Introduction to Flex Circuits
A flex circuit, also known as a flex PCB or flexible printed circuit board, is a type of circuitry made from thin, flexible materials like polyimide. The conductive traces are printed or bonded onto the flexible substrate using materials like copper foil. Flex circuits can be bent, folded and twisted to fit into tight or dynamically moving spaces in all kinds of electronic devices.
Compared to rigid PCBs, flex circuits offer a number of advantages:
- Flexible form factor – can fit into tight spaces and moving parts
- Lightweight and thin profile – reduces weight and space requirements
- Vibration and shock resistance – can withstand dynamic environments
- High reliability – no solder joints to fail from repeated bending
- Scalability – can be designed in high volumes at low cost
Because of these benefits, flex circuits are used for everything from small consumer devices to advanced aerospace systems. They are an enabling technology for the Internet of Things, wearable electronics, robots, UAVs and other applications where flexibility, weight and space savings are critical.
When to Use Quick Turn Flex Circuit Prototypes
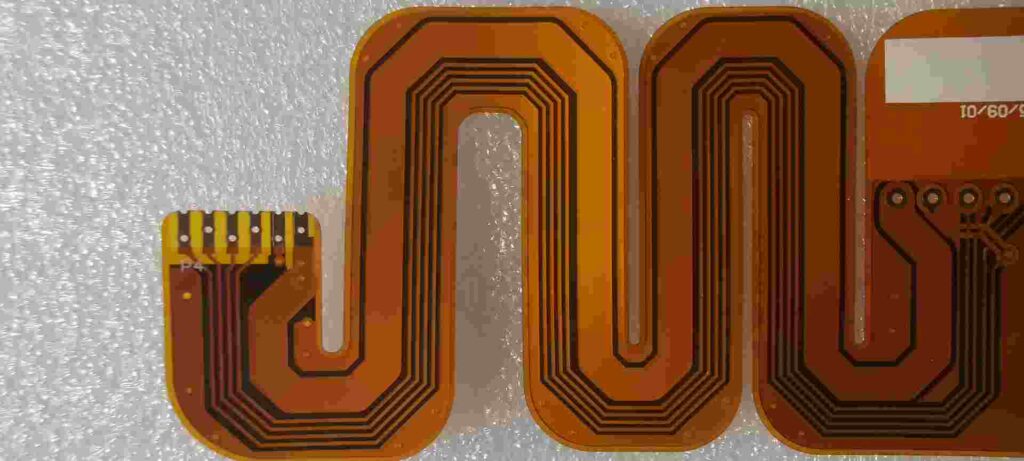
One of the key advantages of flex circuits is the ability to prototype and iterate quickly. Quick turnaround (QTA) flex circuit fabrication services allow you to get prototype flex boards produced in just a few days. This is much faster than the weeks it typically takes for rigid PCB prototyping and fabrication.
Here are some situations where quick turn flex circuits make sense:
- Early stage proof of concept – Test form, fit and function quickly during R&D
- Design validation – Verify layout, components and connections through rapid iterations
- Fast field testing – Get boards in hand quickly for demos, betas and trials
- Accelerated time to market – Develop products faster by prototyping flex designs quickly
- Lower NRE costs – Reduce upfront non-recurring engineering investment
- On demand modifications – Tweak, enhance and customize boards rapidly as needs change
For products where flexibility, weight and space are critical factors, quick turn flex circuits allow you to fail fast and learn quicker. The ability to get prototypes in days rather than weeks helps compress development timelines dramatically.
How to Get Flex Circuit Prototypes Produced Quickly
To leverage quick turn flex PCB capabilities and get your prototypes produced fast, follow these tips:
Choose a Quick Turn Flex Manufacturer
- Select a flex circuit company that offers QTA services and highlights fast turnaround
- Look for domestic facilities with fast shipping times to your location
- Seek out advanced flex material capabilities like polyimide, LCP and metal-backed flex
Provide Complete Design Files
- Submit Gerber files, CAD drawings, assembly files, documentation etc
- Make sure the files are error-free and compatible with latest CAD tools
- Include any special instructions or requirements clear and upfront
Use Simpler Flex Materials
- Standard polyimide flex materials offer the fastest fabrication times
- Avoid specialty dielectric films and adhesives that add lead time
- Skip heavy copper flex layers or metal backing that take longer
Order Modest Quantities
- Start with 5-10 pieces for early prototypes and evolution
- Once the design is stable, go for ~25 pieces for comprehensive testing
- Keep quantities under 50-100 while still verifying performance
Expect Express Delivery
- Leading quick turn houses ship in as fast as 24 hours
- Domestic orders should take 1-3 days to be delivered
- International shipments may take 3-5 days depending on customs
Plan for Multiple Iterations
- Build in expectations for refinements, tweaks and changes
- Budget for at least 2-3 turns while dialing in the optimal design
- Work closely with your flex vendor to expedite re-spins
Following these best practices will help you obtain quality flex circuit prototypes in the shortest possible timeframe. Being able to iteratively test and refine flex designs is the key advantage of rapid prototyping services.
Design Considerations for Quick Turn Flex Circuits
When designing a flex circuit that will utilize quick turn fabrication, there are some important principles to keep in mind:
Simplify the Circuit Geometry
- Minimize intricate bends, folds or complex shapes when possible
- Allow for larger bend radiuses – under 3x substrate thickness absolute minimum
- Enable easy layer-to-layer registration with alignment features or fiducials
Leave Adequate Tolerances
- Specify sufficient tolerances for traces, spaces, features and layers
- Allow for +/- 10% tolerance on critical dimensions as a baseline
- Avoid relying on tight tolerances that push manufacturing limits
Stick to Standard Materials and Features
- Use common flex dielectric films like polyimide instead of LCP or PTFE
- Specify standard 1/1 oz copper instead of thick copper if possible
- Avoid special treatments like sputtered metals, exotic platings or coatings
Provide Complete Documentation
- Note any special handling requirements for moisture sensitivity, ESD, etc
- Clearly specify where flex-to-rigid transitions are required
- Illustrate desired bends, folds and flexing regions in detail
Work Closely With Your Manufacturer!
- Engage technical support experts at your flex vendor
- Heed recommendations from their engineering team
- Be ready to make tweaks or adjustments to ensure manufacturability
Following flex design best practices upfront will ensure your rapid prototypes can be fabricated without issues. Your flex manufacturer wants to help you succeed! Leveraging their expertise will save you time and money.
Key Questions to Ask Your Flex Manufacturer
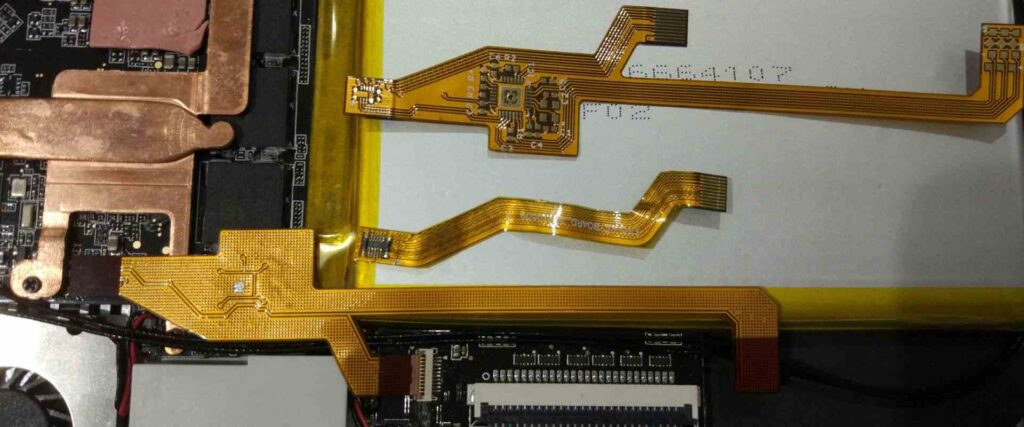
When looking to get quick turn prototypes made, make sure you ask your potential flex circuit vendor the right questions upfront. Here are some key questions to help qualify them:
What is your actual lead time for quick turn fabrication?
- Find out precisely how fast they can deliver flex boards
- Request examples of previous quick turn projects
- Understand the order cut-offs for same day, next day, etc
Which design rules do I need to comply with?
- Ask for their flex design guidelines and rules file
- Review impedance requirements, bend radii, tolerances etc
- Make sure your design falls within their guidelines
What are your quality control procedures?
- Learn about the inspection steps used during quick turns
- Ask about automation vs human inspection
- See what testing and QA is performed to catch defects fast
How do you ensure on-time delivery?
- Find out if they run multiple shifts to enable fast lead times
- Ask about capacity for high priority/emergency orders
- Request examples of previous on-time delivery performance
How can I easily and quickly make design revisions?
- Understand the best ways to submit change orders
- See how soon new designs can be expedited
- Ask about their engineering change process and timelines
Getting responses to these questions upfront will give you confidence in your flex vendor’s capabilities. Partnering with the right manufacturer is crucial for smooth quick turn prototyping.
Conclusion
For products where flexibility and low weight are critical, quick turn flex circuit fabrication enables accelerated design prototyping and validation. The ability to get functional flex boards in just days rather than weeks results in tremendous time and cost savings over the entire product development lifecycle.
By selecting an experienced flex manufacturer, optimizing designs for manufacturability, and working closely with process engineers, innovators can leverage fast flex circuits to fail fast and reach production faster. Quick turnaround flex PCB capabilities provide a distinct competitive advantage for companies looking to gain traction and leadership in emerging flex-based products.
Key Takeaways:
- Quick turn flex circuits allow functional prototypes in days vs weeks
- Ideal for proof of concept, early testing, design validation, and fast iterations
- Choose a capable flex vendor emphasizing fast fabrication and delivery
- Optimize designs for manufacturability – simplify geometry, allow tolerances
- Provide complete design files and documentation – facilitate rapid fabrication
- Work closely with your flex manufacturer and heed recommendations
- Prototype fast and fail early to accelerate overall product development
Frequently Asked Questions
Q: How many layers can you get with quick turn flex circuits?
A: Most rapid flex prototyping services support 1-4 layer flex designs. If you need higher layer count (>6+ layers), lead times get longer.
Q: What are the limitations on minimum trace width and spacing?
A: Typical design rules allow 8 mil trace/space, but you may be able to get down to 5/5 mil for simple layouts. High density interconnects will have longer lead times.
Q: Can stiffeners, covers and other reinforcements be added to quick turn flex boards?
A: Yes, simple stiffeners and covers can be accommodated, but more complex mechanical elements will extend lead times. Keep early prototypes simple.
Q: What testing do you perform on rapid flex prototypes?
A: Most quick turn flex shops do basic electrical testing and inspection. For full ICT and functional testing, expect 1-2 days additional lead time.
Q: How many vias and HDI features can be included on quick turn flex boards?
A: It’s best to limit vias and keep layer transitions simple. For high density interconnects, expect longer lead times or iterative tuning to optimize designs. Work closely with your flex manufacturer.
Leave a Reply