Introduction to Prepreg and Core in PCB Manufacturing
Printed Circuit Boards (PCBs) are essential components in modern electronics, providing a platform for electrical connections and mechanical support for various components. The manufacturing process of PCBs involves several critical materials, two of which are prepreg and core. Understanding the roles of prepreg and core in PCB manufacturing is crucial for designers, engineers, and manufacturers to ensure the production of high-quality, reliable PCBs.
What is Prepreg?
Prepreg, short for pre-impregnated, is a composite material used in the manufacturing of PCBs. It consists of a fiber reinforcement material, typically glass fiber, pre-impregnated with a partially cured thermoset resin, such as epoxy. The resin is partially cured to a B-stage, which means it is not fully cross-linked and remains in a semi-solid state. This allows the prepreg to be flexible and easy to handle during the PCB manufacturing process.
Types of Prepreg Materials
There are several types of prepreg materials used in PCB manufacturing, each with unique properties and applications:
-
FR-4 Prepreg: The most common type of prepreg, FR-4 is a flame-retardant material made from woven glass fabric impregnated with epoxy resin. It offers excellent mechanical and electrical properties, making it suitable for a wide range of applications.
-
High Tg Prepreg: High glass transition temperature (Tg) prepregs are designed to withstand higher temperatures than standard FR-4 prepregs. They are used in applications that require better thermal stability and reliability, such as automotive and aerospace electronics.
-
Low Dk/Df Prepreg: Low dielectric constant (Dk) and low dissipation factor (Df) prepregs are used in high-speed and high-frequency applications, such as 5G networks and radar systems. These materials minimize signal loss and distortion, ensuring optimal performance.
-
Flexible Prepreg: Flexible prepregs are used in the production of flexible and rigid-flex PCBs. They are made from flexible reinforcement materials, such as polyimide or polyester, impregnated with a flexible resin system.
The Role of Prepreg in PCB Manufacturing
Prepreg plays a crucial role in the PCB manufacturing process:
-
Insulation: Prepreg serves as an insulating layer between the conductive copper layers of a PCB. It prevents short circuits and ensures proper electrical insulation.
-
Bonding: During the lamination process, prepreg acts as an adhesive, bonding the copper layers and core materials together to form a solid, multilayer PCB.
-
Structural support: Prepreg provides mechanical strength and rigidity to the PCB, helping to prevent warping and twisting.
-
Thermal management: The choice of prepreg material can influence the thermal properties of the PCB, such as its ability to dissipate heat and withstand high temperatures.
What is Core?
Core, also known as the substrate or base material, is the foundation of a PCB. It is a rigid, insulating material that provides mechanical support for the copper layers and other components. The core is typically made from a laminate material, such as FR-4, which consists of a woven glass fabric impregnated with a fully cured thermoset resin.
Types of Core Materials
There are several types of core materials used in PCB manufacturing:
-
FR-4 Core: FR-4 is the most common type of core material, offering a balance of good mechanical, electrical, and thermal properties at a reasonable cost. It is suitable for a wide range of applications.
-
High Tg Core: Similar to high Tg prepregs, high Tg core materials are designed to withstand higher temperatures and provide better thermal stability than standard FR-4 cores.
-
Aluminum Core: Aluminum core PCBs (also known as metal core PCBs or MCPCBs) use an aluminum substrate to enhance thermal dissipation. They are used in applications that generate significant heat, such as high-power LED lighting and power electronics.
-
Flexible Core: Flexible core materials, such as polyimide or polyester, are used in the production of flexible and rigid-flex PCBs. They provide the necessary flexibility and durability for applications that require bending or folding.
The Role of Core in PCB Manufacturing
The core material plays several essential roles in the PCB manufacturing process:
-
Structural support: The core provides the primary mechanical structure for the PCB, supporting the copper layers and other components.
-
Insulation: The core material acts as an insulator, preventing short circuits between the conductive layers of the PCB.
-
Thermal management: The choice of core material can significantly impact the thermal performance of the PCB. For example, aluminum cores are used to improve heat dissipation in high-power applications.
-
Dimensional stability: The core material helps maintain the PCB’s dimensional stability during the manufacturing process and throughout its lifecycle, minimizing warping and twisting.
The Relationship Between Prepreg and Core in PCB Manufacturing
Prepreg and core work together to create the final PCB structure. In a typical multilayer PCB, the core materials form the base layers, while the prepreg is used to bond the core layers together and provide insulation between the copper layers.
The Lamination Process
The lamination process is a critical step in PCB manufacturing, where the prepreg and core materials are combined to form a solid, multilayer structure. The process involves the following steps:
-
Layup: The core materials, prepreg sheets, and copper foils are stacked in a specific order, according to the PCB design.
-
Pressing: The stacked layers are placed in a lamination press, where they are subjected to high pressure and temperature. The heat and pressure cause the prepreg to flow and bond the layers together.
-
Curing: During the pressing process, the resin in the prepreg fully cures, creating a strong, permanent bond between the layers.
-
Cooling: After curing, the laminated PCB is cooled to room temperature, and the pressure is released.
The lamination process results in a solid, multilayer PCB with the desired electrical and mechanical properties.
The Importance of Proper Material Selection
Selecting the appropriate prepreg and core materials is essential for ensuring the quality, reliability, and performance of the final PCB. Factors to consider when choosing materials include:
-
Application requirements: The specific requirements of the end application, such as operating temperature, frequency, and environmental conditions, will dictate the choice of materials.
-
Compatibility: The prepreg and core materials must be compatible with each other to ensure proper bonding and performance.
-
Cost: Material cost is an important consideration, especially for high-volume production. However, it should be balanced against the required performance and reliability.
-
Manufacturability: The selected materials should be compatible with the PCB manufacturing process and equipment to ensure efficient and reliable production.
Advancements in Prepreg and Core Materials
As the electronics industry continues to evolve, there is a constant demand for improved prepreg and core materials to meet the challenges of new applications and technologies.
High-Speed Materials
The increasing demand for high-speed and high-frequency applications, such as 5G networks and automotive radar, has driven the development of advanced prepreg and core materials with low dielectric constant (Dk) and low dissipation factor (Df). These materials minimize signal loss and distortion, enabling the design of high-performance PCBs for demanding applications.
Thermally Conductive Materials
The growing power density of modern electronics has led to the development of thermally conductive prepreg and core materials. These materials incorporate fillers, such as ceramic or graphite particles, to enhance thermal conductivity and improve heat dissipation. Thermally conductive materials are particularly important for applications such as high-power LEDs, power electronics, and automotive systems.
Eco-Friendly Materials
As environmental concerns gain prominence, there is a growing interest in eco-friendly prepreg and core materials. These materials aim to reduce the environmental impact of PCB manufacturing by using bio-based resins, recycled reinforcement fibers, and halogen-free flame retardants. Eco-friendly materials offer a more sustainable alternative to traditional PCB materials without compromising performance or reliability.
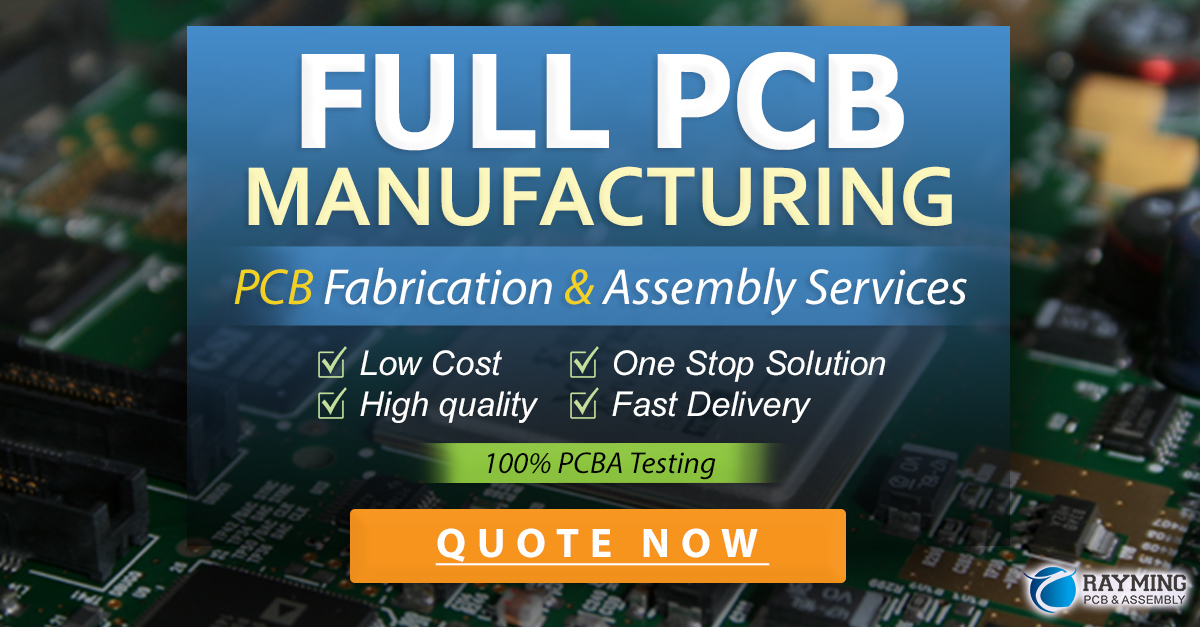
Conclusion
Prepreg and core are two essential materials in the PCB manufacturing process, each playing a critical role in the final product’s performance, reliability, and functionality. Understanding the properties and applications of these materials is crucial for designers, engineers, and manufacturers to make informed decisions and ensure the production of high-quality PCBs.
As the electronics industry continues to advance, the development of new prepreg and core materials will be key to meeting the evolving demands of emerging technologies. By staying informed about the latest material advancements and selecting the most appropriate materials for each application, PCB manufacturers can remain competitive and deliver innovative, high-performance solutions to their customers.
Frequently Asked Questions (FAQ)
- What is the difference between prepreg and core in PCB manufacturing?
Prepreg is a composite material consisting of a fiber reinforcement pre-impregnated with a partially cured resin, while core is the rigid, insulating base material that provides mechanical support for the PCB. Prepreg is used to bond the core layers together and provide insulation between copper layers, while the core forms the foundation of the PCB.
- Can I use different types of prepreg and core materials in the same PCB?
Yes, it is possible to use different types of prepreg and core materials in the same PCB, depending on the specific requirements of the application. For example, a PCB may use a standard FR-4 core for the base layers and a low Dk/Df prepreg for the high-speed signal layers. However, it is essential to ensure that the selected materials are compatible with each other and the manufacturing process.
- How do I select the right prepreg and core materials for my PCB?
When selecting prepreg and core materials, consider the following factors:
– Application requirements (operating temperature, frequency, environmental conditions)
– Compatibility between materials
– Cost and manufacturability
– Specific properties, such as thermal conductivity or eco-friendliness
Consult with your PCB manufacturer or material supplier for guidance on selecting the most appropriate materials for your specific application.
- What is the role of the lamination process in PCB manufacturing?
The lamination process is a critical step in PCB manufacturing where the prepreg and core materials are combined under high pressure and temperature to form a solid, multilayer structure. During lamination, the prepreg flows and bonds the layers together, while the resin fully cures to create a strong, permanent bond.
- How do advancements in prepreg and core materials benefit the electronics industry?
Advancements in prepreg and core materials enable the development of high-performance PCBs for increasingly demanding applications. For example, high-speed materials with low Dk/Df values enable the design of PCBs for 5G networks and automotive radar, while thermally conductive materials improve heat dissipation in high-power applications. Eco-friendly materials offer a more sustainable alternative to traditional PCB materials, reducing the environmental impact of electronics manufacturing.
Material Type | Description | Applications |
---|---|---|
FR-4 Prepreg | Flame-retardant, glass fabric reinforced epoxy resin | General-purpose PCBs |
High Tg Prepreg | Designed for higher operating temperatures | Automotive, aerospace, and high-reliability applications |
Low Dk/Df Prepreg | Low dielectric constant and dissipation factor | High-speed and high-frequency applications (5G, radar) |
Flexible Prepreg | Made from flexible reinforcement materials and resins | Flexible and rigid-flex PCBs |
FR-4 Core | Flame-retardant, glass fabric reinforced epoxy laminate | General-purpose PCBs |
High Tg Core | Designed for higher operating temperatures | Automotive, aerospace, and high-reliability applications |
Aluminum Core | Aluminum substrate for enhanced thermal dissipation | High-power LEDs, power electronics |
Flexible Core | Made from flexible materials (polyimide, polyester) | Flexible and rigid-flex PCBs |
Leave a Reply