What is Soldering Flux?
Soldering flux is a chemical compound that is applied to the metal surfaces before soldering. Its primary purpose is to remove oxidation, prevent further oxidation during the soldering process, and promote the flow of solder for a strong and reliable joint. Flux also helps to lower the surface tension of the molten solder, allowing it to spread evenly and adhere to the metal surfaces.
The Importance of Soldering Flux
Without soldering flux, achieving a strong and reliable solder joint would be extremely difficult, if not impossible. Here are some key reasons why soldering flux is crucial:
-
Removes oxidation: Metals, when exposed to air, form an oxide layer on their surface. This layer prevents the solder from properly bonding with the metal. Flux removes this oxide layer, allowing the solder to adhere to the clean metal surface.
-
Prevents further oxidation: During the soldering process, the high temperature can cause the metal surfaces to oxidize rapidly. Flux creates a protective barrier, preventing oxygen from reaching the metal surfaces and causing oxidation.
-
Promotes solder flow: Flux lowers the surface tension of the molten solder, enabling it to flow smoothly and evenly over the metal surfaces. This helps in creating a strong and uniform solder joint.
-
Improves wetting: Wetting refers to the ability of the molten solder to spread and adhere to the metal surfaces. Flux enhances the wetting properties of the solder, ensuring a better bond between the solder and the metal.
Types of Soldering Flux
There are several types of soldering flux available, each with its unique properties and applications. Let’s explore the most common types:
1. Rosin Flux
Rosin flux is the most widely used type of flux in electronics soldering. It is derived from pine tree sap and is available in various grades and activities. Rosin flux is categorized into three main types:
a. Rosin Core Solder: This type of solder wire has a core filled with rosin flux. As the solder melts, the flux is released, cleaning and protecting the metal surfaces. Rosin core solder is convenient and widely used in electronics soldering.
b. Rosin Paste Flux: Rosin paste flux is a thick, paste-like substance that is applied directly to the metal surfaces before soldering. It provides better flux coverage and is often used for larger components or surface-mount devices.
c. Liquid Rosin Flux: Liquid rosin flux is a solution of rosin dissolved in a solvent, such as isopropyl alcohol. It is applied using a brush or a dispenser and is ideal for hard-to-reach areas or for pre-tinning wires.
2. Water-Soluble Flux
Water-soluble flux, also known as organic acid flux, is a type of flux that can be easily cleaned using water after soldering. It is more aggressive than rosin flux and is suitable for soldering on oxidized or hard-to-clean surfaces. However, water-soluble flux must be thoroughly cleaned after soldering to prevent corrosion.
3. No-Clean Flux
No-clean flux is designed to leave minimal residue after soldering, eliminating the need for post-soldering cleaning. This type of flux is ideal for applications where cleaning is difficult or impractical. No-clean flux is available in various forms, such as rosin-based, synthetic, or halide-free formulations.
4. Inorganic Acid Flux
Inorganic acid flux, such as zinc chloride or ammonium chloride, is a highly active flux used for soldering on heavily oxidized or contaminated surfaces. This type of flux is corrosive and must be thoroughly cleaned after soldering to prevent damage to the components and the PCB.
Selecting the Right Soldering Flux
Choosing the appropriate soldering flux depends on several factors, including the type of metal being soldered, the level of oxidation, the soldering temperature, and the cleaning requirements. Here are some general guidelines for selecting the right soldering flux:
Soldering Application | Recommended Flux Type |
---|---|
Electronics soldering | Rosin flux (rosin core, paste, or liquid) |
Plumbing and sheet metal work | Water-soluble flux or inorganic acid flux |
High-temperature soldering | Inorganic acid flux or specialized high-temperature flux |
Soldering on heavily oxidized surfaces | Inorganic acid flux or water-soluble flux |
Applications requiring minimal residue | No-clean flux |
It’s essential to consider the cleaning requirements and the compatibility of the flux with the components and the PCB material. Always refer to the manufacturer’s recommendations and safety guidelines when selecting and using soldering flux.
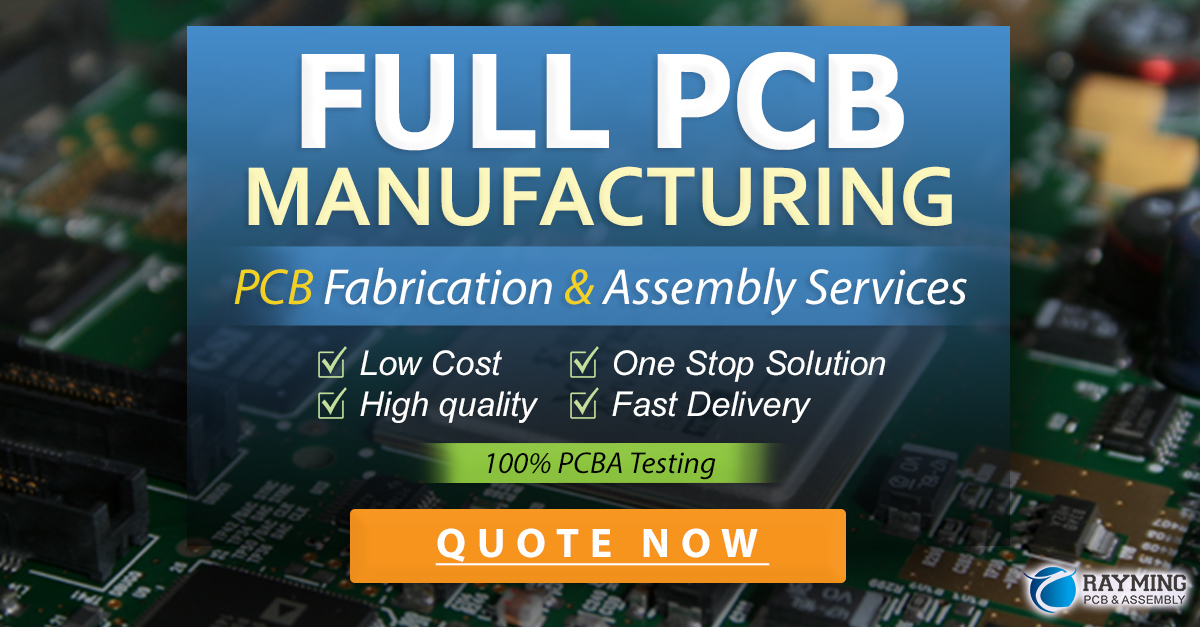
Best Practices for Using Soldering Flux
To achieve the best results when using soldering flux, follow these best practices:
-
Clean the surfaces: Before applying flux, ensure that the metal surfaces are clean and free from dirt, grease, or old solder residue. Use a solvent or abrasive material to clean the surfaces thoroughly.
-
Apply the right amount of flux: Apply a thin, even layer of flux to the metal surfaces. Avoid using too much flux, as it can lead to splattering or create a mess. Too little flux may not provide adequate protection and cleaning.
-
Use the correct soldering temperature: Ensure that the soldering iron is set to the appropriate temperature for the type of solder and flux being used. Excessive heat can cause the flux to burn off too quickly, while insufficient heat may not activate the flux properly.
-
Work quickly and efficiently: Once the flux is applied, and the soldering iron is heated, work quickly to complete the soldering process. Prolonged exposure to heat can cause the flux to degrade and lose its effectiveness.
-
Clean the solder joint: After soldering, clean the solder joint using an appropriate solvent or cleaning method, depending on the type of flux used. Proper cleaning prevents corrosion and ensures the long-term reliability of the solder joint.
Frequently Asked Questions (FAQ)
-
Q: Can I use any type of flux for electronics soldering?
A: While you can use various types of flux for electronics soldering, rosin flux is the most recommended and widely used type. It provides good cleaning and protection without being too corrosive. -
Q: How do I remove flux residue after soldering?
A: The cleaning method depends on the type of flux used. For rosin flux, use isopropyl alcohol or a commercial flux remover. Water-soluble flux can be cleaned using warm water and a mild detergent. Inorganic acid flux requires a more aggressive cleaning process using a designated flux cleaner. -
Q: Can I reuse solder that has flux in it?
A: Yes, solder with flux can be reused as long as it is not contaminated or oxidized. However, keep in mind that the flux may lose its effectiveness over time, especially if the solder has been exposed to air for an extended period. -
Q: Is soldering flux toxic?
A: Some types of soldering flux, particularly inorganic acid flux, can be toxic if inhaled or ingested. Always work in a well-ventilated area, avoid skin contact, and wash your hands thoroughly after soldering. Refer to the flux manufacturer’s safety data sheet for specific precautions and handling instructions. -
Q: Can I solder without using flux?
A: While it is possible to solder without flux, achieving a strong and reliable solder joint is much more difficult. Flux is essential for removing oxidation, preventing further oxidation during soldering, and promoting the flow of solder. Soldering without flux may result in weak, brittle, or unreliable solder joints.
Conclusion
Soldering flux is a critical component in the soldering process, ensuring strong, reliable, and long-lasting solder joints. By understanding the types of soldering flux, their properties, and best practices for using them, you can achieve professional-quality soldering results. Always prioritize safety, follow the manufacturer’s guidelines, and select the appropriate flux for your specific soldering application. With the right knowledge and techniques, you’ll be well on your way to mastering the art of soldering.
Leave a Reply