Types of PCB drilling defects
There are several types of drilling defects that can occur during PCB manufacturing. These defects can be categorized into the following:
1. Hole Size Variations
Hole size variations occur when the drilled holes are either larger or smaller than the specified dimensions. This can happen due to various reasons, such as:
- Worn-out drill bits
- Improper drill bit selection
- Incorrect feed rates and spindle speeds
- Vibrations during drilling
2. Hole Misalignment
Hole misalignment refers to the deviation of drilled holes from their intended positions. This can be caused by:
- Incorrect drill program
- Machine calibration errors
- Improper material handling
- Incorrect registration of the drill file with the PCB Artwork
3. Hole Breakout
Hole breakout occurs when the drill bit exits the PCB material, causing damage to the outer layers or the adjacent holes. This can be due to:
- Dull drill bits
- Excessive drilling speeds
- Inadequate backing material
- Incorrect stack-up of the PCB Layers
4. Burrs and Raised Edges
Burrs and raised edges are the rough or sharp protrusions around the drilled holes. These defects can be caused by:
- Worn-out or damaged drill bits
- Improper choice of drilling parameters
- Insufficient cleaning of the drilled holes
- Inadequate surface preparation
Causes of PCB Drilling Defects
To effectively eliminate PCB drilling defects, it is essential to understand their root causes. Some of the primary reasons for drilling defects are:
1. Drill Bit Wear and Damage
Drill bits are subjected to wear and tear during the drilling process. As the drill bits become worn out or damaged, they can cause various defects, such as hole size variations, burrs, and raised edges. Factors that contribute to drill bit wear and damage include:
- Excessive drilling speeds and feed rates
- Improper coolant application
- Inadequate cleaning and maintenance of the drill bits
- Incorrect drill bit selection for the material being drilled
2. Machine Calibration and Maintenance
PCB drilling machines require regular calibration and maintenance to ensure accurate and consistent drilling results. Improper calibration or lack of maintenance can lead to defects such as hole misalignment and size variations. Some of the key aspects of machine calibration and maintenance include:
- Regular checks and adjustments of the machine’s axis alignment
- Proper lubrication and cleaning of the machine components
- Timely replacement of worn-out or damaged parts
- Periodic software updates and parameter optimization
3. Material Handling and Stack-up
The way PCB materials are handled and stacked-up during the drilling process can also contribute to drilling defects. Improper material handling can cause issues such as:
- Misalignment of the PCB layers
- Damage to the PCB surface or copper traces
- Incorrect registration of the drill file with the PCB artwork
To avoid these issues, it is crucial to follow proper material handling procedures, such as:
- Using clean and flat work surfaces
- Ensuring correct orientation and alignment of the PCB layers
- Applying adequate pressure during stack-up to prevent layer shifting
- Using appropriate backing materials to minimize hole breakout
Elimination Methods for PCB Drilling Defects
To eliminate PCB drilling defects, manufacturers can implement various methods and best practices. Some of the effective approaches include:
1. Proper Drill Bit Selection and Maintenance
Selecting the right drill bit for the specific PCB material and thickness is crucial for achieving accurate and defect-free drilling. Manufacturers should consider factors such as:
- Drill bit material and coating
- Flute design and geometry
- Point angle and chisel edge configuration
- Diameter and length of the drill bit
Regular maintenance and replacement of the drill bits are also essential to prevent wear-related defects. This includes:
- Cleaning and inspecting the drill bits periodically
- Resharpening or replacing the drill bits as needed
- Using appropriate coolants and lubricants during drilling
2. Optimizing Drilling Parameters
Drilling parameters, such as spindle speed, feed rate, and depth of cut, play a significant role in the quality of the drilled holes. Manufacturers should optimize these parameters based on the specific PCB material, thickness, and drill bit characteristics. This can be achieved through:
- Conducting trial runs and analyzing the results
- Using recommended parameters from the drill bit manufacturer
- Monitoring and adjusting the parameters during production
- Implementing statistical process control (SPC) techniques
3. Implementing Quality Control Measures
Implementing robust quality control measures throughout the PCB manufacturing process can help identify and prevent drilling defects. Some of the essential quality control measures include:
- Visual inspection of the drilled holes using microscopes or automated vision systems
- Conducting electrical tests to verify the continuity and insulation resistance of the holes
- Performing cross-sectional analysis to assess the hole quality and integrity
- Implementing a feedback loop to communicate and address any issues promptly
Defect Type | Causes | Elimination Methods |
---|---|---|
Hole Size Variations | – Worn-out drill bits – Improper drill bit selection – Incorrect feed rates and spindle speeds – Vibrations during drilling |
– Proper drill bit selection and maintenance – Optimizing drilling parameters – Implementing quality control measures |
Hole Misalignment | – Incorrect drill program – Machine calibration errors – Improper material handling – Incorrect registration of the drill file with the PCB artwork |
– Machine calibration and maintenance – Proper material handling and stack-up – Implementing quality control measures |
Hole Breakout | – Dull drill bits – Excessive drilling speeds – Inadequate backing material – Incorrect stack-up of the PCB layers |
– Proper drill bit selection and maintenance – Optimizing drilling parameters – Proper material handling and stack-up |
Burrs and Raised Edges | – Worn-out or damaged drill bits – Improper choice of drilling parameters – Insufficient cleaning of the drilled holes – Inadequate surface preparation |
– Proper drill bit selection and maintenance – Optimizing drilling parameters – Implementing quality control measures |
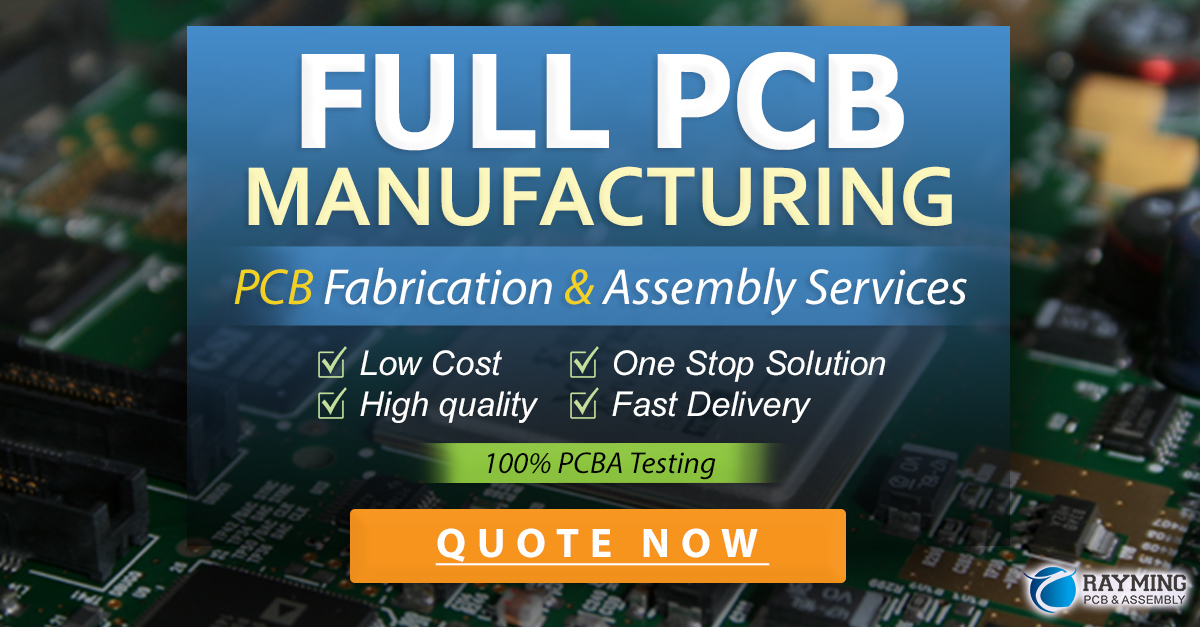
Frequently Asked Questions (FAQ)
- What is the most common cause of PCB drilling defects?
-
The most common cause of PCB drilling defects is worn-out or damaged drill bits. As drill bits wear out, they can cause hole size variations, burrs, and raised edges.
-
How can I prevent hole misalignment during PCB drilling?
-
To prevent hole misalignment, ensure proper machine calibration and maintenance, correct material handling and stack-up, and implement quality control measures such as visual inspection and automated vision systems.
-
What are the consequences of PCB drilling defects?
-
PCB drilling defects can lead to poor quality PCBs, component placement issues, and potential failures in the final product. These defects can also increase production costs and lead to customer dissatisfaction.
-
How often should I replace the drill bits during PCB manufacturing?
-
The frequency of drill bit replacement depends on various factors, such as the PCB material, drilling parameters, and the condition of the drill bits. Manufacturers should monitor the drill bit performance and replace them as needed based on the recommended guidelines and quality control data.
-
Can PCB drilling defects be repaired after the manufacturing process?
- While some minor drilling defects can be repaired using techniques such as hole re-drilling or filling, it is generally more cost-effective and efficient to prevent defects during the manufacturing process. Implementing proper prevention and elimination methods can help minimize the need for post-production repairs.
Conclusion
PCB drilling defects can have a significant impact on the quality and reliability of the final product. By understanding the types of defects, their causes, and the elimination methods, manufacturers can take proactive steps to minimize these issues. Proper drill bit selection and maintenance, optimizing drilling parameters, and implementing quality control measures are essential for achieving defect-free PCB drilling. By adopting these best practices, manufacturers can improve their PCB Quality, reduce production costs, and enhance customer satisfaction.
Leave a Reply