Introduction to Radar PCB
Radar PCB, or Printed Circuit Board, is a specialized radio frequency (RF) circuit designed for detection and automation applications. It plays a crucial role in various industries, including aerospace, automotive, and security systems. Radar PCB utilizes electromagnetic waves to detect and track objects, measure distances, and enable automated processes.
How Radar PCB Works
Radar PCB operates by transmitting high-frequency electromagnetic waves and receiving the reflected signals from target objects. The basic components of a radar PCB include:
- Transmitter: Generates and amplifies the RF signal to be transmitted.
- Antenna: Radiates the RF signal into the environment and receives the reflected signals.
- Receiver: Processes the received signals and extracts relevant information.
- Signal Processing Unit: Analyzes the processed signals to determine object presence, distance, and other characteristics.
The transmitted RF waves interact with objects in their path, and a portion of the energy is reflected back to the radar PCB. By measuring the time delay between the transmitted and received signals, the radar system can calculate the distance to the object. Additionally, the frequency shift (Doppler effect) of the reflected signal provides information about the object’s velocity.
Applications of Radar PCB
Radar PCB finds applications in various fields, enabling detection, tracking, and automation. Some key applications include:
Automotive Industry
In the automotive industry, radar PCB is used for advanced driver assistance systems (ADAS) and autonomous vehicles. It enables features such as:
- Adaptive Cruise Control (ACC): Maintains a safe distance from the vehicle ahead by adjusting speed automatically.
- Collision Avoidance: Detects potential collisions and alerts the driver or initiates emergency braking.
- Blind Spot Detection: Monitors the vehicle’s blind spots and warns the driver of approaching vehicles.
- Parking Assistance: Helps drivers navigate tight parking spaces by detecting obstacles.
Aerospace and Defense
Radar PCB is extensively used in aerospace and defense applications for surveillance, navigation, and guidance. Some examples include:
- Air Traffic Control: Monitors and controls aircraft movement in the airspace.
- Weather Radar: Detects and tracks weather patterns, helping in weather forecasting and aviation safety.
- Missile Guidance: Provides accurate tracking and guidance for missile systems.
- Terrain Mapping: Creates detailed maps of the earth’s surface for navigation and reconnaissance.
Security Systems
Radar PCB is employed in various security systems for intrusion detection and perimeter monitoring. It offers advantages such as:
- Long-Range Detection: Detects intruders at a distance, providing early warning.
- All-Weather Operation: Functions effectively in various weather conditions, including rain, fog, and snow.
- Automated Alerts: Triggers alarms or notifications when unauthorized activity is detected.
- Integration with Other Sensors: Can be combined with cameras, motion sensors, and access control systems for comprehensive security.
Radar PCB Design Considerations
Designing a radar PCB requires careful consideration of several factors to ensure optimal performance and reliability. Some key design aspects include:
Frequency Selection
The choice of operating frequency depends on the specific application and the desired detection range. Common frequency bands used in radar PCB include:
Frequency Band | Frequency Range | Typical Applications |
---|---|---|
L-band | 1-2 GHz | Long-range surveillance, air traffic control |
S-band | 2-4 GHz | Weather radar, medium-range surveillance |
C-band | 4-8 GHz | Long-range tracking, weather radar |
X-band | 8-12 GHz | Short-range tracking, missile guidance, marine radar |
Ku-band | 12-18 GHz | High-resolution mapping, satellite communications |
K-band | 18-27 GHz | Automotive radar, police speed guns |
Ka-band | 27-40 GHz | Airport surveillance, high-resolution imaging |
Antenna Design
The antenna is a critical component of a radar PCB, as it determines the radiation pattern and directivity of the RF signal. Common antenna types used in radar PCBs include:
- Patch Antenna: Compact, low-profile antennas suitable for small-scale applications.
- Microstrip Antenna: Easily integrated onto PCBs and offers good directivity.
- Horn Antenna: Provides high gain and directivity for long-range applications.
- Phased Array Antenna: Consists of multiple antenna elements that can be electronically steered for beam forming and directional control.
Signal Integrity
Maintaining signal integrity is crucial in radar PCB design to ensure accurate and reliable operation. Key considerations include:
- Impedance Matching: Proper matching of impedances between components to minimize reflections and signal distortion.
- Shielding: Adequate shielding to reduce electromagnetic interference (EMI) and crosstalk between components.
- Grounding: Proper grounding techniques to minimize ground loops and ensure a stable reference plane.
- Trace Routing: Careful routing of high-frequency traces to minimize signal losses and maintain signal integrity.
Power Management
Efficient power management is essential in radar PCB design to ensure stable and reliable operation. Considerations include:
- Voltage Regulation: Appropriate voltage regulators to provide stable power supply to different components.
- Heat Dissipation: Proper thermal management to dissipate heat generated by high-power components.
- Battery Management: Efficient battery management techniques for portable and mobile radar systems.
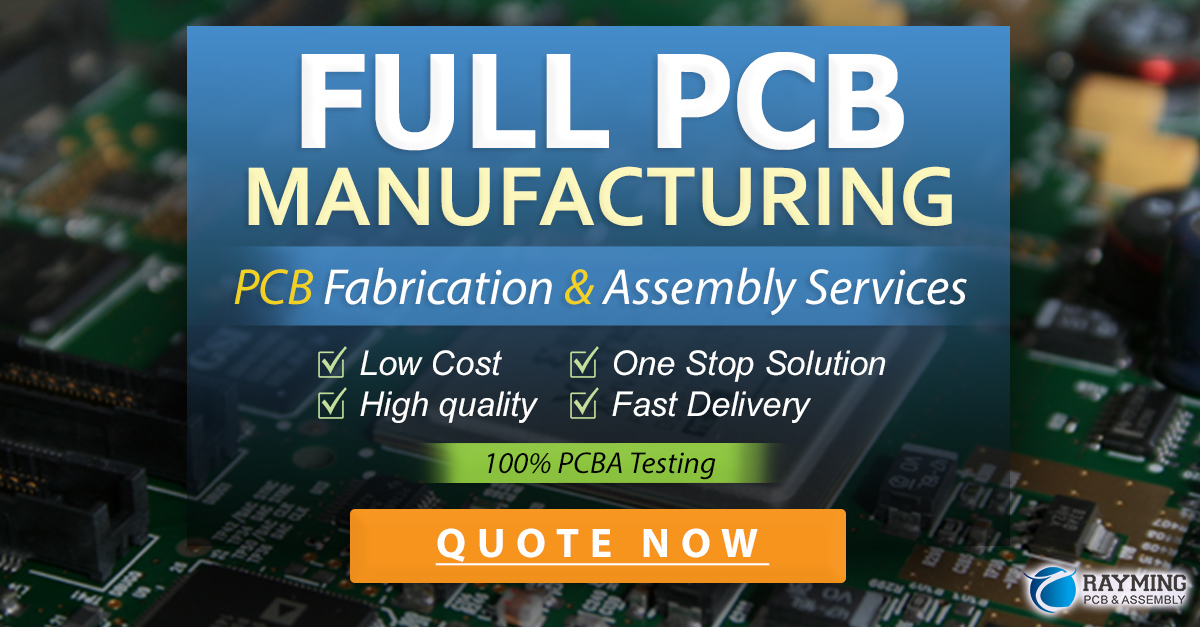
Radar PCB Manufacturing Process
The manufacturing process of a radar PCB involves several steps to ensure high quality and reliability. The typical steps include:
- PCB Design: Creating the schematic and layout of the radar PCB using specialized design software.
- Fabrication: Manufacturing the PCB substrate, copper traces, and vias according to the design specifications.
- Component Placement: Populating the PCB with electronic components using automated pick-and-place machines.
- Soldering: Connecting the components to the PCB using soldering techniques such as reflow soldering or wave soldering.
- Testing and Inspection: Conducting rigorous testing and inspection to verify the functionality, signal integrity, and reliability of the radar PCB.
Quality control measures are implemented throughout the manufacturing process to ensure that the radar PCB meets the required specifications and standards.
Future Trends in Radar PCB Technology
Radar PCB technology continues to evolve, driven by advancements in RF electronics, signal processing, and manufacturing techniques. Some future trends in radar PCB include:
Miniaturization
The demand for smaller and more compact radar systems is driving the miniaturization of radar PCBs. Techniques such as multi-layer PCBs, high-density interconnects (HDI), and advanced packaging methods enable the integration of more functionality in smaller form factors.
Integration with Other Technologies
Radar PCBs are increasingly being integrated with other technologies to enhance their capabilities and applications. For example:
- LiDAR Integration: Combining radar with Light Detection and Ranging (LiDAR) technology for improved object detection and 3D mapping.
- Sensor Fusion: Integrating radar with other sensors like cameras, Ultrasonic Sensors, and inertial measurement units (IMUs) for comprehensive situational awareness.
- Artificial Intelligence (AI): Incorporating AI algorithms for advanced signal processing, object recognition, and decision-making in radar systems.
5G and Beyond
The advent of 5G and future wireless communication technologies will have a significant impact on radar PCB development. Higher bandwidth, lower latency, and increased connectivity will enable new applications and enhance the performance of existing radar systems.
Frequently Asked Questions (FAQ)
- What is the difference between radar and LiDAR?
-
Radar uses radio waves to detect and track objects, while LiDAR uses laser light. Radar has a longer range and can operate in various weather conditions, while LiDAR provides higher resolution and better object recognition capabilities.
-
Can radar PCBs be used for indoor applications?
-
Yes, radar PCBs can be used for indoor applications such as occupancy detection, gesture recognition, and vital sign monitoring. However, the operating frequency and power levels need to be adjusted to comply with indoor regulations and avoid interference with other electronic devices.
-
How does the choice of substrate material affect radar PCB performance?
-
The substrate material’s dielectric constant and loss tangent influence the signal propagation and loss in a radar PCB. Low-loss substrates like Rogers RO4000 series or PTFE-based materials are commonly used for high-frequency radar applications to minimize signal attenuation and ensure consistent performance.
-
What are the challenges in designing and manufacturing radar PCBs?
-
Some challenges include maintaining signal integrity at high frequencies, minimizing EMI and crosstalk, ensuring proper impedance matching, and managing thermal dissipation. Manufacturing challenges include tight tolerances, specialized fabrication processes, and stringent quality control measures.
-
How do I select the appropriate radar PCB for my application?
- Selecting the appropriate radar PCB depends on factors such as the desired detection range, operating frequency, antenna requirements, power consumption, and environmental conditions. It is essential to consult with radar PCB experts or manufacturers to determine the most suitable solution for your specific application.
Conclusion
Radar PCB is a critical component in various detection and automation applications, enabling advanced capabilities in industries such as automotive, aerospace, and security. By leveraging radio frequency technology, radar PCBs provide reliable and efficient object detection, tracking, and measurement.
Designing and manufacturing radar PCBs require careful consideration of factors such as frequency selection, antenna design, signal integrity, and power management. As technology advances, radar PCBs are becoming more miniaturized, integrated with other technologies, and leveraging the benefits of wireless communication advancements.
With their wide range of applications and continued technological advancements, radar PCBs are poised to play an increasingly important role in shaping the future of detection and automation across various domains.
Leave a Reply