Introduction
Printed Circuit Boards (PCBs) are essential components in modern electronic devices, ranging from smartphones and computers to industrial equipment and medical devices. The cost of manufacturing and assembling PCBs can significantly impact the overall production cost of these devices. In this article, we will discuss the top 7 tips to help save cost during PCB manufacturing and assembly, ensuring that you can produce high-quality PCBs while keeping your expenses under control.
Tip 1: Optimize Your PCB Design for Cost-Effective Manufacturing
Choosing the Right PCB Size and Shape
One of the most crucial factors in determining the cost of your PCB is its size and shape. By optimizing your PCB design to use standard sizes and shapes, you can reduce manufacturing costs and minimize waste. Standard PCB sizes include:
PCB Size | Dimensions (mm) |
---|---|
Small | 50 x 50 |
Medium | 100 x 100 |
Large | 200 x 200 |
When designing your PCB, consider using rectangular shapes instead of irregular or complex shapes, as they are easier and more cost-effective to manufacture.
Minimizing the Number of Layers
The number of layers in your PCB directly impacts its manufacturing cost. Fewer layers generally result in lower costs. Consider the following tips to minimize the number of layers in your PCB:
- Use smaller components and optimize their placement to reduce the need for additional layers.
- Utilize both sides of the PCB for component placement and routing.
- Employ efficient routing techniques to minimize the number of required layers.
Number of Layers | Cost Impact |
---|---|
1-2 | Low |
4 | Medium |
6+ | High |
Choosing the Right Materials
The materials used in your PCB can also affect its cost. Consider using standard, readily available materials such as FR-4 for the PCB substrate and copper for the conductive layers. Avoid using exotic or specialty materials unless absolutely necessary, as they can significantly increase costs.
Tip 2: Leverage Economy of Scale
Ordering in Bulk
One of the most effective ways to reduce PCB Manufacturing Costs is to order in bulk. As the quantity of PCBs increases, the cost per unit generally decreases. This is because the fixed costs associated with setting up the manufacturing process are spread across a larger number of units.
Quantity | Cost per Unit |
---|---|
1-10 | $$$$$ |
11-100 | $$$$ |
101-1000 | $$$ |
1000+ | $$ |
Combining Multiple Designs in a Single Panel
If you have multiple PCB designs, consider combining them into a single panel for manufacturing. This approach, known as panelization, allows you to produce multiple PCBs in a single production run, reducing setup costs and increasing efficiency.
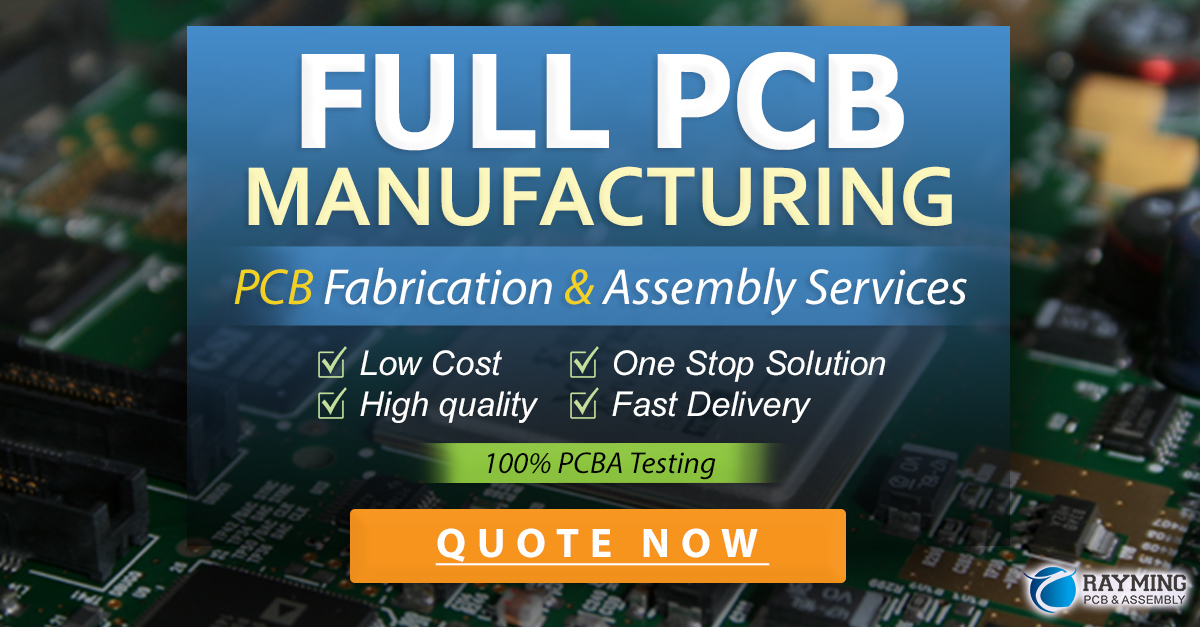
Tip 3: Choose the Right PCB Manufacturer
Researching and Comparing Manufacturers
Not all PCB manufacturers are created equal. It’s essential to research and compare different manufacturers to find one that offers the best combination of quality, cost, and service. Consider factors such as:
- Experience and reputation in the industry
- Quality control processes and certifications (e.g., ISO 9001, UL, RoHS)
- Turnaround time and delivery options
- Customer support and communication
Establishing Long-Term Relationships
Building long-term relationships with your PCB manufacturer can lead to cost savings and improved service. By consistently working with the same manufacturer, you can:
- Negotiate better pricing based on your ongoing business
- Streamline communication and reduce the risk of errors
- Benefit from the manufacturer’s familiarity with your designs and requirements
Tip 4: Optimize Your Component Selection
Using Standard Components
Whenever possible, use standard, readily available components in your PCB design. Standard components are generally less expensive than custom or specialty components, and they are easier to source and replace if needed. Some common standard components include:
- Resistors
- Capacitors
- Inductors
- Diodes
- Transistors
Minimizing the Variety of Components
Minimizing the variety of components used in your PCB can also help reduce costs. By using fewer unique components, you can:
- Simplify your supply chain and reduce inventory costs
- Benefit from volume discounts when purchasing components
- Streamline the assembly process, reducing the time and cost associated with component placement
Tip 5: Consider Automated Assembly
Benefits of Automated Assembly
Automated PCB Assembly, using techniques such as Surface Mount Technology (SMT), can significantly reduce assembly costs compared to manual assembly. Automated assembly offers several benefits:
- Faster assembly times
- Improved accuracy and consistency
- Reduced labor costs
- Higher throughput and production volumes
When to Choose Automated Assembly
Automated assembly is particularly cost-effective for high-volume production runs or PCBs with a large number of components. However, for low-volume production or PCBs with a few components, manual assembly may be more economical.
Production Volume | Recommended Assembly Method |
---|---|
Low (1-100) | Manual |
Medium (101-1000) | Semi-Automated |
High (1000+) | Fully Automated |
Tip 6: Implement Effective Quality Control Measures
Importance of Quality Control
Implementing effective quality control measures throughout the PCB manufacturing and assembly process can help prevent costly errors and rework. Quality control measures should be in place at every stage, including:
- Design review and verification
- Material and component inspections
- Manufacturing process controls
- Post-assembly testing and inspection
Cost Savings Through Quality Control
By catching and correcting issues early in the process, you can avoid the cost of scrapping or reworking defective PCBs. Additionally, effective quality control can help improve your product’s reliability and reduce the risk of field failures, which can be highly expensive to address.
Tip 7: Continuously Monitor and Optimize Your Process
Tracking and Analyzing Costs
To effectively reduce PCB manufacturing and assembly costs, it’s essential to continuously monitor and analyze your costs. Regularly track and review expenses associated with:
- Materials and components
- Manufacturing and assembly processes
- Quality control and testing
- Shipping and logistics
By understanding where your costs are coming from, you can identify areas for improvement and make data-driven decisions to optimize your process.
Implementing Continuous Improvement
Continuously strive to improve your PCB manufacturing and assembly process. Encourage open communication and collaboration among your team members, suppliers, and manufacturers to identify and implement cost-saving opportunities. Some strategies for continuous improvement include:
- Regularly reviewing and updating your PCB designs for cost optimization
- Investigating new materials, components, and manufacturing technologies
- Streamlining your supply chain and logistics processes
- Providing ongoing training and education for your team members
Frequently Asked Questions (FAQ)
-
Q: How much can I expect to save by implementing these cost-saving tips?
A: The amount you can save will depend on various factors, such as your current process, the complexity of your PCBs, and the volume of your production. However, implementing these tips can potentially lead to cost savings of 10-30% or more. -
Q: Can I use these cost-saving tips for both prototype and production PCBs?
A: Yes, many of these tips can be applied to both prototype and production PCBs. However, some strategies, such as ordering in bulk or using automated assembly, may be more suitable for production runs. -
Q: Will implementing these cost-saving measures affect the quality of my PCBs?
A: When implemented correctly, these cost-saving measures should not compromise the quality of your PCBs. In fact, some strategies, such as optimizing your design and implementing effective quality control measures, can actually improve the overall quality of your PCBs. -
Q: How long does it typically take to see the benefits of implementing these cost-saving tips?
A: The time it takes to see the benefits will vary depending on the specific tips you implement and the nature of your PCB manufacturing and assembly process. Some strategies, such as optimizing your design or choosing the right manufacturer, may yield immediate results, while others, such as implementing continuous improvement initiatives, may take longer to show significant cost savings. -
Q: Can I implement these cost-saving tips on my own, or do I need to involve my team and suppliers?
A: While some of these tips can be implemented independently, involving your team, suppliers, and manufacturers can lead to more significant and sustainable cost savings. Collaboration and open communication are key to identifying and implementing the most effective cost-saving strategies for your specific situation.
Conclusion
Reducing PCB manufacturing and assembly costs is crucial for maintaining a competitive edge in today’s market. By implementing the top 7 tips discussed in this article, you can optimize your PCB design, leverage economy of scale, choose the right manufacturer, optimize component selection, consider automated assembly, implement effective quality control measures, and continuously monitor and optimize your process. By taking a proactive approach to cost savings, you can produce high-quality PCBs while keeping your expenses under control, ultimately leading to increased profitability and success for your business.
Leave a Reply