Introduction to Pick-and-place Machines
Pick-and-place machines are automated systems that are used to pick up components from a source location and place them in a specific destination. These machines are widely used in various industries, including electronics manufacturing, automotive, food and beverage, and pharmaceuticals. The primary purpose of using pick-and-place machines is to increase production efficiency, accuracy, and consistency while reducing labor costs and human error.
Types of Pick-and-Place Machines
There are several types of pick-and-place machines available in the market, each designed to cater to specific applications and requirements. Some of the common types include:
- Gantry Pick-and-Place Machines: These machines feature a gantry system that moves the pick-and-place head along the X, Y, and Z axes, allowing for precise placement of components.
- Delta Pick-and-Place Machines: These machines use a parallel robot configuration with three arms connected to a common base, providing high-speed operation and accuracy.
- Cartesian Pick-and-Place Machines: These machines use a Cartesian coordinate system to move the pick-and-place head, offering a simple and cost-effective solution for less demanding applications.
- SCARA Pick-and-Place Machines: These machines feature a Selective Compliance Assembly Robot Arm (SCARA) that provides high-speed, high-precision placement of components.
Placer Camera-Assisted Manual Pick and Place Machines
Placer camera-assisted manual pick and place machines are a specific type of pick-and-place system that combines the benefits of manual operation with the precision of machine vision technology. These machines are designed to assist human operators in accurately placing components on a substrate, such as a printed circuit board (PCB), by providing visual guidance through a camera system.
Key Components of a Placer Camera-Assisted Manual Pick and Place Machine
A typical placer camera-assisted manual pick and place machine consists of the following key components:
- Camera System: A high-resolution camera mounted above the work area captures images of the components and the substrate. The camera is often equipped with zoom and autofocus capabilities to ensure clear and detailed images.
- Illumination System: Proper lighting is essential for accurate image capture and processing. The illumination system typically includes LED lights that provide uniform and adjustable lighting conditions.
- Image Processing Software: The captured images are processed by specialized software that analyzes the features and positions of the components and the substrate. The software generates visual guides and instructions for the operator to follow during the placement process.
- Manual Placement Tool: The operator uses a manual placement tool, such as tweezers or a vacuum pen, to pick up the components and place them on the substrate following the visual guides provided by the machine.
- Work Table: The work table is the surface on which the substrate is placed during the assembly process. It may include fixtures or jigs to hold the substrate in place and ensure accurate alignment.
Benefits of Using Placer Camera-Assisted Manual Pick and Place Machines
Placer camera-assisted manual pick and place machines offer several advantages over traditional manual assembly methods:
- Increased Accuracy: The machine vision system provides precise visual guides, ensuring that components are placed accurately on the substrate. This reduces the risk of misalignment and improves the overall quality of the assembled product.
- Faster Assembly: By providing clear visual instructions, the machine helps operators place components more quickly and efficiently. This results in higher throughput and reduced assembly times.
- Reduced Training Time: The visual guides provided by the machine make it easier for operators to learn and perform the assembly process, reducing the time and cost associated with training new employees.
- Flexibility: Manual pick and place machines can handle a wide variety of components and substrates, making them suitable for low-volume, high-mix production scenarios. They can also be easily reconfigured to accommodate changes in product design or assembly requirements.
- Cost-Effective: Compared to fully automated pick-and-place systems, placer camera-assisted manual machines offer a more affordable solution for small to medium-sized businesses or those with limited production volumes.
Applications of Placer Camera-Assisted Manual Pick and Place Machines
Placer camera-assisted manual pick and place machines find applications in various industries and products, including:
- Electronics Assembly: These machines are commonly used in the assembly of printed circuit boards (PCBs), especially for prototyping, low-volume production, or rework processes. They can handle a wide range of electronic components, such as resistors, capacitors, integrated circuits (ICs), and connectors.
- Medical Device Assembly: In the medical device industry, placer camera-assisted manual machines are used to assemble small, delicate components with high precision. This includes the assembly of medical sensors, implantable devices, and diagnostic equipment.
- Automotive Components: These machines are used in the assembly of small automotive components, such as sensors, switches, and connectors. They help ensure accurate placement and alignment of these components, which is critical for proper functioning and reliability.
- Consumer Products: Placer camera-assisted manual machines are also used in the assembly of various consumer products, such as toys, appliances, and electronic gadgets. They enable efficient and precise assembly of small components, enhancing product quality and consistency.
Factors to Consider When Choosing a Placer Camera-Assisted Manual Pick and Place Machine
When selecting a placer camera-assisted manual pick and place machine for your application, consider the following factors:
- Component Size and Complexity: Ensure that the machine can handle the size and complexity of the components you need to assemble. Consider the minimum and maximum component sizes, as well as any specific features or shapes that may require special handling.
- Substrate Compatibility: Verify that the machine is compatible with the substrates you will be using, such as PCBs, flex circuits, or other materials. Consider the size, thickness, and any special requirements of your substrates.
- Camera Resolution and Precision: Look for a machine with a high-resolution camera system that can provide clear and detailed images of the components and substrate. Higher resolution and precision will result in more accurate placement and better overall quality.
- Illumination System: Ensure that the machine has an adjustable and uniform illumination system that can provide optimal lighting conditions for your specific components and substrates. Good lighting is essential for accurate image capture and processing.
- Software Features: Evaluate the image processing software provided with the machine. Look for features such as real-time image analysis, visual guidance, and user-friendly interfaces that can help operators work efficiently and accurately.
- Ergonomics and Operator Comfort: Consider the ergonomics of the machine, including the work table height, placement tool design, and overall ease of use. A comfortable and ergonomic setup can help reduce operator fatigue and improve productivity.
- Scalability and Upgradability: If you anticipate future growth or changes in your production requirements, choose a machine that can be easily scaled up or upgraded. This may include the ability to add additional cameras, upgrade software, or integrate with other automation systems.
- Training and Support: Look for a manufacturer that provides comprehensive training and support services to help you get the most out of your placer camera-assisted manual pick and place machine. This may include on-site training, online resources, and technical support.
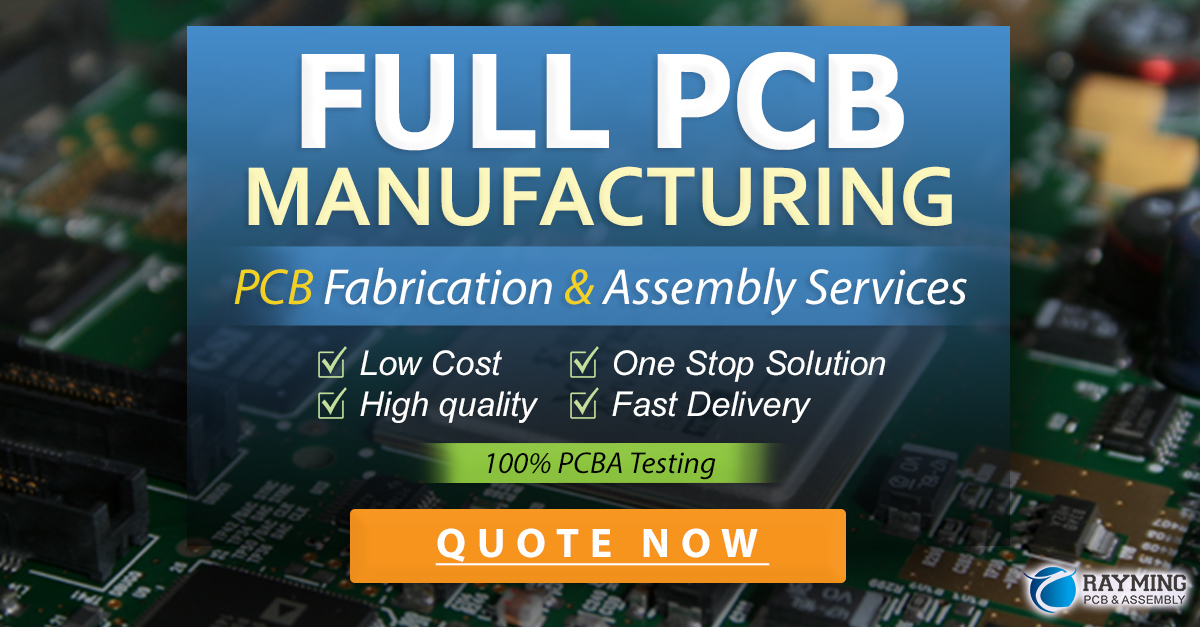
Best Practices for Using Placer Camera-Assisted Manual Pick and Place Machines
To ensure optimal performance and results from your placer camera-assisted manual pick and place machine, follow these best practices:
- Operator Training: Provide thorough training to operators on how to use the machine effectively, including how to interpret visual guides, handle components, and maintain proper ergonomics.
- Component Organization: Keep components organized and easily accessible to operators. Use trays, bins, or feeders that are compatible with the machine and the components being assembled.
- Substrate Preparation: Ensure that substrates are clean, free from debris, and properly aligned before beginning the assembly process. Use fixtures or jigs to secure the substrate and maintain consistent positioning.
- Lighting Optimization: Adjust the illumination system to provide optimal lighting conditions for your specific components and substrates. Uniform and consistent lighting is crucial for accurate image capture and processing.
- Regular Calibration: Perform regular calibration of the camera system to maintain accuracy and precision. Follow the manufacturer’s recommended calibration procedures and frequency.
- Maintenance and Cleaning: Regularly clean and maintain the machine, including the camera lens, illumination system, and placement tools. Follow the manufacturer’s guidelines for proper maintenance to ensure long-term performance and reliability.
- Quality Control: Implement quality control measures to verify the accuracy and consistency of the assembled products. This may include visual inspections, electrical testing, or other methods to ensure that components are placed correctly and the final product meets specifications.
- Continuous Improvement: Monitor the performance of the machine and the operators, and seek opportunities for continuous improvement. This may involve updating software, optimizing processes, or providing additional training to operators.
Frequently Asked Questions (FAQ)
- What is a placer camera-assisted manual pick and place machine?
A placer camera-assisted manual pick and place machine is a system that combines manual placement of components with machine vision technology to provide visual guidance and improve accuracy. - How does a placer camera-assisted manual pick and place machine work?
The machine uses a high-resolution camera to capture images of the components and substrate. The image processing software analyzes these images and generates visual guides for the operator to follow when placing components manually. - What are the benefits of using a placer camera-assisted manual pick and place machine?
The benefits include increased accuracy, faster assembly, reduced training time, flexibility, and cost-effectiveness compared to fully automated systems. - What industries use placer camera-assisted manual pick and place machines?
These machines are used in various industries, including electronics assembly, medical device assembly, automotive components, and consumer products. - How can I ensure optimal performance from my placer camera-assisted manual pick and place machine?
To ensure optimal performance, provide thorough operator training, keep components organized, prepare substrates properly, optimize lighting, perform regular calibration and maintenance, implement quality control measures, and continuously seek opportunities for improvement.
Conclusion
Placer camera-assisted manual pick and place machines offer a valuable solution for businesses looking to improve the accuracy and efficiency of their assembly processes without investing in fully automated systems. By combining the flexibility of manual placement with the precision of machine vision technology, these machines enable operators to work more efficiently and accurately, resulting in higher-quality products and increased productivity.
When selecting a placer camera-assisted manual pick and place machine, consider factors such as component compatibility, camera resolution, software features, ergonomics, and scalability. Implementing best practices for operator training, component organization, substrate preparation, lighting optimization, and maintenance can help ensure optimal performance and long-term success.
As technology continues to advance, placer camera-assisted manual pick and place machines are likely to become increasingly sophisticated, offering even greater accuracy, speed, and ease of use. By investing in these machines and staying up-to-date with the latest developments, businesses can remain competitive and meet the evolving demands of their customers and markets.
Leave a Reply