What is a PCB Substrate?
A PCB (Printed Circuit Board) substrate is the foundation material upon which the electronic components and conductive traces are placed. It provides mechanical support and electrical insulation for the components and interconnections. The substrate is a critical component of a PCB, as its properties directly impact the performance, reliability, and manufacturability of the final product.
Types of PCB Substrates
There are several types of PCB substrates available, each with its own unique properties and characteristics. The most common types include:
- FR-4 (Flame Retardant 4)
- Polyimide
- Teflon
- Ceramic
- Metal Core
FR-4 (Flame Retardant 4)
FR-4 is the most widely used PCB substrate material. It is a composite material made of woven fiberglass cloth with an epoxy resin binder. FR-4 offers excellent mechanical strength, good electrical insulation properties, and is flame retardant. It is suitable for a wide range of applications, from consumer electronics to industrial equipment.
Property | Value |
---|---|
Dielectric Constant | 4.5 |
Dissipation Factor | 0.02 |
Thermal Conductivity | 0.3 W/mK |
Glass Transition Temperature | 130°C |
Polyimide
Polyimide is a high-performance polymer substrate material known for its excellent thermal stability, chemical resistance, and mechanical strength. It is often used in applications that require operation at high temperatures or exposure to harsh environments, such as aerospace and military electronics.
Property | Value |
---|---|
Dielectric Constant | 3.5 |
Dissipation Factor | 0.002 |
Thermal Conductivity | 0.2 W/mK |
Glass Transition Temperature | 360°C |
Teflon
Teflon, or PTFE (Polytetrafluoroethylene), is a low-loss substrate material with excellent dielectric properties. It is often used in high-frequency applications, such as radar systems and wireless communications, due to its low dielectric constant and dissipation factor.
Property | Value |
---|---|
Dielectric Constant | 2.1 |
Dissipation Factor | 0.0002 |
Thermal Conductivity | 0.25 W/mK |
Glass Transition Temperature | 327°C |
Ceramic
Ceramic substrates, such as alumina (Al2O3) and aluminum nitride (AlN), offer excellent thermal conductivity, high mechanical strength, and good electrical insulation properties. They are often used in high-power applications, such as power electronics and LED lighting, where efficient heat dissipation is crucial.
Property | Alumina (Al2O3) | Aluminum Nitride (AlN) |
---|---|---|
Dielectric Constant | 9.8 | 8.8 |
Dissipation Factor | 0.0001 | 0.0005 |
Thermal Conductivity | 24 W/mK | 170 W/mK |
Flexural Strength | 380 MPa | 320 MPa |
Metal Core
Metal core substrates, such as aluminum and copper, are used in applications that require excellent thermal management. The metal core provides a low-resistance thermal path for heat dissipation, while a thin dielectric layer on top of the metal core provides electrical insulation for the components and traces.
Property | Aluminum | Copper |
---|---|---|
Thermal Conductivity | 205 W/mK | 385 W/mK |
Coefficient of Thermal Expansion (CTE) | 23 ppm/°C | 17 ppm/°C |
Density | 2.7 g/cm³ | 8.9 g/cm³ |
Substrate Selection Criteria
When selecting a PCB substrate, several factors must be considered to ensure optimal performance and reliability:
- Electrical Properties
- Dielectric Constant
- Dissipation Factor
- Dielectric Strength
-
Surface Resistivity
-
Thermal Properties
- Thermal Conductivity
- Glass Transition Temperature (Tg)
-
Coefficient of Thermal Expansion (CTE)
-
Mechanical Properties
- Flexural Strength
- Tensile Strength
- Young’s Modulus
-
Dimensional Stability
-
Environmental Factors
- Operating Temperature Range
- Humidity Resistance
- Chemical Resistance
-
Flammability Rating
-
Manufacturing Considerations
- Ease of Processing
- Drilling and Routing Characteristics
- Availability and Cost
Electrical Properties
The electrical properties of a substrate determine its ability to insulate and support the conductive traces and components. The dielectric constant and dissipation factor are crucial parameters that affect signal integrity and high-frequency performance. A lower dielectric constant results in lower capacitance and faster signal propagation, while a lower dissipation factor minimizes signal loss and heat generation.
Thermal Properties
Thermal management is a critical aspect of PCB design, particularly in high-power applications. The thermal conductivity of the substrate determines its ability to dissipate heat away from components, while the glass transition temperature (Tg) sets the maximum operating temperature limit. The coefficient of thermal expansion (CTE) should be closely matched to that of the components to minimize stress and prevent failures due to thermal cycling.
Mechanical Properties
The mechanical properties of a substrate determine its ability to withstand physical stress and maintain dimensional stability. Flexural strength, tensile strength, and Young’s modulus are important parameters that affect the durability and reliability of the PCB. Dimensional stability is crucial for maintaining the alignment of components and traces, particularly in high-density designs.
Environmental Factors
PCBs are often exposed to various environmental conditions during operation, such as extreme temperatures, humidity, and chemical exposure. The substrate must be selected to withstand these conditions without degradation or loss of performance. Flammability ratings, such as UL94, are also important for ensuring safety in applications where fire hazards are a concern.
Manufacturing Considerations
The manufacturability of a PCB is directly influenced by the substrate material. Some substrates, such as FR-4, are easy to process and readily available, while others, such as ceramic, may require specialized equipment and expertise. Drilling and routing characteristics, such as the ease of machining and the minimum achievable feature sizes, also vary between substrate materials. Cost and availability are additional factors to consider when selecting a substrate for a specific application.
PCB Substrate Manufacturing Process
The manufacturing process for PCB substrates typically involves the following steps:
- Raw Material Preparation
- Mixing and blending of resin and reinforcement materials
-
Casting or sheet forming of the substrate material
-
Lamination
- Stacking of substrate layers and copper foils
-
Pressing under heat and pressure to bond the layers together
-
Drilling
-
Creation of through-holes and vias using mechanical or laser drilling
-
Plating
- Electroless copper deposition to create a conductive layer on the hole walls
-
Electrolytic copper plating to increase the thickness of the conductive layer
-
Patterning
- Application of photoresist and exposure to create the desired circuit pattern
-
Etching of the unwanted copper to form the conductive traces
-
Surface Finishing
- Application of protective coatings, such as solder mask and silkscreen
-
Plating of contact pads with materials such as gold, silver, or tin
-
Cutting and Singulation
- Separation of individual PCBs from the panel using routing or punching
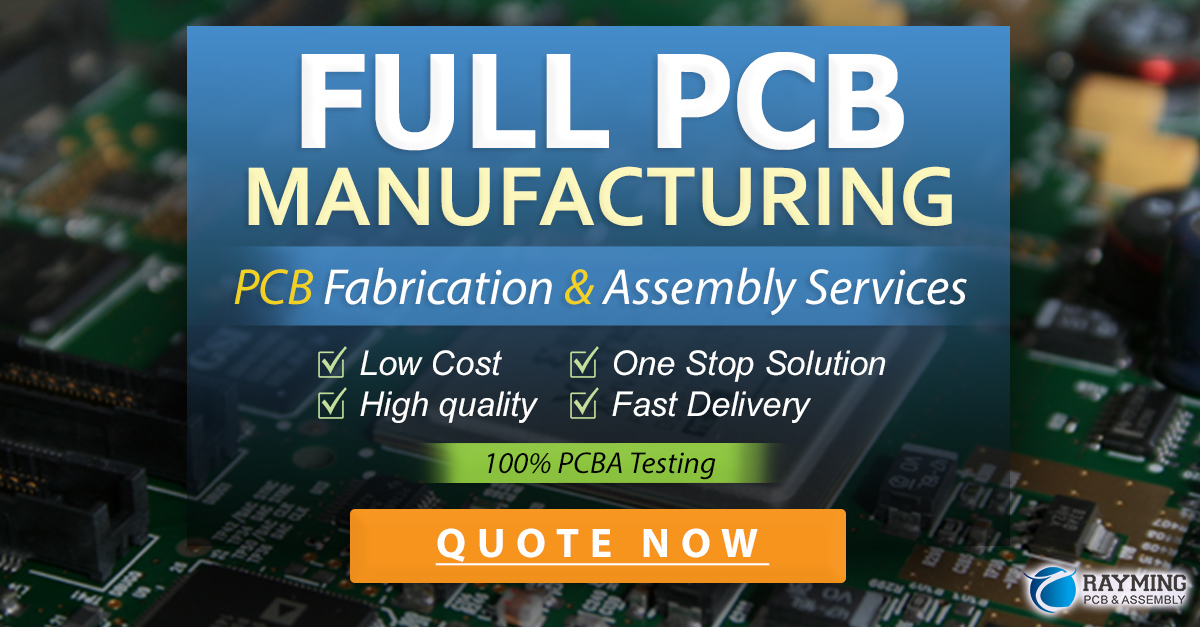
Advanced PCB Substrate Technologies
As the demand for higher performance and smaller form factors continues to grow, several advanced PCB substrate technologies have emerged:
- High-Frequency Laminates
- Low-loss substrates designed for high-frequency applications, such as 5G and millimeter-wave communications
-
Examples include Rogers RO4000 series, Isola I-Tera MT40, and Panasonic Megtron 7
-
Embedded Components
- Integration of passive components, such as resistors and capacitors, within the substrate material
-
Reduces component footprint and improves signal integrity
-
3D Printing
- Additive manufacturing techniques for creating complex PCB structures and shapes
-
Enables rapid prototyping and customization
-
Flexible and Stretchable Substrates
- Substrates that can bend, flex, or stretch without damage
-
Used in wearable electronics, medical devices, and flexible displays
-
Thermally Conductive Substrates
- Substrates with high thermal conductivity for improved heat dissipation
- Examples include ceramic, metal core, and carbon fiber composites
Frequently Asked Questions (FAQ)
- What is the most common PCB substrate material?
-
FR-4 (Flame Retardant 4) is the most widely used PCB substrate material due to its good balance of mechanical, electrical, and thermal properties, as well as its cost-effectiveness and ease of processing.
-
How does the dielectric constant of a substrate affect PCB performance?
-
A lower dielectric constant results in lower capacitance and faster signal propagation, which is particularly important for high-frequency applications. It also helps to reduce crosstalk and signal distortion.
-
What are the advantages of using a metal core substrate?
-
Metal core substrates, such as aluminum and copper, offer excellent thermal conductivity, which helps to dissipate heat away from components more efficiently. This is particularly important in high-power applications, such as power electronics and LED lighting.
-
How do I select the right substrate material for my application?
-
When selecting a substrate material, consider the electrical, thermal, mechanical, and environmental requirements of your application. Factors such as dielectric constant, thermal conductivity, flexural strength, operating temperature range, and chemical resistance should be evaluated against the available substrate options. Manufacturing considerations, such as ease of processing, availability, and cost, should also be taken into account.
-
What are some emerging trends in PCB substrate technology?
- Advanced PCB substrate technologies include high-frequency laminates for 5G and millimeter-wave applications, embedded components for reduced footprint and improved signal integrity, 3D printing for complex structures and rapid prototyping, flexible and stretchable substrates for wearable electronics and medical devices, and thermally conductive substrates for enhanced heat dissipation.
Conclusion
PCB substrates play a critical role in the performance, reliability, and manufacturability of electronic devices. Understanding the properties and characteristics of different substrate materials is essential for selecting the right option for a given application. Factors such as electrical properties, thermal management, mechanical strength, environmental resistance, and manufacturing considerations must be carefully evaluated to ensure optimal results.
As technology continues to advance, new substrate materials and manufacturing techniques are emerging to meet the ever-increasing demands for higher performance, smaller form factors, and greater functionality. By staying informed about the latest developments in PCB substrate technology, designers and engineers can create innovative and reliable electronic products that push the boundaries of what is possible.
Leave a Reply