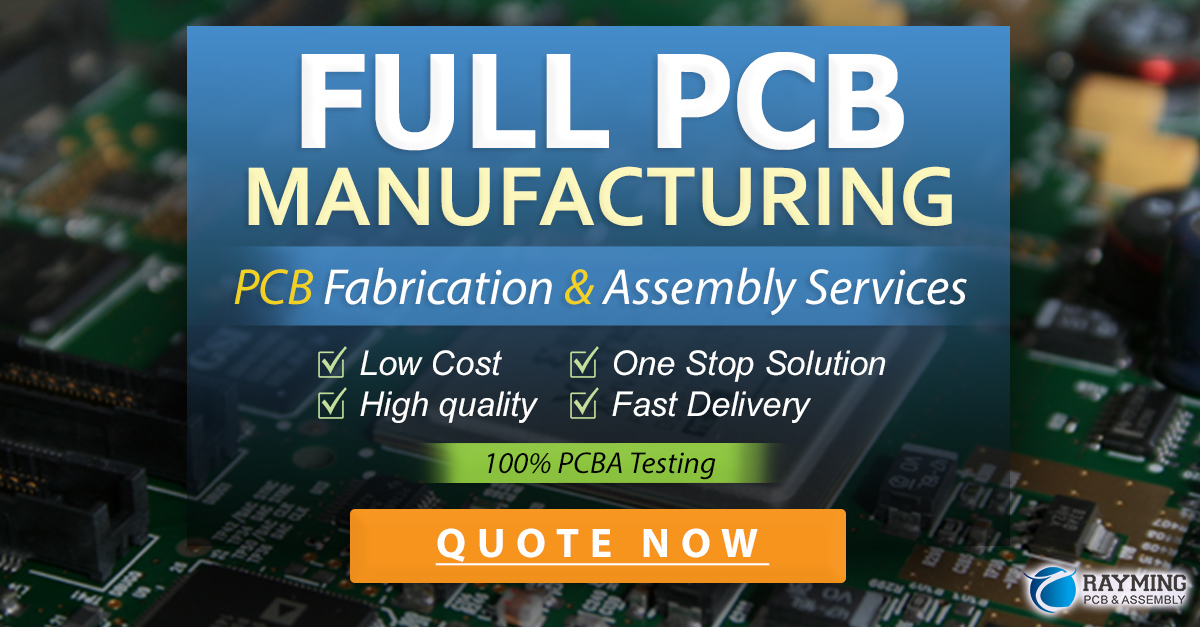
Factors Influencing PCB Thickness Selection
When selecting the appropriate PCB thickness for your project, several factors need to be considered. These factors include:
-
Application Requirements: The specific requirements of your application will heavily influence the choice of PCB thickness. Factors such as the operating environment, mechanical stress, and thermal management needs should be taken into account.
-
Component Placement: The size and type of components used in your design will impact the PCB thickness selection. Larger components, such as connectors or heat sinks, may require a thicker PCB for proper mounting and support.
-
Layer Count: The number of layers in your PCB design will affect the thickness. As the layer count increases, the overall thickness of the PCB will also increase. It’s important to choose a thickness that accommodates the required number of layers while maintaining manufacturability and cost-effectiveness.
-
Manufacturing Capabilities: The manufacturing capabilities of your chosen PCB fabricator will play a role in determining the available thickness options. Some manufacturers may have limitations on the minimum or maximum thickness they can produce. It’s crucial to discuss your thickness requirements with your fabricator to ensure feasibility.
-
Cost Considerations: PCB thickness can impact the overall cost of manufacturing. Thinner PCBs may require specialized processing and materials, which can increase production costs. On the other hand, thicker PCBs may require more material and longer drilling times, also affecting the cost. Finding the right balance between thickness and cost is essential for a successful project.
PCB Thickness and Layer Count
The relationship between PCB thickness and layer count is an important consideration in PCB design. As mentioned earlier, the number of layers in a PCB directly affects its thickness. Here’s a general guide to the correlation between PCB thickness and layer count:
PCB Thickness | Typical Layer Count |
---|---|
0.4 mm | 1-2 layers |
0.6 mm | 2-4 layers |
0.8 mm | 4-6 layers |
1.0 mm | 6-8 layers |
1.2 mm | 8-10 layers |
1.6 mm | 10+ layers |
2.0 mm+ | 12+ layers |
It’s worth noting that these are general guidelines, and the actual layer count may vary depending on the specific design requirements and manufacturing capabilities. It’s always best to consult with your PCB fabricator to determine the optimal thickness and layer count for your project.
PCB Thickness and Manufacturing Considerations
PCB thickness not only affects the electrical and mechanical properties of the board but also has implications for the manufacturing process. Different PCB thicknesses require different manufacturing techniques and considerations. Let’s explore some of the manufacturing aspects related to PCB thickness:
-
Drilling: PCB thickness directly impacts the drilling process. Thicker PCBs require longer drill bits and may necessitate slower drilling speeds to ensure accuracy and prevent drill breakage. The aspect ratio, which is the ratio of the hole depth to the hole diameter, becomes more challenging with increasing thickness.
-
Plating: The plating process, which involves depositing a layer of copper onto the drilled holes to create electrical connections between layers, is affected by PCB thickness. Thicker PCBs require a longer plating time to ensure even coverage and adequate copper thickness in the holes. Uneven plating can lead to reliability issues and poor electrical performance.
-
Lamination: The lamination process, where the individual layers of the PCB are pressed together under high temperature and pressure, is influenced by PCB thickness. Thicker PCBs may require longer lamination cycles and higher pressure to ensure proper bonding between layers. Inadequate lamination can result in delamination, which compromises the integrity of the PCB.
-
Etching: The etching process, which removes unwanted copper from the PCB to create the desired circuit patterns, is also affected by thickness. Thicker PCBs may require longer etching times and more precise control to achieve consistent results. Over-etching or under-etching can lead to manufacturing defects and impact the functionality of the PCB.
-
Soldermask and Silkscreen: The application of soldermask and silkscreen layers onto the PCB is influenced by thickness. Thicker PCBs may require multiple coating passes or specialized equipment to ensure even coverage and adherence. Uneven or incomplete coating can affect the aesthetic appearance and protection of the PCB.
Understanding these manufacturing considerations is crucial when selecting the appropriate PCB thickness for your project. Close collaboration with your PCB fabricator can help address any manufacturing challenges and ensure the successful production of your PCBs.
Frequently Asked Questions (FAQ)
-
What is the most common PCB thickness?
The most common PCB thickness is 1.6 mm (63 mils). This thickness offers a good balance between mechanical strength, layer count support, and manufacturability. It is widely used across various industries and applications. -
Can I use a thinner PCB to reduce the overall size of my device?
Yes, using a thinner PCB can help reduce the overall size of your device. However, it’s important to consider the trade-offs involved. Thinner PCBs may have limitations in terms of layer count, component mounting, and mechanical durability. It’s essential to evaluate your specific design requirements and consult with your PCB fabricator to determine the feasibility of using a thinner PCB. -
How does PCB thickness affect signal integrity?
PCB thickness can have an impact on signal integrity. Thinner PCBs may be more susceptible to signal integrity issues, such as crosstalk and impedance mismatches, due to the closer proximity of traces and reduced dielectric thickness. Thicker PCBs provide more space for proper trace routing and can help mitigate signal integrity problems. However, the actual impact on signal integrity depends on various factors, including the circuit design, material properties, and operating frequency. -
Are there any limitations on the maximum thickness of a PCB?
While there is no strict upper limit on PCB thickness, practical considerations and manufacturing capabilities come into play. PCBs thicker than 2.0 mm (79 mils) are less common and may require specialized manufacturing processes. Extremely thick PCBs can pose challenges in terms of drilling, plating, and lamination. It’s important to discuss your specific requirements with your PCB fabricator to determine the feasibility and any potential limitations. -
How does PCB thickness affect the cost of manufacturing?
PCB thickness can have an impact on manufacturing costs. Thinner PCBs may require specialized materials and processes, which can increase production costs. On the other hand, thicker PCBs consume more material and may require longer processing times, also affecting the overall cost. The most cost-effective thickness option often depends on the specific design requirements, volume, and manufacturing capabilities of your chosen fabricator. It’s recommended to discuss cost implications with your fabricator during the design phase to make informed decisions.
Conclusion
Selecting the appropriate PCB thickness is a critical aspect of PCB design. It influences the mechanical, electrical, and thermal properties of the board, as well as its manufacturability and cost. Understanding the standard PCB thickness options and their suitability for different applications is essential for making informed decisions.
When determining the right PCB thickness for your project, consider factors such as application requirements, component placement, layer count, manufacturing capabilities, and cost. Collaborating closely with your PCB fabricator can help address any challenges and ensure the successful realization of your design.
By following the guidelines and best practices outlined in this article, you can navigate the world of standard PCB thickness with confidence. Remember, the right PCB thickness can make a significant difference in the performance, reliability, and overall success of your electronic devices.
Leave a Reply