Factors to Consider When Choosing PCB Substrate Materials
Before diving into the specific types of PCB substrate materials, it’s essential to understand the key factors that influence substrate selection. These factors include:
-
Dielectric Constant (Dk): The dielectric constant measures the substrate’s ability to store electrical energy. A lower Dk value indicates better signal integrity and higher frequency performance.
-
Dissipation Factor (Df): The dissipation factor represents the substrate’s ability to dissipate electrical energy as heat. A lower Df value means less energy loss and better signal quality.
-
Thermal Conductivity: Thermal conductivity determines how efficiently the substrate can transfer heat away from components. Higher thermal conductivity is desirable for applications with high power dissipation.
-
Coefficient of Thermal Expansion (CTE): CTE measures the substrate’s expansion or contraction with temperature changes. A closely matched CTE between the substrate and components reduces stress and improves reliability.
-
Mechanical Strength: The substrate must have sufficient mechanical strength to withstand the stresses of manufacturing, assembly, and operation.
-
Cost: The cost of the substrate material is an important consideration, especially for high-volume production or cost-sensitive applications.
Common PCB Substrate Materials
FR-4
FR-4 (Flame Retardant 4) is the most widely used PCB substrate material. It is a composite material made of woven fiberglass cloth impregnated with an epoxy resin. FR-4 offers a good balance of electrical, mechanical, and thermal properties at a relatively low cost.
Advantages:
– Good dielectric properties (Dk ~4.5, Df ~0.02)
– Excellent mechanical strength and durability
– Flame retardant
– Wide availability and low cost
Disadvantages:
– Limited high-frequency performance
– Moderate thermal conductivity
– Higher CTE compared to some other materials
Applications: FR-4 is suitable for a wide range of general-purpose electronic applications, including consumer electronics, industrial controls, and telecommunications equipment.
High Tg FR-4
High Tg (Glass Transition Temperature) FR-4 is a variant of standard FR-4 with improved thermal stability. It uses a modified epoxy resin that can withstand higher temperatures without softening or deforming.
Advantages:
– Higher glass transition temperature (typically 170°C or higher)
– Improved thermal stability and reliability
– Reduced warpage and delamination
Disadvantages:
– Slightly higher cost compared to standard FR-4
– Similar electrical and mechanical properties to standard FR-4
Applications: High Tg FR-4 is commonly used in automotive electronics, aerospace systems, and other applications that require enhanced thermal stability.
Rogers Materials (RO4000, RO3000, etc.)
Rogers materials are a family of high-performance laminate substrates designed for demanding RF and microwave applications. They offer excellent dielectric properties, low loss, and controlled impedance.
Advantages:
– Low dielectric constant and dissipation factor
– Excellent high-frequency performance
– Stable dielectric properties over temperature and frequency
– Low CTE for improved reliability
Disadvantages:
– Higher cost compared to FR-4
– Reduced mechanical strength and durability
– Limited availability and longer lead times
Applications: Rogers materials are widely used in wireless communications, radar systems, satellite equipment, and high-speed digital applications.
Polyimide
Polyimide is a high-temperature, chemically resistant polymer substrate material. It offers excellent thermal stability, mechanical strength, and flexibility.
Advantages:
– High glass transition temperature (typically 250°C or higher)
– Excellent thermal stability and chemical resistance
– Good mechanical strength and flexibility
– Low dielectric constant and dissipation factor
Disadvantages:
– Higher cost compared to FR-4
– Challenging to process and fabricate
– Reduced adhesion to copper compared to epoxy-based materials
Applications: Polyimide is commonly used in aerospace, military, and high-temperature applications, as well as in flexible and rigid-flex PCBs.
PTFE (Teflon)
PTFE (Polytetrafluoroethylene), also known as Teflon, is a low-loss, high-frequency substrate material. It offers excellent dielectric properties and thermal stability.
Advantages:
– Very low dielectric constant and dissipation factor
– Excellent high-frequency performance
– High thermal stability and chemical resistance
– Low moisture absorption
Disadvantages:
– High cost compared to other substrate materials
– Difficult to process and fabricate
– Poor mechanical strength and dimensional stability
Applications: PTFE is primarily used in high-frequency RF and microwave applications, such as antenna systems, radar equipment, and satellite communications.
Ceramic
Ceramic substrates, such as alumina (Al2O3) and aluminum nitride (AlN), are used in high-performance, high-reliability applications. They offer excellent thermal conductivity, low dielectric loss, and high mechanical strength.
Advantages:
– High thermal conductivity
– Low dielectric constant and dissipation factor
– Excellent mechanical strength and stability
– High temperature resistance
Disadvantages:
– High cost compared to organic substrates
– Brittle and prone to cracking
– Limited design flexibility and manufacturing complexity
Applications: Ceramic substrates are commonly used in power electronics, high-temperature applications, and RF modules that require efficient heat dissipation.
Comparison of PCB Substrate Materials
The following table provides a comparison of the key properties of the discussed PCB substrate materials:
Material | Dk | Df | Tg (°C) | Thermal Conductivity (W/mK) | CTE (ppm/°C) |
---|---|---|---|---|---|
FR-4 | ~4.5 | ~0.02 | 130-140 | 0.3-0.4 | 14-16 |
High Tg FR-4 | ~4.5 | ~0.02 | 170-180 | 0.3-0.4 | 14-16 |
Rogers RO4000 | 3.3-3.7 | 0.0027-0.0037 | >280 | 0.6-0.7 | 11-16 |
Polyimide | 3.2-3.5 | 0.002-0.003 | >250 | 0.2-0.3 | 12-20 |
PTFE | 2.0-2.1 | 0.0002-0.0009 | >260 | 0.2-0.3 | 60-100 |
Alumina (96%) | 9.4 | 0.0004 | N/A | 24-28 | 6-8 |
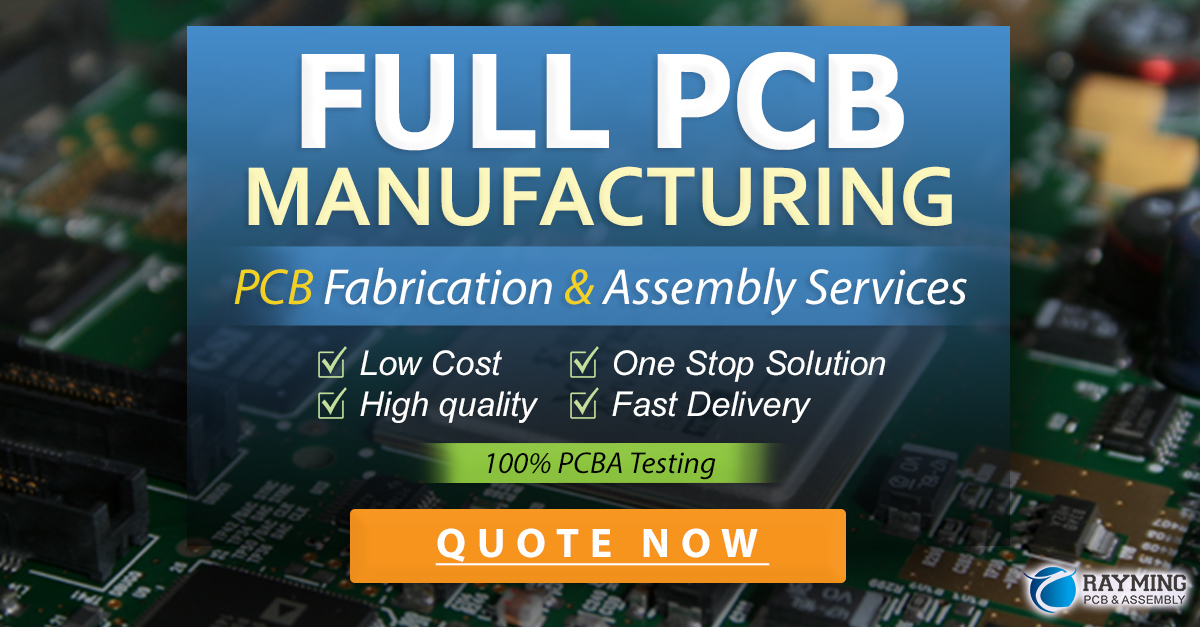
Frequently Asked Questions (FAQ)
-
Q: What is the most commonly used PCB substrate material?
A: FR-4 is the most widely used PCB substrate material due to its good balance of properties, wide availability, and low cost. -
Q: Which substrate material is best for high-frequency applications?
A: For high-frequency applications, low-loss materials like Rogers laminates and PTFE (Teflon) are preferred due to their excellent dielectric properties and high-frequency performance. -
Q: Are ceramic substrates suitable for flexible PCBs?
A: No, ceramic substrates are brittle and not suitable for flexible PCBs. Polyimide is a better choice for flexible and rigid-flex PCB applications. -
Q: Can I use FR-4 for high-temperature applications?
A: Standard FR-4 has a glass transition temperature (Tg) of 130-140°C, which may not be sufficient for high-temperature applications. High Tg FR-4 or polyimide substrates are better suited for high-temperature environments. -
Q: What factors should I consider when selecting a PCB substrate material?
A: When choosing a PCB substrate material, consider factors such as the dielectric constant (Dk), dissipation factor (Df), thermal conductivity, coefficient of thermal expansion (CTE), mechanical strength, and cost, based on your specific application requirements.
Conclusion
Selecting the right PCB substrate material is crucial for ensuring the optimal performance, reliability, and cost-effectiveness of your PCB design. By understanding the properties and trade-offs of various substrate materials, you can make an informed decision that meets the specific requirements of your application.
FR-4 remains the most popular choice for general-purpose electronics, while high-performance materials like Rogers laminates and PTFE excel in demanding RF and microwave applications. Polyimide and ceramic substrates offer unique advantages for high-temperature and thermally challenging environments.
When choosing a PCB substrate material, carefully consider factors such as dielectric properties, thermal conductivity, mechanical strength, and cost. Engage with experienced PCB manufacturers and material suppliers to discuss your specific requirements and obtain guidance on the most suitable substrate for your project.
By selecting the appropriate PCB substrate material, you can optimize signal integrity, thermal management, and overall reliability, ultimately leading to a successful and robust PCB design.
Leave a Reply