Factors Influencing PCB Manufacturing Costs
Several key factors influence the cost of PCB manufacturing. These include:
- PCB Design Complexity
- PCB Size and Thickness
- Number of Layers
- Material Selection
- Surface Finish
- Quantity and Turnaround Time
- Testing and Inspection Requirements
Let’s explore each of these factors in more detail.
PCB Design Complexity
The complexity of your PCB design directly impacts the manufacturing cost. A simple, single-layer board with few components will be less expensive to produce compared to a multi-layer board with intricate routing and numerous components. The more complex the design, the higher the manufacturing cost.
Consider the following aspects of PCB design complexity:
- Number and density of components
- Routing density and trace width
- Via and hole sizes
- Special features (e.g., blind/buried vias, impedance control)
To minimize costs, aim for a design that balances functionality and simplicity. Collaborate with your PCB manufacturer early in the design process to optimize your design for manufacturability and cost-effectiveness.
PCB Size and Thickness
The size and thickness of your PCB also play a significant role in determining the manufacturing cost. Larger boards require more material and processing time, resulting in higher costs. Similarly, thicker boards (e.g., 2.0mm or more) are more expensive to manufacture compared to standard thicknesses (e.g., 1.6mm).
Consider the following table that illustrates the impact of PCB size on manufacturing cost:
PCB Size | Relative Cost |
---|---|
Small (< 50cm²) | Low |
Medium (50-100cm²) | Moderate |
Large (> 100cm²) | High |
To optimize costs, design your PCB to be as compact as possible while still meeting your functional requirements. If your application allows, consider using standard PCB sizes and thicknesses to benefit from economies of scale.
Number of Layers
The number of layers in your PCB directly affects the manufacturing cost. Each additional layer requires more material, processing time, and complexity. As a general rule, the cost increases exponentially with the number of layers.
Consider the following table that shows the relative cost impact of different layer counts:
Number of Layers | Relative Cost |
---|---|
1-2 | Low |
4 | Moderate |
6-8 | High |
10+ | Very High |
To minimize costs, use the minimum number of layers required for your design. If possible, consider alternative design approaches, such as using smaller components or optimizing component placement, to reduce the need for additional layers.
Material Selection
The choice of PCB material significantly influences the manufacturing cost. The most common PCB materials are FR-4, which is a glass-reinforced epoxy laminate, and various high-frequency materials like Rogers or Isola.
FR-4 is the most cost-effective option for the majority of PCB applications. However, if your design requires specific properties, such as high-frequency performance, controlled dielectric constant, or thermal stability, you may need to opt for specialized materials, which come at a higher cost.
Consider the following table that compares the relative costs of different PCB materials:
Material | Relative Cost |
---|---|
FR-4 | Low |
High-Frequency Materials (e.g., Rogers, Isola) | High |
Polyimide | Very High |
Flexible Materials | High |
To optimize costs, select the most cost-effective material that meets your design requirements. If your application allows, consider using standard FR-4 material to benefit from its widespread availability and lower cost.
Surface Finish
The choice of surface finish for your PCB affects both the manufacturing cost and the performance of the final product. Common surface finishes include Hot Air Solder Leveling (HASL), Organic Solderability Preservative (OSP), Electroless Nickel Immersion Gold (ENIG), and Immersion Silver (IAg).
HASL and OSP are the most cost-effective options, while ENIG and IAg offer improved solderability and durability at a higher cost. The choice of surface finish depends on your specific application requirements, such as shelf life, soldering process, and environmental conditions.
Consider the following table that compares the relative costs of different surface finishes:
Surface Finish | Relative Cost |
---|---|
HASL | Low |
OSP | Low |
ENIG | High |
IAg | Moderate |
To optimize costs, select the most cost-effective surface finish that meets your design requirements. If your application allows, consider using HASL or OSP to benefit from their lower cost.
Quantity and Turnaround Time
The quantity of PCBs you order and the required turnaround time significantly impact the manufacturing cost. Higher quantities often result in lower per-unit costs due to economies of scale. Faster turnaround times, on the other hand, typically incur additional charges.
Consider the following table that illustrates the impact of quantity on per-unit cost:
Quantity | Relative Per-Unit Cost |
---|---|
Low (< 100) | High |
Medium (100-500) | Moderate |
High (> 500) | Low |
To optimize costs, plan your PCB requirements in advance and order in larger quantities whenever possible. If your project timeline allows, opt for standard turnaround times to avoid additional charges associated with expedited production.
Testing and Inspection Requirements
The level of testing and inspection required for your PCBs also influences the manufacturing cost. Basic testing, such as electrical continuity and visual inspection, is typically included in the standard manufacturing process. However, more advanced testing, such as in-circuit testing (ICT) or functional testing, comes at an additional cost.
Consider the following table that compares the relative costs of different testing and inspection options:
Testing and Inspection | Relative Cost |
---|---|
Basic (Continuity and Visual) | Low |
Flying Probe Testing | Moderate |
In-Circuit Testing (ICT) | High |
Functional Testing | High |
To optimize costs, determine the appropriate level of testing and inspection required for your application. If your design is relatively simple and has a low risk of failure, basic testing may suffice. For more complex or critical applications, consider the benefits of advanced testing in terms of reliability and long-term cost savings.
Strategies for Cost Optimization
Now that we have explored the various factors influencing PCB manufacturing costs, let’s discuss some strategies for optimizing your expenses:
-
Design for Manufacturability (DFM): Collaborate with your PCB manufacturer early in the design process to ensure your design is optimized for manufacturability. This can help identify potential issues and minimize the need for costly redesigns or rework.
-
Standardize Materials and Processes: Whenever possible, use standard materials, sizes, and thicknesses that are readily available and widely used in the industry. This can help reduce material costs and lead times.
-
Optimize Panel Utilization: Work with your PCB manufacturer to optimize the panel utilization of your design. This involves arranging multiple PCBs on a single production panel to maximize material usage and minimize waste.
-
Consider Bulk Ordering: If your project requires a large number of PCBs, consider placing a bulk order to benefit from economies of scale. This can significantly reduce the per-unit cost of your PCBs.
-
Plan for Inventory Management: If your PCB requirements are consistent over time, consider establishing a long-term supply agreement with your manufacturer. This can help ensure a steady supply of PCBs at a predictable cost and lead time.
-
Evaluate Total Cost of Ownership: When making decisions about PCB manufacturing, consider the total cost of ownership rather than just the upfront manufacturing cost. Factors such as reliability, durability, and maintenance requirements can have a significant impact on the long-term cost of your product.
FAQ
-
Q: What is the most significant factor influencing PCB manufacturing cost?
A: The complexity of the PCB design is often the most significant factor influencing manufacturing cost. A more complex design with higher layer counts, dense component placement, and intricate routing will generally be more expensive to manufacture. -
Q: How can I reduce the cost of PCB manufacturing without compromising quality?
A: To reduce PCB manufacturing costs without compromising quality, consider designing for manufacturability (DFM), using standard materials and processes, optimizing panel utilization, and placing bulk orders when possible. Collaborating with your PCB manufacturer early in the design process can also help identify cost-saving opportunities. -
Q: Is it always cheaper to order PCBs in larger quantities?
A: In most cases, ordering PCBs in larger quantities will result in a lower per-unit cost due to economies of scale. However, it’s essential to consider your actual PCB requirements and avoid over-ordering, as this can lead to excess inventory and storage costs. -
Q: How does the choice of surface finish affect PCB manufacturing cost?
A: The choice of surface finish can significantly impact PCB manufacturing cost. HASL and OSP are generally the most cost-effective options, while ENIG and IAg offer improved performance at a higher cost. The appropriate surface finish depends on your specific application requirements. -
Q: What testing and inspection options are available for PCBs, and how do they affect cost?
A: Basic testing, such as electrical continuity and visual inspection, is typically included in the standard PCB manufacturing process. More advanced testing options, such as flying probe testing, in-circuit testing (ICT), and functional testing, are available at an additional cost. The appropriate level of testing depends on the complexity and criticality of your application.
By understanding the factors influencing PCB manufacturing costs and implementing cost-optimization strategies, you can maximize your cost savings without compromising the quality and performance of your PCBs. Collaborating with your PCB manufacturer and making informed decisions throughout the design and production process will help ensure the success of your project while keeping costs under control.
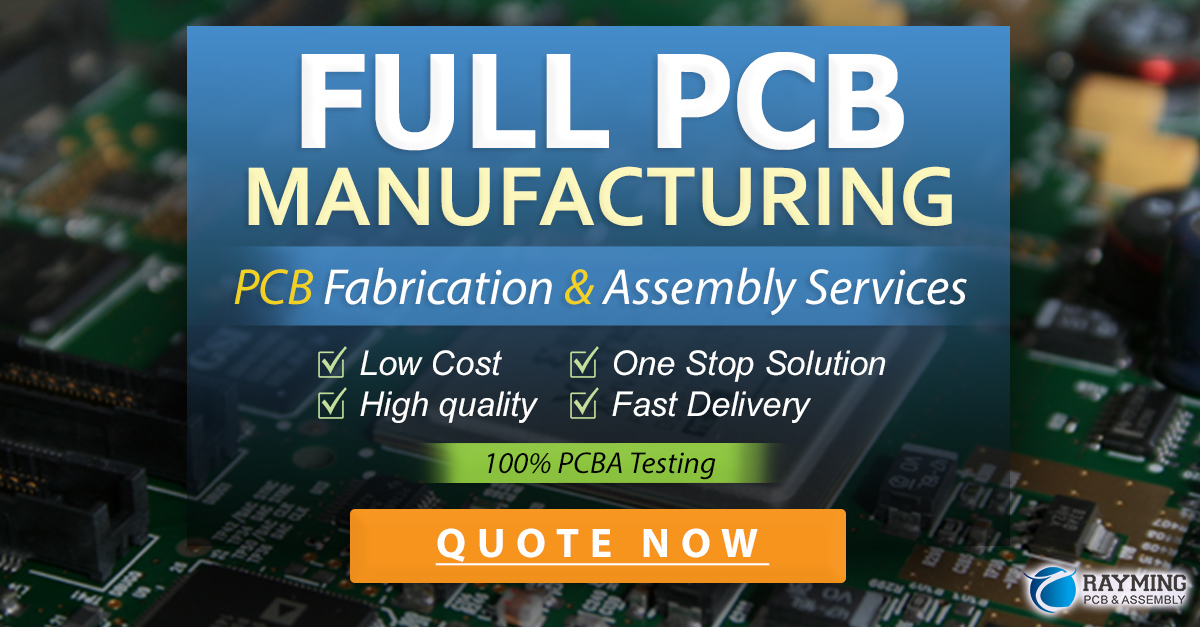
Leave a Reply