Why is PCB Surface Finish Important?
A PCB surface finish serves several essential functions:
-
Protection: The surface finish acts as a barrier, protecting the exposed copper traces from oxidation, contamination, and corrosion, which can degrade the electrical performance and reliability of the PCB.
-
Solderability: The surface finish enhances the solderability of the PCB, ensuring a strong and reliable connection between the components and the board during the assembly process.
-
Compatibility: The surface finish must be compatible with the components and the assembly process, such as through-hole or surface mount technology (SMT), to ensure proper attachment and functionality.
-
Durability: The surface finish should withstand the environmental conditions and mechanical stresses encountered during the PCB’s lifetime, maintaining its integrity and performance.
Factors to Consider When Selecting a PCB Surface Finish
When choosing a surface finish for your PCB, consider the following factors:
1. Application Requirements
The intended application of your PCB will greatly influence the choice of surface finish. Consider the following aspects:
-
Environmental conditions: Will the PCB be exposed to harsh environments, such as high temperatures, humidity, or corrosive substances? Some surface finishes offer better protection against these conditions than others.
-
Electrical requirements: Different surface finishes have varying electrical properties, such as conductivity and resistance. Select a surface finish that meets your application’s electrical requirements.
-
Mechanical requirements: If your PCB will be subjected to mechanical stresses, such as vibration or impact, choose a surface finish with good mechanical stability and adhesion.
2. Assembly Process
The assembly process used for your PCB will also impact the selection of the surface finish. Consider the following:
-
Soldering method: Different surface finishes are compatible with specific soldering methods, such as wave soldering, reflow soldering, or hand soldering. Ensure that the chosen surface finish is suitable for your assembly process.
-
Component compatibility: Some surface finishes may not be compatible with certain component types or packages. Verify that the selected surface finish is compatible with the components used in your design.
3. Cost and Availability
Cost and availability are practical considerations when selecting a surface finish. Some surface finishes may be more expensive or have longer lead times than others. Consider the following:
-
Budget constraints: Determine the acceptable cost range for your project and select a surface finish that fits within your budget.
-
Availability and lead time: Verify the availability of the desired surface finish with your PCB manufacturer and consider the lead time required for its application.
4. Compliance and Regulations
Depending on your industry and target market, your PCB may need to comply with specific regulations or standards. Consider the following:
-
RoHS compliance: If your PCB needs to be RoHS compliant, ensure that the selected surface finish is free of restricted substances, such as lead.
-
Industry standards: Some industries, such as automotive or aerospace, have specific requirements for PCB surface finishes. Ensure that your chosen surface finish meets these standards.
Common PCB Surface Finish Types
There are several common PCB surface finish types, each with its own advantages and disadvantages. The following table provides an overview of the most popular options:
Surface Finish | Composition | Advantages | Disadvantages |
---|---|---|---|
HASL (Hot Air Solder Leveling) | Tin-lead alloy | – Low cost – Good solderability – Excellent shelf life |
– Not suitable for fine-pitch components – Uneven surface – Contains lead (not RoHS compliant) |
Lead-Free HASL | Tin-copper, tin-silver, or tin-bismuth alloy | – RoHS compliant – Good solderability – Excellent shelf life |
– Higher cost than leaded HASL – Uneven surface – Higher process temperatures |
ENIG (Electroless Nickel Immersion Gold) | Nickel and gold layers | – Flat surface – Excellent solderability – Good shelf life – Suitable for fine-pitch components |
– Higher cost than HASL – Sensitive to thermal shock – Potential for “black pad” defect |
OSP (Organic Solderability Preservative) | Organic compound | – Low cost – Flat surface – Suitable for fine-pitch components – RoHS compliant |
– Limited shelf life – Sensitive to handling and contamination – May require nitrogen reflow |
Immersion Silver | Silver | – Flat surface – Good solderability – RoHS compliant – Lower cost than ENIG |
– Limited shelf life – Sensitive to sulfur contamination – Potential for silver migration |
Immersion Tin | Tin | – Flat surface – Good solderability – RoHS compliant – Lower cost than ENIG |
– Limited shelf life – Prone to tin whiskers – Sensitive to thermal shock |
HASL (Hot Air Solder Leveling)
HASL is one of the most common and cost-effective surface finishes. The PCB is dipped in a molten tin-lead alloy and then exposed to hot air to remove excess solder, creating a thin, solderable layer. HASL provides good solderability and excellent shelf life, making it suitable for a wide range of applications.
However, HASL has some disadvantages. The surface is not entirely flat, which can be problematic for fine-pitch components. Additionally, the tin-lead alloy contains lead, making it non-compliant with RoHS regulations.
Lead-Free HASL
Lead-free HASL is an alternative to traditional HASL that addresses the RoHS compliance issue. Instead of a tin-lead alloy, lead-free HASL uses alloys such as tin-copper, tin-silver, or tin-bismuth. This surface finish offers similar advantages to leaded HASL, including good solderability and excellent shelf life.
However, lead-free HASL comes with some drawbacks. It is more expensive than leaded HASL and requires higher process temperatures, which can stress the PCB. The surface also remains uneven, which may be unsuitable for fine-pitch components.
ENIG (Electroless Nickel Immersion Gold)
ENIG is a popular choice for high-reliability applications. The PCB is plated with a layer of nickel, followed by a thin layer of gold. The nickel layer provides a barrier against copper migration, while the gold layer offers excellent solderability and protection against oxidation.
ENIG has several advantages, including a flat surface finish, excellent solderability, and good shelf life. It is suitable for fine-pitch components and is RoHS compliant.
However, ENIG is more expensive than HASL and is sensitive to thermal shock, which can cause the nickel layer to separate from the copper. There is also a potential for a defect known as “black pad,” where the nickel layer becomes oxidized, leading to poor solderability.
OSP (Organic Solderability Preservative)
OSP is a cost-effective and environmentally friendly surface finish. An organic compound is applied to the PCB, forming a protective layer that prevents oxidation and enhances solderability. OSP provides a flat surface finish and is suitable for fine-pitch components.
However, OSP has a limited shelf life compared to other surface finishes and is sensitive to handling and contamination. It may also require nitrogen reflow to achieve optimal soldering results.
Immersion Silver
Immersion silver is a simple and cost-effective surface finish that involves plating a thin layer of silver onto the copper traces. It offers a flat surface, good solderability, and is RoHS compliant. Immersion silver is less expensive than ENIG and provides a suitable alternative for many applications.
However, immersion silver has a limited shelf life and is sensitive to sulfur contamination, which can cause tarnishing and impact solderability. There is also a potential for silver migration, which can lead to electrical shorts.
Immersion Tin
Immersion tin is another cost-effective surface finish that involves plating a thin layer of tin onto the copper traces. It provides a flat surface, good solderability, and is RoHS compliant. Immersion tin is less expensive than ENIG and offers a viable option for many applications.
However, immersion tin has a limited shelf life and is prone to the formation of tin whiskers, which can cause electrical shorts. It is also sensitive to thermal shock, which can cause the tin layer to crack or delaminate.
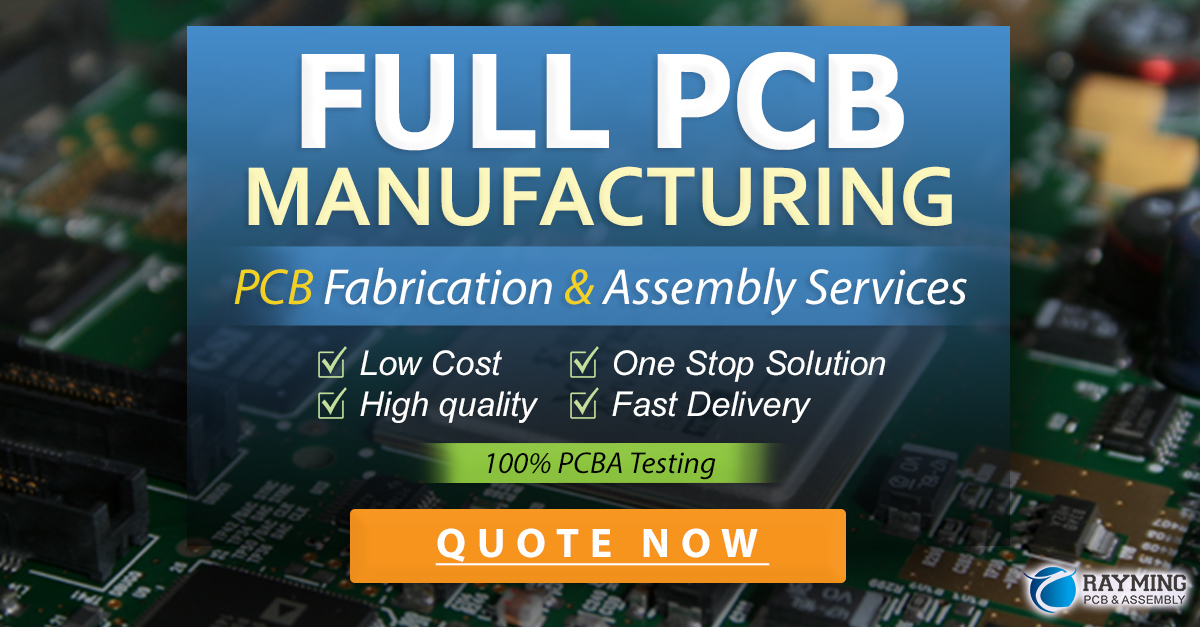
FAQ
-
Q: Which surface finish is the most cost-effective?
A: HASL and OSP are generally the most cost-effective surface finishes. However, the overall cost will depend on factors such as the PCB design, quantity, and manufacturing process. -
Q: Which surface finish is best for high-reliability applications?
A: ENIG is often the preferred choice for high-reliability applications due to its excellent solderability, flat surface, and good shelf life. However, immersion silver and immersion tin can also be suitable for certain high-reliability applications. -
Q: Can I use HASL for fine-pitch components?
A: HASL is not recommended for fine-pitch components due to its uneven surface. ENIG, OSP, immersion silver, and immersion tin are better suited for fine-pitch applications. -
Q: How long does the OSP surface finish last?
A: OSP has a limited shelf life compared to other surface finishes. The exact shelf life depends on factors such as the specific OSP formulation and storage conditions but is typically around 6-12 months. -
Q: Is it possible to switch from one surface finish to another during production?
A: Switching surface finishes during production is possible but may require adjustments to the manufacturing process and additional testing to ensure compatibility and reliability. It is best to consult with your PCB manufacturer when considering a change in surface finish.
Conclusion
Selecting the right surface finish for your PCB is a critical decision that impacts the performance, reliability, and cost of your final product. By considering factors such as application requirements, assembly process, cost, and compliance, you can make an informed choice that meets your specific needs.
HASL, lead-free HASL, ENIG, OSP, immersion silver, and immersion tin are among the most common surface finishes, each with its own strengths and weaknesses. Understanding the characteristics of each surface finish and their suitability for your application will help you select the best option for your PCB.
When in doubt, consult with your PCB manufacturer to discuss your requirements and get their expert advice on the most suitable surface finish for your project. By making the right choice, you can ensure that your PCB performs optimally and reliably throughout its intended lifecycle.
Leave a Reply