What is an Ultrasonic Sensor?
An ultrasonic sensor is an electronic device that emits high-frequency sound waves and measures the time it takes for the waves to bounce back after hitting an object. By calculating the time difference between the emission and reception of the sound waves, the sensor can determine the distance between itself and the object.
Ultrasonic sensors typically operate at frequencies above 20 kHz, which is beyond the range of human hearing. This high frequency allows the sensor to emit short, focused sound pulses that can accurately detect objects at a distance.
How Does an Ultrasonic Sensor Work?
The working principle of an ultrasonic sensor involves the following steps:
-
Transmitting sound waves: The sensor’s transmitter emits a high-frequency sound wave, usually in the range of 40 kHz to 70 kHz.
-
Receiving the echo: When the sound wave hits an object, it bounces back towards the sensor. The sensor’s receiver detects this reflected wave, known as an echo.
-
Measuring the time of flight: The sensor calculates the time it takes for the sound wave to travel from the transmitter to the object and back to the receiver. This time is known as the “time of flight” (TOF).
-
Calculating the distance: Using the TOF and the known speed of sound in the medium (usually air), the sensor calculates the distance between itself and the object using the following formula:
Distance = (Speed of Sound × Time of Flight) / 2
The distance is divided by two because the sound wave travels twice the distance between the sensor and the object (back and forth).
Components of an Ultrasonic Sensor
An ultrasonic sensor consists of the following main components:
-
Transducer: The transducer is responsible for converting electrical energy into sound waves (transmitter) and vice versa (receiver). It usually consists of a piezoelectric material that vibrates when an electrical signal is applied.
-
Oscillator: The oscillator generates the high-frequency electrical signal that drives the transducer to produce sound waves.
-
Amplifier: The amplifier boosts the electrical signal generated by the transducer when it receives the echo, making it easier to process.
-
Microcontroller: The microcontroller is responsible for controlling the sensor’s operation, measuring the TOF, and calculating the distance. It also communicates with external devices to provide the distance information.
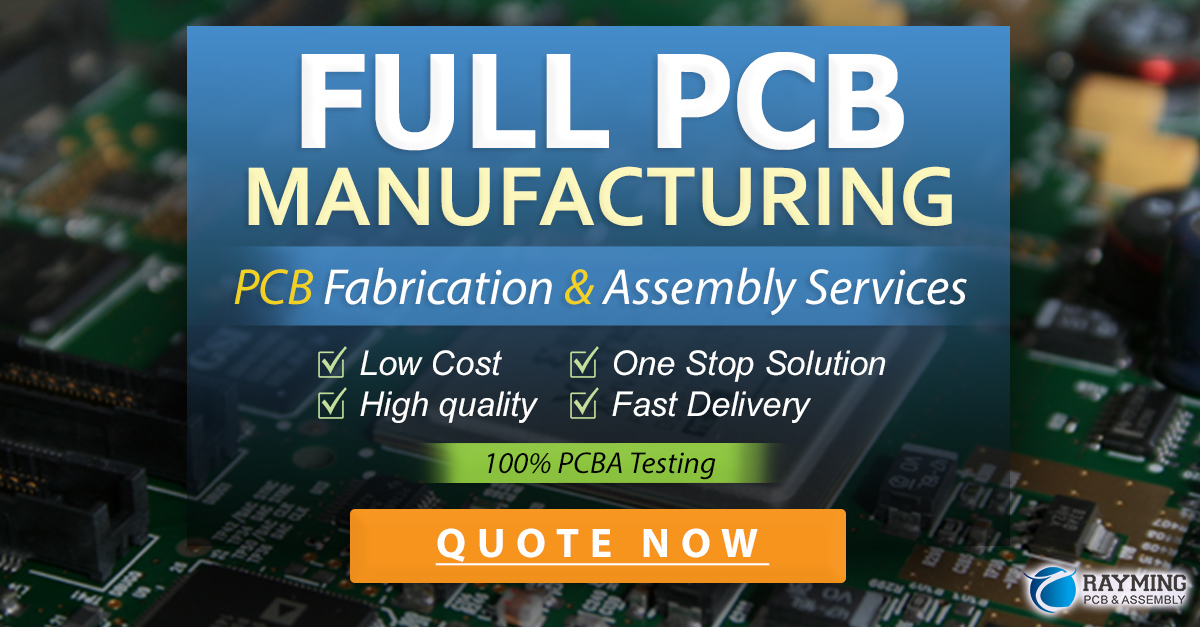
Strengths of Ultrasonic Sensors
Ultrasonic sensors offer several advantages that make them suitable for a wide range of applications:
-
Non-contact measurement: Ultrasonic sensors can measure distances without physical contact with the object, making them ideal for applications where contact is not possible or desirable.
-
Accurate and precise: These sensors provide accurate and precise distance measurements, with typical accuracies ranging from 0.5 mm to 10 mm, depending on the sensor’s specifications and operating conditions.
-
Robust and reliable: Ultrasonic sensors are not affected by factors such as dust, dirt, or moisture, making them suitable for use in harsh environments.
-
Versatile: They can detect objects of various materials, including transparent and reflective surfaces, as long as they have sufficient acoustic reflectivity.
-
Cost-effective: Compared to other distance measurement technologies, such as laser rangefinders, ultrasonic sensors are relatively inexpensive, making them accessible for a wide range of applications.
Weaknesses of Ultrasonic Sensors
Despite their numerous advantages, ultrasonic sensors also have some limitations:
-
Limited range: The maximum detection range of ultrasonic sensors is typically around 10 meters, depending on the sensor’s specifications and the environment. Beyond this range, the signal-to-noise ratio decreases, making it difficult to obtain accurate measurements.
-
Sensitivity to temperature and humidity: The speed of sound in air varies with temperature and humidity, which can affect the accuracy of distance measurements. To compensate for this, some ultrasonic sensors include built-in temperature compensation algorithms.
-
Interference from other ultrasonic sources: In environments with multiple ultrasonic sensors or sources of high-frequency noise, interference can occur, leading to inaccurate measurements or false detections.
-
Difficulty detecting soft or angled surfaces: Ultrasonic sensors may struggle to detect objects with soft, porous, or angled surfaces that absorb or deflect sound waves, resulting in weak or no echoes.
-
Minimum detection distance: Due to the time required for the transducer to switch from transmitting to receiving mode, ultrasonic sensors have a minimum detection distance, typically a few centimeters. Objects closer than this distance may not be detected accurately.
Applications of Ultrasonic Sensors
Ultrasonic sensors find applications in a wide range of industries and products, including:
-
Automotive: In vehicles, ultrasonic sensors are used for parking assistance, collision avoidance, and blind spot detection.
-
Industrial automation: Ultrasonic sensors are employed in manufacturing processes for object detection, level monitoring, and quality control.
-
Robotics: Mobile robots and drones use ultrasonic sensors for obstacle avoidance, navigation, and mapping.
-
Consumer electronics: Devices such as smartphones, tablets, and smart home appliances use ultrasonic sensors for proximity detection and gesture recognition.
-
Medical: Ultrasonic sensors are used in medical equipment for non-invasive diagnostics, such as in ultrasound imaging and blood flow monitoring.
Choosing the Right Ultrasonic Sensor
When selecting an ultrasonic sensor for a specific application, consider the following factors:
-
Range: Determine the minimum and maximum distances you need to measure and choose a sensor with an appropriate detection range.
-
Accuracy and resolution: Consider the required accuracy and resolution for your application. Higher-end sensors typically offer better accuracy and resolution, but at a higher cost.
-
Beam angle: The beam angle determines the sensor’s field of view. A wider beam angle can detect objects over a larger area but may be more prone to interference. A narrower beam angle provides better directional sensitivity but may miss objects not directly in front of the sensor.
-
Operating conditions: Consider the environment in which the sensor will be used, including temperature, humidity, and the presence of dust, dirt, or other contaminants. Choose a sensor that can withstand these conditions.
-
Interface and communication: Ensure that the sensor is compatible with your system’s communication interface, such as analog, digital (I2C, SPI, UART), or CAN bus.
FAQ
-
What is the difference between ultrasonic and infrared sensors?
Ultrasonic sensors use sound waves to detect objects, while infrared sensors use light. Ultrasonic sensors can detect objects of various materials and colors, while infrared sensors may struggle with transparent or reflective surfaces. However, infrared sensors typically have faster response times and can detect objects at greater distances. -
Can ultrasonic sensors detect objects underwater?
Yes, ultrasonic sensors can detect objects underwater because sound waves travel well in liquid media. In fact, they are often used in underwater applications, such as depth measurement and object detection in submarines and boats. -
Do ultrasonic sensors work in a vacuum?
No, ultrasonic sensors do not work in a vacuum because sound waves require a medium (such as air or water) to propagate. In a vacuum, there are no particles to vibrate and transmit the sound waves. -
How do I interface an ultrasonic sensor with a microcontroller?
Most ultrasonic sensors have a simple interface consisting of power (VCC), ground (GND), trigger (TRIG), and echo (ECHO) pins. To interface with a microcontroller, connect VCC and GND to the appropriate power supply, and connect TRIG and ECHO to the microcontroller’s digital I/O pins. Use the microcontroller’s timer or interrupt functions to measure the TOF and calculate the distance. -
Can multiple ultrasonic sensors be used together without interference?
Yes, multiple ultrasonic sensors can be used together, but care must be taken to avoid interference. One common technique is to use a multiplexing scheme, where each sensor is triggered sequentially to avoid overlapping echoes. Another approach is to use sensors with different operating frequencies or to physically separate the sensors to minimize cross-talk.
Conclusion
Ultrasonic sensors are versatile and reliable devices that offer non-contact distance measurement for a wide range of applications. By understanding their working principles, strengths, and weaknesses, engineers and developers can effectively integrate these sensors into their designs and products.
As technology advances, ultrasonic sensors continue to improve in terms of accuracy, range, and miniaturization. With their cost-effectiveness and robustness, these sensors are likely to remain a popular choice for distance measurement in various industries for years to come.
Leave a Reply