Introduction to Resistive Touch Technology
Resistive touch is a common type of touchscreen technology used in various electronic devices, including smartphones, tablets, point-of-sale systems, and industrial control panels. It offers a cost-effective solution for enabling touch input and has been widely adopted due to its reliability, durability, and compatibility with various input methods.
In this comprehensive article, we will dive deep into the world of resistive Touch Sensors, exploring their working principles, advantages, disadvantages, and applications. By the end of this article, you will have a thorough understanding of how resistive touch technology functions and its significance in the realm of human-machine interaction.
What is a Resistive Touch Sensor?
A resistive touch sensor is a type of touchscreen that relies on the principle of electrical resistance to detect and localize touch inputs. It consists of two flexible, transparent layers separated by a thin gap. These layers are coated with a resistive material, typically indium tin oxide (ITO), and have conductive traces running along the edges.
When a user touches the screen, the two layers make contact at the point of pressure, causing a change in electrical resistance. The touchscreen controller then measures this change and calculates the coordinates of the touch point, enabling the device to respond accordingly.
Key Components of a Resistive Touch Sensor
- Top layer: A flexible, transparent polyester film coated with a resistive material (usually ITO) on the inner side.
- Bottom layer: A rigid, transparent substrate (glass or acrylic) coated with a resistive material (usually ITO) on the surface facing the top layer.
- Spacer dots: Tiny, transparent dots placed between the two layers to maintain a small gap and prevent accidental contact.
- Conductive traces: Thin, conductive lines running along the edges of the layers, used for applying voltage and measuring resistance.
- Touchscreen controller: A microcontroller that applies voltage, measures resistance changes, and calculates touch coordinates.
How Does a Resistive Touch Sensor Work?
The working principle of a resistive touch sensor involves measuring changes in electrical resistance to determine the location of a touch input. Let’s break down the process step by step:
- Voltage application: The touchscreen controller applies a voltage across the conductive traces on one layer, creating a uniform voltage gradient.
- Touch input: When a user touches the screen, the two layers make contact at the point of pressure, causing a change in electrical resistance at that location.
- Resistance measurement: The touchscreen controller measures the voltage drop across the conductive traces on the other layer, which is proportional to the resistance at the touch point.
- Coordinate calculation: By comparing the measured voltage drop to the known voltage gradient, the controller calculates the X and Y coordinates of the touch point.
- Signal processing: The calculated coordinates are then processed by the device’s software to trigger the appropriate response or action.
This process is repeated continuously, allowing the device to track touch inputs in real-time.
Voltage Divider Principle
The resistive touch sensor’s operation is based on the voltage divider principle. When a voltage is applied across a uniform resistive layer, it creates a linear voltage gradient. The measured voltage at any point along the layer is proportional to the distance from the edge where the voltage is applied.
In a resistive touch sensor, the two layers act as variable resistors in a voltage divider circuit. When a touch occurs, the resistance at the contact point changes, causing a corresponding change in the measured voltage. By measuring the voltage drop along both the X and Y axes, the touchscreen controller can determine the precise coordinates of the touch point.
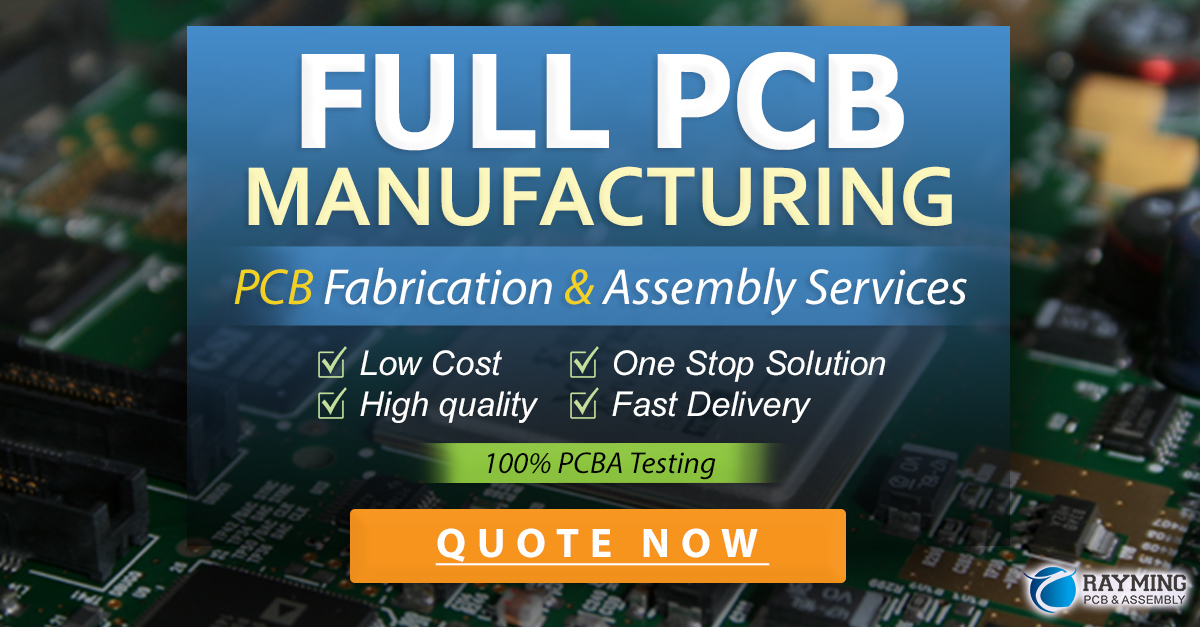
Advantages of Resistive Touch Sensors
Resistive touch sensors offer several advantages that make them a popular choice for various applications:
- Cost-effectiveness: Resistive touch sensors are relatively inexpensive to manufacture compared to other touchscreen technologies, making them a cost-effective solution for many devices.
- Durability: The flexible top layer of a resistive touch sensor can withstand repeated pressure and is resistant to scratches and abrasions, ensuring a long lifespan.
- Versatility: Resistive touch sensors can be operated with any object that applies pressure, including fingers, styluses, and gloved hands, making them suitable for various environments and use cases.
- Reliability: Resistive touch technology is well-established and has proven to be reliable in a wide range of applications, from consumer electronics to industrial control panels.
- Low power consumption: Resistive touch sensors require minimal power to operate, making them ideal for battery-powered devices and energy-efficient applications.
Disadvantages of Resistive Touch Sensors
Despite their advantages, resistive touch sensors also have some limitations:
- Reduced optical clarity: The multiple layers of a resistive touch sensor can reduce the optical clarity of the display, as light must pass through both the top and bottom layers.
- Pressure requirement: Resistive touch sensors require a certain amount of pressure to activate, which may not be suitable for applications that rely on light touches or gestures.
- Limited multi-touch support: Most resistive touch sensors only support single-touch input, while some advanced models may offer limited multi-touch capabilities.
- Wear and tear: Over time, the repeated pressure applied to the flexible top layer can cause wear and tear, potentially leading to reduced sensitivity or dead spots on the screen.
- Interference from contaminants: Contaminants such as dust, dirt, or liquids can interfere with the proper functioning of a resistive touch sensor, requiring regular cleaning to maintain optimal performance.
Applications of Resistive Touch Sensors
Resistive touch sensors are used in a wide range of applications across various industries:
- Consumer electronics: Smartphones, tablets, e-readers, and gaming devices.
- Retail and hospitality: Point-of-sale systems, kiosks, and self-service terminals.
- Industrial control: Machine control panels, human-machine interfaces (HMIs), and automation systems.
- Medical devices: Patient monitors, medical equipment control panels, and diagnostic tools.
- Automotive: In-vehicle infotainment systems, navigation displays, and climate control panels.
- Education: Interactive whiteboards, educational tablets, and learning aids.
Industry | Applications |
---|---|
Consumer electronics | Smartphones, tablets, e-readers, gaming devices |
Retail and hospitality | Point-of-sale systems, kiosks, self-service terminals |
Industrial control | Machine control panels, HMIs, automation systems |
Medical devices | Patient monitors, medical equipment control panels, diagnostic tools |
Automotive | In-vehicle infotainment systems, navigation displays, climate control panels |
Education | Interactive whiteboards, educational tablets, learning aids |
The versatility and cost-effectiveness of resistive touch sensors make them a popular choice across these diverse applications, enabling intuitive and user-friendly interactions between humans and machines.
Touchscreen Controller and Interface
The touchscreen controller is a crucial component of a resistive touch sensor system, responsible for managing the touch input process and communicating with the host device. Let’s explore the role of the touchscreen controller and the common interfaces used for communication.
Touchscreen Controller Functions
The touchscreen controller performs several key functions:
- Voltage application: The controller applies the necessary voltages across the conductive traces of the touch sensor layers to create a voltage gradient.
- Analog-to-digital conversion (ADC): It converts the analog voltage measurements from the touch sensor into digital values for processing.
- Coordinate calculation: The controller uses the digital voltage values to calculate the X and Y coordinates of the touch point based on the voltage divider principle.
- Filtering and calibration: It applies filtering algorithms to reduce noise and performs calibration to ensure accurate and consistent touch readings.
- Communication: The controller communicates the touch coordinates and other relevant data to the host device using a standard interface protocol.
Common Interface Protocols
Touchscreen controllers communicate with the host device using various interface protocols, depending on the specific application and system requirements. Some common interface protocols include:
- I2C (Inter-Integrated Circuit): A widely used two-wire serial communication protocol that allows the host device to communicate with the touchscreen controller using just two lines: SCL (serial clock) and SDA (serial data).
- SPI (Serial Peripheral Interface): A four-wire serial communication protocol that offers higher data transfer speeds compared to I2C, using four lines: SCLK (serial clock), MOSI (master output, slave input), MISO (master input, slave output), and SS (slave select).
- USB (Universal Serial Bus): A popular interface for connecting peripherals to host devices, offering high bandwidth and ease of use. Some touchscreen controllers include USB interfaces for direct connection to a host device.
- UART (Universal Asynchronous Receiver/Transmitter): A serial communication protocol that transmits data asynchronously, commonly used in embedded systems and microcontroller-based applications.
The choice of interface protocol depends on factors such as data transfer speed requirements, available system resources, and compatibility with the host device.
Touchscreen Overlay Materials and Construction
The performance and durability of a resistive touch sensor largely depend on the materials and construction techniques used in its manufacture. In this section, we will explore the common materials and construction methods employed in resistive touch sensors.
Transparent Conductive Materials
The transparent conductive material used in resistive touch sensors is crucial for maintaining optical clarity while enabling touch sensitivity. The most common material used is indium tin oxide (ITO), a transparent and conductive oxide made from a mixture of indium oxide (In2O3) and tin oxide (SnO2).
ITO offers several advantages:
- High transparency: ITO films can achieve an optical transmittance of over 90%, ensuring minimal impact on display quality.
- Good conductivity: ITO has a relatively low electrical resistance, allowing for efficient voltage gradient creation and touch sensing.
- Durability: ITO films are resistant to scratches and abrasions, contributing to the overall durability of the touch sensor.
Other transparent conductive materials, such as aluminum-doped zinc oxide (AZO) and graphene, are being explored as potential alternatives to ITO, offering improved performance and cost-effectiveness.
Layer Construction
The construction of a resistive touch sensor involves the following layers:
- Top layer: A flexible, transparent polyester film (such as PET) is coated with a thin layer of ITO on the inner side. This layer serves as the touch surface and flexes under pressure to make contact with the bottom layer.
- Spacer dots: Tiny, transparent spacer dots are printed or applied onto the inner surface of either the top or bottom layer. These dots maintain a uniform gap between the two layers, preventing accidental contact and ensuring consistent touch sensitivity.
- Bottom layer: A rigid, transparent substrate (usually glass or acrylic) is coated with a thin layer of ITO on the surface facing the top layer. This layer acts as the stable base for the touch sensor.
- Conductive traces: Thin, conductive traces (usually made from silver or carbon) are printed along the edges of the ITO layers, enabling voltage application and resistance measurement.
- Protective coating: A clear, protective coating may be applied to the outer surface of the top layer to improve durability and resistance to scratches and contaminants.
The layers are laminated together using optically clear adhesives (OCAs) to create a compact and stable touch sensor assembly.
Manufacturing Processes
The manufacturing of resistive touch sensors involves several key processes:
- ITO deposition: The ITO layers are deposited onto the polyester film and glass/acrylic substrate using techniques such as sputtering or physical vapor deposition (PVD).
- Patterning: The ITO layers are patterned using photolithography or laser ablation to create the desired electrode layout and conductive traces.
- Spacer dot application: The spacer dots are applied to one of the layers using screen printing, photolithography, or other precise deposition methods.
- Lamination: The layers are aligned and laminated together using OCAs and pressure-sensitive adhesives (PSAs) to create the final touch sensor assembly.
- Bonding: The touch sensor assembly is bonded to the display module or cover lens using OCAs or other bonding techniques to ensure proper integration and optical clarity.
Careful control of these manufacturing processes is essential for ensuring the quality, reliability, and performance of the resistive touch sensor.
Touchscreen Performance and Specification
Resistive touchscreens are specified based on several key performance factors and specifications. When selecting the right resistive touch sensor for a particular application, it’s essential to consider the following factors:
-
Resolution: The resolution of a resistive touchscreen is usually specified in terms of the number of touch points that can be detected per inch (PPI). Higher resolutions allow for more accurate and precise touch detection. Typical resolutions range from 4096 x 4096 to 16384 x 16384.
-
Linearity: Linearity refers to the accuracy of the touch point measurement across the entire screen surface. It is usually expressed as a percentage of the maximum deviation from the ideal, linear response. A linearity of ±1.5% is considered acceptable for most applications.
-
Sensitivity: Touch sensitivity is the amount of pressure required to trigger a touch event. It is usually specified in terms of the minimum activation force (in grams or Newtons) needed to cause a touch registration. Typical activation forces range from 20g to 100g. Lower activation forces enable lighter touch interactions but may also lead to accidental touches.
-
Response time: The response time is the time taken for the touchscreen to detect and report a touch event to the host device. Faster response times enable more responsive and fluid user interactions. Response times are usually measured in milliseconds (ms) and can range from 5ms to 20ms.
-
Durability: The durability of a resistive touchscreen is determined by its ability to withstand repeated touches, pressure, and environmental factors such as temperature and humidity. Durability is usually specified in terms of the number of touch cycles the screen can endure before experiencing significant degradation in performance. Typical durability ratings range from 1 million to 10 million touches.
-
Optical clarity: Optical clarity refers to the amount of light that can pass through the touchscreen layers without being absorbed or scattered. It is usually specified in terms of the percentage of light transmission. Higher optical clarity ensures better display quality and readability. Typical optical clarity values range from 80% to 90%.
-
Operating temperature range: The operating temperature range specifies the minimum and maximum temperatures at which the touchscreen can function reliably. This is particularly important for applications in harsh or outdoor environments. Typical operating temperature ranges are from -20°C to 70°C.
-
Compatibility: Compatibility refers to the touchscreen’s ability to work seamlessly with different operating systems, software frameworks, and communication interfaces (such as I2C, SPI, USB). Ensuring compatibility with the intended host device and software environment is crucial for successful integration.
Specification | Typical Range |
---|---|
Resolution (PPI) | 4096 x 4096 to 16384 x 16384 |
Linearity | ±1.5% |
Sensitivity (activation force) | 20g to 100g |
Response time | 5ms to 20ms |
Durability (touch cycles) | 1 million to 10 million |
Optical clarity (light transmission) | 80% to 90% |
Operating temperature range | -20°C to 70°C |
By carefully considering these performance factors and specifications, designers and engineers can select the most suitable resistive touchscreen for their specific application requirements, ensuring optimal user experience and system functionality.
Future Developments and Alternatives
While resistive touch technology has been widely adopted and proven reliable, there are ongoing developments and alternative touchscreen technologies that aim to address some of the limitations of resistive touch sensors. In this section, we will explore some of these future developments and alternative technologies.
Hybrid Touch Sensors
Hybrid touch sensors combine the benefits of resistive and capacitive touch technologies to create a more versatile and high-performance touchscreen solution. These sensors typically consist of a resistive touch layer and a capacitive touch layer, enabling both pressure-based and proximity-based touch detection.
Advantages of hybrid touch sensors include:
- Multi-touch support: The capacitive layer enables true multi-touch functionality, allowing for more advanced gestures and interactions.
- Improved sensitivity: The combination of resistive and capacitive sensing enhances overall touch sensitivity, enabling lighter touch interactions and improved responsiveness.
- Compatibility with various input methods: Hybrid touch sensors can be operated with fingers, styluses, and gloved hands, combining the versatility of resistive touch with the precision of capacitive touch.
Piezoelectric Touch Sensors
Piezoelectric touch sensors utilize the piezoelectric effect to detect touch inputs. These sensors are made from piezoelectric materials, such as polyvinylidene fluoride (PVDF), which generate an electrical charge when subjected to mechanical stress or pressure.
Advantages of piezoelectric touch sensors include:
- High sensitivity: Piezoelectric materials are highly sensitive to pressure, enabling the detection of even the lightest touch inputs.
- Fast response time: The piezoelectric effect occurs almost instantaneously, resulting in faster touch detection and response times compared to resistive touch sensors.
- **Dur
Leave a Reply