Introduction to PCB Manufacturing
Printed Circuit Board (PCB) manufacturing is a vital process in the electronics industry. PCBs are the backbone of almost all electronic devices, from smartphones and computers to medical equipment and aerospace systems. A PCB is a flat board made of insulating materials, such as fiberglass or plastic, with conductive copper tracks printed on its surface. These tracks connect various electronic components, such as resistors, capacitors, and integrated circuits, to form a complete electronic circuit.
The Importance of PCB Manufacturing
PCB manufacturing has revolutionized the electronics industry by enabling the production of compact, reliable, and cost-effective electronic devices. Some of the key benefits of PCB manufacturing include:
- Miniaturization: PCBs allow for the miniaturization of electronic devices by enabling the integration of numerous components onto a single board.
- Reliability: PCBs provide a stable and reliable platform for electronic components, reducing the risk of short circuits and other failures.
- Cost-effectiveness: PCB manufacturing is a highly automated process, which reduces labor costs and enables the mass production of electronic devices at a lower cost per unit.
- Customization: PCBs can be customized to meet specific design requirements, allowing for the creation of unique electronic devices tailored to specific applications.
The PCB Manufacturing Process
The PCB manufacturing process involves several steps, each of which is critical to ensuring the quality and reliability of the final product. The main steps in the PCB manufacturing process are:
- Design: The first step in PCB manufacturing is the design phase. This involves creating a schematic diagram of the electronic circuit and a layout of the PCB using specialized software tools.
- Fabrication: Once the design is complete, the PCB is fabricated using a series of chemical and mechanical processes. This typically involves the following sub-steps:
- Printing the circuit pattern onto the copper-clad board using photoresist and exposure to UV light.
- Etching away the unwanted copper using a chemical solution, leaving only the desired circuit pattern.
- Drilling holes for through-hole components and vias.
- Applying a solder mask to protect the copper tracks and prevent short circuits.
- Adding a silkscreen layer for labeling and identification of components.
- Assembly: After the PCB is fabricated, the electronic components are assembled onto the board using either through-hole or surface-mount technology (SMT). Through-hole components are inserted into drilled holes and soldered in place, while SMT components are placed directly onto the surface of the board and soldered using a reflow oven.
- Testing: Once the PCB is assembled, it undergoes a series of tests to ensure its functionality and reliability. This may include visual inspections, automated optical inspections (AOI), and electrical tests such as continuity and insulation resistance tests.
- Finishing: Finally, the PCB may undergo additional finishing processes, such as conformal coating or potting, to protect it from environmental factors such as moisture, dust, and vibration.
Types of PCBs
There are several types of PCBs, each with its own unique characteristics and applications. The most common types of PCBs are:
- Single-sided PCBs: These PCBs have copper tracks on only one side of the board. They are the simplest and most cost-effective type of PCB, suitable for low-complexity circuits.
- Double-sided PCBs: These PCBs have copper tracks on both sides of the board, allowing for more complex circuits and higher component density. They require through-hole plating to connect the tracks on both sides.
- Multi-layer PCBs: These PCBs have multiple layers of copper tracks separated by insulating layers. They offer the highest component density and are used for complex, high-speed circuits such as those found in smartphones and computers.
- Flexible PCBs: These PCBs are made from flexible materials such as polyimide, allowing them to bend and fold. They are used in applications where space is limited, or where the PCB needs to conform to a specific shape.
- Rigid-Flex PCBs: These PCBs combine the benefits of rigid and flexible PCBs, with rigid sections for mounting components and flexible sections for connecting them. They are used in applications where both stability and flexibility are required.
PCB Materials
The choice of materials used in PCB manufacturing is critical to the performance and reliability of the final product. The most common materials used in PCB manufacturing are:
- FR-4: This is the most widely used material for PCBs. It is a composite material made from woven fiberglass and epoxy resin, offering good mechanical strength, electrical insulation, and thermal stability.
- Polyimide: This is a high-performance material used in flexible PCBs. It offers excellent thermal and chemical resistance, as well as high tensile strength and dimensional stability.
- Teflon: This is a low-loss material used in high-frequency PCBs. It offers excellent electrical insulation and low dielectric constant, making it suitable for applications such as radar and wireless communication.
- Aluminum: This is a metal-based material used in PCBs for heat dissipation. It offers excellent thermal conductivity and is often used in high-power applications such as LED lighting and power electronics.
PCB Manufacturing Services
PCB manufacturing services are provided by specialized companies that have the expertise and equipment necessary to produce high-quality PCBs. These services can be broadly categorized into two types:
- Turnkey PCB manufacturing: This is a full-service option where the PCB manufacturer handles all aspects of the PCB production process, from design to assembly and testing. This is suitable for companies that do not have in-house PCB manufacturing capabilities or those that want to outsource the entire process.
- Bare board PCB manufacturing: This is a partial-service option where the PCB manufacturer only produces the bare PCB without assembling the components. This is suitable for companies that have in-house assembly capabilities or those that want to source components separately.
When choosing a PCB manufacturing service, it is important to consider factors such as:
- Experience and expertise in PCB manufacturing
- Quality control processes and certifications
- Turnaround time and delivery options
- Pricing and minimum order quantities
- Customer support and communication
PCB Design Considerations
Designing a PCB involves several considerations to ensure optimal performance, reliability, and manufacturability. Some of the key design considerations are:
- Schematic design: The first step in PCB design is creating a schematic diagram of the electronic circuit. This involves selecting the appropriate components, defining their connections, and ensuring that the circuit functions as intended.
- Layout design: Once the schematic is complete, the next step is to create a layout of the PCB. This involves placing the components on the board, routing the copper tracks to connect them, and ensuring that the layout meets the design rules and constraints.
- Signal integrity: This refers to the quality of the electrical signals transmitted through the PCB. Factors that can affect signal integrity include trace width and spacing, impedance matching, and crosstalk between adjacent traces.
- Electromagnetic compatibility (EMC): This refers to the ability of the PCB to operate without causing or being affected by electromagnetic interference (EMI). EMC considerations include proper grounding, shielding, and filtering of signals.
- Thermal management: This refers to the ability of the PCB to dissipate heat generated by the components. Thermal management considerations include the use of heatsinks, thermal vias, and proper component placement.
- Manufacturability: This refers to the ease with which the PCB can be manufactured. Manufacturability considerations include the use of standard component sizes and footprints, the avoidance of tight tolerances and small features, and the use of design for manufacturing (DFM) guidelines.
PCB Design Software
PCB design software is used to create the schematic and layout of the PCB. There are several PCB design software tools available, ranging from free and open-source tools to commercial and enterprise-level tools. Some of the popular PCB design software tools are:
- Altium Designer: This is a high-end PCB design tool used by professional designers and engineers. It offers advanced features such as 3D modeling, simulation, and automatic routing.
- KiCad: This is a free and open-source PCB design tool that offers a complete suite of tools for schematic capture, PCB layout, and gerber file generation.
- Eagle: This is a popular PCB design tool used by hobbyists and small businesses. It offers a simple and intuitive interface and a large library of components.
- OrCAD: This is a commercial PCB design tool used by large enterprises. It offers advanced features such as constraint-driven design, signal integrity analysis, and design collaboration.
PCB Design Services
For companies that do not have in-house PCB design capabilities, PCB design services are available from specialized companies. These services can be broadly categorized into two types:
- Full-service PCB design: This is a complete PCB design service that includes schematic capture, PCB layout, and generation of manufacturing files. This is suitable for companies that do not have any PCB design expertise or those that want to outsource the entire design process.
- PCB layout only: This is a partial PCB design service that only includes PCB layout based on a provided schematic. This is suitable for companies that have in-house schematic design capabilities but lack PCB layout expertise.
When choosing a PCB design service, it is important to consider factors such as:
- Experience and expertise in PCB design
- Familiarity with the specific industry or application
- Communication and collaboration processes
- Pricing and turnaround time
- Intellectual property (IP) protection and confidentiality
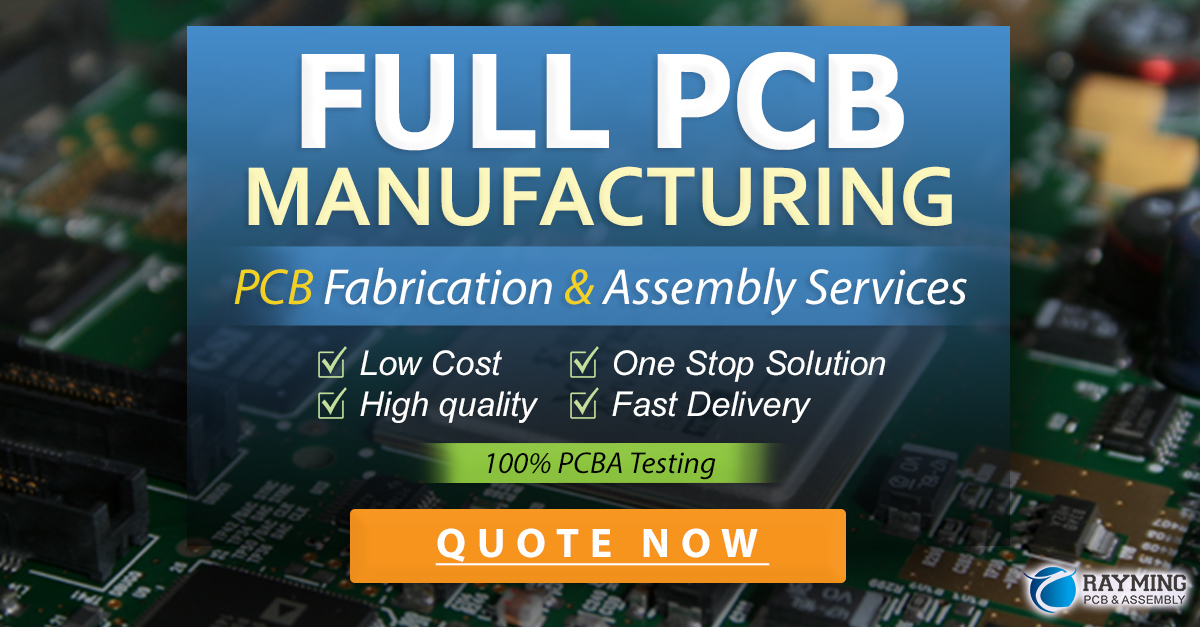
PCB Assembly
PCB assembly is the process of assembling electronic components onto the PCB to create a functional electronic device. There are two main types of PCB assembly: through-hole assembly and surface-mount assembly.
Through-Hole Assembly
Through-hole assembly involves inserting the leads of the components through holes drilled in the PCB and soldering them in place on the opposite side. This type of assembly is typically used for larger components such as connectors, transformers, and heavy-duty switches.
The main advantages of through-hole assembly are:
- Stronger mechanical bonding between the components and the PCB
- Easier to solder and inspect visually
- Suitable for high-power and high-voltage applications
The main disadvantages of through-hole assembly are:
- Larger component sizes and lower component density
- Higher labor costs and slower assembly speeds
- Limited routing space on the PCB due to the presence of drilled holes
Surface-Mount Assembly
Surface-mount assembly involves placing the components directly onto the surface of the PCB and soldering them in place using a reflow oven. This type of assembly is typically used for smaller components such as resistors, capacitors, and integrated circuits.
The main advantages of surface-mount assembly are:
- Smaller component sizes and higher component density
- Lower labor costs and faster assembly speeds
- More routing space on the PCB due to the absence of drilled holes
The main disadvantages of surface-mount assembly are:
- Weaker mechanical bonding between the components and the PCB
- More difficult to solder and inspect visually
- Limited to low-power and low-voltage applications
PCB Assembly Services
PCB assembly services are provided by specialized companies that have the expertise and equipment necessary to assemble PCBs. These services can be broadly categorized into two types:
- Turnkey PCB assembly: This is a full-service option where the PCB assembly provider handles all aspects of the assembly process, from component sourcing to final testing and packaging. This is suitable for companies that do not have in-house assembly capabilities or those that want to outsource the entire process.
- Consignment PCB assembly: This is a partial-service option where the customer provides the components and the PCB assembly provider only performs the assembly process. This is suitable for companies that have in-house component sourcing capabilities or those that want to maintain control over the bill of materials (BOM).
When choosing a PCB assembly service, it is important to consider factors such as:
- Experience and expertise in PCB assembly
- Quality control processes and certifications
- Turnaround time and delivery options
- Pricing and minimum order quantities
- Customer support and communication
PCB Testing and Quality Control
PCB testing and quality control are critical to ensuring the reliability and functionality of the final product. There are several types of tests that can be performed on PCBs, including:
- Visual inspection: This involves visually examining the PCB for defects such as solder bridges, cold solder joints, and component misalignment.
- Automated optical inspection (AOI): This involves using a camera-based system to automatically inspect the PCB for defects such as missing components, incorrect component placement, and solder defects.
- X-ray inspection: This involves using X-rays to inspect the internal structure of the PCB, including the solder joints and vias.
- In-circuit testing (ICT): This involves using a bed-of-nails fixture to test the functionality of individual components and circuits on the PCB.
- Functional testing: This involves testing the overall functionality of the PCB in its intended application or environment.
In addition to these tests, PCB manufacturers also implement several quality control processes to ensure consistent and reliable production. These include:
- Statistical process control (SPC) to monitor and control the manufacturing process
- Lean manufacturing principles to minimize waste and optimize efficiency
- Six Sigma methodologies to reduce defects and improve quality
- ISO 9001 and other quality management system certifications
Benefits of PCB Testing and Quality Control
Implementing effective PCB testing and quality control processes offers several benefits, including:
- Reduced defects and failures: By identifying and correcting defects early in the manufacturing process, PCB testing and quality control can significantly reduce the number of defective or failed products.
- Improved reliability: By ensuring that PCBs meet the required quality standards, PCB testing and quality control can improve the reliability and longevity of the final product.
- Lower costs: By reducing defects and failures, PCB testing and quality control can lower the overall costs associated with repairs, returns, and replacements.
- Faster time-to-market: By identifying and correcting issues early in the manufacturing process, PCB testing and quality control can help reduce development and production times, enabling faster time-to-market.
- Enhanced customer satisfaction: By delivering high-quality and reliable products, PCB testing and quality control can enhance customer satisfaction and loyalty.
Conclusion
PCB manufacturing is a complex and multi-faceted process that requires expertise, precision, and attention to detail. From design and fabrication to assembly and testing, each stage of the PCB manufacturing process plays a critical role in ensuring the quality and reliability of the final product.
By understanding the various aspects of PCB manufacturing, including the types of PCBs, materials, design considerations, assembly techniques, and testing and quality control processes, companies can make informed decisions when selecting PCB manufacturing services and ensure the success of their electronic products.
As the electronics industry continues to evolve and advance, PCB manufacturing will remain a critical enabler of innovation and progress, powering the devices and technologies that shape our world.
FAQs
-
What is the difference between a PCB and a PCBA?
A PCB (Printed Circuit Board) is the bare board without any components assembled onto it, while a PCBA (Printed Circuit Board Assembly) is a PCB with all the components assembled onto it, ready for use in an electronic device. -
What are the different types of PCBs?
The main types of PCBs are single-sided, double-sided, multi-layer, flexible, and rigid-flex PCBs. Each type has its own unique characteristics and applications, depending on the complexity and requirements of the electronic circuit. -
What are the key considerations when designing a PCB?
The key considerations when designing a PCB include schematic design, layout design, signal integrity, electromagnetic compatibility (EMC), thermal management, and manufacturability. Each of these factors plays a critical role in ensuring the optimal performance and reliability of the final product. -
What are the main differences between through-hole and surface-mount assembly?
Through-hole assembly involves inserting component leads through drilled holes in the PCB and soldering them in place, while surface-mount assembly involves placing components directly onto the surface of the PCB and soldering them using a reflow oven. Through-hole assembly is typically used for larger components and offers stronger mechanical bonding, while surface-mount assembly is used for smaller components and offers higher component density and faster assembly speeds. -
Why are PCB testing and quality control important?
PCB testing and quality control are critical to ensuring the reliability and functionality of the final product. By identifying and correcting defects early in the manufacturing process, PCB testing and quality control can reduce defects and failures, improve reliability, lower costs, accelerate time-to-market, and enhance customer satisfaction.
PCB Type | Layers | Application | Cost |
---|---|---|---|
Single-sided | 1 | Simple circuits, low-power applications | Low |
Double-sided | 2 | Moderately complex circuits, higher component density | Medium |
Multi-layer | 3+ | Complex circuits, high-speed applications, high component density | High |
Flexible | 1-2 | Wearable devices, portable electronics, tight spaces | High |
Rigid-Flex | 1-12 | Complex 3D circuits, high reliability, mixed rigid and flex sections | Very High |
Assembly Type | Component Size | Advantages | Disadvantages |
---|---|---|---|
Through-hole | Larger | Stronger mechanical bonding, easier |
Leave a Reply