The Evolution of PCB Technology
PCBs have come a long way since their invention in the early 20th century. The first PCBs were simple, single-sided boards with through-hole components. As electronics became more complex and miniaturized, PCBs evolved to accommodate these changes. The introduction of double-sided boards, multi-layer boards, and surface-mount technology (SMT) allowed for higher component density and improved performance.
Era | PCB Technology | Key Features |
---|---|---|
1900s-1950s | Through-hole technology | Simple, single-sided boards |
1960s-1970s | Double-sided boards | Increased component density |
1980s-1990s | Multi-layer boards | Higher complexity, improved signal integrity |
2000s-present | Advanced materials and manufacturing | High-density interconnect (HDI), embedded components, flexible and rigid-flex PCBs |
Recent PCB Advancements
High-Density Interconnect (HDI) PCBs
HDI PCBs are characterized by their fine line widths, small vias, and high component density. These boards enable the creation of compact, high-performance electronics for applications such as smartphones, wearables, and IoT devices. HDI PCBs use advanced manufacturing techniques like microvias, buried vias, and sequential lamination to achieve their high density and reliability.
Embedded Components
Embedded components take PCB miniaturization to the next level by integrating passive components like resistors and capacitors within the PCB substrate itself. This approach saves space on the board surface, reduces the number of solder joints, and improves overall reliability. Embedded components are particularly useful in applications where size and weight are critical, such as aerospace and medical devices.
Flexible and Rigid-Flex PCBs
Flexible PCBs use thin, flexible substrates that can bend and conform to various shapes. These boards are ideal for applications that require flexibility, such as wearables, medical implants, and aerospace systems. Rigid-flex PCBs combine the benefits of both rigid and flexible boards, allowing for complex, three-dimensional designs that can fit into tight spaces and withstand harsh environments.
Advanced Materials
PCB manufacturers are continually exploring new materials to improve the performance, reliability, and environmental friendliness of their products. Some recent advancements include:
- High-temperature materials for automotive and aerospace applications
- Low-loss materials for high-frequency RF and microwave applications
- Halogen-free and lead-free materials for eco-friendly PCBs
- Thermally conductive materials for improved heat dissipation
The Future of PCB Technology
As electronics continue to evolve, so too will PCB technology. Some of the key trends and developments we can expect to see in the coming years include:
5G and Beyond
The rollout of 5G networks and the development of future wireless technologies will drive demand for high-frequency, low-loss PCBs. These boards will need to support higher data rates, lower latencies, and more complex antenna designs. PCB manufacturers will need to invest in advanced materials and manufacturing processes to meet these challenges.
Artificial Intelligence and Edge Computing
The growth of artificial intelligence (AI) and edge computing will require PCBs that can handle high-performance processing, memory, and storage in compact form factors. These boards will need to be highly integrated, energy-efficient, and capable of operating in harsh environments. Embedded components and advanced packaging technologies will play a key role in enabling these applications.
Sustainability and Circular Economy
As environmental concerns continue to grow, PCB manufacturers will need to focus on developing more sustainable and eco-friendly products. This will involve the use of recyclable and biodegradable materials, as well as the adoption of circular economy principles like design for disassembly and reuse. Governments and industry organizations are already setting standards and regulations to drive this transition.
Industry 4.0 and Smart Manufacturing
The fourth industrial revolution, or Industry 4.0, is transforming the way PCBs are designed and manufactured. Smart factories equipped with advanced automation, robotics, and data analytics are enabling faster, more flexible, and more efficient production. PCB designers are also leveraging artificial intelligence and machine learning to optimize layouts, predict failures, and improve overall quality.
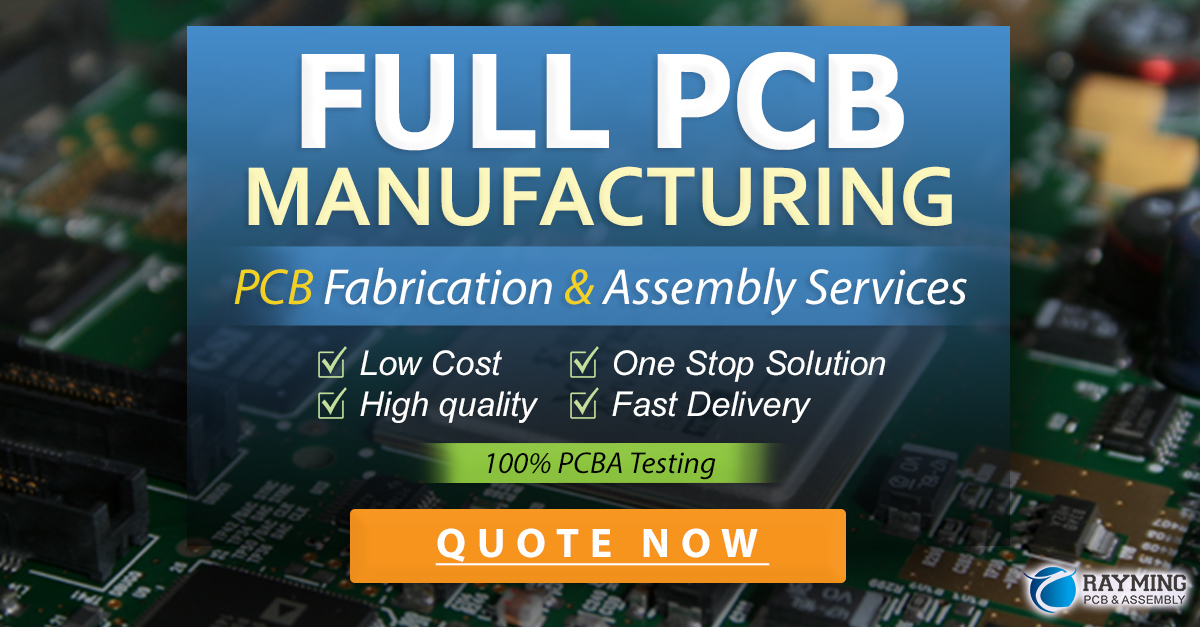
Frequently Asked Questions (FAQ)
-
What is the difference between HDI and traditional PCBs?
HDI PCBs have finer line widths, smaller vias, and higher component density compared to traditional PCBs. This allows for more compact and high-performance designs, but also requires more advanced manufacturing processes. -
Are embedded components more expensive than surface-mounted components?
Embedded components can be more expensive initially due to the specialized manufacturing processes required. However, they can offer cost savings in the long run by reducing board size, simplifying assembly, and improving reliability. -
What are the benefits of using flexible PCBs?
Flexible PCBs offer several benefits, including the ability to conform to complex shapes, improved resistance to vibration and shock, and reduced weight and size compared to rigid boards. They are ideal for applications that require flexibility or need to fit into tight spaces. -
How are PCB manufacturers addressing environmental concerns?
PCB manufacturers are adopting various strategies to improve sustainability, such as using eco-friendly materials, implementing lead-free and halogen-free manufacturing processes, and designing boards for easier recycling and reuse. Many are also working to reduce energy consumption and waste in their operations. -
What role will artificial intelligence play in the future of PCB design and manufacturing?
Artificial intelligence and machine learning are expected to play a significant role in the future of PCB design and manufacturing. These technologies can help optimize board layouts, predict potential failures, and improve overall quality. They can also enable more flexible and efficient production in smart factories equipped with advanced automation and robotics.
Conclusion
PCB technology has come a long way since its inception, and it continues to evolve at a rapid pace. Recent advancements like HDI, embedded components, flexible and rigid-flex boards, and advanced materials are enabling the creation of more complex, compact, and high-performance electronics. As we look to the future, trends like 5G, artificial intelligence, sustainability, and Industry 4.0 are set to shape the next generation of PCBs.
To stay competitive in this dynamic landscape, PCB manufacturers and designers will need to invest in research and development, adopt new technologies and processes, and collaborate closely with their customers and partners. By embracing innovation and adapting to change, the PCB industry can continue to play a vital role in driving technological progress and improving our daily lives.
Leave a Reply