What is Selective Soldering?
Selective soldering is a process that involves applying solder to specific areas of a PCB, typically where through-hole components are located. This method is more precise and targeted compared to Wave Soldering, as it allows for the selective application of solder to individual components or groups of components. Selective soldering is performed using a machine that dispenses solder onto the desired locations of the PCB, ensuring that only the intended areas are soldered.
Advantages of Selective Soldering
-
Precision: Selective soldering offers high precision, as it targets specific areas of the PCB. This is particularly useful when dealing with complex PCB Designs that have densely populated components or when certain components require special attention.
-
Reduced thermal stress: Since selective soldering focuses on specific areas, the overall thermal stress on the PCB and its components is reduced compared to wave soldering. This is advantageous for temperature-sensitive components or PCBs with delicate structures.
-
Flexibility: Selective soldering allows for greater flexibility in terms of the types of components that can be soldered. It can handle a wide range of component sizes and shapes, including those with unusual pin configurations or those that are difficult to solder using other methods.
-
Reduced masking requirements: With selective soldering, the need for masking or pallets to protect certain areas of the PCB is reduced. This can lead to cost savings and simplified PCB design.
Disadvantages of Selective Soldering
-
Slower process: Selective soldering is generally slower compared to wave soldering, as it requires precise positioning and soldering of individual components or groups of components. This can impact the overall production throughput.
-
Higher equipment cost: Selective soldering machines are typically more expensive than wave Soldering Equipment due to their precision and customization capabilities.
-
Programming complexity: Setting up and programming a selective soldering machine can be more complex and time-consuming compared to wave soldering. It requires careful planning and programming to ensure accurate soldering of specific areas.
What is Wave Soldering?
Wave soldering is a process in which a PCB is passed over a wave of molten solder. The solder wave comes into contact with the bottom of the PCB, where the through-hole component leads are located. As the PCB moves over the wave, the molten solder adheres to the component leads and the corresponding pads on the PCB, creating a solid electrical and mechanical connection.
Advantages of Wave Soldering
-
High throughput: Wave soldering is a fast and efficient process, capable of soldering a large number of PCBs in a short amount of time. This makes it suitable for high-volume production runs.
-
Cost-effective: Wave soldering is generally more cost-effective compared to selective soldering, especially for large production volumes. The equipment and setup costs are lower, and the process is faster, resulting in reduced labor costs.
-
Consistency: Wave soldering provides consistent results across a large number of PCBs. Once the process parameters are optimized, the soldering quality remains uniform throughout the production run.
Disadvantages of Wave Soldering
-
Limited precision: Wave soldering lacks the precision of selective soldering. The entire bottom surface of the PCB is exposed to the solder wave, which can lead to unwanted solder bridges or short circuits if the PCB design is not optimized for wave soldering.
-
Thermal stress: The PCB and its components undergo higher thermal stress during wave soldering compared to selective soldering. This can be a concern for temperature-sensitive components or PCBs with delicate structures.
-
Masking requirements: Wave soldering often requires the use of masks or pallets to protect certain areas of the PCB from the solder wave. This adds complexity to the PCB design and increases the overall production cost.
-
Limited flexibility: Wave soldering may not be suitable for all types of components or PCB designs. Components with unusual pin configurations or those that are sensitive to high temperatures may not be compatible with wave soldering.
Factors to Consider When Choosing Between Selective Soldering and Wave Soldering
When deciding between selective soldering and wave soldering for your through-hole PCB Assembly process, consider the following factors:
-
PCB complexity: If your PCB design is complex, with densely populated components or intricate layouts, selective soldering may be the better choice due to its precision and flexibility.
-
Production volume: For high-volume production runs, wave soldering is generally more cost-effective and efficient. However, if you have low to medium production volumes or require frequent changeovers, selective soldering may be more suitable.
-
Component compatibility: Consider the types of components used on your PCB. If you have temperature-sensitive components or those with unusual pin configurations, selective soldering may be the preferred option.
-
Available resources: Take into account the available equipment, skilled personnel, and budget. Selective soldering machines are generally more expensive and require specialized programming, while wave soldering equipment is more widely available and easier to set up.
-
Quality requirements: Evaluate your quality requirements and the level of precision needed for your PCB assembly. Selective soldering offers higher precision and reduced thermal stress, which may be necessary for certain applications.
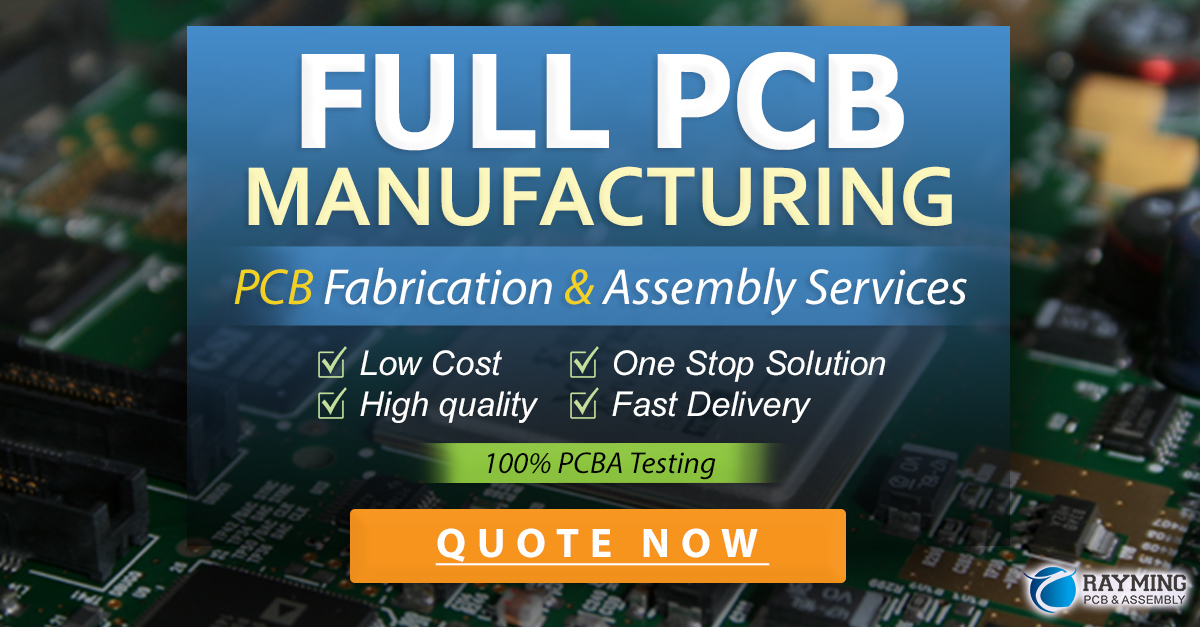
Comparison Table: Selective Soldering vs Wave Soldering
Factor | Selective Soldering | Wave Soldering |
---|---|---|
Precision | High | Low |
Thermal Stress | Low | High |
Flexibility | High | Low |
Masking Requirements | Low | High |
Process Speed | Slow | Fast |
Equipment Cost | High | Low |
Programming Complexity | High | Low |
Production Volume | Low to Medium | High |
FAQ
-
Q: Can selective soldering and wave soldering be used together on the same PCB?
A: Yes, it is possible to use both selective soldering and wave soldering on the same PCB. This is known as a hybrid approach, where certain components are selectively soldered while others are wave soldered. This can be advantageous when dealing with PCBs that have a mix of through-hole and surface-mount components. -
Q: Is selective soldering suitable for high-volume production?
A: While selective soldering is generally slower compared to wave soldering, it can still be used for high-volume production. Modern selective soldering machines are capable of handling larger volumes and offer improved speed and efficiency. However, for very high-volume production runs, wave soldering may still be the more cost-effective option. -
Q: Can wave soldering be used for double-sided PCBs?
A: Yes, wave soldering can be used for double-sided PCBs. However, it requires careful design considerations and the use of appropriate masking techniques to prevent solder bridges and short circuits on the top side of the PCB. Additionally, the components on the top side must be able to withstand the thermal stress of the wave soldering process. -
Q: Is selective soldering more expensive than wave soldering?
A: In terms of equipment cost and setup, selective soldering is generally more expensive than wave soldering. Selective soldering machines are more complex and require specialized programming, which contributes to the higher cost. However, when considering the overall production cost, including labor and material expenses, the cost difference between the two methods may be less significant, especially for low to medium production volumes. -
Q: What are the common defects associated with selective soldering and wave soldering?
A: Some common defects associated with selective soldering include insufficient solder, solder bridging, and poor wetting. These defects can be caused by improper machine setup, incorrect solder parameters, or contamination of the soldering area. In wave soldering, common defects include solder bridges, solder balls, and poor hole fill. These defects can be caused by incorrect conveyor speed, improper fluxing, or inadequate PCB design for wave soldering.
Conclusion
Selective soldering and wave soldering are two distinct methods for soldering through-hole components on PCBs. Selective soldering offers high precision, reduced thermal stress, and flexibility, making it suitable for complex PCB designs and low to medium production volumes. On the other hand, wave soldering is fast, cost-effective, and consistent, making it ideal for high-volume production runs.
When choosing between selective soldering and wave soldering, consider factors such as PCB complexity, production volume, component compatibility, available resources, and quality requirements. By understanding the advantages and disadvantages of each method and evaluating your specific needs, you can make an informed decision and select the most appropriate soldering technique for your through-hole PCB assembly process.
Leave a Reply