What are PCB Laminates?
PCB laminates are the base material used to manufacture printed circuit boards (PCBs). They provide the foundation upon which copper traces, components, and other features are added to create a functional electronic circuit.
PCB laminates consist of a non-conductive substrate material, typically fiberglass, which is impregnated with a resin, usually epoxy. This combination of materials provides the necessary mechanical strength, electrical insulation, and thermal stability required for reliable PCB performance.
Types of PCB Laminates
There are several types of PCB laminates available, each with its own unique properties and characteristics. The choice of laminate depends on the specific requirements of the PCB application, such as the operating temperature, frequency, and environmental conditions. Some common types of PCB laminates include:
-
FR-4: The most widely used PCB laminate, FR-4 is a glass-reinforced epoxy laminate that offers good mechanical strength, electrical insulation, and thermal stability. It is suitable for a wide range of applications, from consumer electronics to industrial equipment.
-
High Tg FR-4: This variant of FR-4 has a higher glass transition temperature (Tg), which allows it to maintain its mechanical and electrical properties at higher temperatures. It is often used in automotive, aerospace, and military applications where thermal stability is critical.
-
Polyimide: Polyimide laminates are known for their excellent thermal stability, chemical resistance, and low dielectric constant. They are ideal for high-temperature applications, such as aerospace and defense systems.
-
PTFE: Polytetrafluoroethylene (PTFE) laminates, also known as Teflon, offer exceptional dielectric properties and low dissipation factors. They are commonly used in high-frequency applications, such as radar and wireless communications.
-
Ceramic: Ceramic laminates, such as alumina and beryllia, provide excellent thermal conductivity and electrical insulation. They are often used in high-power applications, such as power electronics and LED lighting.
Properties of PCB Laminates
When selecting a PCB laminate, several key properties must be considered to ensure optimal performance and reliability. These properties include:
-
Dielectric Constant (Dk): The dielectric constant is a measure of a material’s ability to store electrical energy. A lower Dk value indicates better signal integrity and higher signal speed. Typical Dk values for PCB laminates range from 2.5 to 10.
-
Dissipation Factor (Df): The dissipation factor, also known as loss tangent, is a measure of a material’s ability to dissipate electrical energy as heat. A lower Df value indicates lower signal loss and better high-frequency performance. Typical Df values for PCB laminates range from 0.001 to 0.03.
-
Thermal Conductivity: Thermal conductivity is a measure of a material’s ability to conduct heat. A higher thermal conductivity allows for better heat dissipation, which is essential for high-power applications. Typical thermal conductivity values for PCB laminates range from 0.2 to 200 W/mK.
-
Coefficient of Thermal Expansion (CTE): The CTE is a measure of a material’s dimensional change in response to temperature changes. A lower CTE value indicates better dimensional stability and reduces the risk of thermal stress and delamination. Typical CTE values for PCB laminates range from 10 to 70 ppm/°C.
-
Moisture Absorption: Moisture absorption is a measure of a material’s ability to absorb moisture from the environment. High moisture absorption can lead to dimensional instability, delamination, and reduced electrical performance. Typical moisture absorption values for PCB laminates range from 0.1 to 2.5%.
Manufacturing Process of PCB Laminates
The manufacturing process of PCB laminates involves several steps to create a uniform and high-quality substrate material. The process typically includes:
-
Impregnation: The first step in manufacturing PCB laminates is to impregnate the reinforcement material, usually fiberglass, with a resin, typically epoxy. This is done by passing the reinforcement material through a bath of liquid resin, which is then partially cured to form a prepreg (pre-impregnated) material.
-
Layup: The prepreg material is then cut to size and layered with copper foil to form a stack. The number of layers and their arrangement depends on the specific PCB design and requirements.
-
Pressing: The layered stack is then placed in a heated press, where high temperature and pressure are applied to fully cure the resin and bond the layers together. This process typically takes several hours and results in a solid, rigid laminate sheet.
-
Cooling: After pressing, the laminate sheet is allowed to cool to room temperature. This process must be carefully controlled to avoid warping or other dimensional distortions.
-
Cutting: The cooled laminate sheet is then cut to the desired size and shape using precision cutting tools, such as diamond-tipped saws or routers.
-
Inspection: The final step in the manufacturing process is to inspect the laminate for any defects, such as voids, delamination, or surface imperfections. Various inspection methods, such as visual inspection, ultrasonic testing, and X-ray imaging, may be used to ensure the quality of the laminate.
Quality Control in PCB Laminate Manufacturing
Ensuring the quality of PCB laminates is critical to the performance and reliability of the final PCB Assembly. Several quality control measures are employed throughout the manufacturing process to maintain consistent and high-quality laminates:
-
Raw Material Testing: The raw materials used in PCB laminate manufacturing, such as fiberglass and resin, are tested for purity, consistency, and conformance to specifications. This ensures that only high-quality materials are used in the manufacturing process.
-
Process Control: The manufacturing process parameters, such as temperature, pressure, and time, are closely monitored and controlled to ensure consistent laminate properties. Statistical process control (SPC) techniques are often used to identify and correct any process deviations.
-
Inspection and Testing: As mentioned earlier, various inspection and testing methods are used to verify the quality of the laminate at different stages of the manufacturing process. These methods include visual inspection, dimensional measurement, electrical testing, and mechanical testing.
-
Traceability: Each laminate sheet is assigned a unique identification number, which allows for traceability throughout the manufacturing process and supply chain. This enables manufacturers to quickly identify and address any quality issues that may arise.
-
Certification: PCB laminate manufacturers often obtain certifications, such as ISO 9001 and UL recognition, to demonstrate their commitment to quality and conformance to industry standards. These certifications provide assurance to PCB manufacturers and end-users that the laminates meet the necessary quality and performance requirements.
Selecting the Right PCB Laminate
Choosing the right PCB laminate is crucial to ensure the optimal performance, reliability, and cost-effectiveness of the final PCB assembly. When selecting a PCB laminate, several factors must be considered, including:
-
Application Requirements: The first step in selecting a PCB laminate is to understand the specific requirements of the application, such as the operating temperature range, frequency, power level, and environmental conditions. This information will help narrow down the suitable laminate options.
-
Electrical Properties: The electrical properties of the laminate, such as dielectric constant and dissipation factor, must be carefully considered to ensure signal integrity and minimize signal loss. For high-frequency applications, laminates with low Dk and Df values are preferred.
-
Thermal Properties: The thermal properties of the laminate, such as thermal conductivity and CTE, are critical for applications that generate significant heat or are subjected to temperature fluctuations. Laminates with high thermal conductivity and low CTE are ideal for these applications.
-
Mechanical Properties: The mechanical properties of the laminate, such as flexural strength and modulus, impact resistance, and dimensional stability, must be considered to ensure the physical integrity of the PCB assembly. Laminates with high mechanical strength and stability are preferred for applications that are subjected to mechanical stress or vibration.
-
Cost: The cost of the laminate is an important consideration, particularly for high-volume production. While high-performance laminates may offer superior properties, they also tend to be more expensive. It is essential to strike a balance between performance and cost to ensure the overall cost-effectiveness of the PCB assembly.
PCB Laminate Selection Guide
To aid in the selection of the right PCB laminate, the following table provides a general guide based on common application requirements:
Application | Recommended Laminate | Key Properties |
---|---|---|
Consumer Electronics | FR-4 | Good balance of mechanical, electrical, and thermal properties; cost-effective |
Automotive Electronics | High Tg FR-4 | Excellent thermal stability; high mechanical strength; suitable for high-temperature environments |
High-Frequency RF/Microwave | PTFE | Low dielectric constant and dissipation factor; excellent high-frequency performance |
Aerospace and Defense | Polyimide | High thermal stability; low CTE; excellent chemical resistance |
Power Electronics | Ceramic | High thermal conductivity; excellent electrical insulation; suitable for high-power applications |
It is important to note that this guide is a general recommendation, and the actual laminate selection may vary based on the specific requirements of each application. It is always advisable to consult with PCB laminate experts or manufacturers to ensure the most suitable laminate is chosen for a given application.
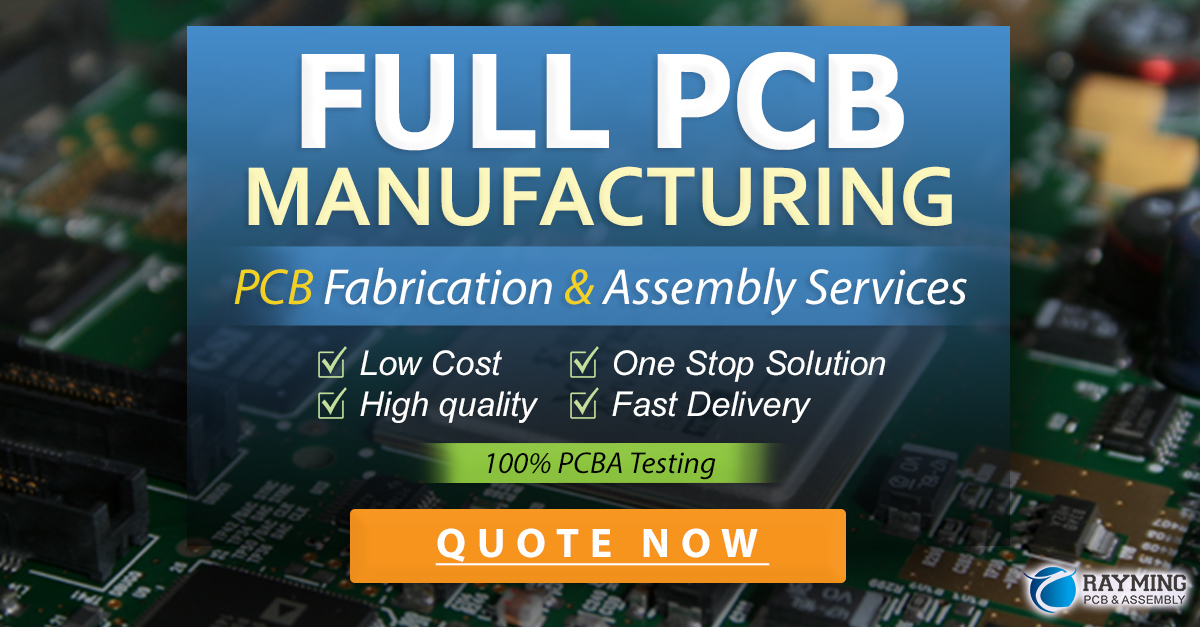
Conclusion
PCB laminates are the foundation of modern electronic circuits, providing the necessary mechanical, electrical, and thermal properties to support the reliable operation of PCBs. With a wide range of laminate materials available, each with its own unique characteristics, selecting the right laminate is crucial to ensure optimal performance and reliability.
By understanding the properties and manufacturing process of PCB laminates, as well as considering the specific requirements of the application, PCB designers and manufacturers can make informed decisions when selecting laminates. This, in turn, leads to the development of high-quality, reliable, and cost-effective PCB assemblies that meet the ever-increasing demands of the electronics industry.
As technology continues to advance, so too will the development of new and improved PCB laminate materials. By staying up-to-date with the latest advancements in laminate technology and working closely with laminate manufacturers and suppliers, the electronics industry can continue to push the boundaries of what is possible with PCBs and enable the development of innovative and cutting-edge electronic products.
Frequently Asked Questions (FAQ)
1. What is the most commonly used PCB laminate material?
The most commonly used PCB laminate material is FR-4, a glass-reinforced epoxy laminate. FR-4 offers a good balance of mechanical, electrical, and thermal properties, making it suitable for a wide range of applications. It is also cost-effective, which contributes to its widespread use in the electronics industry.
2. How do I select the right PCB laminate for my application?
To select the right PCB laminate for your application, consider the following factors:
– Application requirements (operating temperature, frequency, power level, environmental conditions)
– Electrical properties (dielectric constant, dissipation factor)
– Thermal properties (thermal conductivity, CTE)
– Mechanical properties (flexural strength, impact resistance, dimensional stability)
– Cost
Consult with PCB laminate experts or manufacturers to ensure the most suitable laminate is chosen for your specific application.
3. What is the difference between FR-4 and High Tg FR-4 laminates?
The main difference between FR-4 and High Tg FR-4 laminates is their glass transition temperature (Tg). High Tg FR-4 laminates have a higher Tg value, typically around 170°C, compared to standard FR-4, which has a Tg of around 130°C. This higher Tg allows High Tg FR-4 laminates to maintain their mechanical and electrical properties at higher temperatures, making them suitable for applications that operate in high-temperature environments, such as automotive and aerospace electronics.
4. What are the advantages of using PTFE laminates for high-frequency applications?
PTFE (polytetrafluoroethylene) laminates offer several advantages for high-frequency applications:
– Low dielectric constant (Dk) and dissipation factor (Df), which minimize signal loss and improve signal integrity
– Excellent thermal stability, allowing for operation in high-temperature environments
– Low moisture absorption, ensuring stable performance in humid conditions
– High chemical resistance, making them suitable for harsh environments
These properties make PTFE laminates ideal for applications such as radar, wireless communications, and satellite systems.
5. How can I ensure the quality of PCB laminates during the manufacturing process?
To ensure the quality of PCB laminates during the manufacturing process, several quality control measures can be implemented:
– Raw material testing to ensure high-quality materials are used
– Process control to maintain consistent laminate properties
– Inspection and testing at various stages of the manufacturing process
– Traceability to identify and address quality issues quickly
– Certification to demonstrate conformance to industry standards
By adhering to these quality control measures, PCB laminate manufacturers can consistently produce high-quality laminates that meet the necessary performance and reliability requirements for a wide range of applications.
Leave a Reply