Introduction to Round PCBs
Round printed circuit boards (PCBs) are a unique and specialized type of PCB that offers several advantages over traditional rectangular designs. Unlike standard rectangular PCBs, round PCBs have a circular shape, which can provide benefits such as improved signal integrity, reduced electromagnetic interference (EMI), and enhanced mechanical stability. This comprehensive guide will explore the various aspects of round PCBs, including their applications, design considerations, manufacturing processes, and more.
Applications of Round PCBs
Round PCBs find applications in a wide range of industries and devices. Some common applications include:
Automotive Industry
In the automotive industry, round PCBs are used in various systems such as:
– Instrument clusters
– Steering wheel controls
– Airbag systems
– Tire pressure monitoring systems (TPMS)
The circular shape of round PCBs allows for easy integration into the limited space available in automotive components, while also providing enhanced durability against vibrations and shocks.
Aerospace and Defense
Round PCBs are well-suited for aerospace and defense applications due to their ability to withstand harsh environmental conditions and high-stress situations. Some examples include:
– Avionics systems
– Radar systems
– Satellite communication devices
– Military-grade equipment
The circular shape of round PCBs helps in minimizing the effects of vibrations and mechanical stresses, ensuring reliable performance in critical applications.
Medical Devices
In the medical industry, round PCBs are used in various devices such as:
– Wearable health monitors
– Implantable devices
– Surgical instruments
– Diagnostic equipment
The compact and space-efficient design of round PCBs makes them ideal for miniaturized medical devices, while their enhanced signal integrity ensures accurate and reliable data transmission.
Consumer Electronics
Round PCBs are also used in a variety of consumer electronics, including:
– Smartwatches
– Wireless earbuds
– Virtual reality (VR) and augmented reality (AR) devices
– Gaming controllers
The circular shape of round PCBs allows for sleek and ergonomic designs, while also providing improved signal quality and reduced EMI.
Advantages of Round PCBs
Round PCBs offer several advantages over traditional rectangular designs, making them an attractive choice for various applications. Some of the key benefits include:
Improved Signal Integrity
The circular shape of round PCBs helps in reducing the signal path length, which leads to improved signal integrity. Shorter signal paths result in reduced signal distortion, crosstalk, and signal reflections, ensuring cleaner and more reliable signal transmission.
Reduced Electromagnetic Interference (EMI)
Round PCBs have a more uniform distribution of copper traces compared to rectangular designs, which helps in minimizing EMI. The circular shape also eliminates sharp corners and edges that can act as sources of EMI, further reducing the overall electromagnetic emissions from the PCB.
Enhanced Mechanical Stability
The circular shape of round PCBs provides enhanced mechanical stability compared to rectangular designs. Round PCBs are less susceptible to warping, twisting, and bending, making them more durable and resistant to mechanical stresses. This enhanced stability is particularly beneficial in applications that are subject to vibrations, shocks, or extreme temperature variations.
Space Efficiency
Round PCBs offer a more space-efficient design compared to rectangular PCBs. The circular shape allows for better utilization of available space, making it possible to accommodate more components and features within a smaller footprint. This space efficiency is particularly advantageous in applications where size and weight are critical factors, such as wearable devices and portable electronics.
Aesthetic Appeal
Round PCBs can add a unique and visually appealing element to product designs. The circular shape can be leveraged to create aesthetically pleasing and distinctive devices, setting them apart from traditional rectangular designs. This aesthetic appeal can be particularly valuable in consumer electronics and high-end products where visual appearance is a key differentiating factor.
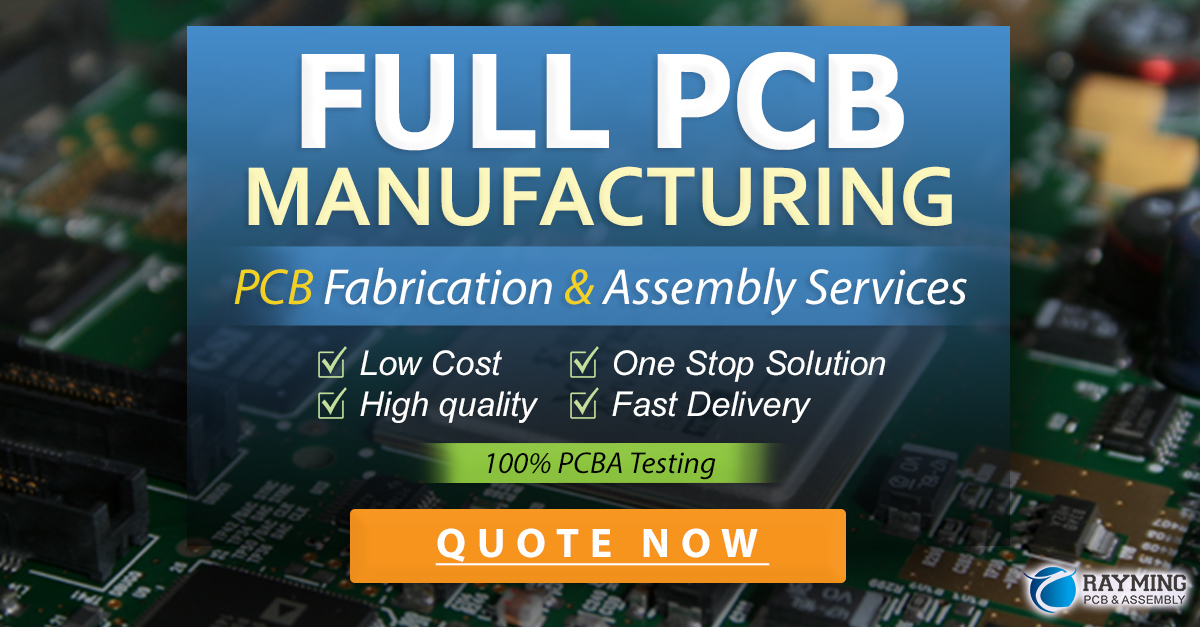
Design Considerations for Round PCBs
Designing round PCBs requires careful consideration of several factors to ensure optimal performance and manufacturability. Some key design considerations include:
Component Placement
When designing a round PCB, it is essential to consider the placement of components to ensure proper functionality and efficient use of available space. Components should be strategically placed to minimize signal path lengths, reduce EMI, and facilitate easy assembly and testing. It is also important to consider the mechanical constraints and clearances required for each component.
Signal Routing
Signal routing on round PCBs requires a different approach compared to rectangular designs. The circular shape presents unique challenges in terms of signal trace placement and routing. Designers must carefully plan the signal routes to ensure proper signal integrity, minimize crosstalk, and avoid signal reflections. The use of curved traces and strategic placement of vias can help in optimizing signal routing on round PCBs.
Thermal Management
Proper thermal management is crucial for the reliable operation of round PCBs, especially in applications with high power dissipation. Designers must consider the placement of heat-generating components and incorporate appropriate thermal management techniques such as heatsinks, thermal vias, and copper pours to dissipate heat effectively. Thermal simulations can be used to analyze and optimize the thermal performance of round PCBs.
Manufacturability
Designing round PCBs for manufacturability is essential to ensure cost-effectiveness and reliable production. Designers must consider factors such as minimum feature sizes, copper weights, drill sizes, and soldermask and silkscreen clearances to ensure compatibility with the manufacturing processes. Collaborating with the PCB manufacturer and adhering to their design guidelines can help in minimizing manufacturing issues and ensuring successful production of round PCBs.
Manufacturing Process for Round PCBs
The manufacturing process for round PCBs is similar to that of rectangular PCBs, with a few additional considerations. The key steps involved in the manufacturing process include:
PCB Fabrication
- Material Selection: The appropriate PCB substrate material, such as FR-4, is selected based on the application requirements and desired properties.
- Copper Cladding: The substrate is clad with a layer of copper on one or both sides, depending on the design requirements.
- Drilling: Holes are drilled through the PCB to accommodate components and vias.
- Patterning: The desired copper traces and pads are patterned onto the PCB using photolithography and etching processes.
- Soldermask and Silkscreen: A soldermask layer is applied to protect the copper traces, and a silkscreen layer is added for component labeling and identification.
PCB Assembly
- Solder Paste Application: Solder paste is applied to the pads on the PCB using a stencil or screen printing process.
- Component Placement: The components are placed onto the PCB using automated pick-and-place machines or manual assembly techniques.
- Reflow Soldering: The PCB is subjected to a controlled heating process to melt the solder paste and create permanent electrical connections between the components and the PCB.
- Inspection and Testing: The assembled PCB undergoes visual inspection and electrical testing to ensure proper functionality and quality.
Specialized Considerations for Round PCBs
- Panelization: Round PCBs are often panelized, which involves arranging multiple round PCBs on a larger rectangular panel for efficient manufacturing. Special attention must be given to the panelization layout to ensure proper spacing and support for the individual round PCBs.
- Depanelization: After the manufacturing process, the individual round PCBs need to be separated from the panel. Specialized depanelization techniques, such as routing or punching, are used to ensure clean and accurate separation of the round PCBs.
- Tooling: Manufacturing round PCBs may require specialized tooling, such as custom drill bits or routers, to accommodate the circular shape and ensure precise fabrication.
Testing and Quality Control
Ensuring the quality and reliability of round PCBs is crucial for their successful deployment in various applications. Thorough testing and quality control measures are implemented throughout the manufacturing process to identify and address any issues. Some common testing and quality control techniques include:
Visual Inspection
Visual inspection is performed at various stages of the manufacturing process to identify any visible defects or anomalies. This includes inspecting the PCB for proper copper patterning, soldermask coverage, silkscreen legibility, and overall appearance. Automated optical inspection (AOI) systems can be used to enhance the speed and accuracy of visual inspection.
Electrical Testing
Electrical testing is conducted to verify the functionality and performance of the round PCB. This includes tests such as:
– Continuity Testing: Verifies the electrical continuity of the copper traces and ensures there are no open circuits.
– Resistance Testing: Measures the resistance of the copper traces to ensure they meet the specified requirements.
– Insulation Resistance Testing: Checks the insulation resistance between different conductive parts of the PCB to detect any potential short circuits or leakage paths.
– Functional Testing: Verifies the overall functionality of the PCB by testing it under real-world operating conditions.
Environmental Testing
Environmental testing is performed to assess the performance and reliability of round PCBs under various environmental conditions. This includes tests such as:
– Temperature Cycling: Subjects the PCB to alternating high and low-temperature cycles to evaluate its ability to withstand thermal stresses.
– Humidity Testing: Exposes the PCB to high humidity levels to assess its resistance to moisture and potential corrosion.
– Vibration and Shock Testing: Evaluates the mechanical integrity of the PCB by subjecting it to vibrations and mechanical shocks.
– Electromagnetic Compatibility (EMC) Testing: Verifies the PCB’s compliance with EMC standards and ensures it does not generate excessive EMI or is susceptible to external electromagnetic interference.
Burn-In Testing
Burn-in testing involves operating the PCB under elevated temperature and voltage conditions for an extended period to identify any early failures or weak components. This testing helps in weeding out potential reliability issues and ensures the long-term stability of the round PCB.
Quality Control Documentation
Maintaining comprehensive quality control documentation is essential for traceability and continuous improvement. This includes recording test results, inspection reports, and any corrective actions taken. Quality control documentation helps in identifying trends, analyzing failure modes, and implementing necessary improvements in the design and manufacturing processes.
Frequently Asked Questions (FAQ)
1. What are the key advantages of using round PCBs over rectangular PCBs?
Round PCBs offer several advantages, including improved signal integrity, reduced electromagnetic interference (EMI), enhanced mechanical stability, space efficiency, and aesthetic appeal. The circular shape helps in minimizing signal distortions, reducing EMI emissions, and providing better resistance to mechanical stresses.
2. Are there any specific design considerations for round PCBs?
Yes, designing round PCBs requires careful consideration of factors such as component placement, signal routing, thermal management, and manufacturability. Designers must strategically place components, plan signal routes, incorporate appropriate thermal management techniques, and ensure compatibility with manufacturing processes to achieve optimal performance and reliability.
3. How does the manufacturing process differ for round PCBs compared to rectangular PCBs?
The manufacturing process for round PCBs is similar to that of rectangular PCBs, with a few additional considerations. Round PCBs often require panelization for efficient manufacturing, specialized depanelization techniques for separating individual PCBs from the panel, and customized tooling to accommodate the circular shape.
4. What types of testing and quality control measures are employed for round PCBs?
Round PCBs undergo various testing and quality control measures to ensure their quality and reliability. This includes visual inspection, electrical testing (continuity, resistance, insulation resistance, and functional testing), environmental testing (temperature cycling, humidity, vibration, and EMC testing), and burn-in testing. Comprehensive quality control documentation is maintained for traceability and continuous improvement.
5. In which industries are round PCBs commonly used?
Round PCBs find applications in a wide range of industries, including automotive (instrument clusters, steering wheel controls, airbag systems), aerospace and defense (avionics, radar systems, satellite communication devices), medical devices (wearable health monitors, implantable devices, surgical instruments), and consumer electronics (smartwatches, wireless earbuds, VR/AR devices).
Conclusion
Round PCBs offer a unique and advantageous alternative to traditional rectangular PCBs in various applications. With their improved signal integrity, reduced EMI, enhanced mechanical stability, and space efficiency, round PCBs are well-suited for industries such as automotive, aerospace, medical devices, and consumer electronics.
Designing and manufacturing round PCBs requires careful consideration of factors such as component placement, signal routing, thermal management, and manufacturability. Thorough testing and quality control measures, including visual inspection, electrical testing, environmental testing, and burn-in testing, ensure the quality and reliability of round PCBs.
As technology continues to advance and the demand for compact, high-performance electronics grows, round PCBs are expected to find increasing adoption in various industries. By understanding the advantages, design considerations, manufacturing processes, and testing requirements of round PCBs, designers and engineers can leverage this technology to create innovative and reliable products that meet the evolving needs of the market.
Leave a Reply