Introduction to PCB
Printed Circuit Boards (PCBs) are the backbone of modern electronics. They are used in almost every electronic device, from smartphones and computers to medical equipment and aerospace systems. PCBs are designed to mechanically support and electrically connect electronic components using conductive pathways, tracks, or signal traces etched from copper sheets laminated onto a non-conductive substrate.
In this comprehensive guide, we will explore the world of PCBs, covering everything from the basics of PCB design to advanced manufacturing techniques. Whether you are a beginner or an experienced engineer, this guide will provide you with valuable insights and practical tips to help you create high-quality PCBs.
PCB Design Fundamentals
Understanding the Basics
Before diving into the details of PCB design, it is essential to understand the basic concepts and terminology. Here are some key terms you should be familiar with:
- Substrate: The non-conductive material on which the copper traces and components are placed.
- Copper Traces: The conductive pathways that carry electrical signals between components.
- Pads: The exposed areas of copper on the PCB where components are soldered.
- Vias: The small holes drilled through the PCB that allow electrical connections between different layers.
- Solder Mask: The protective coating applied to the PCB to prevent accidental short circuits and improve the board’s durability.
- Silkscreen: The text and symbols printed on the PCB to aid in assembly and identification of components.
PCB Layers and Stackup
PCBs can be single-sided, double-sided, or multi-layered. The number of layers in a PCB depends on the complexity of the design and the required functionality. Here’s a brief overview of each type:
- Single-sided PCB: Has components and copper traces on only one side of the substrate.
- Double-sided PCB: Has components and copper traces on both sides of the substrate, with vias connecting the layers.
- Multi-layer PCB: Has multiple layers of copper traces separated by insulating layers, allowing for more complex designs and higher component density.
When designing a PCB, it is crucial to consider the stackup, which refers to the arrangement of layers in the board. A well-designed stackup ensures proper signal integrity, minimizes electromagnetic interference (EMI), and improves the overall performance of the PCB.
Component Placement and Routing
Component placement and routing are critical aspects of PCB design. Proper placement of components can minimize the length of copper traces, reduce signal interference, and improve the overall manufacturability of the board. When placing components, consider the following factors:
- Group related components together to minimize the length of traces.
- Place sensitive components away from sources of EMI, such as power supplies and high-speed digital circuits.
- Ensure adequate spacing between components to allow for proper soldering and assembly.
Once the components are placed, the next step is to route the copper traces between them. Routing can be done manually or using automated tools in PCB design software. When routing, keep these tips in mind:
- Use the shortest possible path between components to minimize signal loss and delay.
- Avoid sharp angles and sudden changes in direction, as they can cause signal reflections and EMI.
- Maintain consistent trace width and spacing to ensure uniform impedance and minimize crosstalk.
- Use ground planes and power planes to provide a low-impedance return path for signals and reduce EMI.
PCB Manufacturing Process
PCB Fabrication Steps
The PCB manufacturing process involves several steps, each of which plays a crucial role in ensuring the quality and reliability of the final product. Here’s a brief overview of the main steps involved:
- Design: The PCB design is created using specialized software, taking into account the required functionality, component placement, and routing.
- Substrate Preparation: The substrate material, typically FR-4, is cut to the desired size and shape.
- Copper Lamination: Thin layers of copper foil are laminated onto the substrate using heat and pressure.
- Drilling: Holes are drilled through the board to accommodate through-hole components and vias.
- Plating: The drilled holes are plated with copper to create electrical connections between layers.
- Etching: The unwanted copper is removed using a chemical etching process, leaving behind the desired copper traces and pads.
- Solder Mask Application: A protective solder mask is applied to the board, covering the copper traces while leaving the pads exposed.
- Silkscreen Printing: Text and symbols are printed onto the board using a silkscreen process to aid in assembly and identification.
- Surface Finishing: A final surface finish, such as HASL, ENIG, or OSP, is applied to the exposed copper to prevent oxidation and improve solderability.
- Electrical Testing: The completed board undergoes electrical testing to ensure proper functionality and connectivity.
Choosing the Right PCB Manufacturer
Selecting the right PCB manufacturer is essential to ensure the quality and reliability of your PCBs. When choosing a manufacturer, consider the following factors:
- Experience: Look for a manufacturer with a proven track record in producing high-quality PCBs for a wide range of applications.
- Capabilities: Ensure that the manufacturer has the necessary equipment and expertise to handle your specific PCB requirements, such as multi-layer boards or fine-pitch components.
- Quality Control: Choose a manufacturer that adheres to strict quality control standards, such as ISO 9001, and has a robust testing and inspection process in place.
- Lead Time: Consider the manufacturer’s lead time and ability to meet your production schedule.
- Customer Support: Look for a manufacturer that offers excellent customer support and is responsive to your questions and concerns.
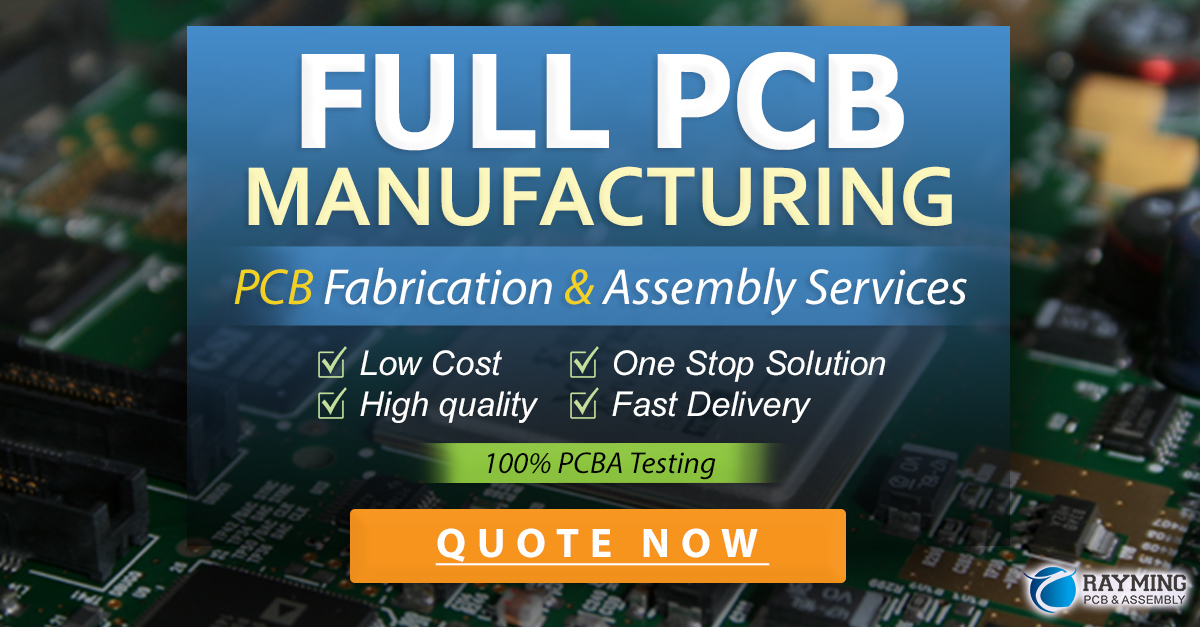
Advanced PCB Techniques
High-Speed PCB Design
Designing PCBs for high-speed applications requires careful consideration of signal integrity and EMI. Here are some tips for successful high-speed PCB design:
- Use controlled impedance traces to maintain signal integrity and minimize reflections.
- Implement proper termination techniques, such as series termination or parallel termination, to minimize signal overshoots and undershoots.
- Use ground planes and power planes to provide a low-impedance return path for high-speed signals.
- Minimize the use of vias, as they can cause signal discontinuities and reflections.
- Use differential signaling for high-speed data transmission to reduce EMI and improve signal quality.
Flexible and Rigid-Flex PCBs
Flexible and rigid-flex PCBs offer unique advantages over traditional rigid PCBs. Flexible PCBs are made from thin, flexible substrates that can bend and conform to various shapes, making them ideal for applications with limited space or requiring movable connections. Rigid-flex PCBs combine the benefits of both rigid and flexible PCBs, allowing for a combination of stable and flexible sections in a single board.
When designing flexible or rigid-flex PCBs, consider the following:
- Choose the appropriate substrate material based on the required flexibility and durability.
- Use larger bend radii to minimize stress on the copper traces and prevent damage to the board.
- Implement strain relief features, such as stiffeners or support structures, to protect the flexible portions of the board.
- Follow the manufacturer’s guidelines for minimum trace width and spacing to ensure reliable performance.
PCB Assembly Techniques
Proper PCB assembly is crucial for ensuring the reliability and functionality of the final product. Here are some common PCB assembly techniques:
- Through-Hole Assembly: Components with long leads are inserted through holes in the PCB and soldered on the opposite side.
- Surface Mount Assembly: Components with small leads or no leads are placed directly on the surface of the PCB and soldered in place.
- Mixed Assembly: A combination of through-hole and surface mount components are used on the same PCB.
When assembling PCBs, follow these best practices:
- Use the appropriate soldering technique and temperature for the specific components and PCB material.
- Ensure proper alignment and orientation of components during placement.
- Use adequate amounts of solder to create strong and reliable connections.
- Inspect the assembled board for any defects, such as bridging, cold solder joints, or missing components.
PCB Testing and Troubleshooting
PCB Testing Methods
Testing PCBs is essential to ensure their proper functionality and reliability. Here are some common PCB testing methods:
- Visual Inspection: A visual examination of the PCB to check for any obvious defects, such as missing components, solder bridges, or damaged traces.
- Continuity Testing: Verifying the electrical continuity between various points on the PCB to ensure proper connections.
- Impedance Testing: Measuring the impedance of controlled impedance traces to ensure they meet the specified requirements.
- Functional Testing: Verifying the proper operation of the PCB under real-world conditions, such as power-on tests, signal integrity tests, and environmental stress tests.
- Automated Optical Inspection (AOI): Using computer vision and image processing techniques to automatically inspect the PCB for defects and anomalies.
Troubleshooting Common PCB Issues
Despite careful design and manufacturing, PCBs can sometimes experience issues that require troubleshooting. Here are some common PCB issues and their potential causes:
Issue | Potential Causes |
---|---|
No Power | – Faulty power supply – Broken traces or connections – Short circuits |
Intermittent Operation | – Loose or faulty connections – Damaged components – Environmental factors (temperature, vibration) |
Signal Integrity Problems | – Improper trace routing – Inadequate ground or power planes – EMI from nearby sources |
Component Failures | – Overheating – Electrostatic discharge (ESD) – Mechanical stress or damage |
When troubleshooting PCBs, follow a systematic approach:
- Gather information about the issue, including symptoms, operating conditions, and any recent changes or modifications.
- Visually inspect the PCB for any obvious defects or anomalies.
- Check the power supply and ensure proper voltage levels.
- Use a multimeter or oscilloscope to measure voltages, currents, and signals at various test points.
- Isolate the faulty component or section of the PCB by systematically testing and eliminating potential causes.
- Consult the schematic and PCB layout to identify potential design issues or problematic areas.
- If necessary, replace faulty components or rework the PCB to correct any issues.
FAQs
-
Q: What is the difference between a single-sided and double-sided PCB?
A: A single-sided PCB has components and copper traces on only one side of the substrate, while a double-sided PCB has components and copper traces on both sides, with vias connecting the layers. -
Q: What is the purpose of a solder mask on a PCB?
A: The solder mask is a protective coating applied to the PCB that prevents accidental short circuits and improves the board’s durability by covering the copper traces while leaving the pads exposed for soldering. -
Q: What factors should I consider when choosing a PCB manufacturer?
A: When choosing a PCB manufacturer, consider their experience, capabilities, quality control standards, lead time, and customer support. Look for a manufacturer with a proven track record in producing high-quality PCBs for a wide range of applications and one that is responsive to your needs and concerns. -
Q: What is the importance of controlled impedance in high-speed PCB design?
A: Controlled impedance is crucial in high-speed PCB design to maintain signal integrity and minimize reflections. By carefully designing the trace width, spacing, and dielectric properties, controlled impedance traces ensure that the signals propagate with minimal distortion and loss, resulting in better performance and reliability. -
Q: What are some common PCB testing methods?
A: Common PCB testing methods include visual inspection, continuity testing, impedance testing, functional testing, and automated optical inspection (AOI). These methods help verify the proper functionality, reliability, and quality of the PCB, ensuring that it meets the specified requirements and performs as intended in the final application.
Conclusion
PCBs are essential components in modern electronics, and understanding their design, manufacturing, and testing processes is crucial for creating high-quality and reliable products. This comprehensive guide has covered the fundamentals of PCB design, manufacturing techniques, advanced PCB technologies, and testing and troubleshooting methods.
By following the tips and best practices outlined in this guide, you can create PCBs that meet your specific requirements and perform optimally in your applications. Remember to consider factors such as component placement, routing, stackup design, and manufacturing processes when designing your PCBs, and always work with a reputable manufacturer that can deliver high-quality boards that meet your needs.
As technology continues to advance, staying up-to-date with the latest PCB design and manufacturing techniques will be essential for staying competitive in the electronics industry. By continuously learning and adapting to new challenges, you can create PCBs that push the boundaries of what is possible and drive innovation in your field.
Leave a Reply