What is Surface Mount Technology (SMT)?
Surface Mount Technology (SMT) is a method of assembling electronic components onto a printed circuit board (PCB) by mounting them directly onto the surface of the board, rather than through holes as in through-hole technology. SMT components are smaller, lighter, and have shorter leads than their through-hole counterparts, allowing for higher component density and more compact designs.
Advantages of SMT over Through-Hole Technology
Feature | SMT | Through-Hole |
---|---|---|
Component Size | Smaller | Larger |
Component Weight | Lighter | Heavier |
PCB Real Estate | Less | More |
Assembly Speed | Faster | Slower |
Solder Joint Reliability | Higher | Lower |
Manufacturing Cost | Lower | Higher |
Components of an SMT Machine
An SMT machine is a complex system that consists of several key components working together to achieve precise and efficient assembly of electronic components onto PCBs. The main components of an SMT machine include:
1. Solder Paste Printer
The solder paste printer is responsible for applying solder paste onto the PCB pads. It uses a stencil with apertures that correspond to the PCB pads, and a squeegee to spread the solder paste evenly across the stencil and onto the pads.
2. Pick and Place Machine
The pick and place machine is the heart of the SMT Assembly process. It uses a system of nozzles and cameras to pick up electronic components from feeders and place them accurately onto the solder paste-coated pads on the PCB.
3. Reflow Oven
After the components are placed onto the PCB, the board is sent through a reflow oven. The reflow oven heats the PCB and components to a specific temperature profile, melting the solder paste and creating a permanent electrical and mechanical connection between the components and the PCB.
4. Inspection Systems
Inspection systems are used at various stages of the SMT assembly process to ensure the quality and accuracy of the assembled PCBs. These systems include:
- Solder Paste Inspection (SPI): Checks the quality and consistency of the solder paste application.
- Automated Optical Inspection (AOI): Inspects the placed components for correct positioning, orientation, and presence.
- X-ray Inspection: Used for inspecting solder joints underneath components that are not visible to the naked eye.
The SMT Assembly Process
The SMT assembly process consists of several steps that must be followed in a specific order to ensure the proper assembly of electronic components onto PCBs.
Step 1: PCB Preparation
Before the SMT assembly process can begin, the PCB must be properly prepared. This includes cleaning the board to remove any contaminants, applying a solder mask to protect the non-solderable areas, and applying a silkscreen to label the components and provide assembly instructions.
Step 2: Solder Paste Application
The solder paste printer applies solder paste onto the PCB pads using a stencil. The stencil is aligned with the PCB, and a squeegee spreads the solder paste evenly across the stencil and onto the pads. The thickness and consistency of the solder paste application are critical for achieving reliable solder joints.
Step 3: Component Placement
The pick and place machine picks up electronic components from feeders and places them accurately onto the solder paste-coated pads on the PCB. The machine uses a system of nozzles and cameras to ensure precise placement of the components. The placement speed and accuracy are crucial for high-volume production and reducing assembly errors.
Step 4: Reflow Soldering
After the components are placed onto the PCB, the board is sent through a reflow oven. The reflow oven heats the PCB and components to a specific temperature profile, typically following a ramp-soak-spike pattern. The heat melts the solder paste, creating a permanent electrical and mechanical connection between the components and the PCB.
Step 5: Inspection and Testing
Inspection systems are used at various stages of the SMT assembly process to ensure the quality and accuracy of the assembled PCBs. Solder Paste Inspection (SPI) checks the quality and consistency of the solder paste application, Automated Optical Inspection (AOI) inspects the placed components for correct positioning and orientation, and X-ray inspection is used for inspecting solder joints underneath components that are not visible to the naked eye. After the assembly process, the PCBs undergo functional testing to ensure proper operation and performance.
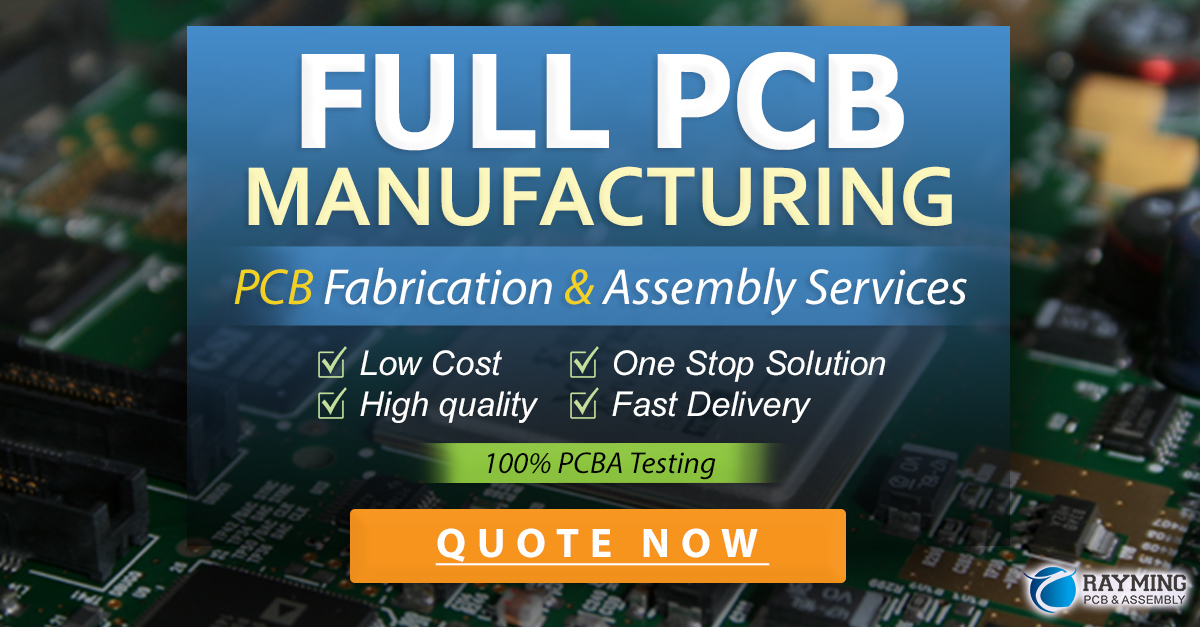
Advantages of SMT Assembly
SMT assembly offers numerous advantages over traditional through-hole technology, making it the preferred method for modern electronics manufacturing.
1. Higher Component Density
SMT components are smaller and have shorter leads than through-hole components, allowing for higher component density on the PCB. This enables the design of more compact and lightweight electronic devices.
2. Faster Assembly Speed
The SMT assembly process is highly automated, with pick and place machines capable of placing thousands of components per hour. This high-speed assembly enables faster production times and reduces labor costs.
3. Improved Solder Joint Reliability
SMT components have a larger surface area in contact with the PCB pads compared to through-hole components, resulting in stronger and more reliable solder joints. This improves the overall reliability and durability of the assembled PCBs.
4. Lower Manufacturing Costs
The high-speed and automated nature of SMT assembly, combined with the smaller size of SMT components, results in lower manufacturing costs compared to through-hole technology. This makes SMT assembly a cost-effective choice for high-volume production.
Challenges in SMT Assembly
Despite the numerous advantages of SMT assembly, there are also some challenges that must be addressed to ensure the success of the assembly process.
1. Miniaturization of Components
As electronic devices continue to shrink in size, the components used in these devices are also becoming smaller. This miniaturization poses challenges for the SMT assembly process, requiring more precise placement and solder paste application.
2. Thermal Management
The high component density in SMT assemblies can lead to increased heat generation, which can affect the performance and reliability of the electronic device. Proper thermal management techniques, such as the use of heat sinks and thermal interface materials, must be employed to ensure the longevity of the assembled PCBs.
3. Counterfeit Components
The proliferation of counterfeit electronic components poses a significant risk to the integrity and reliability of SMT assemblies. Manufacturers must implement strict component sourcing and inspection procedures to ensure the authenticity of the components used in their assemblies.
Frequently Asked Questions (FAQ)
1. What is the difference between SMT and through-hole technology?
SMT (Surface Mount Technology) mounts components directly onto the surface of the PCB, while through-hole technology involves inserting component leads through holes in the PCB and soldering them on the opposite side. SMT components are smaller, lighter, and allow for higher component density compared to through-hole components.
2. What are the main components of an SMT machine?
The main components of an SMT machine include:
– Solder Paste Printer: Applies solder paste onto the PCB pads using a stencil.
– Pick and Place Machine: Picks up electronic components from feeders and places them accurately onto the solder paste-coated pads on the PCB.
– Reflow Oven: Heats the PCB and components to a specific temperature profile, melting the solder paste and creating a permanent electrical and mechanical connection.
– Inspection Systems: Used at various stages of the SMT assembly process to ensure the quality and accuracy of the assembled PCBs.
3. What are the advantages of SMT assembly over through-hole technology?
SMT assembly offers several advantages over through-hole technology, including:
– Higher component density
– Faster assembly speed
– Improved solder joint reliability
– Lower manufacturing costs
4. What are some challenges faced in SMT assembly?
Some challenges faced in SMT assembly include:
– Miniaturization of components, requiring more precise placement and solder paste application.
– Thermal management issues due to high component density.
– Counterfeit components posing risks to the integrity and reliability of the assemblies.
5. What inspection methods are used in the SMT assembly process?
The inspection methods used in the SMT assembly process include:
– Solder Paste Inspection (SPI): Checks the quality and consistency of the solder paste application.
– Automated Optical Inspection (AOI): Inspects the placed components for correct positioning, orientation, and presence.
– X-ray Inspection: Used for inspecting solder joints underneath components that are not visible to the naked eye.
Conclusion
SMT Machines have revolutionized the way electronic components are assembled onto PCBs, offering numerous advantages over traditional through-hole technology. The SMT assembly process, consisting of solder paste application, component placement, reflow soldering, and inspection, enables the production of high-quality, reliable, and cost-effective electronic devices. As electronic components continue to shrink in size and increase in complexity, SMT machines will play an increasingly crucial role in meeting the demands of modern electronics manufacturing.
Leave a Reply