Introduction to PCB Assembly
PCB (Printed Circuit Board) assembly is the process of soldering or mounting electronic components onto a printed circuit board. It is a crucial step in the manufacturing of electronic devices, as it transforms the bare PCB into a functional electronic assembly. PCB assembly involves several processes, including solder paste application, component placement, soldering, and inspection.
In this comprehensive article, we will delve into the various aspects of PCB assembly, providing you with essential information to help you understand this critical process better.
Types of PCB Assembly
There are two main types of PCB assembly: Through-Hole (THT) and Surface Mount (SMT) assembly.
Through-Hole Technology (THT) Assembly
Through-hole technology involves mounting components with wire leads onto a PCB by inserting the leads through drilled holes on the board. The leads are then soldered to pads on the opposite side of the board. THT assembly is generally used for larger components that require more mechanical stability, such as transformers, connectors, and some capacitors.
Advantages of THT assembly:
– Stronger mechanical bonds
– Easy to replace or repair components
– Suitable for high-power and high-voltage applications
Disadvantages of THT assembly:
– Slower assembly process
– Larger components and PCB sizes
– Higher cost for high-volume production
Surface Mount Technology (SMT) Assembly
Surface mount technology involves placing components directly onto pads on the surface of a PCB, without the need for drilled holes. The components are then soldered to the pads using techniques such as reflow soldering or wave soldering. SMT assembly is widely used for smaller components, such as resistors, capacitors, and integrated circuits.
Advantages of SMT assembly:
– Faster assembly process
– Smaller components and PCB sizes
– Lower cost for high-volume production
– Higher component density
Disadvantages of SMT assembly:
– Requires specialized equipment and skills
– More difficult to replace or repair components
– Less suitable for high-power and high-voltage applications
PCB Assembly Process
The PCB assembly process typically involves the following steps:
-
Solder Paste Application: Solder paste, a mixture of tiny solder particles and flux, is applied to the pads on the PCB using a stencil or screen printing process.
-
Component Placement: The electronic components are placed onto the PCB, either manually or using automated pick-and-place machines. The components are aligned with the pads and held in place by the solder paste.
-
Soldering: The PCB is heated to melt the solder paste, forming a permanent electrical and mechanical connection between the components and the pads. This is typically done using reflow soldering for SMT components and wave soldering for THT components.
-
Inspection: The assembled PCB undergoes visual and automated optical inspection (AOI) to ensure that all components are correctly placed and soldered. Any defects or issues are identified and corrected at this stage.
-
Testing: The assembled PCB is tested for functionality and performance using various methods, such as in-circuit testing (ICT), boundary scan testing, or functional testing.
-
Conformal Coating and Potting: In some cases, the assembled PCB may be coated with a protective layer (conformal coating) or encapsulated in a resin (potting) to protect it from environmental factors such as moisture, dust, or mechanical stress.
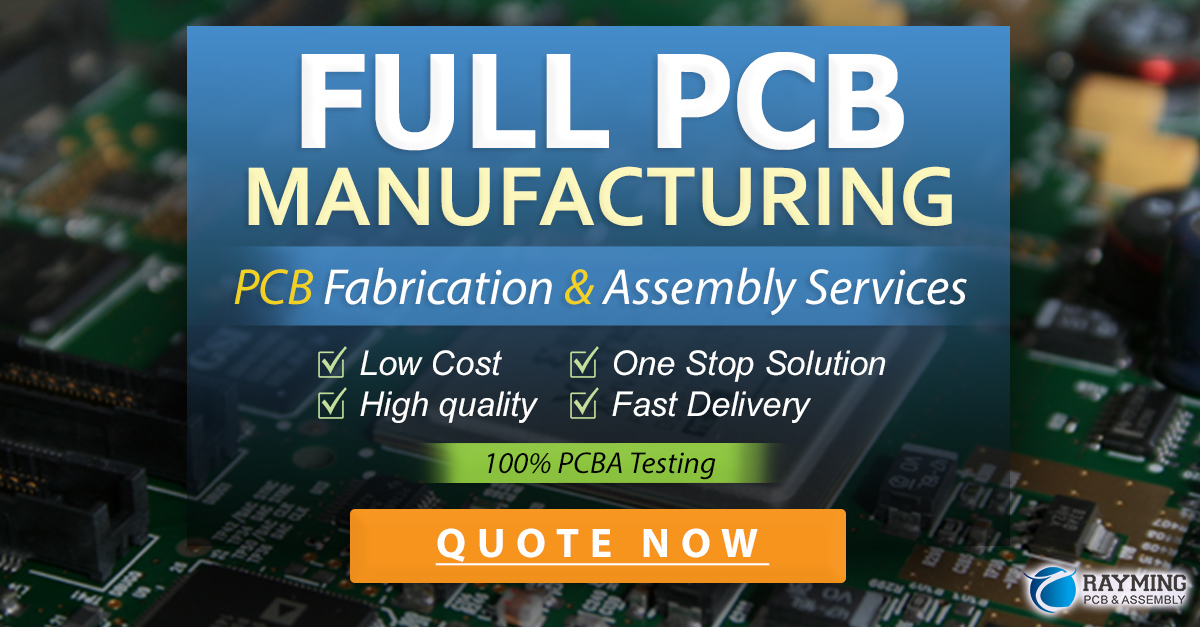
Factors Affecting PCB Assembly Quality
Several factors can impact the quality of PCB assembly, including:
-
PCB Design: A well-designed PCB with appropriate component spacing, trace widths, and clearances can facilitate easier and more reliable assembly.
-
Component Selection: Choosing high-quality, reliable components from reputable suppliers can minimize the risk of defects and failures.
-
Solder Paste Quality: The quality and composition of the solder paste can affect the soldering process and the final joint strength.
-
Manufacturing Equipment: Using modern, well-maintained manufacturing equipment, such as pick-and-place machines and reflow ovens, can improve the accuracy and consistency of the assembly process.
-
Operator Skill: Skilled and experienced operators are essential for manual assembly tasks and for monitoring and troubleshooting automated processes.
-
Process Control: Implementing strict process controls, such as temperature profiles, cleanliness standards, and ESD (electrostatic discharge) protection, can help ensure consistent assembly quality.
Benefits of Outsourcing PCB Assembly
Many companies choose to outsource PCB assembly to specialized service providers, rather than maintaining in-house assembly capabilities. Some benefits of outsourcing PCB assembly include:
-
Cost Savings: Outsourcing can reduce capital investment in equipment and facilities, as well as labor and overhead costs.
-
Access to Expertise: PCB assembly service providers have specialized knowledge and experience in various assembly techniques and can provide valuable advice and support.
-
Scalability: Outsourcing allows companies to quickly scale their production up or down based on demand, without the need to invest in additional capacity.
-
Focus on Core Competencies: By outsourcing PCB assembly, companies can focus on their core competencies, such as product design and marketing, while leaving the manufacturing to experts.
-
Quality Assurance: Reputable PCB assembly service providers have stringent quality control processes and certifications, such as ISO 9001, IPC-A-610, and J-STD-001, ensuring high-quality assembly.
Choosing a PCB Assembly Service Provider
When selecting a PCB assembly service provider, consider the following factors:
-
Experience and Expertise: Look for a provider with a proven track record in assembling PCBs similar to yours, in terms of complexity, volume, and technology.
-
Quality Standards: Ensure that the provider adheres to industry-recognized quality standards, such as IPC-A-610 and J-STD-001, and has appropriate certifications.
-
Manufacturing Capabilities: Verify that the provider has the necessary equipment and processes to handle your specific assembly requirements, such as SMT, THT, or mixed-technology assembly.
-
Turnaround Time: Consider the provider’s typical lead times and their ability to meet your delivery schedules.
-
Customer Support: Evaluate the provider’s responsiveness, communication, and willingness to collaborate and provide support throughout the assembly process.
-
Cost: While cost is an important factor, it should not be the sole deciding factor. Balance cost with quality, reliability, and service to ensure the best value for your investment.
Common PCB Assembly Defects and How to Prevent Them
Despite advances in manufacturing processes and quality control, PCB assembly defects can still occur. Some common defects include:
-
Solder Bridges: Unintended connections between adjacent pads or traces due to excess solder. Prevention: Proper solder paste application, stencil design, and temperature control.
-
Cold Solder Joints: Weak or unreliable solder connections due to insufficient heat or poor wetting. Prevention: Correct soldering temperature profiles and adequate flux activity.
-
Component Misalignment: Components not properly aligned with pads, leading to poor connections or short circuits. Prevention: Accurate pick-and-place machine programming and regular calibration.
-
Tombstoning: Chip components standing on end due to uneven heating or solder wetting. Prevention: Balanced solder paste deposition and proper reflow temperature profile.
-
Insufficient Solder: Weak or open connections due to too little solder. Prevention: Appropriate solder paste volume and stencil aperture design.
-
Lifted Pads: Pads separating from the PCB surface due to mechanical stress or poor adhesion. Prevention: Proper PCB design, gentle handling, and controlled soldering temperatures.
To minimize the occurrence of these defects, it is essential to follow best practices in PCB design, component selection, process control, and quality assurance.
Future Trends in PCB Assembly
As electronic devices continue to evolve, PCB assembly technologies and processes must adapt to meet new challenges. Some future trends in PCB assembly include:
-
Miniaturization: The demand for smaller, more compact devices will drive the adoption of advanced packaging technologies, such as chip-scale packages (CSP) and wafer-level packages (WLP).
-
Flexible and Stretchable Electronics: The growing interest in wearable devices and the Internet of Things (IoT) will require PCB assembly processes that can handle flexible and stretchable substrates.
-
3D Printing: Additive manufacturing techniques, such as 3D printing, may be used to create complex PCB structures and embed components within the board.
-
Automation and Industry 4.0: Increased automation, data analytics, and machine learning will be employed to optimize PCB assembly processes, improve quality control, and reduce costs.
-
Sustainable and Eco-Friendly Practices: There will be a greater emphasis on using environmentally friendly materials, such as lead-free solders and halogen-free PCBs, and implementing sustainable manufacturing practices to reduce waste and energy consumption.
PCB Assembly FAQs
-
Q: What is the difference between PCB fabrication and PCB assembly?
A: PCB fabrication is the process of manufacturing the bare printed circuit board, while PCB assembly involves soldering or mounting electronic components onto the fabricated PCB. -
Q: How long does PCB assembly typically take?
A: The lead time for PCB assembly varies depending on factors such as the complexity of the board, the volume of the order, and the workload of the assembly service provider. Typical lead times range from a few days to several weeks. -
Q: What is the minimum order quantity (MOQ) for PCB assembly?
A: The MOQ for PCB assembly varies among service providers. Some providers may offer low-volume or prototype assembly services with no minimum order quantity, while others may require a minimum order of a few hundred or thousand pieces. -
Q: Can I provide my own components for PCB assembly?
A: Yes, many PCB assembly service providers offer consignment services, where you can supply your own components for assembly. However, you must ensure that the components are properly packaged, labeled, and documented to avoid delays or assembly errors. -
Q: How much does PCB assembly cost?
A: The cost of PCB assembly depends on several factors, such as the complexity of the board, the number of components, the assembly technology (SMT or THT), and the volume of the order. Generally, higher volumes will result in lower per-unit costs due to economies of scale. It is best to request quotes from multiple service providers to compare prices and services.
Conclusion
PCB assembly is a critical process in the manufacturing of electronic devices, transforming bare PCBs into functional electronic assemblies. Understanding the different types of PCB assembly, the assembly process, and the factors affecting assembly quality can help you make informed decisions when designing and manufacturing your electronic products.
Outsourcing PCB assembly to a reputable service provider can offer numerous benefits, such as cost savings, access to expertise, and quality assurance. When selecting a PCB assembly partner, consider their experience, capabilities, quality standards, and customer support.
As electronic devices continue to evolve, PCB assembly technologies and processes must adapt to meet new challenges, such as miniaturization, flexible electronics, and sustainable manufacturing practices.
By staying informed about the latest trends and best practices in PCB assembly, you can ensure that your electronic products are manufactured to the highest standards of quality, reliability, and performance.
Leave a Reply