What are PCB Surface Finishes?
PCB surface finishes are the final coatings applied to the exposed copper traces and pads on a printed circuit board (PCB). These finishes serve several important functions, including:
- Protection against oxidation and corrosion
- Enhancing solderability
- Improving electrical conductivity
- Providing a suitable surface for component assembly
The choice of surface finish depends on various factors such as the intended application, environmental conditions, cost, and manufacturing requirements. In this article, we will explore the different types of PCB surface finishes commonly used in PCB Prototype manufacturing.
Types of PCB Surface Finishes
1. Hot Air Solder Leveling (HASL)
Hot Air Solder Leveling (HASL) is one of the most widely used surface finishes in the PCB industry. The process involves dipping the PCB into a molten solder bath, followed by the use of hot air knives to remove excess solder, resulting in a flat, even surface.
Advantages of HASL:
– Cost-effective
– Excellent solderability
– Good shelf life
– Suitable for through-hole components
Disadvantages of HASL:
– Uneven surface due to solder bumps
– Not suitable for fine-pitch components
– High thermal shock during the process
– Contains lead (Pb), which is not RoHS compliant
2. Electroless Nickel Immersion Gold (ENIG)
Electroless Nickel Immersion Gold (ENIG) is a popular choice for high-reliability applications. The process involves depositing a layer of nickel onto the copper surface, followed by a thin layer of gold. The nickel layer provides a barrier against copper diffusion, while the gold layer offers excellent solderability and corrosion resistance.
Advantages of ENIG:
– Flat and uniform surface
– Excellent solderability
– Good corrosion resistance
– Suitable for fine-pitch components
– RoHS compliant
Disadvantages of ENIG:
– Higher cost compared to HASL
– Potential for “black pad” issue due to excessive nickel corrosion
– Longer processing time
3. Immersion Silver (IAg)
Immersion Silver (IAg) is a cost-effective alternative to ENIG. The process involves depositing a thin layer of silver directly onto the copper surface through a chemical displacement reaction. IAg provides good solderability and is suitable for both leaded and lead-free soldering processes.
Advantages of IAg:
– Cost-effective compared to ENIG
– Flat and uniform surface
– Good solderability
– Suitable for fine-pitch components
– RoHS compliant
Disadvantages of IAg:
– Limited shelf life due to silver tarnishing
– Not suitable for high-temperature applications
– Potential for silver migration in high-humidity environments
4. Organic Solderability Preservative (OSP)
Organic Solderability Preservative (OSP) is a thin, organic coating applied to the copper surface to prevent oxidation and maintain solderability. OSP is a cost-effective and environmentally friendly option, as it does not contain any metals.
Advantages of OSP:
– Cost-effective
– Environmentally friendly
– Flat and uniform surface
– Suitable for fine-pitch components
– RoHS compliant
Disadvantages of OSP:
– Limited shelf life (typically 6-12 months)
– Requires careful handling and storage to prevent contamination
– Not suitable for multiple reflow cycles or rework
5. Electroless Nickel Electroless Palladium Immersion Gold (ENEPIG)
Electroless Nickel Electroless Palladium Immersion Gold (ENEPIG) is an advanced surface finish that combines the benefits of ENIG and Immersion Palladium. The process involves depositing a layer of nickel, followed by a layer of palladium and a thin layer of gold. ENEPIG offers excellent solderability, wire bonding capabilities, and corrosion resistance.
Advantages of ENEPIG:
– Suitable for both soldering and wire bonding
– Excellent solderability
– Good corrosion resistance
– Flat and uniform surface
– Suitable for fine-pitch components
– RoHS compliant
Disadvantages of ENEPIG:
– Higher cost compared to other surface finishes
– Longer processing time
– Potential for palladium corrosion in harsh environments
Comparison of PCB Surface Finishes
Surface Finish | Solderability | Shelf Life | Fine-Pitch Compatibility | Cost | RoHS Compliance |
---|---|---|---|---|---|
HASL | Excellent | Good | Limited | Low | No |
ENIG | Excellent | Excellent | Suitable | High | Yes |
IAg | Good | Limited | Suitable | Moderate | Yes |
OSP | Good | Limited | Suitable | Low | Yes |
ENEPIG | Excellent | Excellent | Suitable | High | Yes |
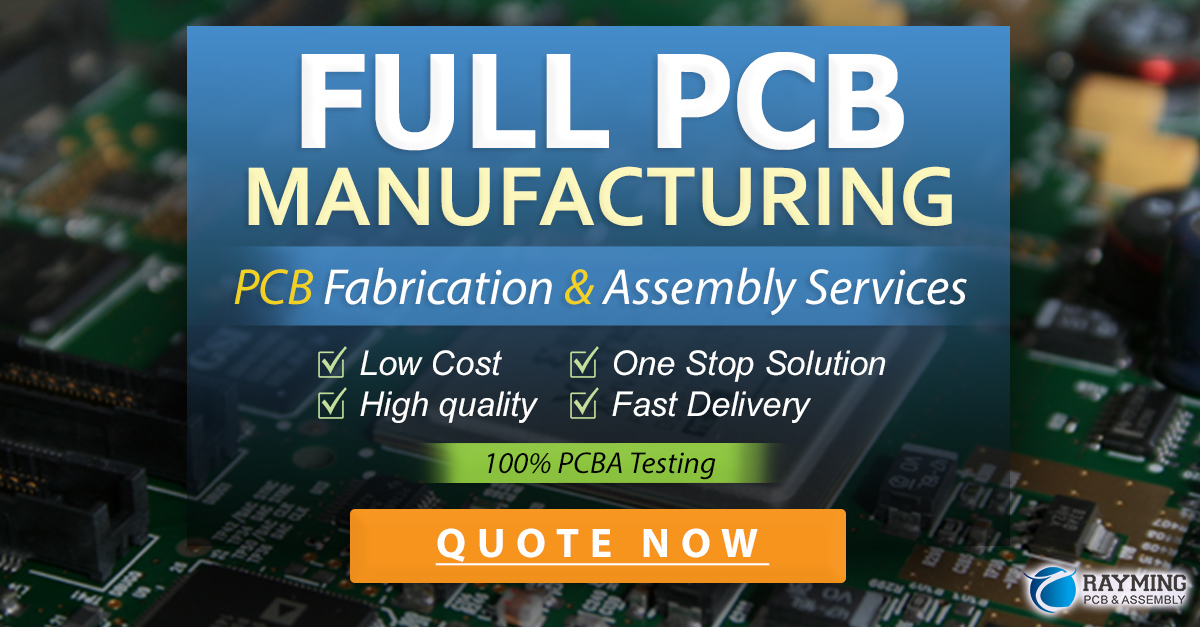
Frequently Asked Questions (FAQ)
-
Q: What is the most cost-effective PCB surface finish for prototypes?
A: Hot Air Solder Leveling (HASL) and Organic Solderability Preservative (OSP) are the most cost-effective surface finishes for PCB Prototypes. However, HASL contains lead, which is not RoHS compliant, so OSP may be a better choice for prototypes that require RoHS compliance. -
Q: Which surface finish is best suited for high-reliability applications?
A: Electroless Nickel Immersion Gold (ENIG) and Electroless Nickel Electroless Palladium Immersion Gold (ENEPIG) are both well-suited for high-reliability applications. These finishes provide excellent solderability, corrosion resistance, and are compatible with fine-pitch components. -
Q: Can I use Immersion Silver (IAg) for PCB prototypes that will be exposed to high humidity?
A: While Immersion Silver (IAg) is a cost-effective option for PCB prototypes, it may not be the best choice for applications exposed to high humidity. Silver can tarnish and migrate in high-humidity environments, which can lead to reliability issues. In such cases, ENIG or ENEPIG may be a better choice. -
Q: How long can I store PCB prototypes with Organic Solderability Preservative (OSP) surface finish?
A: PCB prototypes with an OSP surface finish typically have a limited shelf life of 6-12 months. It is important to handle and store OSP-coated PCBs carefully to prevent contamination and ensure optimal solderability within this timeframe. -
Q: Is it possible to rework PCB prototypes with HASL surface finish?
A: Reworking PCB prototypes with HASL surface finish can be challenging due to the uneven surface caused by solder bumps. The high thermal shock during the HASL process can also make the PCB more susceptible to damage during rework. If multiple reflow cycles or rework are anticipated, consider using a surface finish like ENIG or ENEPIG instead.
Conclusion
Selecting the appropriate surface finish for your PCB prototype is crucial for ensuring optimal performance, reliability, and manufacturability. Each surface finish has its own advantages and disadvantages, and the choice depends on factors such as the intended application, environmental conditions, cost, and manufacturing requirements.
For cost-sensitive prototypes, HASL and OSP are popular choices, while ENIG and ENEPIG are preferred for high-reliability applications. Immersion Silver (IAg) offers a balance between cost and performance but may not be suitable for high-humidity environments.
By understanding the characteristics and trade-offs of each surface finish, you can make an informed decision when choosing the best option for your PCB prototype. Always consult with your PCB manufacturer to discuss your specific requirements and ensure that the selected surface finish meets your project’s needs.
Leave a Reply