Introduction to PCB Price Composition
Printed Circuit Boards (PCBs) are essential components in modern electronics, providing a platform for electrical connections and mechanical support for various components. The price of a PCB is determined by several factors, including materials, manufacturing processes, design complexity, and order quantity. In this article, we will dive into the composition of PCB prices and explore the various elements that contribute to the overall cost.
Factors Influencing PCB Price
1. Materials
The materials used in PCB fabrication play a significant role in determining the final price. The most common base material for PCBs is FR-4, a glass-reinforced epoxy laminate. However, other materials such as polyimide, PTFE, and ceramic may be used for specific applications, which can impact the cost.
Common PCB Materials and Their Costs
Material | Cost (USD/sq. ft.) |
---|---|
FR-4 | 0.10 – 0.30 |
Polyimide | 1.00 – 2.00 |
PTFE | 2.00 – 4.00 |
Ceramic | 5.00 – 10.00 |
In addition to the base material, the copper used for the conductive layers also affects the price. The thickness of the copper layer, measured in ounces per square foot (oz/ft²), directly impacts the cost. Thicker copper layers are more expensive but offer better current-carrying capacity and heat dissipation.
2. Manufacturing Processes
The manufacturing processes involved in PCB fabrication significantly influence the overall price. The complexity of the PCB design, the number of layers, and the required precision all contribute to the manufacturing costs.
PCB Manufacturing Processes and Their Impact on Price
Process | Impact on Price |
---|---|
Drilling | Low |
Plating | Medium |
Etching | Medium |
Solder Mask Application | Low |
Silkscreen Printing | Low |
Surface Finishing | Medium to High |
The more complex the PCB design, the more manufacturing steps are required, leading to higher costs. For example, multi-layer PCBs are more expensive than single-layer boards due to the additional processing steps involved.
3. Design Complexity
The complexity of the PCB design is another crucial factor in determining the price. Design aspects such as the number of layers, trace width and spacing, via size, and component density all contribute to the overall complexity and, consequently, the cost.
PCB Design Complexity Factors
Factor | Impact on Price |
---|---|
Number of Layers | High |
Trace Width & Spacing | Medium |
Via Size | Low to Medium |
Component Density | Medium to High |
As the number of layers increases, the manufacturing process becomes more complex, requiring additional steps and materials, thus driving up the cost. Similarly, smaller trace widths and spacing, as well as higher component density, demand more precise manufacturing techniques, resulting in higher prices.
4. Order Quantity
The order quantity is another significant factor in PCB pricing. Manufacturers often offer volume discounts for larger orders, as the fixed costs associated with setup and tooling can be spread across more units.
PCB Order Quantity and Price
Order Quantity | Price per Unit (Relative) |
---|---|
1-50 | 100% |
51-100 | 80% |
101-500 | 60% |
501-1000 | 50% |
1000+ | 40% |
As the order quantity increases, the price per unit decreases, making it more cost-effective for buyers to purchase larger quantities. However, it is essential to consider the balance between order quantity and inventory management to avoid excess stock and associated storage costs.
Additional Factors Affecting PCB Price
Apart from the main factors discussed above, several other elements can influence the price of PCBs:
1. Lead Time
The lead time, or the time required to manufacture and deliver the PCBs, can impact the price. Faster turnaround times often come at a premium, as manufacturers may need to prioritize orders and allocate additional resources to meet tight deadlines.
2. Quality Control and Testing
Rigorous quality control and testing procedures are essential to ensure the reliability and functionality of PCBs. However, these processes add to the overall cost. Higher-quality PCBs with extensive testing may come at a higher price, but they offer better performance and reliability in the long run.
3. Certifications and Standards
Certain applications, such as military, aerospace, or medical devices, require PCBs to meet specific certifications and standards. Compliance with these standards often involves additional manufacturing processes, materials, and testing, which can increase the overall cost of the PCBs.
4. Shipping and Logistics
The cost of shipping and logistics can also impact the final price of PCBs, especially for international orders. Factors such as shipping method, distance, and customs fees can add to the overall expense. It is important to consider these costs when comparing prices from different suppliers.
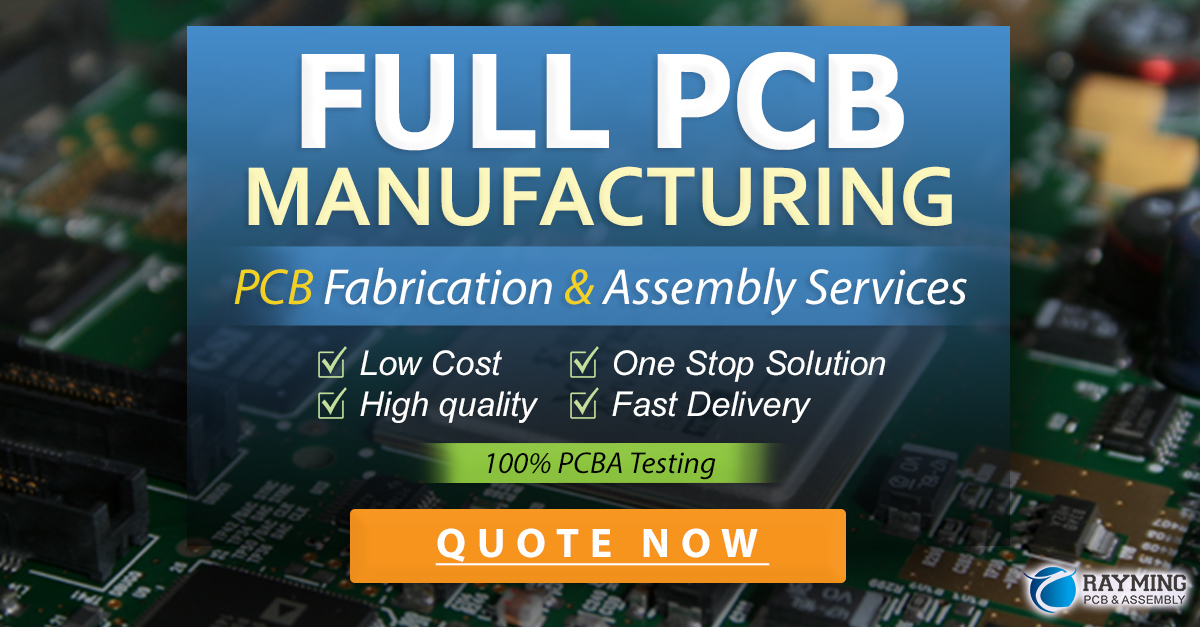
Strategies for Optimizing PCB Costs
While the price of PCBs is influenced by various factors, there are strategies that buyers can employ to optimize costs without compromising on quality or functionality:
1. Design Optimization
Collaborating with experienced PCB designers can help optimize the design for manufacturability and cost-effectiveness. By considering factors such as layer count, trace width and spacing, and component placement early in the design process, it is possible to reduce manufacturing complexity and associated costs.
2. Material Selection
Choosing the appropriate materials for the specific application can help balance cost and performance. While exotic materials may offer superior properties, they come at a higher price. Selecting standard materials that meet the requirements can help keep costs in check.
3. Volume Ordering
As discussed earlier, ordering PCBs in larger quantities can lead to significant cost savings due to volume discounts. By carefully planning production and inventory requirements, buyers can take advantage of these discounts without overstocking.
4. Supplier Selection
Engaging with multiple PCB Suppliers and comparing their prices, capabilities, and value-added services can help identify the most cost-effective option. It is essential to consider factors beyond just the unit price, such as quality, reliability, lead times, and customer support, to ensure a successful partnership.
5. Standardization
Standardizing PCB designs across multiple products or projects can lead to cost savings through economies of scale. By using common materials, components, and design elements, buyers can benefit from volume discounts and reduced setup costs.
FAQ
-
Q: What is the most significant factor influencing PCB price?
A: The most significant factor influencing PCB price is the design complexity, which includes aspects such as the number of layers, trace width and spacing, and component density. More complex designs require advanced manufacturing processes and materials, leading to higher costs. -
Q: How can I reduce the cost of my PCB order?
A: To reduce the cost of your PCB order, consider strategies such as design optimization, material selection, volume ordering, supplier selection, and standardization. Collaborating with experienced PCB designers and manufacturers can help identify cost-saving opportunities without compromising on quality or functionality. -
Q: Are there any hidden costs associated with PCB manufacturing?
A: Yes, there can be hidden costs associated with PCB manufacturing, such as shipping and logistics, certifications and compliance, and quality control and testing. It is important to discuss these aspects with your supplier upfront to avoid unexpected expenses. -
Q: How does the order quantity affect PCB pricing?
A: Order quantity has a significant impact on PCB pricing. Manufacturers often offer volume discounts for larger orders, as the fixed costs associated with setup and tooling can be spread across more units. As the order quantity increases, the price per unit typically decreases. -
Q: Can I use cheaper materials to reduce PCB costs?
A: While using cheaper materials may seem like an attractive option to reduce PCB costs, it is essential to consider the specific requirements of your application. Cheaper materials may not offer the same performance, reliability, or durability as higher-quality alternatives. It is important to strike a balance between cost and quality to ensure the long-term success of your product.
Conclusion
Understanding the composition of PCB prices is crucial for buyers looking to optimize costs without compromising on quality or functionality. By considering factors such as materials, manufacturing processes, design complexity, and order quantity, it is possible to make informed decisions and develop effective cost-saving strategies.
Collaborating with experienced PCB designers and manufacturers, carefully selecting materials, optimizing designs for manufacturability, and leveraging volume discounts can all contribute to reducing PCB costs. However, it is essential to approach cost optimization holistically, taking into account factors such as quality, reliability, and long-term performance.
By gaining a comprehensive understanding of PCB price composition and employing smart cost-saving strategies, buyers can ensure they are getting the best value for their investment while meeting the specific requirements of their applications.
Leave a Reply