Types of SMT Machines
SMT machines can be categorized into several types based on their functionality and the specific tasks they perform in the SMT assembly process. Here are the main types of SMT machines:
1. Solder Paste Printer
Solder paste printers are used to apply solder paste onto the PCB pads where the electronic components will be placed. These machines use stencils to ensure precise and consistent solder paste deposition. They come in two main types:
- Manual Solder Paste Printers
- Automated Solder Paste Printers
Type | Advantages | Disadvantages |
---|---|---|
Manual Solder Paste Printers | – Lower cost – Suitable for low-volume production |
– Slower process – Less consistent results |
Automated Solder Paste Printers | – High-speed printing – Consistent results – Suitable for high-volume production |
– Higher cost – Requires more maintenance |
2. Pick and Place Machine
Pick and place machines, also known as component placement machines, are responsible for picking up electronic components from feeders and placing them onto the PCB pads with high precision. There are three main types of pick and place machines:
- Chip Shooter Machines
- Flexible Placement Machines
- Multi-Function Placement Machines
Type | Advantages | Disadvantages |
---|---|---|
Chip Shooter Machines | – High-speed placement – Suitable for small components |
– Limited component range – Less flexibility |
Flexible Placement Machines | – Wide component range – High placement accuracy |
– Slower than chip shooters – Higher cost |
Multi-Function Placement Machines | – Combines chip shooter and flexible placement capabilities – Versatile |
– Higher cost – Requires more maintenance |
3. Reflow Oven
Reflow ovens are used to melt the solder paste and create permanent electrical connections between the electronic components and the PCB pads. There are two main types of reflow ovens:
- Convection Reflow Ovens
- Infrared (IR) Reflow Ovens
Type | Advantages | Disadvantages |
---|---|---|
Convection Reflow Ovens | – Even heat distribution – Suitable for most PCBs |
– Slower heating process – Higher energy consumption |
Infrared (IR) Reflow Ovens | – Faster heating process – More energy-efficient |
– Uneven heat distribution – May not be suitable for certain PCBs |
4. Inspection Machines
Inspection machines are used to verify the quality of the assembled PCBs and detect any defects or errors in the SMT process. There are several types of inspection machines:
- Automated Optical Inspection (AOI) Machines
- X-Ray Inspection Machines
- In-Circuit Testing (ICT) Machines
Type | Advantages | Disadvantages |
---|---|---|
Automated Optical Inspection (AOI) Machines | – High-speed inspection – Detects surface-level defects |
– Cannot detect internal defects – May require additional programming |
X-Ray Inspection Machines | – Detects internal defects – Suitable for complex PCBs |
– Higher cost – Slower inspection process |
In-Circuit Testing (ICT) Machines | – Tests functionality of assembled PCBs – Identifies component-level faults |
– Requires custom test fixtures – May not detect all defects |
Features of Excellent SMT Machines
When selecting SMT machines for your manufacturing needs, it is essential to consider the features that make them excellent. Here are some key features to look for in high-quality SMT machines:
1. High Precision
Excellent SMT machines should offer high precision in component placement and solder paste deposition. This ensures that the assembled PCBs are of high quality and reliability. Look for machines with advanced vision systems, closed-loop feedback, and high-resolution cameras for accurate component alignment.
2. High Speed
In order to achieve high throughput and efficiency, excellent SMT machines should have high-speed capabilities. This includes fast component placement rates, quick solder paste printing, and efficient reflow processes. High-speed machines can significantly reduce production time and increase overall productivity.
3. Flexibility
Excellent SMT machines should be flexible enough to accommodate a wide range of PCB sizes, component types, and production volumes. This allows manufacturers to adapt to changing product requirements and customer demands. Look for machines with adjustable conveyor systems, multi-nozzle heads, and quick changeover capabilities.
4. User-Friendly Interface
An user-friendly interface is essential for efficient operation and maintenance of SMT machines. Excellent machines should have intuitive software interfaces that allow operators to easily set up, monitor, and control the production process. Look for machines with touchscreen displays, real-time data monitoring, and remote access capabilities.
5. Reliability and Durability
Excellent SMT machines should be reliable and durable to minimize downtime and ensure consistent performance over time. Look for machines with robust construction, high-quality components, and advanced error detection and recovery systems. Regular maintenance and calibration are also important for ensuring the longevity and reliability of SMT machines.
Frequently Asked Questions (FAQ)
-
Q: What is the difference between SMT and through-hole technology?
A: SMT involves placing components directly onto the surface of the PCB, while through-hole technology requires inserting component leads through holes in the PCB and soldering them on the opposite side. SMT allows for smaller component sizes and higher component density compared to through-hole technology. -
Q: How do I choose the right SMT machine for my manufacturing needs?
A: When choosing an SMT machine, consider factors such as your production volume, PCB complexity, component types, and budget. Evaluate the machine’s precision, speed, flexibility, and user-friendliness to ensure it meets your specific requirements. It’s also advisable to consult with SMT machine manufacturers or experts to help you make an informed decision. -
Q: What is the role of solder paste in the SMT process?
A: Solder paste is a mixture of tiny solder particles and flux that is applied onto the PCB pads before component placement. It serves two main purposes: to temporarily hold the components in place before reflow soldering and to create permanent electrical and mechanical connections between the components and the PCB pads during the reflow process. -
Q: How often should SMT machines be maintained and calibrated?
A: The frequency of maintenance and calibration depends on the specific SMT machine and its usage. Generally, it is recommended to perform regular cleaning, lubrication, and inspection of machine parts to ensure optimal performance. Calibration should be done periodically, typically every few months or as recommended by the machine manufacturer, to maintain high precision and accuracy. -
Q: Can SMT machines be used for both prototyping and mass production?
A: Yes, there are SMT machines suitable for both prototyping and mass production. For prototyping and low-volume production, desktop SMT machines or manual pick and place machines are often used. For high-volume mass production, fully automated SMT assembly lines with high-speed placement machines and conveyorized systems are employed to achieve high throughput and efficiency.
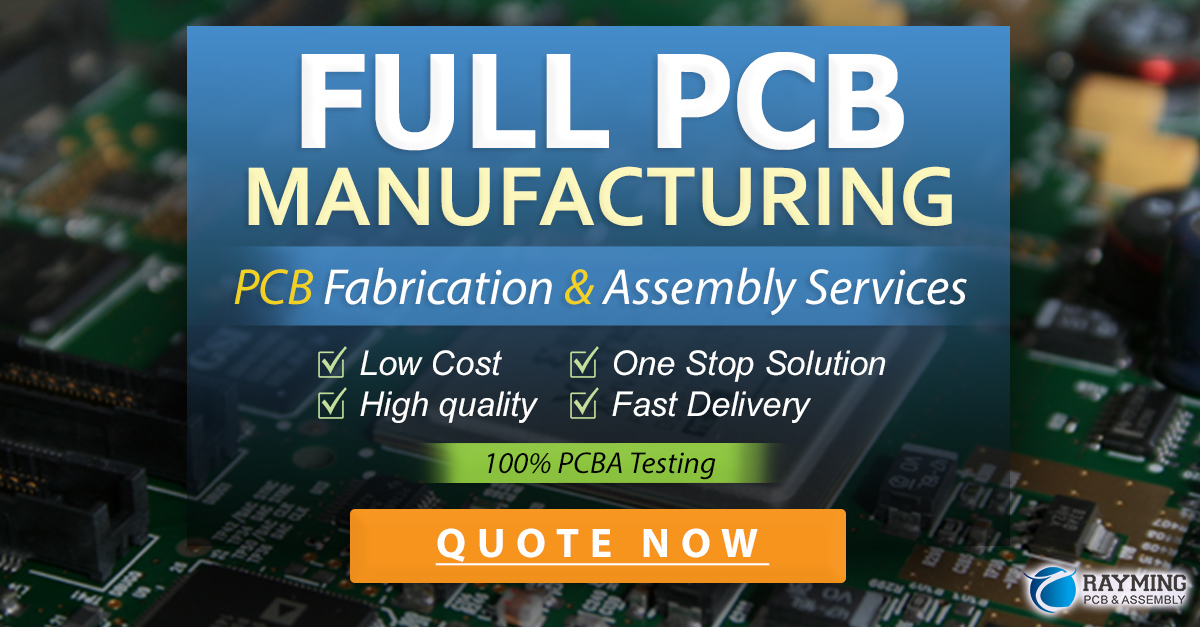
Conclusion
SMT machines have become indispensable tools in the electronics manufacturing industry, enabling the efficient and precise assembly of PCBs. Understanding the different types of SMT machines and their features is crucial for selecting the right equipment for your manufacturing needs. From solder paste printers and pick and place machines to reflow ovens and inspection machines, each type of SMT machine plays a critical role in the SMT assembly process.
When choosing SMT machines, prioritize features such as high precision, high speed, flexibility, user-friendliness, and reliability. These features contribute to the production of high-quality, reliable electronic devices while maximizing efficiency and productivity.
As technology continues to advance, SMT machines are expected to evolve and offer even more sophisticated capabilities in the future. By staying informed about the latest developments in SMT equipment and processes, manufacturers can stay competitive and meet the ever-increasing demands of the electronics industry.
Leave a Reply