Understanding RoHS and Its Requirements
RoHS is a directive that originated in the European Union (EU) and has since been adopted by many countries worldwide. The directive restricts the use of six hazardous substances in electrical and electronic equipment:
- Lead (Pb)
- Mercury (Hg)
- Cadmium (Cd)
- Hexavalent Chromium (Cr6+)
- Polybrominated Biphenyls (PBB)
- Polybrominated Diphenyl Ethers (PBDE)
PCB manufacturers must ensure that their products contain no more than the maximum concentration values (MCVs) of these substances, which are set at 0.1% by weight for all substances except cadmium, which has an MCV of 0.01% by weight.
RoHS impact on PCB Materials and Components
One of the most significant impacts of RoHS on the PCB industry has been the need to find alternative materials and components that comply with the directive. This has led to the development of new, RoHS-compliant materials and the phasing out of non-compliant ones.
Lead-Free Solders
Lead-based solders were widely used in the PCB industry before the introduction of RoHS. However, as lead is one of the restricted substances, manufacturers have had to switch to lead-free alternatives. Some common lead-free solders include:
- Tin-Silver-Copper (SAC) alloys
- Tin-Copper (SnCu) alloys
- Tin-Bismuth (SnBi) alloys
While lead-free solders have helped PCB manufacturers comply with RoHS, they have also presented some challenges. Lead-free solders typically have higher melting points than lead-based solders, which can lead to increased thermal stress on components during the soldering process. This has required manufacturers to adjust their processes and equipment to accommodate the new materials.
Flame Retardants
Another area where RoHS has had an impact is in the use of flame retardants. Polybrominated biphenyls (PBBs) and polybrominated diphenyl ethers (PBDEs) were commonly used as flame retardants in PCBs before RoHS. As these substances are now restricted, manufacturers have had to find alternative flame retardants that comply with the directive. Some RoHS-compliant flame retardants include:
- Phosphorus-based compounds
- Nitrogen-based compounds
- Inorganic compounds (e.g., aluminum hydroxide, magnesium hydroxide)
Surface Finishes
RoHS has also affected the choice of surface finishes used on PCBs. Some traditional surface finishes, such as hot air solder leveling (HASL) with lead-based solders, are not compliant with RoHS. As a result, manufacturers have had to adopt alternative surface finishes, such as:
- Immersion tin
- Immersion silver
- Electroless nickel immersion gold (ENIG)
- Organic solderability preservatives (OSP)
Each of these surface finishes has its own advantages and disadvantages, and manufacturers must choose the most appropriate one based on factors such as cost, performance, and compatibility with the intended application.
RoHS Impact on PCB Manufacturing Processes
In addition to the changes in materials and components, RoHS has also had an impact on the manufacturing processes used in the PCB industry. Manufacturers have had to adapt their processes to ensure compliance with the directive and to accommodate the new materials being used.
Soldering Processes
The switch to lead-free solders has required changes in the soldering processes used by PCB manufacturers. Lead-free solders have higher melting points than lead-based solders, which means that higher temperatures are required for soldering. This has led to the development of new soldering techniques and equipment, such as:
- Nitrogen-assisted soldering
- Vapor phase soldering
- Laser soldering
These techniques help to minimize the thermal stress on components during the soldering process and ensure the formation of reliable solder joints.
Cleaning Processes
RoHS has also had an impact on the cleaning processes used in PCB manufacturing. Some traditional cleaning agents, such as those containing halogenated solvents, are not compliant with RoHS. As a result, manufacturers have had to adopt alternative cleaning agents and processes, such as:
- Aqueous cleaning
- Semi-aqueous cleaning
- No-clean fluxes
These cleaning methods are designed to remove flux residues and other contaminants from the PCB surface without the use of hazardous substances.
Quality Control and Testing
RoHS compliance has also led to changes in the quality control and testing procedures used by PCB manufacturers. Manufacturers must now ensure that their products meet the RoHS requirements for restricted substances, which has led to the development of new testing methods and equipment, such as:
- X-ray fluorescence (XRF) spectroscopy
- Inductively coupled plasma (ICP) spectroscopy
- Ion chromatography
These methods allow manufacturers to accurately measure the levels of restricted substances in their products and ensure compliance with RoHS.
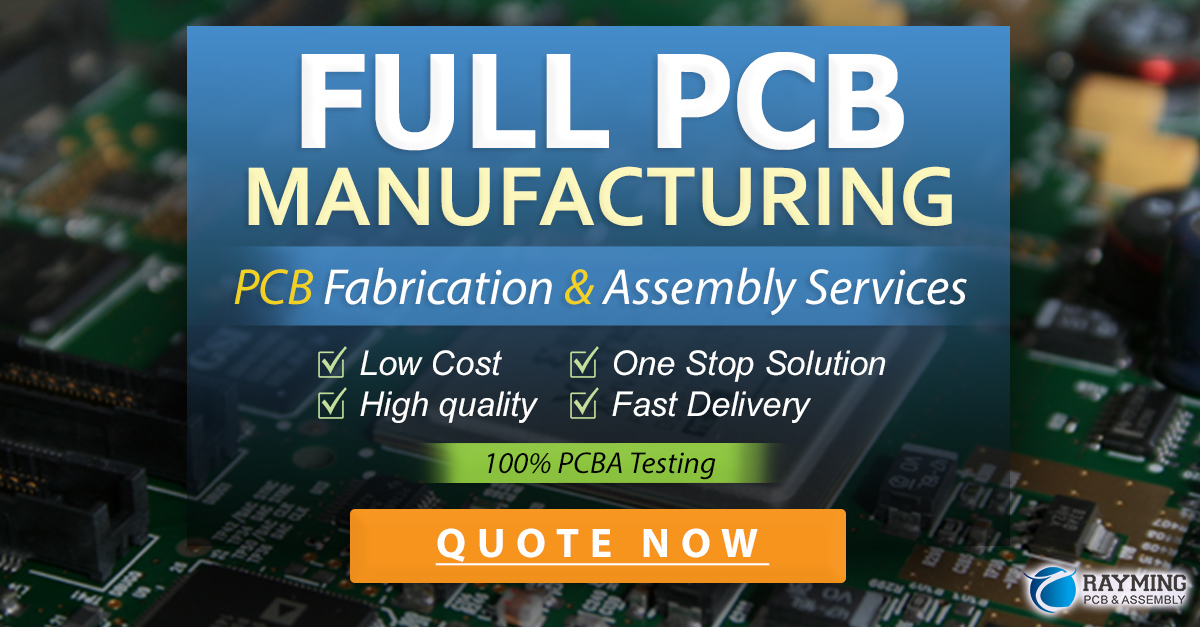
RoHS Impact on PCB Design
RoHS has also had an impact on the design of PCBs. Designers must now take into account the restrictions on hazardous substances when selecting materials and components for their designs. This has led to changes in the way PCBs are designed, such as:
Component Selection
Designers must now choose components that are RoHS-compliant and avoid those that contain restricted substances. This has led to the development of extensive databases of RoHS-compliant components and the phasing out of non-compliant ones.
Material Selection
Similarly, designers must also choose PCB materials that are RoHS-compliant. This includes the base material, soldermask, and silkscreen inks used in the PCB. Designers must work closely with their PCB manufacturers to ensure that the materials used in their designs are compliant with RoHS.
Design for Manufacturing (DFM)
RoHS has also had an impact on the design for manufacturing (DFM) practices used in the PCB industry. Designers must now take into account the new materials and processes being used by manufacturers and design their PCBs accordingly. This includes considerations such as:
- Selecting components with suitable lead-free terminations
- Providing adequate clearances and tolerances for lead-free soldering
- Specifying RoHS-compliant surface finishes and soldermasks
By incorporating these considerations into their designs, PCB designers can help ensure that their products can be manufactured in compliance with RoHS.
RoHS Compliance and Documentation
One of the key aspects of RoHS is the requirement for manufacturers to provide documentation to demonstrate compliance with the directive. This documentation must include information on the materials and components used in the product, as well as the testing and quality control procedures used to ensure compliance.
PCB manufacturers must maintain detailed records of their materials and processes, including:
- Material declarations from suppliers
- Certificates of compliance for components and materials
- Test reports demonstrating compliance with RoHS limits
- Process control records and quality control data
This documentation must be made available to customers and regulatory authorities upon request to demonstrate compliance with RoHS.
Future Developments and Challenges
As RoHS continues to evolve and new requirements are introduced, the PCB industry will need to adapt to stay compliant. Some potential future developments and challenges include:
Expansion of RoHS to New Substances
The list of restricted substances under RoHS may be expanded in the future to include new substances that are deemed to be hazardous. PCB manufacturers will need to stay up-to-date with any changes to the directive and be prepared to adapt their materials and processes accordingly.
Increasing Complexity of Electronics
As electronic devices become increasingly complex, with more components and higher performance requirements, PCB manufacturers will face new challenges in ensuring RoHS compliance. This may require the development of new materials, processes, and testing methods to meet the demands of these advanced applications.
Supply Chain Management
RoHS compliance requires close cooperation and communication throughout the supply chain, from material suppliers to end-product manufacturers. PCB manufacturers will need to work closely with their suppliers and customers to ensure that all materials and components used in their products are RoHS-compliant and that the necessary documentation is available.
Recycling and Disposal
The restriction of hazardous substances in electronics also has implications for the recycling and disposal of these products at the end of their life. PCB manufacturers will need to consider the environmental impact of their products and work with recycling and disposal facilities to ensure that they are handled appropriately.
Frequently Asked Questions (FAQ)
- What is RoHS, and why was it introduced?
-
RoHS (Restriction of Hazardous Substances) is a directive that restricts the use of certain hazardous substances in electrical and electronic equipment. It was introduced to reduce the environmental and health risks associated with the disposal of electronic waste.
-
What are the substances restricted under RoHS?
-
The six substances restricted under RoHS are lead (Pb), mercury (Hg), cadmium (Cd), hexavalent chromium (Cr6+), polybrominated biphenyls (PBB), and polybrominated diphenyl ethers (PBDE).
-
How has RoHS affected the materials used in PCBs?
-
RoHS has led to the development of new, compliant materials for PCBs, such as lead-free solders, alternative flame retardants, and RoHS-compliant surface finishes. Non-compliant materials have been phased out.
-
What changes have PCB manufacturers made to their processes to comply with RoHS?
-
PCB manufacturers have adapted their soldering, cleaning, and quality control processes to accommodate the new materials and ensure compliance with RoHS. This includes the use of new soldering techniques, cleaning agents, and testing methods.
-
How can PCB designers ensure RoHS compliance in their products?
- PCB designers can ensure RoHS compliance by selecting RoHS-compliant components and materials, providing adequate clearances and tolerances for lead-free soldering, and specifying RoHS-compliant surface finishes and soldermasks. They should also work closely with their PCB manufacturers to ensure compliance throughout the manufacturing process.
Conclusion
The introduction of RoHS has had a profound impact on the PCB industry, requiring manufacturers to adapt their materials, processes, and designs to comply with the directive. While this has presented challenges, it has also led to the development of new, more environmentally friendly materials and techniques.
As RoHS continues to evolve and new requirements are introduced, the PCB industry will need to remain vigilant and adaptable to stay compliant. This will require close cooperation and communication throughout the supply chain, as well as a commitment to ongoing research and development.
Despite the challenges, the benefits of RoHS are clear. By restricting the use of hazardous substances in electronics, RoHS helps to protect human health and the environment, while also promoting the development of more sustainable and responsible manufacturing practices. As the world becomes increasingly focused on sustainability and environmental protection, the importance of directives like RoHS will only continue to grow.
Leave a Reply