Understanding Signal Integrity
Signal integrity refers to the ability of an electrical signal to maintain its intended characteristics as it travels through a system. In PCB design, signal integrity is concerned with preserving the quality and timing of signals as they propagate through the interconnects, vias, and components on the board. Poor signal integrity can lead to issues such as signal distortion, crosstalk, reflections, and electromagnetic interference (EMI), which can compromise the performance and reliability of the system.
Factors Affecting Signal Integrity
Several factors can impact signal integrity in PCB design:
-
Impedance mismatch: Impedance mismatch occurs when there is a difference in the characteristic impedance between the signal source, interconnects, and the load. This mismatch can cause reflections and signal distortion.
-
Crosstalk: Crosstalk is the unwanted coupling of signals between adjacent traces or components. It can lead to signal interference and noise.
-
Electromagnetic interference (EMI): EMI is the unintentional generation of electromagnetic energy that can interfere with the proper functioning of electronic devices. It can be caused by factors such as high-speed switching, improper grounding, and poor shielding.
-
Timing issues: Timing problems can arise when signals arrive at their destination at different times due to variations in trace lengths or delays caused by components. This can lead to synchronization issues and data corruption.
Designing for Signal Integrity
To ensure signal integrity in PCB design, several techniques and best practices should be employed:
Impedance Control
Impedance control is the process of matching the characteristic impedance of the interconnects to the impedance of the source and load. This minimizes reflections and ensures proper signal propagation. There are two main types of impedance control:
-
Controlled impedance: Controlled impedance involves designing the PCB stackup and trace geometries to achieve a specific characteristic impedance. This is typically done by adjusting the trace width, spacing, and dielectric thickness.
-
Differential signaling: Differential signaling uses a pair of complementary signals to transmit data. The signals are equal in magnitude but opposite in polarity, which helps to cancel out common-mode noise and reduce EMI.
Routing Techniques
Proper routing techniques can help minimize crosstalk, reduce signal reflections, and improve signal integrity:
-
Trace spacing: Adequate spacing between traces should be maintained to minimize crosstalk. The spacing depends on factors such as the signal speed, dielectric constant, and trace geometry.
-
Trace length matching: Traces carrying related signals should be matched in length to ensure that the signals arrive at their destination at the same time. This is particularly important for high-speed differential pairs.
-
Via optimization: Vias should be minimized and placed strategically to reduce signal reflections and discontinuities. Via stubs should be avoided or minimized to prevent unwanted resonances.
Grounding and Shielding
Proper grounding and shielding techniques are essential for maintaining signal integrity and reducing EMI:
-
Ground planes: Solid ground planes should be used to provide a low-impedance return path for signals and minimize ground bounce. Split ground planes should be avoided unless necessary for isolation purposes.
-
Shielding: Sensitive signals or components can be shielded using techniques such as ground shields, Faraday cages, or shielded cables to reduce EMI and crosstalk.
-
Decoupling capacitors: Decoupling capacitors should be placed close to the power pins of ICs to provide a local source of charge and minimize power supply noise.
Simulation and Analysis
Simulation and analysis tools can help identify and resolve signal integrity issues early in the design process:
-
Signal integrity simulation: Signal integrity simulation tools can be used to analyze the behavior of signals in the time and frequency domains. They can help identify issues such as reflections, crosstalk, and timing violations.
-
Electromagnetic simulation: Electromagnetic simulation tools can be used to analyze the electromagnetic fields generated by the PCB and identify potential EMI issues.
-
Design rule checking (DRC): DRC tools can be used to verify that the PCB design adheres to the specified design rules and constraints, helping to catch potential signal integrity issues before fabrication.
Best Practices for Signal Integrity
In addition to the specific techniques mentioned above, there are several general best practices that can help ensure signal integrity in PCB design:
-
Keep signal traces as short as possible: Shorter traces minimize the opportunity for signal degradation and reduce the impact of impedance mismatches.
-
Avoid sharp bends in traces: Sharp bends can cause reflections and impedance discontinuities. Use smooth, gradual bends instead.
-
Terminate signals properly: Use appropriate termination techniques, such as series termination or parallel termination, to match the impedance of the source and load and minimize reflections.
-
Use appropriate dielectric materials: Choose dielectric materials with suitable properties, such as low loss tangent and stable dielectric constant, to minimize signal attenuation and maintain consistent impedance.
-
Follow manufacturer guidelines: Adhere to the guidelines provided by component manufacturers regarding pin assignments, layout recommendations, and power supply requirements to ensure optimal signal integrity.
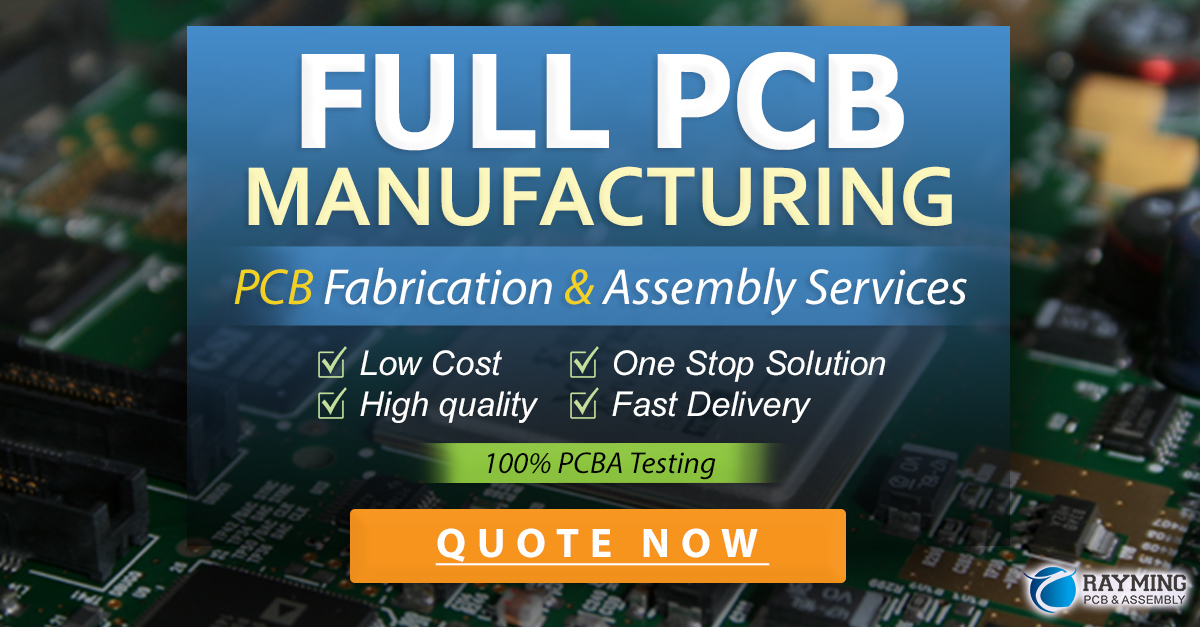
Example: Designing a High-Speed DDR Memory Interface
To illustrate the application of signal integrity techniques, let’s consider the design of a high-speed DDR (Double Data Rate) memory interface on a PCB.
DDR Memory Interface Requirements
Parameter | Value |
---|---|
Data rate | 3200 MT/s |
Bus width | 64 bits |
Supply voltage | 1.2V |
Characteristic impedance | 50Ω |
Signal Integrity Considerations
-
Impedance matching: The characteristic impedance of the DDR data lines should be matched to 50Ω to minimize reflections. This can be achieved by adjusting the trace width and spacing based on the PCB stackup and dielectric properties.
-
Length matching: The data lines and strobe signals should be length-matched to ensure that the signals arrive at the receiver within the specified timing window. Length matching can be achieved by serpentine routing or using delay lines.
-
Decoupling capacitors: Adequate decoupling capacitors should be placed close to the DDR memory device to provide a stable power supply and minimize power supply noise.
-
Termination: On-die termination (ODT) should be used on the DDR memory device to match the impedance of the data lines and minimize reflections.
Simulation and Verification
Signal integrity simulation should be performed to analyze the behavior of the DDR memory interface and identify any potential issues. This can include:
-
Time-domain simulation: Analyzing the eye diagram and verifying that the signal levels and timing meet the DDR specification.
-
Frequency-domain simulation: Analyzing the insertion loss and return loss of the data lines to ensure they meet the specified requirements.
-
Crosstalk analysis: Verifying that the crosstalk between adjacent data lines is within acceptable limits.
By applying these signal integrity techniques and verifying the design through simulation, the DDR memory interface can be designed to achieve reliable high-speed performance.
Frequently Asked Questions (FAQ)
-
What is signal integrity, and why is it important in PCB design?
Signal integrity refers to the ability of an electrical signal to maintain its intended characteristics as it propagates through a system. In PCB design, signal integrity is crucial because it ensures the proper functioning and reliability of electronic devices by managing the quality and timing of signals as they travel through the interconnects and components on the board. -
What are some common issues that can affect signal integrity in PCB design?
Some common issues that can affect signal integrity in PCB design include impedance mismatch, crosstalk, electromagnetic interference (EMI), and timing issues. Impedance mismatch occurs when there is a difference in the characteristic impedance between the signal source, interconnects, and the load, leading to reflections and signal distortion. Crosstalk is the unwanted coupling of signals between adjacent traces or components, causing signal interference and noise. EMI is the unintentional generation of electromagnetic energy that can interfere with the proper functioning of electronic devices. Timing issues arise when signals arrive at their destination at different times due to variations in trace lengths or delays caused by components. -
What are some techniques used to control impedance in PCB design?
Two main techniques used to control impedance in PCB design are controlled impedance and differential signaling. Controlled impedance involves designing the PCB stackup and trace geometries to achieve a specific characteristic impedance by adjusting the trace width, spacing, and dielectric thickness. Differential signaling uses a pair of complementary signals to transmit data, with the signals being equal in magnitude but opposite in polarity, which helps to cancel out common-mode noise and reduce EMI. -
How can simulation and analysis tools help in ensuring signal integrity in PCB design?
Simulation and analysis tools can help identify and resolve signal integrity issues early in the design process. Signal integrity simulation tools can analyze the behavior of signals in the time and frequency domains, helping to identify issues such as reflections, crosstalk, and timing violations. Electromagnetic simulation tools can analyze the electromagnetic fields generated by the PCB and identify potential EMI issues. Design rule checking (DRC) tools can verify that the PCB design adheres to the specified design rules and constraints, helping to catch potential signal integrity issues before fabrication. -
What are some best practices for maintaining signal integrity in high-speed PCB designs?
Some best practices for maintaining signal integrity in high-speed PCB designs include keeping signal traces as short as possible to minimize signal degradation, avoiding sharp bends in traces to prevent reflections and impedance discontinuities, using appropriate termination techniques to match the impedance of the source and load, choosing suitable dielectric materials with low loss tangent and stable dielectric constant, and following manufacturer guidelines regarding pin assignments, layout recommendations, and power supply requirements. Additionally, employing proper grounding and shielding techniques, such as using solid ground planes and shielding sensitive signals or components, can help reduce EMI and maintain signal integrity.
Conclusion
Signal integrity is a critical aspect of PCB design that directly impacts the performance and reliability of electronic systems. As the demand for high-speed and high-density PCBs continues to grow, designers must employ various techniques and best practices to ensure signal integrity. These include impedance control, proper routing, grounding and shielding, and the use of simulation and analysis tools.
By understanding the factors that affect signal integrity and applying the appropriate design techniques, PCB designers can minimize signal distortion, crosstalk, EMI, and timing issues. This leads to more robust and reliable electronic devices that meet the ever-increasing demands of modern applications.
As technology advances and signal speeds continue to rise, the importance of signal integrity in PCB design will only continue to grow. Designers must stay up-to-date with the latest techniques and tools to effectively tackle the challenges of maintaining signal integrity in complex, high-speed systems.
Leave a Reply