What are Proximity Switches?
Proximity switches, also known as proximity sensors, are devices that detect the presence or absence of an object without physical contact. They operate by emitting an electromagnetic field or beam of electromagnetic radiation and detecting changes in the field or return signal caused by the presence of an object.
Proximity switches come in various types, each with its own unique characteristics and applications. The main types of proximity switches include:
- Inductive Proximity Switches
- Capacitive Proximity Switches
- Photoelectric Proximity Switches
- Ultrasonic Proximity Switches
- Magnetic Proximity Switches
How do Proximity Switches Work?
The working principle of proximity switches varies depending on the type of switch. Let’s explore the operating mechanisms of each type:
Inductive Proximity Switches
Inductive proximity switches detect the presence of metallic objects. They consist of a coil, an oscillator, and a detection circuit. The oscillator generates a high-frequency electromagnetic field around the coil. When a metallic object enters this field, it induces eddy currents in the object, which in turn affects the amplitude of the oscillator. The detection circuit senses these changes and triggers the switch output.
Capacitive Proximity Switches
Capacitive proximity switches detect the presence of both metallic and non-metallic objects. They work on the principle of capacitance change. The switch has a sensing surface that acts as one plate of a capacitor, while the target object acts as the other plate. When an object approaches the sensing surface, it changes the capacitance, which is detected by the switch’s circuitry, triggering the output.
Photoelectric Proximity Switches
Photoelectric proximity switches use light to detect the presence of objects. They consist of an emitter that sends out a beam of light (usually infrared) and a receiver that detects the reflected light. When an object enters the path of the light beam, it reflects the light back to the receiver, triggering the switch output. Photoelectric switches can be further classified into through-beam, retroreflective, and diffuse types based on their configuration.
Ultrasonic Proximity Switches
Ultrasonic proximity switches emit high-frequency sound waves and measure the time it takes for the waves to bounce back from an object. They consist of a transducer that generates the sound waves and a receiver that detects the reflected waves. The switch calculates the distance to the object based on the time delay between the emitted and received signals. Ultrasonic switches can detect both metallic and non-metallic objects and are suitable for applications with transparent or shiny surfaces.
Magnetic Proximity Switches
Magnetic proximity switches detect the presence of magnetic fields or magnetically permeable objects. They consist of a reed switch or a Hall effect sensor. Reed switches contain ferromagnetic contacts that close in the presence of a magnetic field, while Hall effect sensors generate a voltage proportional to the strength of the magnetic field. Magnetic switches are often used in applications involving permanent magnets or electromagnets.
Applications of Proximity Switches
Proximity switches find applications in a wide range of industries and sectors. Some common applications include:
Industry | Application |
---|---|
Automotive | Door and trunk sensing, seat position detection, gear shift position sensing |
Manufacturing | Object detection on conveyor belts, machine guarding, part presence detection |
Packaging | Bottle and can counting, fill level monitoring, cap presence detection |
Robotics | End effector positioning, collision avoidance, gripper presence detection |
Elevators and Lifts | Door safety sensing, leveling detection, call button sensing |
Agriculture | Grain level monitoring, livestock tracking, irrigation control |
Security | Intrusion detection, access control, door and window sensing |
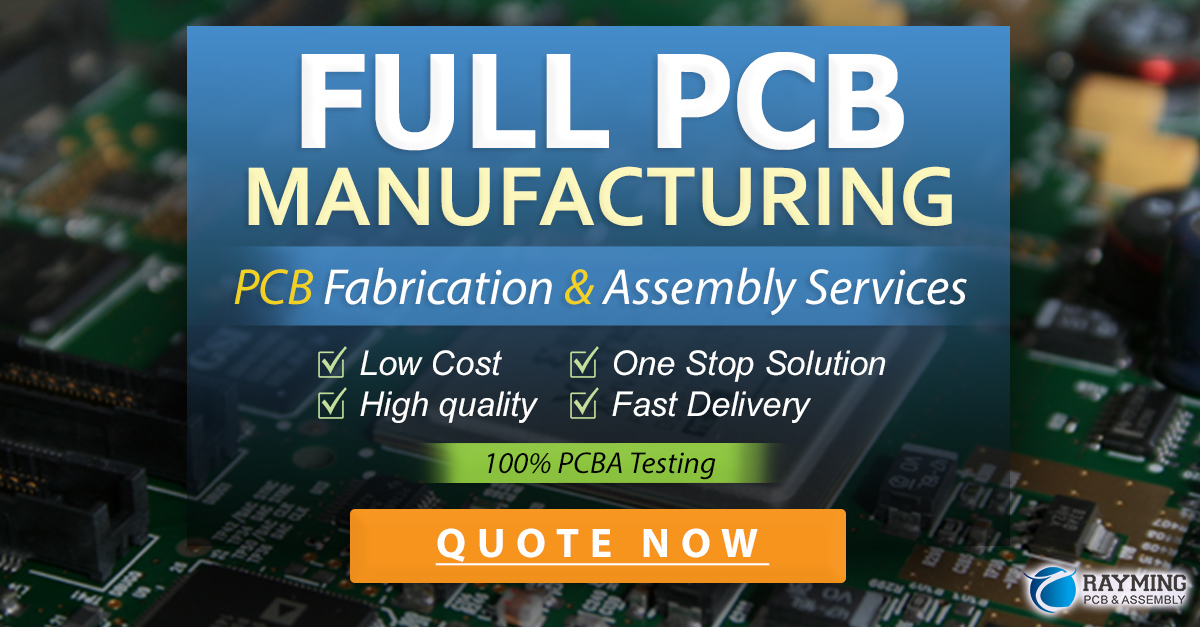
Advantages of Proximity Switches
Proximity switches offer several advantages over traditional mechanical switches:
- Non-contact sensing: Proximity switches detect objects without physical contact, reducing wear and tear and increasing the switch’s lifespan.
- Fast response: Proximity switches have fast response times, making them suitable for high-speed applications.
- Reliability: With no moving parts, proximity switches are less prone to failure and provide reliable operation in harsh environments.
- Versatility: Proximity switches can detect various materials, including metals, plastics, liquids, and granular substances.
- Adjustable sensing range: Many proximity switches allow users to adjust the sensing range to suit specific application requirements.
Selecting the Right Proximity Switch
When choosing a proximity switch for your application, consider the following factors:
- Target material: Select a switch compatible with the material you want to detect (e.g., inductive for metals, capacitive for non-metals).
- Sensing range: Determine the required sensing distance and choose a switch with an appropriate range.
- Environment: Consider the operating environment, including temperature, humidity, dust, and vibrations, and select a switch with suitable environmental ratings (e.g., IP rating).
- Output type: Choose a switch with the desired output type (e.g., NPN, PNP, relay) to interface with your control system.
- Mounting: Consider the available space and mounting options (e.g., flush, non-flush) when selecting a switch.
Installation and Maintenance
Proper installation and maintenance are crucial for the optimal performance and longevity of proximity switches. Follow these guidelines:
- Mounting: Ensure the switch is securely mounted and aligned with the target object. Follow the manufacturer’s recommendations for mounting distances and orientations.
- Wiring: Use the correct wire gauge and follow the wiring diagram provided by the manufacturer. Ensure proper grounding and shielding to prevent electromagnetic interference.
- Adjustment: If the switch has adjustable sensitivity, tune it to achieve the desired sensing range and avoid false triggering.
- Cleaning: Regularly clean the sensing surface to prevent the buildup of dust, dirt, or debris that may affect the switch’s performance.
- Inspection: Periodically inspect the switch for signs of damage, loose connections, or other issues. Replace the switch if necessary.
Troubleshooting
If you encounter problems with your proximity switch, consider the following troubleshooting steps:
- Check the power supply: Ensure the switch is receiving the correct voltage and current.
- Verify the wiring: Double-check the wiring connections and ensure they are secure and properly connected.
- Inspect the sensing surface: Clean the sensing surface and remove any obstructions or debris.
- Adjust the sensitivity: If the switch has adjustable sensitivity, try adjusting it to resolve any sensing issues.
- Check for interference: Ensure there are no sources of electromagnetic interference nearby that may affect the switch’s performance.
Frequently Asked Questions (FAQ)
-
Q: Can proximity switches detect all types of materials?
A: Different types of proximity switches are designed to detect specific materials. Inductive switches detect metals, capacitive switches detect both metals and non-metals, and photoelectric and ultrasonic switches can detect a wide range of materials. -
Q: What is the typical sensing range of a proximity switch?
A: The sensing range varies depending on the type and model of the proximity switch. Inductive switches typically have a range of a few millimeters to several centimeters, while photoelectric and ultrasonic switches can have ranges up to several meters. -
Q: Are proximity switches affected by environmental conditions?
A: Yes, environmental factors such as temperature, humidity, dust, and vibrations can affect the performance of proximity switches. It is important to select a switch with appropriate environmental ratings for your specific application. -
Q: Can proximity switches be used in hazardous environments?
A: Some proximity switches are designed for use in hazardous environments, such as those with explosive atmospheres. These switches have special certifications (e.g., ATEX, IECEx) and are constructed with appropriate protection features. -
Q: How do I interface a proximity switch with my control system?
A: Proximity switches come with various output types, such as NPN, PNP, or relay outputs. Select a switch with an output type compatible with your control system’s input requirements. Follow the manufacturer’s wiring diagrams and specifications for proper interfacing.
Conclusion
Proximity switches are valuable components in numerous industrial applications, providing reliable and efficient non-contact sensing solutions. By understanding the different types of proximity switches, their working principles, and their applications, you can select the most suitable switch for your specific needs.
Remember to consider factors such as target material, sensing range, environment, output type, and mounting when choosing a proximity switch. Proper installation, maintenance, and troubleshooting practices will ensure optimal performance and longevity of your proximity switch.
With this comprehensive guide, you now have a solid foundation of knowledge about proximity switches. Whether you are designing a new system or troubleshooting an existing one, this information will help you make informed decisions and effectively utilize proximity switches in your applications.
Leave a Reply