Introduction to PCB Trace Width
Printed Circuit Board (PCB) trace width refers to the width of the copper tracks or traces on a PCB that carry electrical signals between components. Determining the appropriate trace width is crucial for ensuring proper current carrying capacity, minimizing voltage drop, controlling impedance, and maintaining signal integrity in PCB designs.
Factors Affecting PCB Trace Width
Several factors influence the calculation of PCB trace width:
1. Current carrying capacity
2. Allowable temperature rise
3. Copper thickness (weight)
4. Trace length
5. Ambient temperature
6. Number of copper layers
7. Via size and placement
Understanding PCB Trace Width Calculators
A PCB trace width calculator is a tool that helps designers determine the appropriate width of PCB traces based on various input parameters. These calculators take into account factors such as current, copper thickness, temperature rise, and trace length to provide accurate trace width recommendations.
Types of PCB Trace Width Calculators
There are two main types of PCB trace width calculators:
-
Online Calculators: Web-based tools that allow users to input parameters and obtain trace width results instantly.
-
Standalone Software: Dedicated PCB design software often includes built-in trace width calculators as part of their feature set.
Benefits of Using a PCB Trace Width Calculator
Using a PCB trace width calculator offers several advantages:
-
Accuracy: Calculators provide precise trace width values based on industry-standard formulas and guidelines.
-
Time-saving: Designers can quickly determine appropriate trace widths without manual calculations.
-
Consistency: Calculators ensure consistent results across different projects and design teams.
-
Optimization: Proper trace width selection helps optimize PCB performance, reliability, and manufacturability.
How to Use a PCB Trace Width Calculator
Using a PCB trace width calculator involves the following steps:
-
Gathering Input Parameters: Collect the necessary information such as current, copper thickness, temperature rise, and trace length.
-
Accessing the Calculator: Open the online calculator or launch the PCB design software with the built-in calculator.
-
Entering Input Values: Input the gathered parameters into the designated fields of the calculator.
-
Selecting Units: Choose the appropriate units for each parameter (e.g., amps, mils, °C).
-
Calculating Trace Width: Click the “Calculate” button or equivalent to obtain the recommended trace width.
-
Interpreting Results: The calculator will display the minimum trace width required to meet the specified criteria.
Example Calculation
Let’s walk through an example calculation using a PCB trace width calculator:
Input Parameters:
– Current: 1 A
– Copper Thickness: 1 oz (1.4 mils)
– Temperature Rise: 10 °C
– Trace Length: 100 mm
After entering these values into the calculator, the recommended minimum trace width is found to be 0.5 mm (19.7 mils).
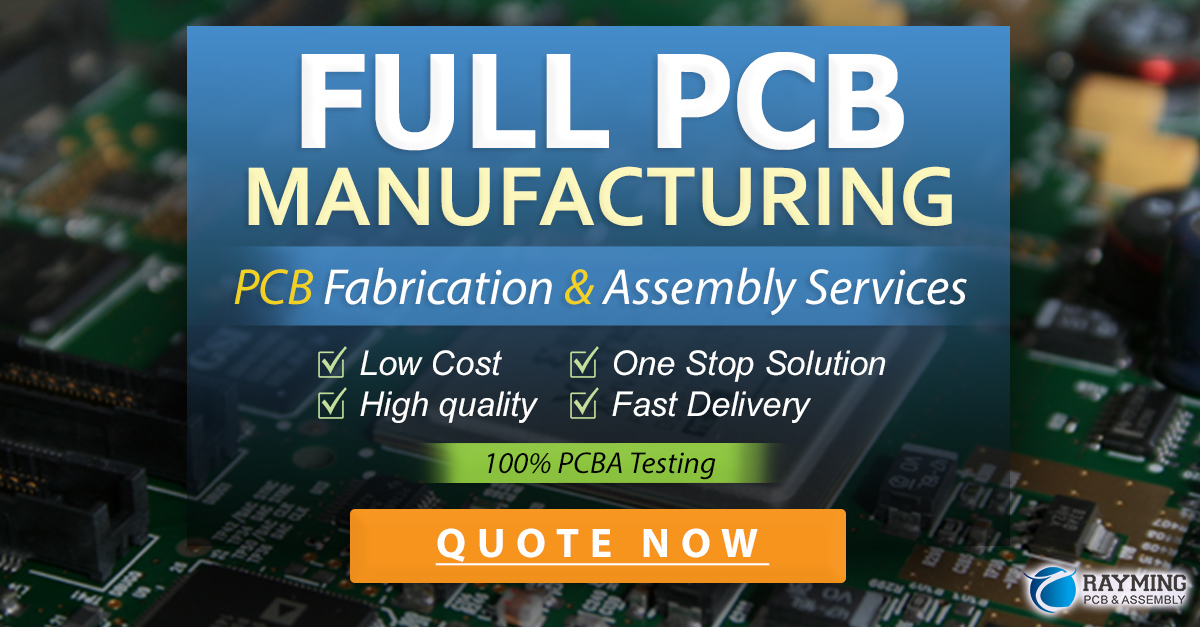
PCB Trace Width Design Guidelines
When designing PCB traces, consider the following guidelines:
-
Current Capacity: Ensure traces can handle the expected current without excessive heating.
-
Voltage Drop: Minimize voltage drop along traces to maintain signal integrity.
-
Impedance Control: Match trace impedance to the characteristic impedance of connected components.
-
Clearance and Spacing: Maintain appropriate clearance between traces and components to avoid short circuits and signal interference.
-
Manufacturing Constraints: Consider the limitations of the PCB manufacturing process, such as minimum trace width and spacing.
IPC-2221 Standards for PCB Trace Width
The IPC-2221 standard provides guidelines for determining PCB trace widths based on current, temperature rise, and copper thickness. Here is a summary table of IPC-2221 recommendations:
Copper Thickness (oz) | Trace Width (mils) | Current Capacity (A) |
---|---|---|
0.5 | 10 | 0.5 |
1 | 20 | 1.0 |
2 | 40 | 2.0 |
3 | 60 | 3.0 |
Note: The above values are for a temperature rise of 10 °C and a trace length of 100 mm.
Advanced PCB Trace Width Considerations
In addition to the basic trace width calculation, designers should consider the following advanced factors:
High-Speed Signals
For high-speed signals, trace width plays a critical role in maintaining signal integrity. Factors such as impedance matching, crosstalk, and reflections become more significant at higher frequencies. Designers should use appropriate trace width and spacing to control impedance and minimize signal distortion.
Power Traces
Power traces require special attention due to their higher current carrying requirements. Wider traces are necessary to handle the increased current flow without excessive voltage drop or heating. Additionally, proper via placement and sizing are crucial for distributing power effectively across the PCB.
Thermal Management
PCB trace width affects the thermal performance of the board. Wider traces have lower resistance and can dissipate heat more effectively. However, designers must strike a balance between trace width and available board space. Thermal simulations can help optimize trace widths for optimal heat dissipation.
Frequently Asked Questions (FAQ)
-
What happens if PCB traces are too narrow?
If PCB traces are too narrow, they may not have sufficient current carrying capacity, leading to excessive heating and potential damage to the traces or connected components. Narrow traces can also result in higher voltage drop and signal integrity issues. -
Can I use different trace widths for different sections of a trace?
Yes, it is possible to use different trace widths for different sections of a trace. This is known as necking down or tapering. It allows designers to optimize trace widths based on the current requirements of specific sections while conserving board space. However, proper design rules must be followed to ensure smooth transitions and avoid signal reflections. -
How does copper thickness affect PCB trace width?
Copper thickness, typically expressed in ounces (oz), directly affects the current carrying capacity of PCB traces. Thicker copper allows for higher current flow and enables the use of narrower traces. The standard copper thicknesses are 0.5 oz, 1 oz, 2 oz, and 3 oz, with 1 oz being the most common. -
What is the minimum trace width that can be manufactured?
The minimum trace width that can be manufactured depends on the capabilities of the PCB fabrication process. Most PCB manufacturers can reliably produce trace widths down to 0.1 mm (4 mils). However, for high-density designs or advanced manufacturing processes, trace widths as small as 0.075 mm (3 mils) or even 0.05 mm (2 mils) can be achieved. -
How do I determine the appropriate trace width for my PCB design?
To determine the appropriate trace width for your PCB design, follow these steps: - Identify the maximum current expected to flow through each trace.
- Consider the copper thickness of your PCB.
- Determine the acceptable temperature rise and trace length.
- Use a PCB trace width calculator or refer to IPC-2221 guidelines to find the recommended minimum trace width based on your input parameters.
- Verify that the calculated trace width meets your PCB manufacturing capabilities and design constraints.
Conclusion
PCB trace width calculation is a critical aspect of PCB design that ensures proper current carrying capacity, signal integrity, and overall performance. By using a PCB trace width calculator and following industry guidelines, designers can determine the appropriate trace widths for their specific requirements.
Remember to consider factors such as current, copper thickness, temperature rise, and trace length when calculating trace widths. Additionally, keep in mind advanced considerations like high-speed signals, power traces, and thermal management.
By understanding and applying PCB trace width calculations effectively, designers can create reliable, efficient, and manufacturable PCB designs that meet the demands of modern electronics.
Leave a Reply