What is PCB Warpage?
PCB warpage refers to the deviation of a PCB from its intended flat shape. It is a type of dimensional instability that occurs when the board experiences uneven thermal expansion or contraction during the manufacturing process or under certain environmental conditions. The warpage can be classified into different types based on the direction and severity of the deformation.
Types of PCB Warpage
- Bow warpage: The PCB curves along its length, forming a bow-like shape.
- Twist warpage: The PCB twists along its diagonal axis, resulting in a twisted appearance.
- Cup warpage: The PCB curves along both its length and width, forming a cup-like shape.
- Saddle warpage: The PCB curves along its length in opposite directions, resembling a saddle shape.
The severity of warpage is typically measured in mils (thousandths of an inch) or millimeters, and the acceptable level of warpage depends on the specific application and the components used on the board.
Causes of PCB Warpage
Several factors can contribute to the development of PCB warpage, including:
Thermal Stress
One of the primary causes of PCB warpage is thermal stress. During the manufacturing process, the PCB undergoes multiple heating and cooling cycles, such as during soldering and reflow. If the thermal expansion coefficients of the materials used in the PCB (e.g., copper, fiberglass, and solder mask) are not well-matched, uneven expansion and contraction can occur, leading to warpage.
Moisture Absorption
PCBs are often exposed to humidity during storage and transportation. The materials used in PCBs, particularly the substrate (e.g., FR-4), can absorb moisture from the environment. When the board is subjected to high temperatures during soldering or reflow, the absorbed moisture evaporates rapidly, causing localized swelling and warpage.
Unbalanced Copper Distribution
An uneven distribution of copper on the PCB can also contribute to warpage. If one side of the board has significantly more copper than the other, the difference in thermal expansion can cause the board to warp. This is particularly common in designs with large copper planes or heavy copper pours.
Mechanical Stress
Mechanical stress during handling, assembly, or use can also lead to PCB warpage. Improper handling during manufacturing, such as excessive bending or twisting, can permanently deform the board. Additionally, the mounting of heavy components or the application of excessive pressure during assembly can cause localized warpage.
Effects of PCB Warpage
PCB warpage can have several detrimental effects on the performance and reliability of electronic devices:
Component Misalignment
Warped PCBs can cause component misalignment during the assembly process. Surface-mount components, such as chips and connectors, require precise placement on the board. If the board is warped, the components may not align properly with their designated pads, leading to poor soldering and potential connectivity issues.
Soldering Difficulties
Warpage can also create challenges during the soldering process. If the board is not flat, it may not make proper contact with the soldering iron or the solder paste, resulting in incomplete or weak solder joints. This can lead to intermittent connections, increased resistance, and a higher risk of failure.
Stress on Components
A warped PCB can exert uneven stress on the mounted components. As the board deforms, it can cause the components to bend or twist, potentially damaging their internal structure or breaking their leads. This stress can also accelerate the aging process of the components, reducing their lifespan and increasing the likelihood of premature failure.
Mechanical Interference
In some cases, PCB warpage can cause mechanical interference with other parts of the device. If the warped board comes into contact with the casing or other components, it can lead to shorts, damage, or even complete device failure. This is particularly problematic in compact devices where clearances are tight.
Reduced Reliability
The cumulative effects of component misalignment, soldering issues, and mechanical stress can significantly reduce the overall reliability of the electronic device. Warped PCBs are more prone to failures, both during the manufacturing process and in the field, leading to increased costs associated with repairs, replacements, and customer dissatisfaction.
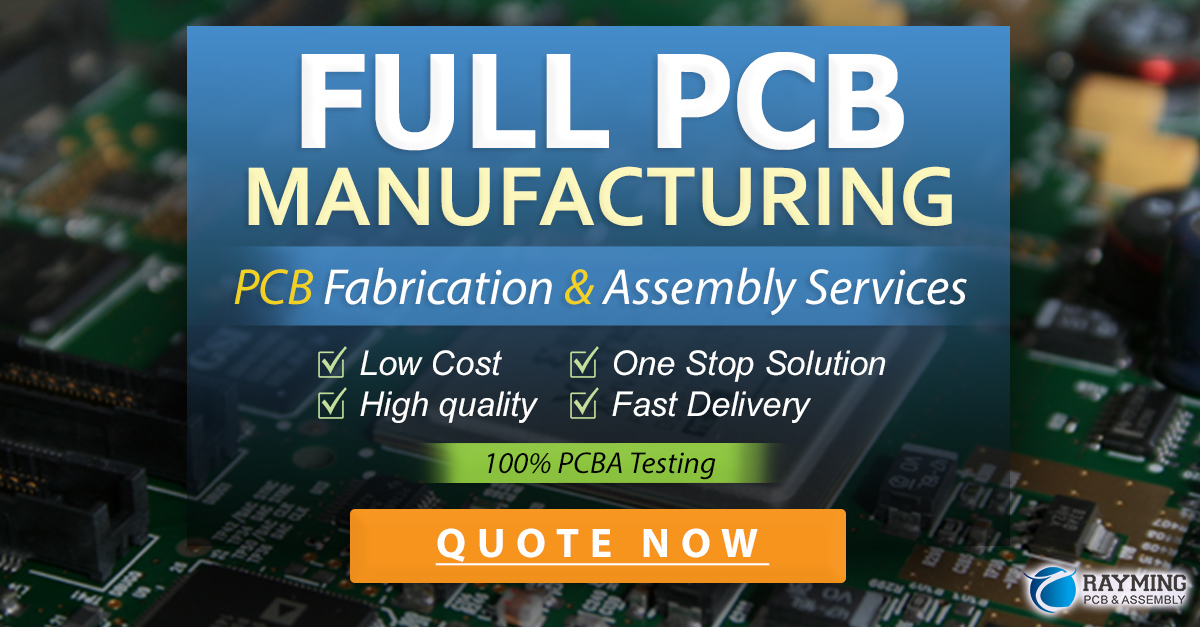
Prevention and Mitigation Strategies
To minimize the occurrence and impact of PCB warpage, several prevention and mitigation strategies can be employed:
Material Selection
Choosing materials with similar thermal expansion coefficients can help reduce the likelihood of warpage. For example, using a substrate material with a coefficient of thermal expansion (CTE) that closely matches that of copper can minimize thermal stress. Additionally, selecting materials with low moisture absorption properties can help prevent warpage due to humidity.
Balanced Copper Distribution
Designing the PCB with a balanced copper distribution across all layers can help prevent warpage caused by uneven thermal expansion. This can be achieved by using symmetrical copper pours, minimizing large copper planes, and distributing copper evenly on both sides of the board.
Proper Handling and Storage
Implementing proper handling and storage procedures can help minimize mechanical stress and moisture absorption. PCBs should be stored in a dry, temperature-controlled environment and handled with care during manufacturing and assembly. Using ESD-safe packaging materials and avoiding excessive bending or twisting of the boards can also help prevent warpage.
Moisture Management
To combat moisture-related warpage, several techniques can be employed. Baking the PCBs prior to soldering or reflow can help remove absorbed moisture, reducing the risk of warpage during high-temperature processes. Additionally, using moisture-sensitive device (MSD) packaging and following proper storage and handling guidelines can help minimize moisture absorption.
Design Optimization
Optimizing the PCB design can also help reduce the risk of warpage. This may involve adjusting the placement of components, using stiffeners or support structures, or incorporating stress-relief features such as slotted or routed areas. Conducting thorough warpage simulations and analysis during the design phase can help identify and address potential warpage issues before manufacturing.
Process Control
Strict process control during manufacturing can help minimize warpage. This includes maintaining consistent temperature profiles during soldering and reflow, using appropriate soldering techniques, and implementing quality control measures to detect and address warpage issues promptly. Regular calibration and maintenance of manufacturing equipment can also help ensure consistent results.
FAQ
-
What is the main cause of PCB warpage?
The main cause of PCB warpage is thermal stress, which occurs when the materials used in the PCB have different coefficients of thermal expansion and experience uneven expansion or contraction during temperature changes. -
Can PCB warpage be completely eliminated?
While it may not be possible to completely eliminate PCB warpage, it can be minimized through proper material selection, balanced copper distribution, design optimization, and strict process control during manufacturing. -
How does moisture affect PCB warpage?
Moisture absorbed by the PCB materials, particularly the substrate, can cause localized swelling and warpage when the board is subjected to high temperatures during soldering or reflow. The rapid evaporation of the absorbed moisture leads to uneven expansion and deformation. -
What are the consequences of PCB warpage?
PCB warpage can lead to component misalignment, soldering difficulties, stress on components, mechanical interference, and reduced overall reliability of the electronic device. These issues can result in increased costs, device failures, and customer dissatisfaction. -
How can PCB warpage be mitigated during the design phase?
During the design phase, PCB warpage can be mitigated by selecting materials with similar thermal expansion coefficients, ensuring a balanced copper distribution, optimizing component placement, using stiffeners or support structures, and conducting thorough warpage simulations and analysis to identify and address potential issues.
PCB Warpage Type | Description |
---|---|
Bow | The PCB curves along its length, forming a bow-like shape |
Twist | The PCB twists along its diagonal axis, resulting in a twisted appearance |
Cup | The PCB curves along both its length and width, forming a cup-like shape |
Saddle | The PCB curves along its length in opposite directions, resembling a saddle shape |
In conclusion, PCB warpage is a complex issue that requires careful consideration throughout the design, manufacturing, and handling processes. By understanding the causes, effects, and prevention strategies, electronics manufacturers can minimize the occurrence and impact of PCB warpage, leading to more reliable and cost-effective electronic devices.
Leave a Reply